1. INTRODUCTION
Formaldehyde-based synthetic adhesives possess some advantageous characteristics in terms of bonding quality and quantity available in the market (Danielson and Simonson, 1998; Umemura et al., 2013b; 2015). Application of urea-formaldehyde adhesives (Hong et al., 2017a; Iswanto et al., 2017), melamine-ureaformaldehyde adhesives (Hong et al., 2017b; Lubis et al., 2019a) and hybrid adhesives of blocked-pMDI/ melamine-urea-formaldehyde (Lubis et al., 2019b) on particleboard, glued laminated timber and plywood have been reported to produce high bonding strength. However, they also have the disadvantage of being nonbiodegradable, and non-renewable, specifically leading to formaldehyde emissions (Foyer et al., 2016), and subsequently encouraging the development of natural adhesives from natural resources that tend to be more environmentally friendly.
There have been many studies on natural adhesives, including citric acid (Umemura et al., 2011; Widyorini et al., 2013; Widyorini et al., 2016a), maltodextrin with citric acid (Santoso et al., 2017), citric acid with sucrose (Umemura et al., 2013b; Widyorini et al., 2016b), sucrose and starch (Lamaming et al., 2013), tannin, lignin, and protein-based varieties (Pizzi, 2006). However, tannins, especially the condensed forms have been continuously developed, owing to high reactivity towards aldehydes and other reagents (Pizzi, 2008). As their chemical structures are similar to phenols, hence, it is increasingly used for the replacement in phenolformaldehyde (PF) resin (Pizzi, 2006; Kim et al., 2003; Santoso, 2005). In addition, they have been identified from various sources, including plants, encompassing quebracho, chestnut, oak, tsuga, acacia, mangrove, and pine. Therefore, the modifications of tannin adhesives with hardener or binder components have been conducted, leading to the formation of tannin- formaldehyde, tannin-hexamine, tannin-isocyanates, tannin-phenols, tanninresorcinol, and tannin-sucrose adhesives (Pichelin et al., 2006; Pizzi, 2006; Valenzuela et al., 2012; Hendrik et al., 2019). Meanwhile, it has been established that the formaldehyde and hexamine additives are not environmentally friendly because they emerge from fossil fuels that cause emissions.
One tannin sources with the potential as an adhesive is gambir (Uncaria gambir (Hunter) Roxb.) (Pizzi, 1994; Kasim et al., 2007), based on the 33% tannin content present, especially the condensed tannin variety (Santoso et al., 2012; Ferdinal, 2014). This specific form has been identified in quebracho, tsuga, acacia, rhus, and pine (Pizzi, 2008), which are known to contain about 70% polyphenol tannin, and 20~25% non-tannin components, including simple sugars and polymeric carbohydrates. In addition, gambir is an extract derived from the leaves and twigs of Uncaria gambir plants, widely discovered in various regions of Indonesia, encompassing West Sumatera, Riau, North Sumatera, Bengkulu, South Sumatera, and Aceh (Sabarni, 2015). Moreover, in 2012, the Indonesian state had 29,326 ha of planted area capable of producing 20,511 tons of dried gambir, and 15,685 tons worth US $34 million were exported (Ministry of Agriculture of Indonesia, 2013).
The gambir extract has been evaluated to possess the following chemical components: catechin (7~33%), tannic acid-tannin (20~50%), pyrocatechol (20~30%), fluorescence gambir (1~3%), red catechu (3~5%), quercetin (2~4%), fat (1~2%), and wax (1~2%) (Amos, 2010). Meanwhile, others include alkaloids (dihydrogambirtannine, gambirdine, gambirtannine, gambirine, isogambirdine, auroparine, oxogambirtannine) (Hiller and Melzig, 2007). In addition, catechin is a monomer of condensed tannins, and the gambir production centers in Indonesia reported 2.5% to 95% content in gambir (Amos, 2010).
Tannin resins polymerized with formaldehyde typically have a higher internal bond (IB) strength (0.65 MPa) than those polymerized with other non-toxic and nonvolatile aldehydes, depending on the tannin reactivity (Ballerini et al., 2005). Meanwhile gambir-formaldehyde adhesives were previously examined for the particleboard developed (Kasim et al., 2007; Fathanah and Sofyana, 2013), and the mechanical properties were reported to meet the SNI 03-2105-2006 standard, although water absorption values were lower than the specifications. Based on the research, it is supposed that tannin in gambir has not been reacted optimally.
In other research, Umemura (2013a) found that the mixture of tannin and sucrose as a wood adhesive has potential. Tannin-sucrose adhesives for particleboard were then investigated (Zhao and Umemura, 2014; 2015), and the optimal ratio of tannin to sucrose was reported as 25/75 wt%. Nevertheless, the basic properties of gambir-sucrose adhesives and their adhesion strength of wood-based materials have not been studied.
The purpose of this study is to examine the basic properties of gambir-sucrose adhesive, specifically based on the appearance, pH, viscosity, density, solid content, gelation time, and insoluble matter content (IMC) in boiling water, as well as to measure the IB strength of particleboard. In this study, the gambir and sucrose are formulated in 100/0, 75/25, 50/50 and 25/75 wt% gambir/sucrose adhesives. Therefore, the effect of adding sucrose to gambir was investigated on the adhesive properties and adhesive strength of the particleboard. The change of chemical structure of the gambir-sucrose adhesive was investigated by Fourier transform-infrared (FTIR) spectroscopy. This was conducted to identify the basic properties and potentials of the adhesives composed of gambir-sucrose as wood composite adhesives.
2. MATERIALS and METHODS
The research material was gambir extract (Uncaria gambir) purchased from the traditional market, commonly termed gambir bootch, and the cylindrical forms as well as the dark brown color were used without purification. In addition, sucrose (99.5%) and sodium hydroxide (97%) analyzed grade were purchased from Merck. Each material employed were ground into powder and screened until it passed the 20-mess screen. Bamboo betung particle (Dendrocalamus asper (Schult.f.) Backer ex Heyne)) were obtained from waste of small industry roof trust in Sleman District, Special Region of Yogyakarta, Indonesia. For three months, bamboo has been immersed in cold water by the industry to minimize the content of extractive and starch, such as the purpose of pre-treatment immersion of acacia wood strands into hot water (Febrianto et al., 2009) and immersion of jatropha fruit hulls into hot and cold water (Iswanto et al., 2018) before being manufactured into boards. Bamboo particles were screened to collect 10 mess sieve particle passes, and particle were dried up to 11% (equilibrium moisture content).
The gambir extract (1 mg/ml in ethyl acetate) was prepared for direct injection into a GC-MS, and the data obtained with a GC-MS (QP 2010, Shimadzu, Japan) under the following conditions: RTx-5MS capillary column (30 m lenght; Restek Corp.); column temperature from 70°C within the first min, to 320°C at 5°C/min; injection temperature of 250°C; the detection temperature was 320°C; acquisition mass range of 50~800 amu, using helium as the carries gas. In addition, the components were identified with the assistance of a comparison between experimental GC-MS data with authentic catechin compounds (Sigma-Aldrich) and the NIST MS library.
The gambir-sucrose adhesives were made by dissolving gambir and sucrose powder in distilled water, at the blending ratios (wt%) of 100/0, 75/25, 50/50, and 25/75. Therefore, the solution concentration was adjusted to 45 wt%, and sodium hydroxide was added to each formulation, to adjust the pH to 8, as summarized in Table 1.
The adhesive properties were measured by the method described in the Indonesia Standards (SNI 06–4567–1998), regarding phenol-formaldehyde solution for plywood adhesives. Their characteristics evaluated were the appearance (color and presence of substance), pH, viscosity, and density, using pH meter (Sato SK-620PH, Japan), viscometer (Brookfield LV DV-E, USA), and 25ml pycnometer, respectively. The assessment of solid content, and gelation time were determined with three replications. Gelation time obtained by boiling the solution in hot water, providing indication of the limited flow characteristics when the test tube containing it is tilted. The properties of gambir-sucrose adhesive were also compared with those of phenol-formaldehyde resins.
The measurements of insoluble matter content (IMC) of the adhesives were made by the reported method (Umemura et al., 2017), which involved the drying at 80°C for 12 h in an oven, and the dried mixture was heated at 160°C, 180°C, and 200°C in an oven for 15 min. In addition, the heat-treated mixture was pulverized through a mesh size less than 60, and about 3 g of each treated powder was then immersed into boiling water for 4 h. Therefore, the solution was filtrated with filter paper, and the IMC remaining on the paper was dried at 80°C for 12 h in an oven, and subsequently determined according to the Equation (1):
Where, IMC (%), Wa = the dry weight of the insoluble matter after boiling water immersion (g), Wb = the dry weight of mixture before boiling water immersion (g).
Moreover, the component quantification was calculated based on relative peak area, and the FT-IR spectroscopy for gambir, sucrose, gambir-sucrose of 75/25 blending ratio (wt%) mixture was conducted. Therefore, each mixture was subsequently dried at 60°C for 5 h, and the infrared spectra of the mixtures were obtained with a FT-IR spectroscopy (IRPrestige 21, Shimadzu, Japan), using KBr disk method, and an average of 32 scans at a resolution of 4 cm-1 was identified.
Based on the optimal of gambir/sucrose blending ratio and hot-pressed temperature (indicated by insoluble matter content), bamboo particleboard were then manufactured in four blending ratios of gambir/sucrose such as 100/0, 75/25, 50/50, and 25/75 wt%. The gambir-sucrose solution was used as an adhesive and mixed onto particles at 30 wt% resin content based on the weight of the oven-dried particles. The particleboard was made from the bamboo betung particle with hot-pressed at 200°C for 10 min. The dimension of the manufactured particleboard was 250 × 250 × 10 mm and 0.8 g/cm3 in target density. The particleboards were conditioned for 1 week and then evaluated according to the JIS A 5908 2003 standard. The IB strength was obtained with 12 samples on 50 × 50 × 10 mm dimension.
3. RESULTS and DISCUSSION
Based on the GC-MS analysis, the chemical composition of gambir was calculated based on the relative peak area, which gave 31.11% catechin, 29.62% 2-aminoacetamide, 20.82%, and 5-acetoxy-3-(4-pyridyl) isoxazoline (Fig. 1), and other minor components. Meanwhile, other studies showed 7~33% of the catechin contents (Amos, 2010; Hiller and Melzig, 2007).
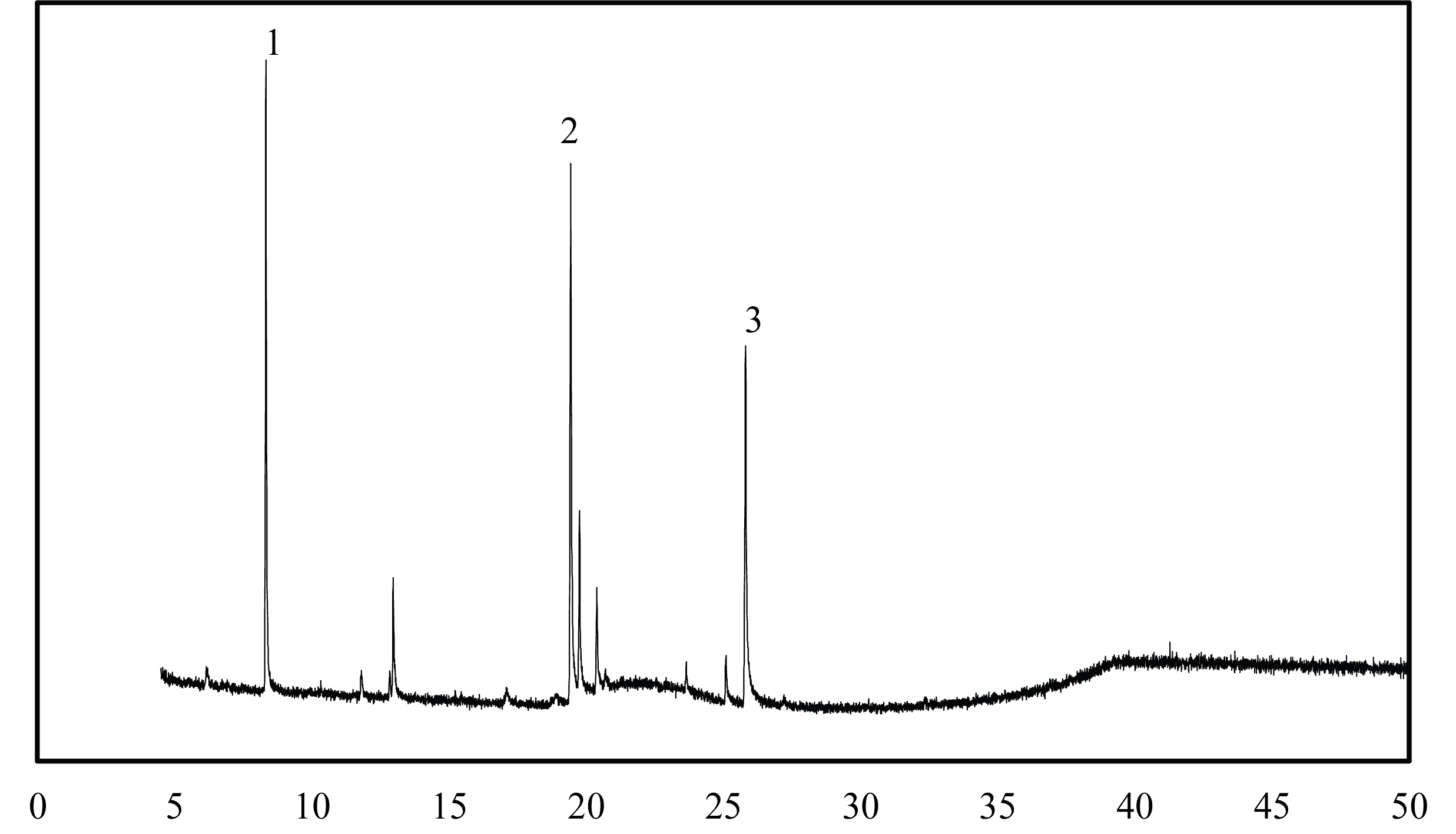
Fig. 2 showed pH of each gambir/sucrose blending ratio (wt%) of 100/0, 75/25, 50/50, and 25/75 to be 5.39, 5.60, 5.85, and 6.41, respectively. Therefore, pH adjustment for each sequentially increased the adhesive property to 8.00, 8.06, 8.08, and 8.00 with a NaOH 50% solution of 15, 10, 8, and 3 ml. This pH value was observed to be lower than that of phenolformaldehyde (PF) resins of about 12 ± 1.
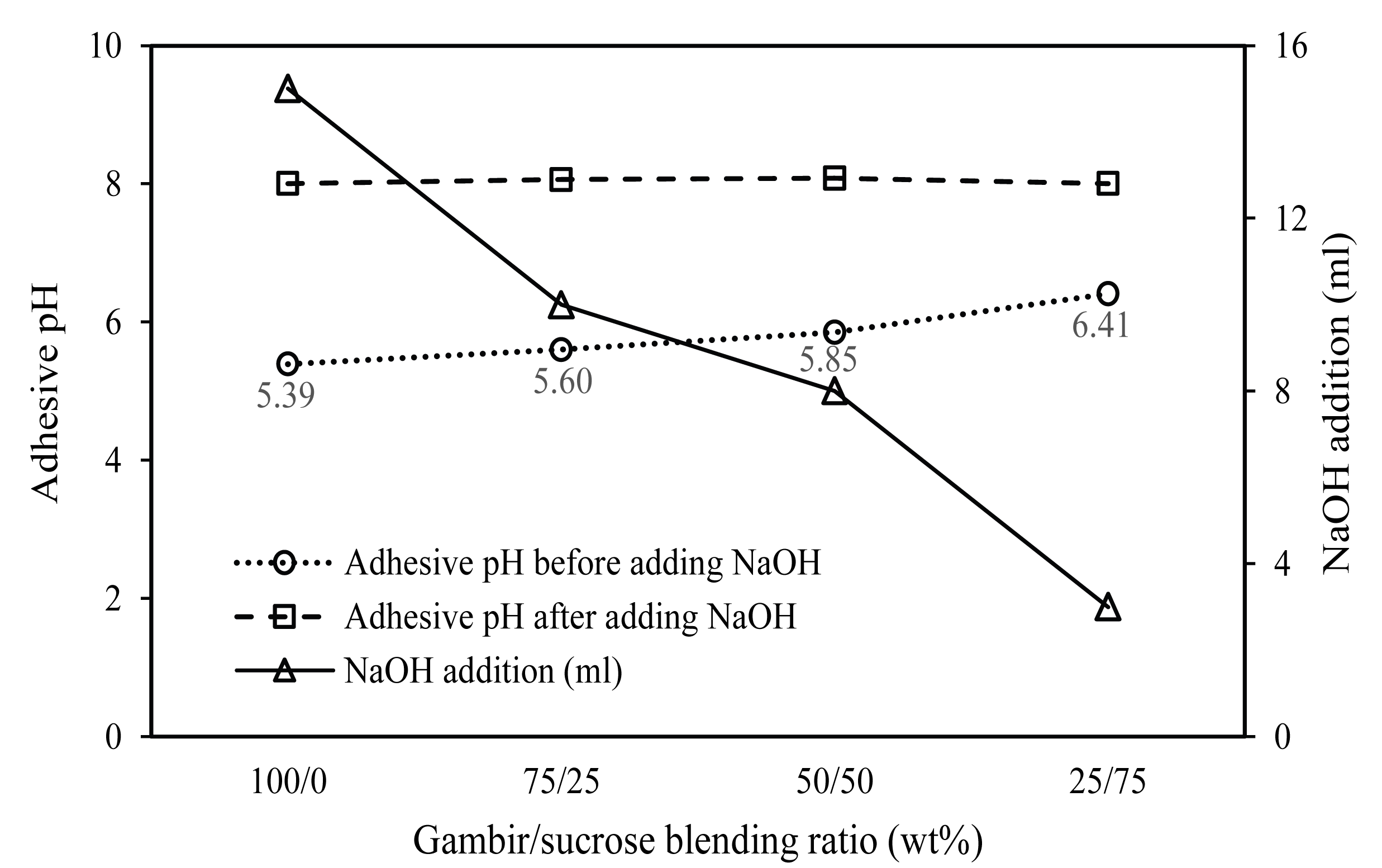
Gambir adhesive without sucrose (100/0 wt%) had a comparably lower pH than the combined variety, and an increase in the amount of sucrose added subsequently elevates the final pH, as the value recorded for the 75/25 wt% mixture was 5.60, which increased to 5.85 for the blending ratio of 50/50 wt%, and 6.41 for 25/75 wt%.
Catechin and tannic acid content were observed to affect the nature of gambir extract into being acidic (Amos, 2010), while sucrose is a disaccharide formed from glucose and fructose monomer units (Ophardt, 2003). This is because it is a non-ionic compound that does not dissolve into ions when water is added, and it also tends not to release H or OH ions in the process, therefore, the acidic or alkaline properties of the solution are unaffected. In addition, the pH of the formulated solution is often neutral or similar with the levels in water without its incorporation. Furthermore, the purpose of adding of sodium hydroxide to the adhesive mixture was to increase the pH that is naturally close to neutral. Thus, it also functions as a catalyst, subsequently accelerating the polymerization reaction between the adhesive and cellulose particles.
Table 2 and 3 shows the properties of gambir-sucrose adhesive and commercial PF resins, and it generally exhibited a brown color, due to the basic pigmentation of tannin (Eastaugh et al., 2004). Meanwhile, sucrose possesses a white-clear color, thus, the combination tends to brighten the brown tint, and this coloration obtained from several plants is widely used as natural dyes for clothing, e.g., Indonesian batik. Furthermore, its application was not suitable to timber composites within the wood industry, especially the brightly colored variety, based on its capacity to produce dark stained glue lines. This subsequently reduces the aesthetic characteristics of the products created, but not the mechanical properties.
* Phenol-formaldehyde resins IP-100 type specification (Intanwijaya International, 2019)
** Phenol-formaldehyde resins IP-100 type specification (Intanwijaya International, 2019)
Fine grain substance were found in the adhesive solution, which emerges from gambir particles that are insoluble in water, thus illustrating its comparably lesser solubility than sucrose at room temperature. Therefore, adding sugar to water promotes materials dissolution, subsequently creating a solution, which becomes saturated after a significant amount have been dissolved.
The viscosity is a concept describing how a liquid material flows, which is often applied in adhesive liquid. Therefore, diluted forms tend to give lower values, and easy flow, while more viscous varieties results in high viscosity. The viscosity of the adhesives varied from 7.30 mPa.s to 33.24 mPa.s (Table 3), and the highest values was obtained for the gambir adhesives (100/0 wt%). By contrast, those of the gambir-sucrose adhesives at different blending ratios (75/25, 50/50, and 25/75 wt%) were influenced by the low solubility of gambir. Furthermore, the addition of sucrose in the gambir reduced the viscosity obtained.
The densities of the gambir-sucrose adhesives were about 1.12 g/cm3, which was relatively similar to that of PF resins (1.17 to 1.18 g/cm3), while the value recorded for the solid content varied from 25.56% to 28.44%. This non-volatile solids content represents the binder content without the water, which is expected to improve its adhesion because a less amount of the solvent is present.
Meanwhile, the gelation time of gambir-sucrose adhesives varied greatly, ranging from 73 min to 420 min. This value demonstrates the time needed for the occurrence of gelation. In addition, tannin adhesives obtained from quebracho, mimosa, and mangium normally exhibited a gelation time of 17, 15, and 9 min, respectively (Santoso, 1997). Furthermore, the gambir-sucrose adhesives that contained less reactive and un-purified tannin as well as sucrose, had a 10 times higher value than PF adhesive (Intanwijaya International, 2019), which was consisted of reactive phenol and formaldehyde.
Fig. 3 shows that the gambir-sucrose adhesives with the blending ratio of 100/0 (wt%) provided insoluble matter contents, ranging from 43.72% to 50.53%, after heating at 160°C, 180°C, and 200°C for 15 min. Moreover, the addition of sucrose increased it about 49.05~62.10%, at 180°C and 200°C. The subsequent measurement of insoluble matter content was conducted as an indicator of a degree of the polymerization.
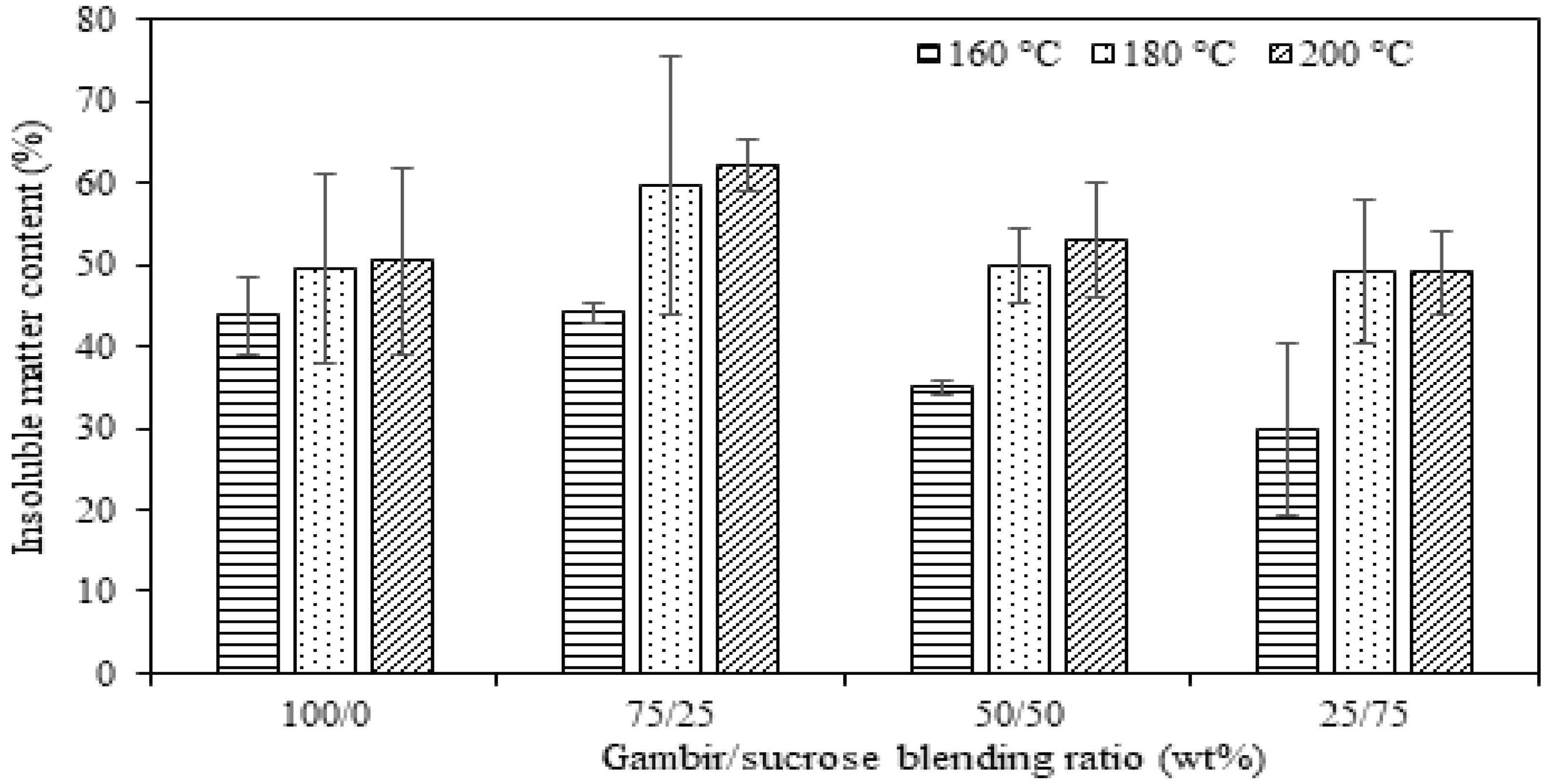
The insoluble matter content of the gambir-sucrose adhesive heated at 160°C was lower than others, which was reduced with the addition of sucrose. This is due to its easily soluble characteristic in hot and even in cold-water, with a value of 2,000 g/l at 25°C. Therefore, the insoluble matter content of sucrose is hardly identified, irrespective of the heating temperatures, as those heated at 120~200°C for 10 min were soluble in boiling water (Umemura et al., 2017).
Conversely, gambir tends to possess a relatively lower solubility or insolubility, as is often difficult to be dissolved the catechin content, which is the main component in a pure state. This constituent is, however, easily soluble in hot water, alcohol and also ethyl acetate (Muchtar et al., 2010; Yeni et al., 2014). In addition, heating gambir-sucrose adhesives to 160°C confers a low insoluble matter content, due to the fact that polymerization has not occurred. This occurs because the melting point of catechin, specifically 174~178°C (Rahmawati et al., 2012) was not reached.
The highest insoluble matter content values (59.75% and 62.10%) were achieved on gambir/sucrose blending ratio of 75/25 (wt%), with respective heating at 180°C and 200°C for 15 min, leading to the most significant degree of the polymerization. These temperatures were adopted as optimal for polymerization on the gambirsucrose adhesive.
Absorption peaks of the gambir are shown by FT-IR analysis, and an increase is observed with the subsequent addition of sucrose (Fig. 4). The 1620 cm-1 peak of the gambir-sucrose adhesive is taper and higher than the gambir adhesive was observed. Meanwhile, the peaks for the gambir at about 1620 cm-1 was ascribed to the C=O stretching of 5-hydroxymethylfurfural (Chuntanapum and Matsumura, 2009; Zhao and Umemura, 2015), and the combination of both as adhesives tend to produce a reaction between sucrose and the catechin obtained from the tannin of gambir.
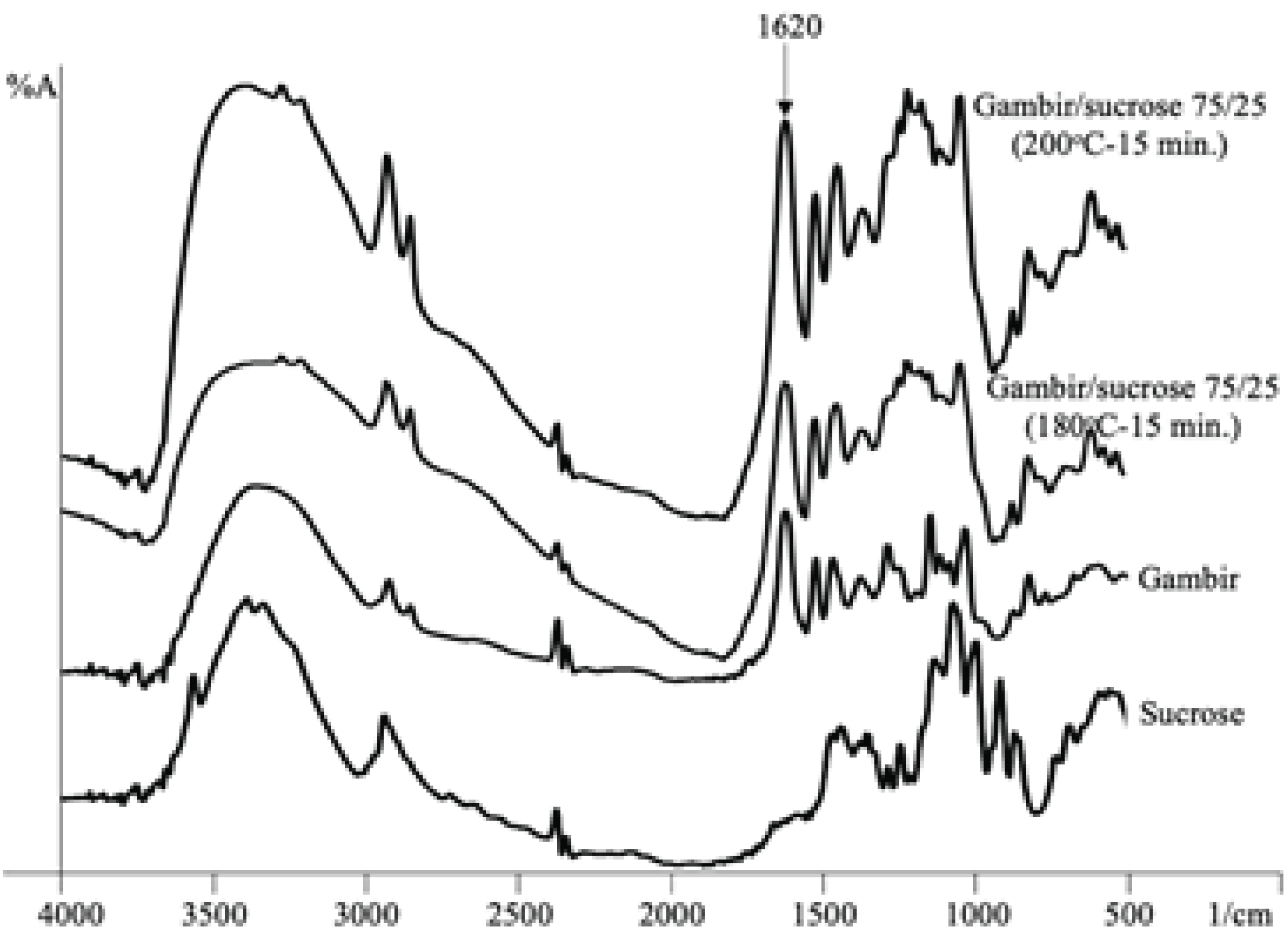
Therefore, this mixture is expected to improve adhesion performance, due to the dimethylene ether bridge between gambir tannin and the hydroxymethylfurfural (5-HMF) derived from the sucrose decomposition, as mentioned by Zhao and Umemura (2014). FTIR analysis indicated a potential of employing the gambir-sucrose adhesives as a particleboard adhesive. The possible reaction scheme between catechin tannin and sucrose was shown in Fig. 5.
The bamboo particleboard prepared with the gambir/ sucrose adhesives (100/0, 75:25, 50/50, and 25/75 wt% gambir/sucrose blending ratio) by hot-pressing at 200°C for 10 min had IB strength ranged from 0.30 MPa to 0.89 MPa, as summarized in Table 4. All the IB strengths met the requirements of the JIS A5908-2003. In particular, particleboards IB strength that pressed at 200°C was greater than 0.30 MPa, which was the standard requirement of particleboard type 18. The gambir-sucrose adhesives with 25/75 wt% blending ratio and 200°C hot-pressing temperature resulted in the highest internal bond strength (0.89 MPa).
4. CONCLUSION
Based on the result and discussion, it was established that gambir contains 31.11% catechin, which showed a potential as an adhesive. The addition of sucrose subsequently improved the solid content and gelation time properties. Furthermore, the gambir-sucrose adhesives with the blending ratios of 75/25, 50/50, and 25/75 wt% at 200°C heating temperature resulted in greater insoluble matter content. In addition, the properties of viscosity, density, solid content, and gelation time values were 7.30~33.24 mPa.s, 1.2~1.3 g/cm3, 25.56~28.44%, and 73~420 min, respectively. Also, FT-IR analysis showed that the absorption peaks of the gambir occurring around 1620 cm-1 was ascribed to the C=O stretching of 5-hydroxymethylfurfural, which tended to increase with the addition of sucrose. FT-IR spectra showed that the mechanism of reaction between gambir and sucrose was due to the bridges of dimethylene ether. The bamboo particleboards prepared with the gambirsucrose adhesives had an internal bond strength of around 0.30 to 0.89 MPa. The gambir-sucrose adhesives with 25/75 wt% blending ratio and 200°C hot-pressed temperature resulted in the highest internal bond (0.89 MPa), and met the requirement of JIS A5908 2003 type 18. Based on the research, a new adhesive composed of gambir-sucrose has a great potential for particleboard production.