1. INTRODUCTION
Large-cross-section timber is used in restoration projects for cultural heritage such as palaces and temples, and a continuous stream of studies have investigated ways to dry timber without check formation although the suitable solution is yet to be established (Lee and Lee, 2023; Park et al., 2020). In an actual site of such projects, air-dried materials are used in construction, while the moisture content in such materials only reaches the ideal level for construction after years of exposure to outdoor air (Han et al., 2019a; Han et al., 2019b).
However, for large-cross-section timber with a considerable length of internal moisture movement, air drying involves exposure to uncontrollable climate conditions so that a long time is taken for the moisture content to reach a desired level, while there is a possibility of biological defects such as discoloration and decay caused by microorganisms and drying defects such as surface checks. If a air-dried material that has not yet attained the target moisture content is applied in construction, problems such as shrinkage and check formation may arise to cause deformations in the entire structure. As incomplete drying can have a significant impact on the stability of the structure after construction, it is necessary to ensure that the target moisture content has been met to prevent checks prior to construction. Thus, efficient drying of large-cross-section timber is viewed as a critical task, for which investigations are ongoing (Jiang et al., 2023).
In the process of moisture removal from timber during kiln drying, the lower moisture content on the surface than on the interior is known to increase the relative level of shrinkage, which induces tensile stress. When the tensile stress on the surface exceeds the binding strength across the surface cells, checks are known to form on the surface to reduce the quality of dried timber (Kim et al., 2017; Lee, 2020). The kerfing process is used to prevent surface checks, whereby the drying stress in the tangential direction during drying is reduced so that checks are prevented from surfaces other than the kerf surface (Jung et al., 2022; Lee and Eom, 2021). The kerfing in the fiber direction was shown not to have a significant effect on the drying rate compared to the control, but it may affect the final moisture profile (Lee et al., 2017).
Red pine and Korean pine were treated with partial end sealing (PES) for the subsequent high-temperature low-humidity drying in Lee et al. (2017). The result showed that the moisture profile was low in red pine with the final moisture content at approximately 10%, while the moisture profile on the timber interior was uniform.
In general, surface checks are known to form due to tensile stress arising on the outer surface as the moisture that has moved from the interior to the surface evaporates to the exterior (Diawanich et al., 2012). Park et al. (2014) produced a hollow-core material through boring in the longitudinal direction, and treated the material with outer surface sealing to shift the direction of moisture movement from the inner to the outer surface. This caused tensile stress on the inner surface and compression stress on the outer surface, by which surface checks were prevented. The speed of moisture movement on the timber interior varies in each direction and across different tree species, and it should thus be assessed in accordance with the given conditions (Hwang et al., 2022; Kim et al., 2020; Sutapa and Hidyatullah, 2023).
The size and distribution patterns of residual stress are important in controlling drying defects (Yamamoto et al., 2021). Furthermore, pretreatment at high temperatures could reduce the stress arising from the anisotropy caused by shrinkage and moisture gradient, to prevent drying defects (Kang et al., 2020; Moya and Tenorio, 2022; Roger et al., 2021).
Kiln drying is a traditional and validated technique to remove moisture in timber. Suitable treatment of timber in the kiln allows moisture removal as well as reduced residual stress in dried timber (Jiang et al., 2023).
Previous studies have applied step steam to reduce the drying stress in kiln drying (Matsuo-Ueda et al., 2022). In Toba et al. (2023), where 100 × 100 mm lumber materials were steam-treated in the drying pretreatment, the effect of the steam treatment on the incidence of drying defects was determined based on the measurements of changes in surface size and drying stress.
Red pine is a tree species that has been frequently used from the past to the present in construction materials and daily commodities (Jang, 2022; Jung et al., 2022; Lee et al., 2021a, 2021b, 2022; Nam and Kim, 2021).
In this study, specimens from different parts of red pine timber were treated through sealing, followed by kerfing or boring, for subsequent drying, so as to alter the direction and speed of moisture movement on the timber interior and the direction of the drying stress. The aim was to identify a rapid drying pretreatment method that does not cause the formation of surface checks.
2. MATERIALS and METHODS
Red pine (Pinus densiflora S. et Z.) round timber of 450 mm diameter and 4.2 mm length, cut in the forest located in Gangwon-do, South Korea, was prepared. The timber was cut as shown in Fig. 1 to obtain five large-cross-section round timber of 600 mm length. Additionally, from the two ends of the large-cross-section timber, 20 mm thick specimens were obtained for measuring the initial moisture content and the wood density.
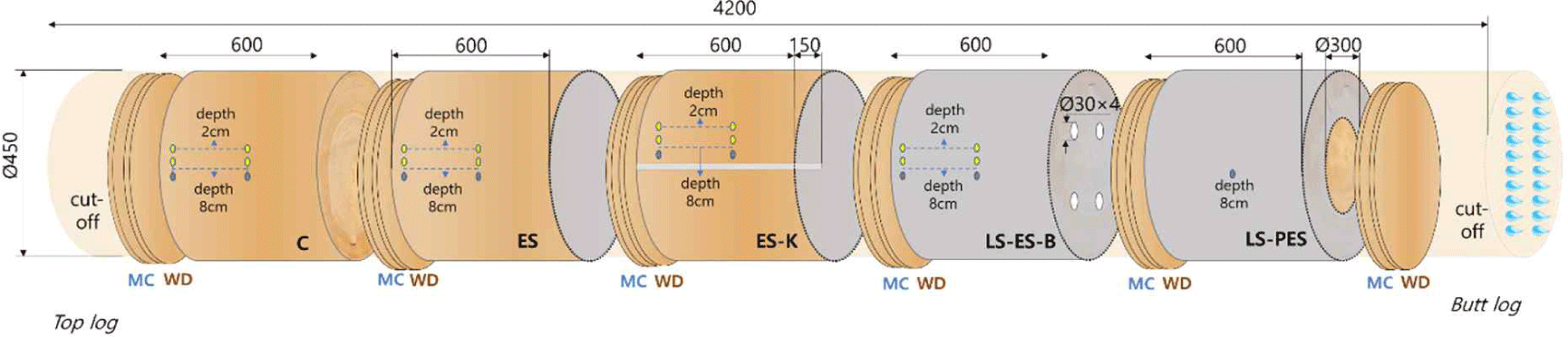
To control the direction of moisture movement during drying, the following pretreatments were applied before drying (Fig. 1).
The control materials were round timber dried after the exposure of the cross and lateral surfaces to outdoor air.
The formation of checks on the cross surface was minimized by suppressing rapid moisture evaporation on the cross surface. To prevent end checks from extending to the timber surface, the cross surface was sealed with a polyethylene wrap.
A chain saw was used to apply kerfing before drying to approximately 10 mm (8.2–12 mm) width and 150 mm depth. The cross surface was sealed with a polyethylene wrap.
A hole of 30 mm diameter was made in the longitudinal direction of the round timber on the parts that are half the radius on the cross-section. From this hole, the second, third, and fourth holes were made at 90°, 180°, and 270° rotated positions on the cross-section. To ensure that moisture evaporates only at the four holes of 30 mm diameter on the cross-section, all other parts on the cross and timber surfaces were sealed with a polyethylene wrap.
The lateral surface was sealed with a polyethylene wrap to reduce the moisture profile on the surface and interior during drying. The outer perimeter of the cross surface, excluding the inner perimeter of 300 mm radius, was sealed with a polyethylene wrap.
A kiln dryer (Hanbeak HB-503LF-0) that allows temperature and humidity control at ≤ 100°C was used. The target moisture content was set at 19%, and the drying proceeded in the conditions presented in Table 1.
From each of the two ends of the five round timber of 600 mm length, disc specimens of 20 mm thickness were obtained. Six specimens were prepared for measuring the initial moisture content. Using a small saw that allows simultaneous cutting of nine columns, the discs for measuring moisture content were prepared. After the cutting as shown in Fig. 2, the moisture profile was analyzed for each position.
From each of the two outer cross surfaces of five round timber of 600 mm length, six-disc specimens of 20 mm thickness were obtained.
where ρ(disk) is the wood density (kg/m3) in the disc specimen, Wod(disk) is the oven-dried weight (kg) of the disc specimen, and V(disk) is the volume of the disc specimen (m3) (Korea standard, 2022).
The Wod of the round timber was estimated using the wood density of the disc specimens collected from the outer cross surfaces on the two ends of the round timber and the volume of the round timber of 600 mm in length. Using the estimated Wod and the weight of the round timber of 600 mm length during drying, the moisture content in the round timber during drying was estimated. A digital scale was used to measure the disc specimens weight down to 0.01 g unit, and the flotation method involving the specific volume of water after the immersion of the disc specimens was used to estimate the specimen volume. The weight of the 600 mm round timber was measured down to 0.01 kg unit using a digital scale. Based on the wood density of the disc specimens from the cross surfaces, the Wod was calculated for each round timber using Equation (2) (Hwang and Lee, 1995). The estimated Wod and the measured weight of the round timber during drying were used to assess the changes in moisture content by time using Equation (3).
where Wod(timber) is the oven-dried weight of the 600 mm specimen (kg), V(timber) is the volume of the 600 mm specimen (m3), ρ(disk) is the mean wood density (kg/m3) of the 20 mm thick disc specimens collected from the two ends of the 600 mm specimen, MC(timber) is the moisture content in the 600 mm specimen, Wg(timber) is the fresh weight of the 600 mm specimen (kg).
To measure the timber interior temperature during drying, a K-type thermocouple was inserted at 20 and 80 mm depths from the surface, and the measured interior temperatures were recorded in 30-second intervals by a data logger (CR1000X, Campbell Scientific, Logan, UT, USA). To measure the changes in temperature and humidity during drying, a small sensor (iButton) was inserted at an 80 mm depth in the middle and edge of the 600 mm specimen. The measurements were used to calculate the equilibrium moisture content (EMC) for the specimen through the Hailwood-Horrobin equation shown in Equation (4). The trend of change in EMC was examined (Ra, 2014).
where EMC is the equilibrium moisture content (%), RH is the relative humidity on the timber interior (%), and W, K1, and K2 are the coefficients in the adsorption model developed by Hailwood-Horrobin.
For all dried specimens, the area of surface checks caused by the pretreatment was estimated by measuring the length and width of the checks of ≥ 1 mm width using Vernier calipers. Additionally, for the 20 mm thick specimen collected from the middle of the round timber, the number of checks on the interior and the length of each check were visually examined. During drying, the outer surface checks were monitored, and images were taken.
The kerf widening rate was calculated using Equation (5) (Lee, 2020).
where Widthbefore is the width of the kerf (mm) before drying and Widthafter is the width of the kerf (mm) after drying.
To estimate the volumetric shrinkage after drying, positional markings were made on the specimen as shown in Fig. 3, and the lengths before and after drying were measured at identical positions using calipers (CD-30PSX, Mitutoyo, Sakado, Japan) and pi-tape. The width and length of the cross surface were measured, and the circumference was measured at three positions. The mean values of these measurements were used to estimate the specimen volume. The volume before drying was also measured using the floatation method, involving the specific volume of water after the immersion of the specimen. A 3D scanner (Leica C10) was used to take volumetric measurements.
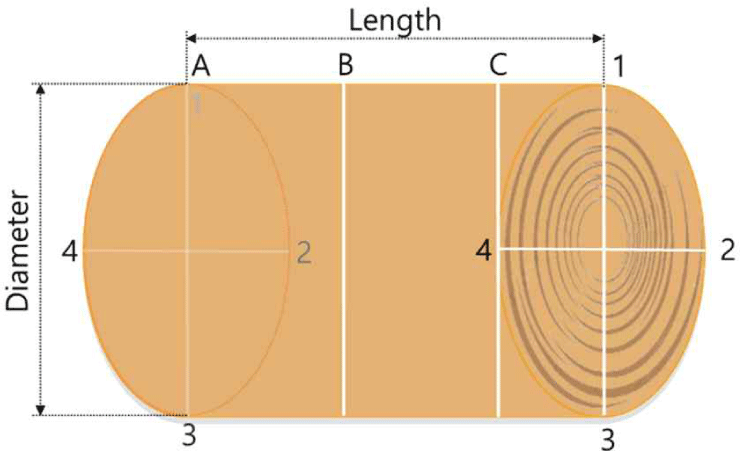
The volumetric shrinkage in the 600 mm specimen was calculated using Equation (6).
where αv is the volumetric shrinkage (%), Vg is the volume of the fresh material (m3), and Vafter is the volume of the dried material (m3).
3. RESULTS and DISCUSSION
The initial moisture contents at different parts inside the 4.2 m round timber were measured using the oven-drying method. As described in the MATERIALS and METHODS section, six-disc specimens for measuring the moisture content were collected from the middle area of the 4.2 m round timber, and five specimens of 600 mm length were taken from between the discs. Fig. 4 shows the moisture profile based on the measurements at each 600 mm length with the distal cross surface of the 600 mm specimen as the reference point. The moisture content in the fresh material of red pine was 150% at the sapwood and 30% at the heartwood, with a difference of approximately 120.0%.
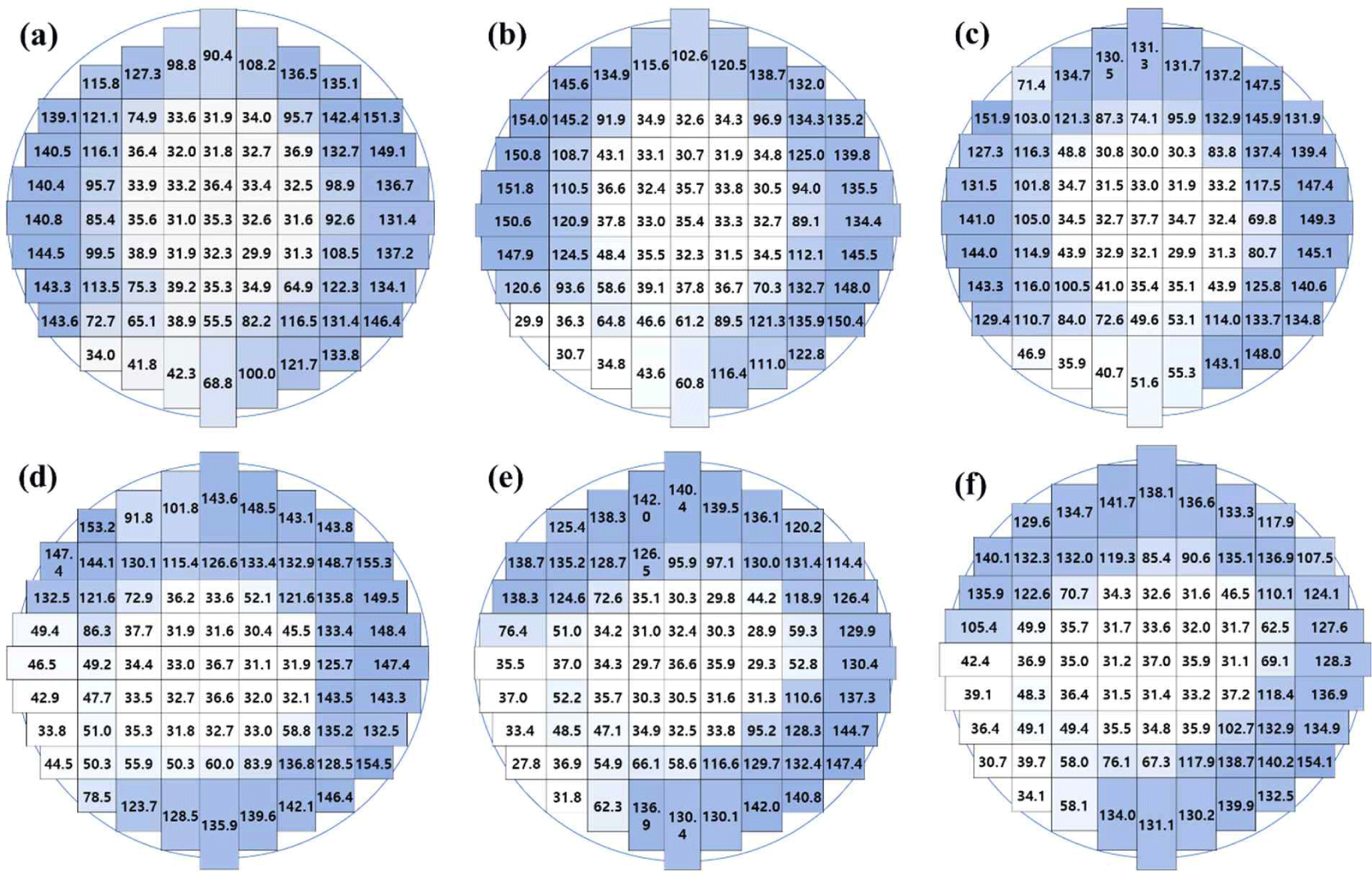
The wood density was estimated using the disc specimen collected from an area close to each cross surface of the 600 mm kiln-dried specimen; i.e. at each position distanced by 600 mm in the longitudinal direction of large-cross-section round timber. After estimating the volume of six-disc specimens using the floatation method, rapid oven-drying was applied to measure the oven-dried weight to estimate the wood density. Fig. 5 shows the wood density measured at different parts in the longitudinal direction of large-cross-section timber. As shown, a decreasing trend in wood density was observed from the lower end to the upper end of the timber.
Furthermore, the initial moisture content was estimated for the disc specimens using the total fresh and oven-dried weights of 77 small specimens obtained from each disc used in measuring the moisture profile presented in Fig. 4. The moisture content at each different part in the longitudinal direction of large-cross-section timber is as shown in Fig. 5.
The moisture content varied according to the part in the longitudinal direction of large-cross-section timber. With moisture movement from the cross surface according to the log storage time after felling, the deviation in moisture content between the timber center and the two ends of the timber in the longitudinal direction increases.
The variation in wood density was lower compared to the moisture content at each different part in the longitudinal direction. With changes in log storage time after felling, the variation in wood density is still low. The volumetric shrinkage at the two ends in the longitudinal direction due to moisture evaporation at the cross surface during log storage is relatively very low compared to the variation in moisture content at the two ends. Thus, compared to the moisture content, the variation in wood density was low at different parts in the longitudinal direction.
Fig. 6(a) shows the changes in moisture content of the control, ES, and ES-K materials during drying. The graphs present the changes in outdoor temperature and humidity and timber moisture content for 1,146 hours. With the lateral surface exposed to outdoor air and the cross surface sealed, tensile stress arises in the tangential direction of the material as the surface moisture content falls below the fiber saturation point. If the stress exceeds the tensile strength in the tangential direction of the timber, a surface check occurs, and as timber exhibits low tensile strength in the tangential direction, surface checks occur readily upon exposure of the cut surface with only the ES treatment. Thus, in the case of traversing moisture movement in the timber due to ES, the moisture profile between the surface and internal layers should be decreased, and to reduce the drying stress, low temperature, and high humidity conditions should be applied [Fig. 6(a)].
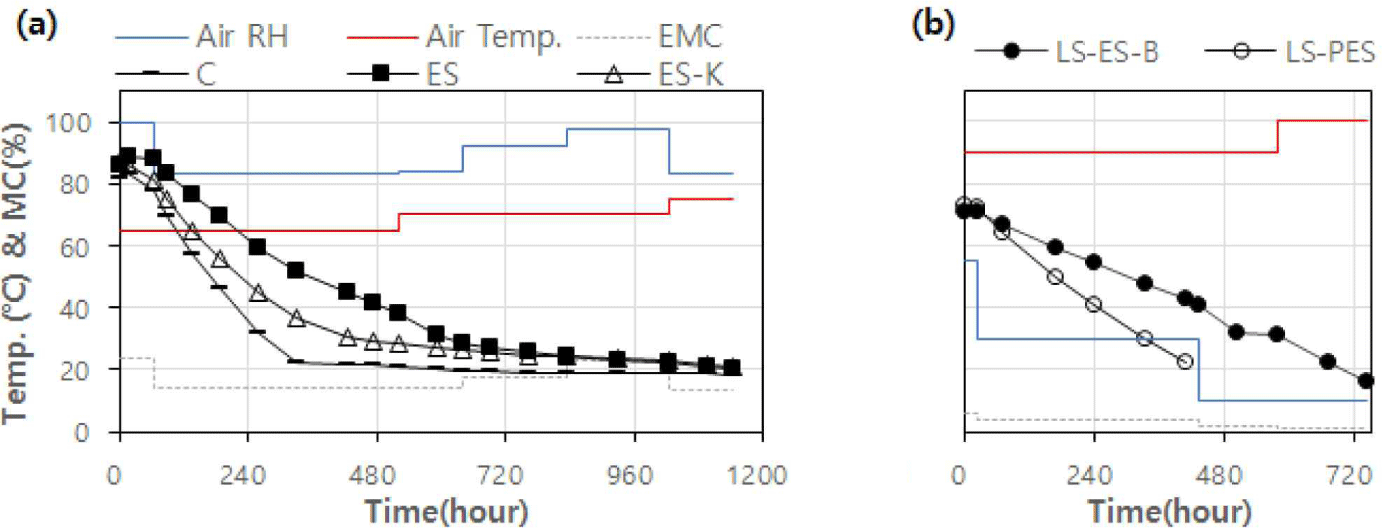
Fig. 6(b) shows the changes in moisture content of the LS-ES-B and LS-PES materials during drying. The graphs present the changes in outdoor temperature and humidity and timber moisture content for 745 hours. With the cross surface exposed to outdoor air and the lateral surface sealed, the surface moisture is able to stay close to the fiber saturation point for a long time until the mean moisture content of the entire timber reaches the fiber saturation point and falls below it. Thus, drying stress caused by the moisture profile between the surface and internal layers is difficult to arise.
Meanwhile, due to the rapid moisture movement in the fiber direction from the center to the cross surface, drying stress is induced by the moisture profile in the fiber direction. If the stress exceeds the timber strength in the fiber direction, the fiber on the surface or timber interior is cleaved in the longitudinal direction. However, as the level of timber strength in the fiber direction is substantially high, such fiber cleavage on the surface does not readily occur. Thus, with a low risk of surface checks after lateral sealing and upon the moisture movement in the fiber direction on the timber interior, high temperature, and low humidity conditions were applied [Fig. 6(b)].
The drying rate is as shown in Fig. 7. For the control (C), the drying rate was 0.15% per hour, an approximately 2-fold higher level compared to the ES-treated specimens (ES and ES-K) in the same kiln drying conditions.

On the contrary, comparing the two LS-treated specimens (LS-ES-B and LS-PES) after drying at relatively high temperatures showed that the drying rate was higher for the LS-PES specimens. This is presumed to be because the moisture evaporation at the unsealed parts of a 300 mm diameter on the interior at the cross surface occurred in the fiber direction with rapid moisture movement on the timber interior.
The drying rate was low for the LS-ES-B specimens. With complete sealing of the outer surfaces, the moisture evaporation occurred solely on the inner surfaces at the area of boring so that the bore size determined the drying rate. This is presumably because the inner surface of the bore, which is determined by the applied bore size, was considerably small compared to the sum of all outer surfaces. For the moisture evaporation on the inner surface of the bore, the relatively slow moisture movement in the cross-sectional direction on the timber interior, compared to the fiber direction, is presumed to have lowered the drying rate compared to exposed cross surfaces.
Fig. 8(b) presents the estimated EMC using the temperature and humidity data recorded by the small sensor (iButton) inserted at 80 mm depths of the middle and edge in the longitudinal direction of the 600 mm specimen. The trend of change in EMC was similar to the trend of moisture content based on weight measurements for the 600 mm specimen during kiln drying.
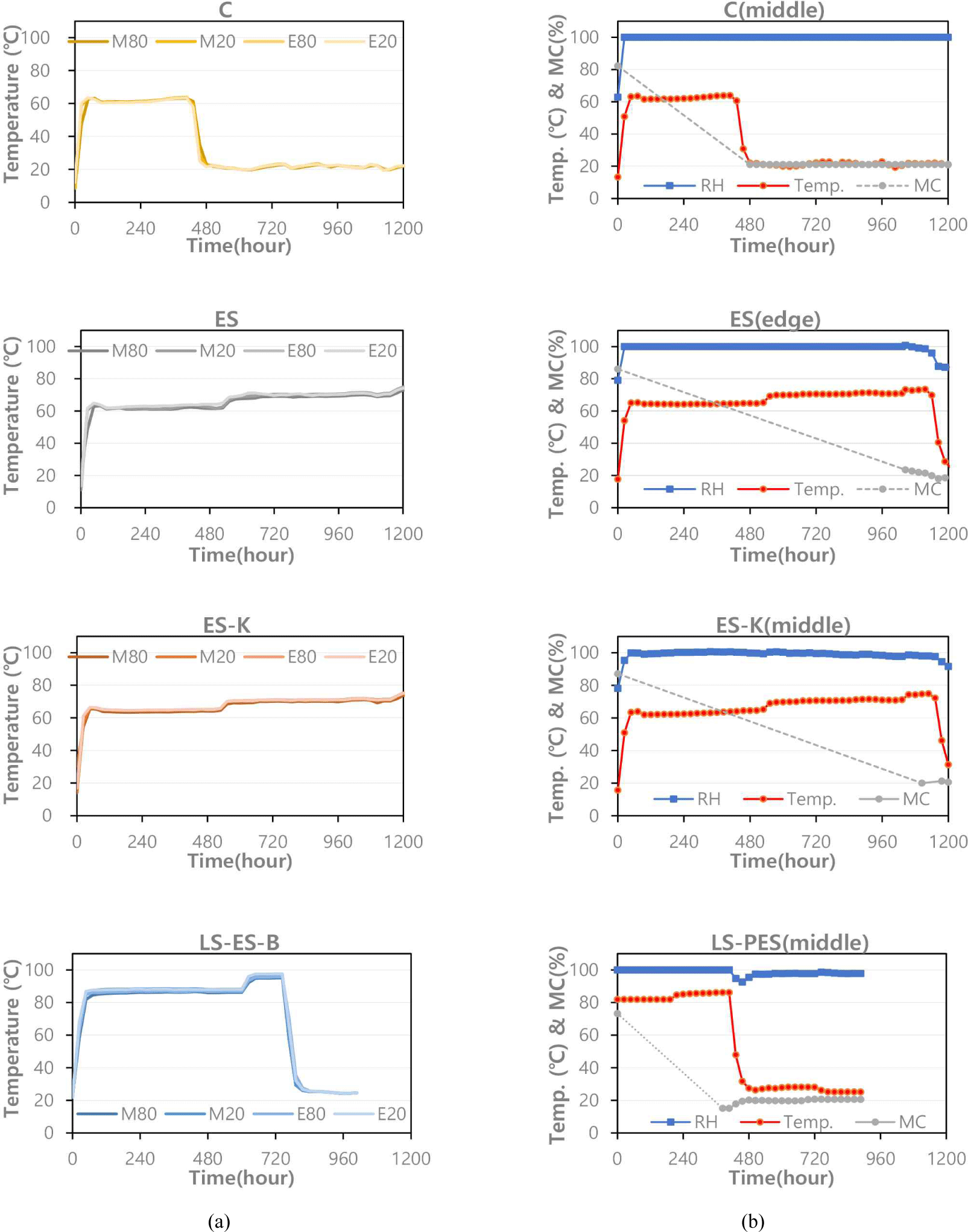
Fig. 8(a) presents the thermocouple-measured temperatures at 80 mm and 20 mm depths from lateral surface at the middle and edge in the longitudinal direction of the 600 mm specimen. At an early stage of the drying experiment, the temperatures at 80 mm (M80) and 20 mm (M20) depths from the surface varied significantly in the middle of the specimen, but the variation was markedly reduced after 48 hours. For the end cross surfaces, the temperatures at 80 mm (E80) and 20 mm (E20) depths increased rapidly from a state of low variation.
The final moisture profile detected using the oven-drying method and the small specimens from different parts of the disc collected from the middle of the 600 mm specimen, is presented in Fig. 9(a–e). The moisture content at the completion of drying for the 600 mm specimen was 22.2% in the control group, 21.9% in the ES group, 17.4% in the ES-K group, 18.5% in the LS-ES-B group, and 21.5% in the LS-PES group. After drying, the deviation in moisture content between the surface and the interior was within 10%.

Detecting timber surface defects is useful in the evaluation and enhancement of timber product quality (Lee et al., 2017). The measured area of surface checks after drying was 58.6 cm2 in the control group, 42.5 cm2 in the ES group, 0 cm2 in the LS-ES-B group, and 27.8 cm2 in the LS-PES group (Fig. 10).
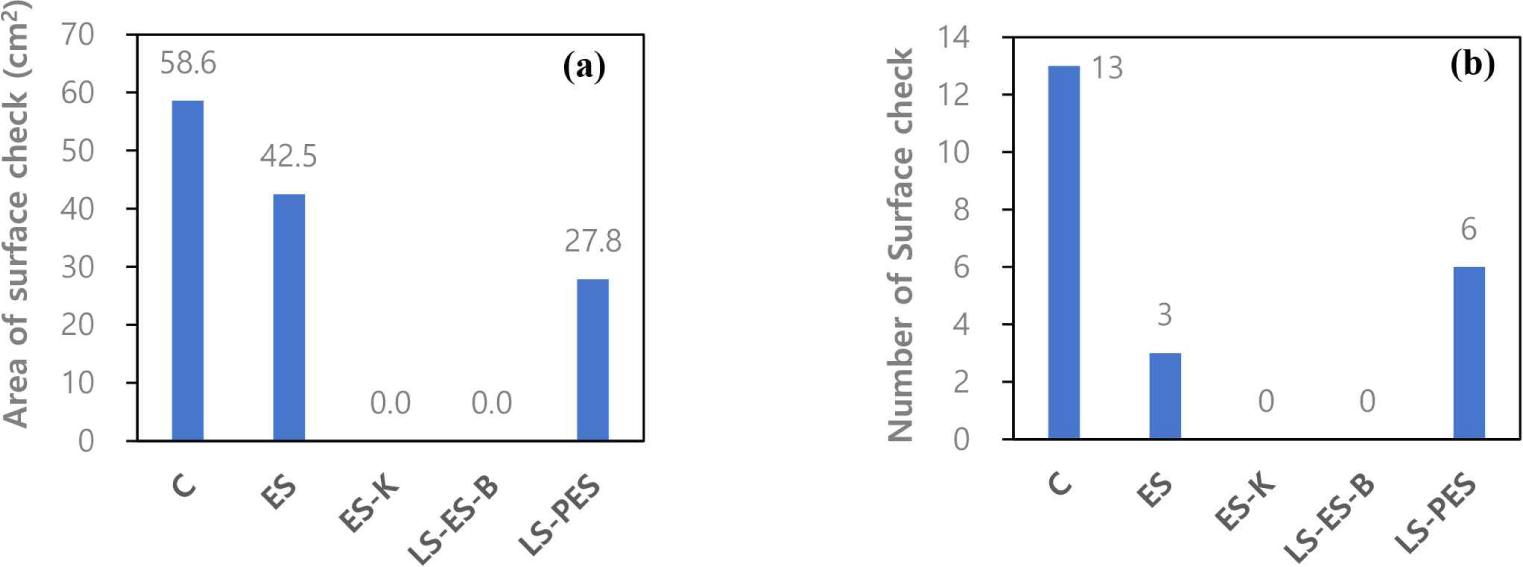
Compared to the control and ES groups, surface checks can be significantly prevented in the LS-ES-B group due to the considerably low interior moisture profile and negligible tensile stress on the outer surface.
Fig. 11 presents the images of actual cross surfaces. Cross-sectional checks of large size and amount were observed at the cross surfaces of the control materials [Fig. 11(a)]. The detected level of cross-sectional checks was lower in the ES-treated materials [Fig. 11(b) and (c)] compared to the control. No check was detected on the surface, except in the kerf area, in the ES-K-treated materials [Fig. 11(c)]. Instead, the width of the kerf after pretreatment was increased from 10 mm to 40 mm at a kerf widening rate of 300%. Similar findings were reported in Jung et al. (2022). No check was detected on the lateral surface in the LS-ES-B-treated materials.
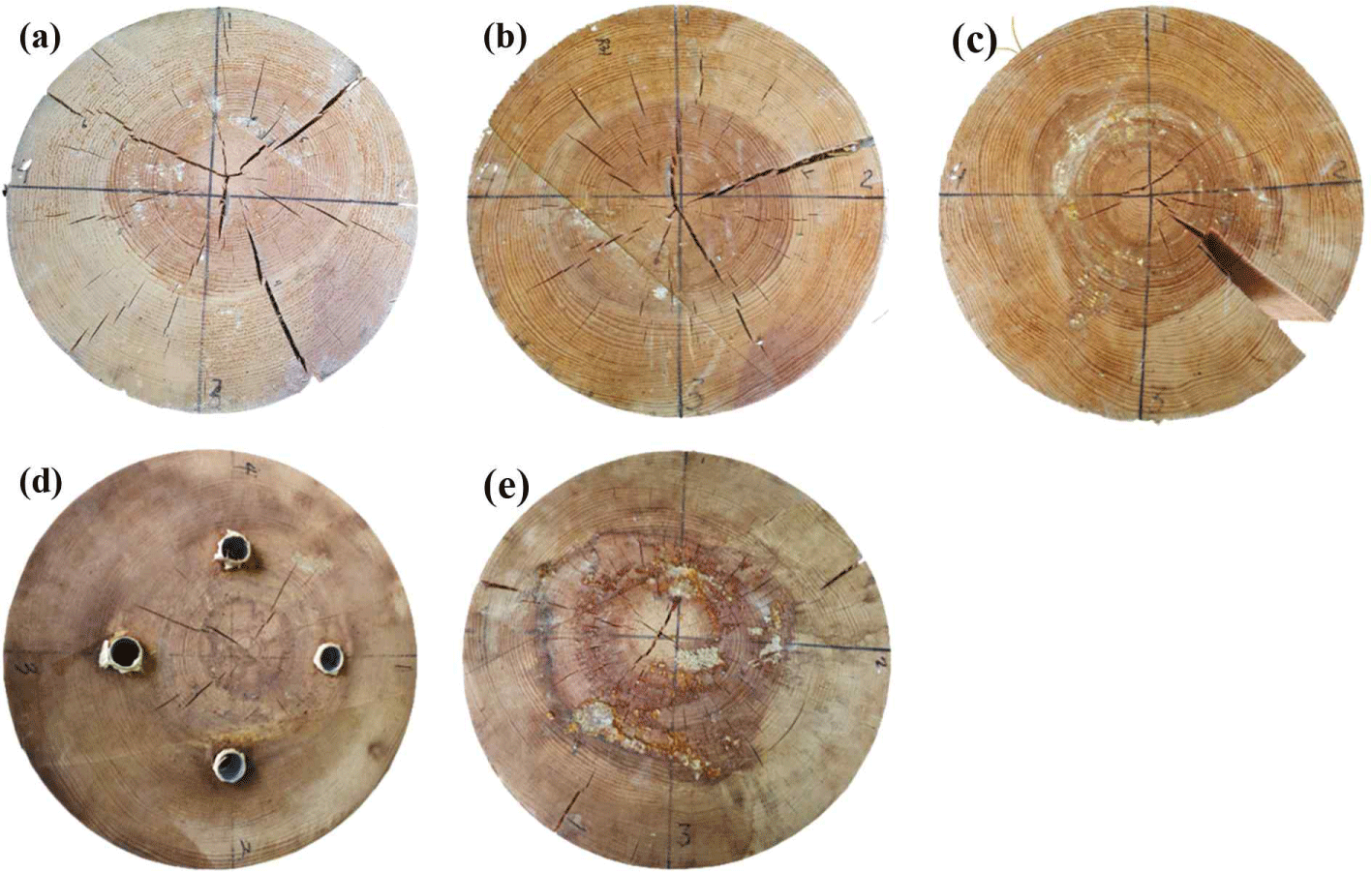
In the LS-PES treatment, moisture evaporation at lateral surfaces is prevented and moisture movement is allowed solely at cross surfaces, which resulted in almost zero detection of checks on the outer surface. As such, checks at the timber surface and cross surfaces were shown to be reduced through the LS-PES treatment [Fig. 11(d) and (e)].
Three methods were used to measure the volume of large-cross-section timber specimens: the 3D scan, floatation, and caliper methods. Table 2 presents the results. The results of the 3D scan and caliper methods were compared based on the result of the flotation method, determined to be the closest to true values, and the deviation in volume was 0.68% between the 3D scan involving image analysis and the flotation involving the specific volume of water. The deviation was 0.89% between the caliper method and the flotation method. The 3D scan and caliper methods were shown to display highly similar values to the true values. Hence, the caliper method with a short measurement time and few required devices were shown to allow accurate volume measurements.
Table 3 shows the volumetric shrinkage determined based on the volume measurements of the caliper method. For the ES-treated specimens after drying, with the exposure of the lateral surfaces to outdoor air (C, ES, and ES-K), the volumetric shrinkage was 2.5%. For the LS-ES-B-treated specimens, the volumetric shrinkage was the highest at 4.7%.
Sample | Volume before drying (m3) | Volume after drying (m3) | Shrinkage (%) |
---|---|---|---|
C | 0.0993 | 0.0973 | 2.02 |
ES | 0.0980 | 0.0956 | 2.50 |
ES-K | 0.0981 | 0.0956 | 2.60 |
LS-ES-B | 0.0974 | 0.0931 | 4.70 |
LS-PES | 0.1003 | 0.0968 | 3.62 |
4. CONCLUSIONS
To develop an artificial drying technique to ensure the production of large-cross-section red pine timber without drying defects, five round timber specimens were pretreated with the ES, ES-K, LS-ES-B, and LS-PES methods, and the changes in moisture content during kiln drying and the incidence of drying defects were investigated. The following conclusions were drawn:
-
The oven-dried weight of round timber and the moisture content during drying could be estimated based on the wood density and volume measured for the discs collected from the two ends of the round timber. Notably, the calculation of moisture content based on wood density is anticipated to allow practical estimation of moisture content with minimized waste of materials in the test of final products and during processing for the large-cross-section timber.
-
The level of drying checks in large-cross-section timber materials could be substantially reduced through the LS-ES-B treatment. As lateral sealing enhances the interior moisture profile but induces no tensile stress on the outer surface, the treatment had an effect on preventing surface checks that are common upon the drying of large-cross-section timber materials.
-
The level of drying checks decreased on the timber surface, except in the kerf area generated during the ES-K treatment. The treatment was highly effective as an artificial control of the potential areas of checks.
The findings of this study are anticipated to prove valuable as basic data for investigating the position and time to apply the partial sealing or boring treatment so as to prevent drying defects in large-cross-section timber.