1. INTRODUCTION
The sugar palm tree (Arenga pinnata), a member of the Palmae family, is widespread in Indonesia and other Asian countries and is known as a multi-benefit plant that produces food and non-food products (Ishak et al., 2013; Lim, 2012; Rinawati et al., 2021). In Indonesia, its plantations cover around 64,025 hectares in 29 provinces (Ministry of Agriculture Republic Indonesia, 2021). This tree is a great source of food, beverages, bioenergy, biofibers, biopolymers, and biocomposites (Ilyas et al., 2020; Mukhtar et al., 2016; Sanyang et al., 2016). Each sugar palm tree has a yield of 1.44 kg/day over four productive months/year (or 172.8 kg/year) for palm sugar and 50–75 kg for starch (Elbersen and Oyen, 2010; Mogea et al., 1991; Pontoh and Smits, 2015).
Starch is extracted from the inner core of the sugar palm trunk using a grinding process, water pouring, and squeezing technique (Sanyang et al., 2018), in which high-fiber dregs are discarded as organic waste (Agustina et al., 2022). According to Sudaryono et al. (2013) in Hakim et al. (2022), material balance in palm sugar industry consists of solid waste/fibre (56%), starch (17%), bark (25%), and others (2%), based on wet conditions. According to Sahari et al. (2012), the chemical composition of a sugar palm trunk comprises cellulose (40.56%), holocellulose (61.10%), lignin (46.44%), ash (2.38 %), and extractives (6.30%). On the other hand, the chemical composition of the fiber dregs comprises cellulose (60.61%), hemicellulose (15.74%), and lignin (14.21%; Purnavita and Sriyana, 2013). Sahari et al. (2012) evaluated the tensile strength of fibers from sugar palm trunk as 198 N/mm2, making it a suitable raw material for particleboard production. Owing to their high fiber content, dregs also appear to be a potential raw material for the manufacturing of particleboard.
Currently, particleboards with natural adhesives are being widely studied and developed owing to the increased public awareness of non-hazardous products as well as governmental regulations. Some natural adhesives/ binders have been explored such as lignin, casein, keratin, collagen, wheat gluten, soy-protein, rapeseed-protein, zein-protein, starch, konjac glucomannan, chitosan, sucrose, shellac, gum, rubber, tannin, maltodextrin, gambir, citric acid, and maleic acid, as well as their combinations (Bertaud et al., 2012; Kollmann et al., 1975; Raydan et al., 2021; Sahari et al., 2013; Santoso et al., 2017; Sucipto et al., 2020; Sutiawan et al., 2022; Umemura et al., 2003, 2013; Widyorini et al., 2016a, 2016b, 2018a). Among these adhesives, sucrose/citric acid is promising because of its excellent bonding strength and high availability. This excellent bonding strength is attributed to the esterification reaction between the furan polymer of sucrose dehydration and citric acid, which also forms an esterification reaction with the hydroxyl groups of wood (Ando and Umemura, 2021). The particleboard manufactured using sucrose/citric acid (75/25 wt%) and 30 wt% adhesive content had the properties that met the Japanese Industrial Standard (JIS) A 5908 type 18 (Umemura et al., 2013, 2015). Moreover, the particleboard made from sweet sorghum bagasse with 20 wt% adhesive content at the same sucrose/citric acid ratio had the properties that fulfilled the JIS A 5908 type 18 (Kusumah et al., 2017). In contrast, the properties of the particleboard made from teak wood with the same sucrose/citric acid ratio and pressing conditions satisfied the JIS A 5908 type 8 at 10 wt% adhesive content (Widyorini et al., 2016a). These results showed that the properties of the particleboard were affected by the adhesive content and raw material. Furthermore, increasing the adhesive content tends to improve the mechanical performances of particleboard (Hwang and Oh, 2020a; Maulana et al., 2019).
In addition to the raw material and adhesive content, the size and shape of the particles can affect the properties of particleboard (Sackey et al., 2008). Smaller particles have larger particle surfaces for gluing, a higher number and area of interparticle contact points between adjacent particles, and closer spacing, which in turn can contribute to the overall final panel strength (Gam et al., 2012; Hristov and Vlachopoulos, 2008; Sackey et al., 2008). Owing to their high surface areas, they require more adhesive content for application. Small/fine particles produce higher internal bonding strength, but lower static bending strength than coarse particles (Hwang and Oh, 2021; Karlinasari et al., 2021; Widyorini et al., 2016b). The application of materials with a high length-to-thickness ratio (slenderness ratio) improves the bending properties compared with shorter and thicker materials (Iswanto et al., 2020; Kwon et al., 2013; Rofii et al., 2013, 2016). Hwang and Oh (2020b) and Jamaludin et al. (2020) stated that particleboard properties are influenced by the combination ratio of different particle types.
High-quality particleboard properties can be achieved by mixing particles of different shapes and sizes under optimal conditions. This study was conducted to determine the physico-mechanical properties of particleboard from sugar palm dregs with various ratios of fiber:fine particles (100:0, 75:25, and 50:50 wt%) and amounts of sucrose-citric acid adhesive (10, 15, and 20 wt% basedn air-dried particles).
2. MATERIALS and METHODS
Dregs were collected from sugar palm (A. pinnata) starch industries in Klaten, Central Java, Indonesia. The dregs were still clumped; therefore, they needed to be separated manually. They were then sieved through a 10-mesh screen. The dregs retained on a 10-mesh screen consisted of fibers with an average length of 6.84 ± 3.23 cm. The particles that passed through the 10 mesh-screen and those retained on the 60-mesh screen were referred to as fine particles, as shown in Fig. 1. All of the materials were then air-dried to a moisture content of approximately 12%. Sucrose (Meade-King Robinson, Liverpool, UK) and citric acid (anhydrous; Weifang Ensign Industry, Weifang, China) were used as adhesives at a 75/25 wt% ratio.
The dregs were ground into a powder and prepared for chemical analysis. Ethanol-toluene extractives, cold and hot water extractives, and ash contents were tested according to the American Society for Testing Material (ASTM) standards (ASTM, 2001a, 2001b, 2001c). The lignin content was determined using the Klason method and the holocellulose and alpha-cellulose contents were estimated using Wise’s chlorite method (Browning, 1967).
The sucrose-citric acid adhesive was sprayed onto the fiber/fine particles at three levels of adhesive contents (10, 15, and 20 wt% based on air-dried particles). The concentration of the adhesive solution was 50 wt%. The fiber/fine particle ratios used in this experiment were 100:0, 75:25, and 50:50 (wt%). The sprayed particles were then oven-dried at 80°C for 4 h to reduce their moisture content (Widyorini et al., 2018b).
The particles were then handformed into a single-layer mat using a forming box. The dimensions of the mat were 25 cm × 25 cm, and the target thickness was 1 cm. The mat was then hot pressed using a three-step method (Widyorini et al., 2018b) with a pressing temperature of 180°C for 10 minutes, respectively. Three replicates for each manufacturing condition were used. All boards were then conditioned under ambient conditions for approximately 7–10 days, prior to the evaluation of the mechanical and physical properties.
The boards were evaluated according to the Japanese Industrial Standard for Particleboards (JIS, 2003). The physical properties of the boards included the density, moisture content, thickness swelling (TS), and water absorption (WA). TS and WA were evaluated on a 5 cm × 5 cm × 1 cm specimen from each board after water immersion for 24 h at room temperature. The values were then calculated based on the differences in the thickness and weight of the specimens before and after water immersion.
The bending properties of the boards, i.e., the modulus of rupture (MOR) and modulus of elasticity (MOE), were evaluated by conducting static three-point bending tests on a 200 mm × 50 mm × 10 mm specimen of each board under dry conditions. The effective span and loading speed were set at 150 mm and 10 mm/min, respectively. An internal bond (IB) strength test was conducted using specimens of the same size as those used in the TS test. A universal testing machine (UTM) 3369 (Instron, Norwood, MA, USA) was used to evaluate the mechanical properties. The mechanical properties of the boards were corrected for each target density, based on the specimen densities. Each experiment was performed in triplicate.
Microscopic analysis was performed using a digital microscope (AM413ZT, Dino-Lite, New Taipei City, Taiwan) at 20× magnification. The transverse areas were captured after the IB strength test.
3. RESULTS and DISCUSSION
Table 1 lists the chemical composition of the sugar palm dregs. The results showed that the water extractive was still high, with values of 11.55% for cold water extractive and 13.15% for hot water extractive. The dregs comprised 75.9% holocellulose, 43.7% α-cellulose, 32.2% hemicellulose, and 26% lignin. These results are similar to those for the chemical components of the sugar palm trunk (Sahari et al., 2012). As reported by Sanyang et al. (2016), the high cellulose content of sugar palm fibers from the trunk provides better mechanical strength, making them potential material for particleboard applications.
The results showed that the particleboards made from the sugar palm dregs had density values that ranged from 0.73 to 0.75 g/cm2. The densities of the particleboards were lower than the target density because of the board widening after hot pressing. In addition, the moisture content of the particleboards were in the range 7.88%–8.78%, which met the JIS (2003).
The TS and WA have been considered important parameters in describing dimensional stability of the boards. Fig. 2 shows TS and the WA of the particleboard. The range of the WA of the boards was 47.0%–98.7%, whereas the range of the TS of the boards was 12.4%–49.3%, respectively. None of the TS values of the particleboards met the requirements of JIS A 5908. The TS and WA of particleboards made from teak with the same adhesive, pressing temperature, and time were approximately 15% and 40%, respectively (Widyorini et al., 2016a), whereas those of particleboards made from softwood were approximately 50% and 70%, respectively (Umemura et al., 2015). These findings suggest that differences in the properties of the raw materials also affect how adhesives and materials adhere to one another.
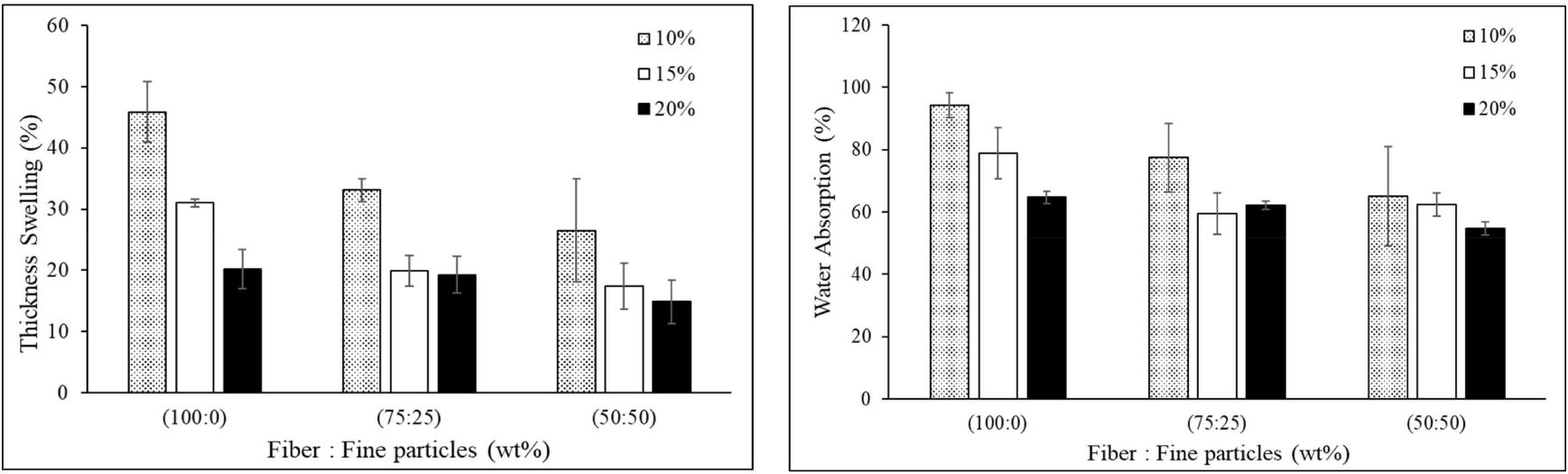
This shows that the increase in fine particles caused a decrease in the TS and WA values. This possibly occurred because the fine particles provide a larger contact area among the particles compared to the fiber, thereby resulting in stronger bonding of the particleboard, as also reported by Okuda and Sato (2004). The fine particles were in powder form; therefore, it was easy to fill the gaps between the fibers in the particleboard, as shown in Fig. 3. The results showed that fine particles provided more compact contact between particles [Fig. 3(b) and (c)] than fibers only [Fig. 3(a)]. Therefore, water may not easily break the bonds between the fibers and particles. However, the TS and WA values of the particleboard made of only coarse particles were better than those made of only fine bamboo particles (Karlinasari et al., 2021).
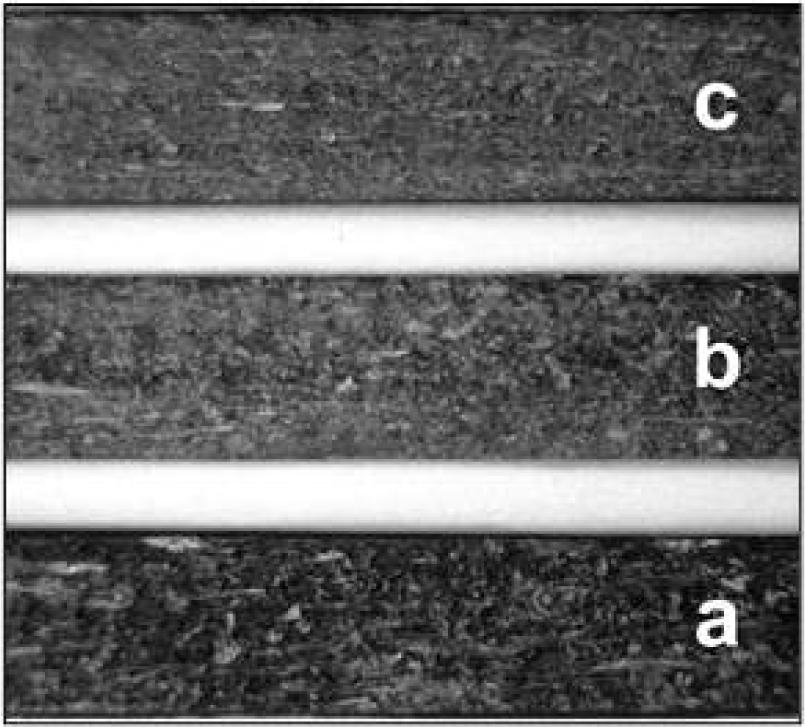
In addition, as shown in Fig. 2, increasing the resin content of the adhesive also had a significant effect on TS and WA, as reported by Widyorini et al. (2016b). Increasing the resin content made the particles more compact, resulting in higher bonding between them and lowering the TS and WA values. Generally, the main factors influencing the TS were the compressibility of the board, type of adhesive, and resin content. An increase in the resin content led to a decrease in the number of particles. A decrease in the reaction force of the compressed particles and the adhesive coating of the particles resulted in a reduction in TS (Umemura et al., 2013).
Fig. 4 shows that the value of IB strength of boards had values in the range 0.16–0.49 MPa. All the particleboards met the requirements of the eight types of JIS (2003), and several even met the requirements of all 18 types. The IB strength of teak particleboards was approximately 0.17 MPa (Widyorini et al., 2016a) and that of softwood particleboards was approximately 1 MPa (Umemura et al., 2015) with the same adhesive, pressing temperature and time. Compared with this study, the IB of softwood particleboards was relatively high, which might also be due to the resin content being 30 wt% (Umemura et al., 2015). Adhesiveness was developed by ester linkages formed from the reaction between citric acid and wood components with hydroxyl groups and furan polymers from sucrose dehydration during heat treatment (Ando and Umemura, 2021; Umemura et al., 2015; Widyorini et al., 2016a). Fig. 4 shows that increasing the resin content significantly increases the IB. As shown in Fig. 5, the transverse area of the particleboard with 50/50 wt% (fiber/particle) and 20 wt% resin content was more compact than that with 10 wt%, resulting in a higher IB value.
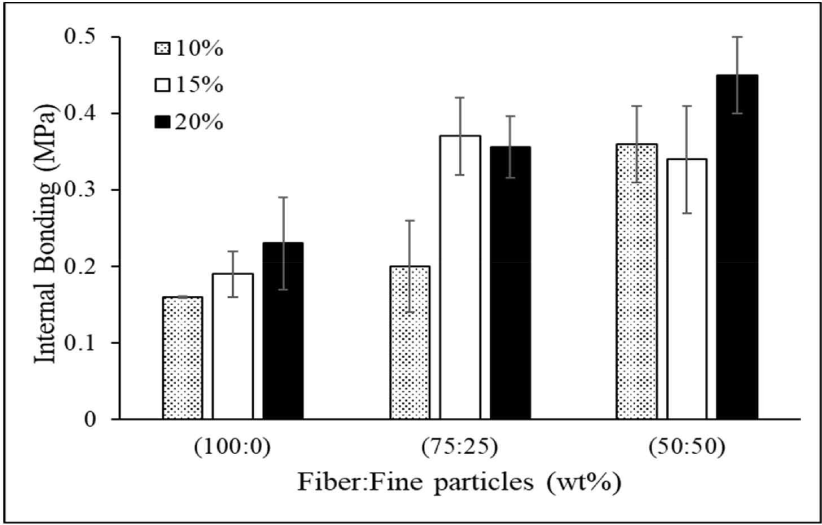
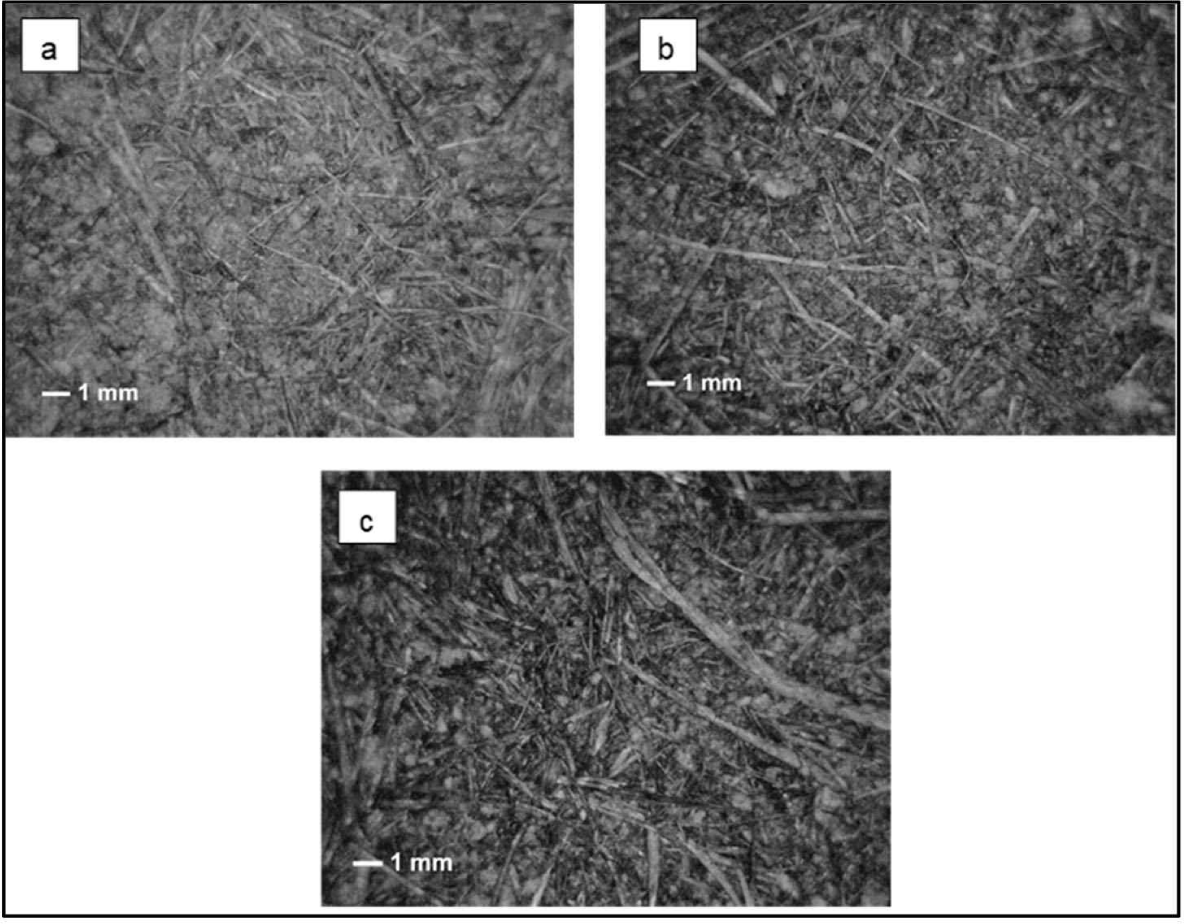
After mixing with the fine particles, the IB of the particleboard increased. At the same resin content (10 wt%), the particleboard that was made from particle ratio of fiber/particle (50/50 wt%) had an IB value more than twice compared to particleboard that was made from 100% only fibers. Interestingly, the addition of fine particles increased the bonding properties, even at a low resin content. This is probably because the fine particles fill the gaps between the fibers, resulting in a more compact and larger bonding contact area, as shown in Figs. 3 and 6. Karlinasari et al. (2021) found that boards made with coarse particles had lower IB values than those made with fine particles. It is well known that the particle size and geometry play a significant role in determining the properties of the boards. As mentioned by Umemura et al. (2015), IB strength is influenced by the adhesiveness of the inner layer of the board. In addition, fine particles that provide large surface areas are important for obtaining high internal bonding strength. This also indicates that the combination of surface area and resin content affected the properties of the board.
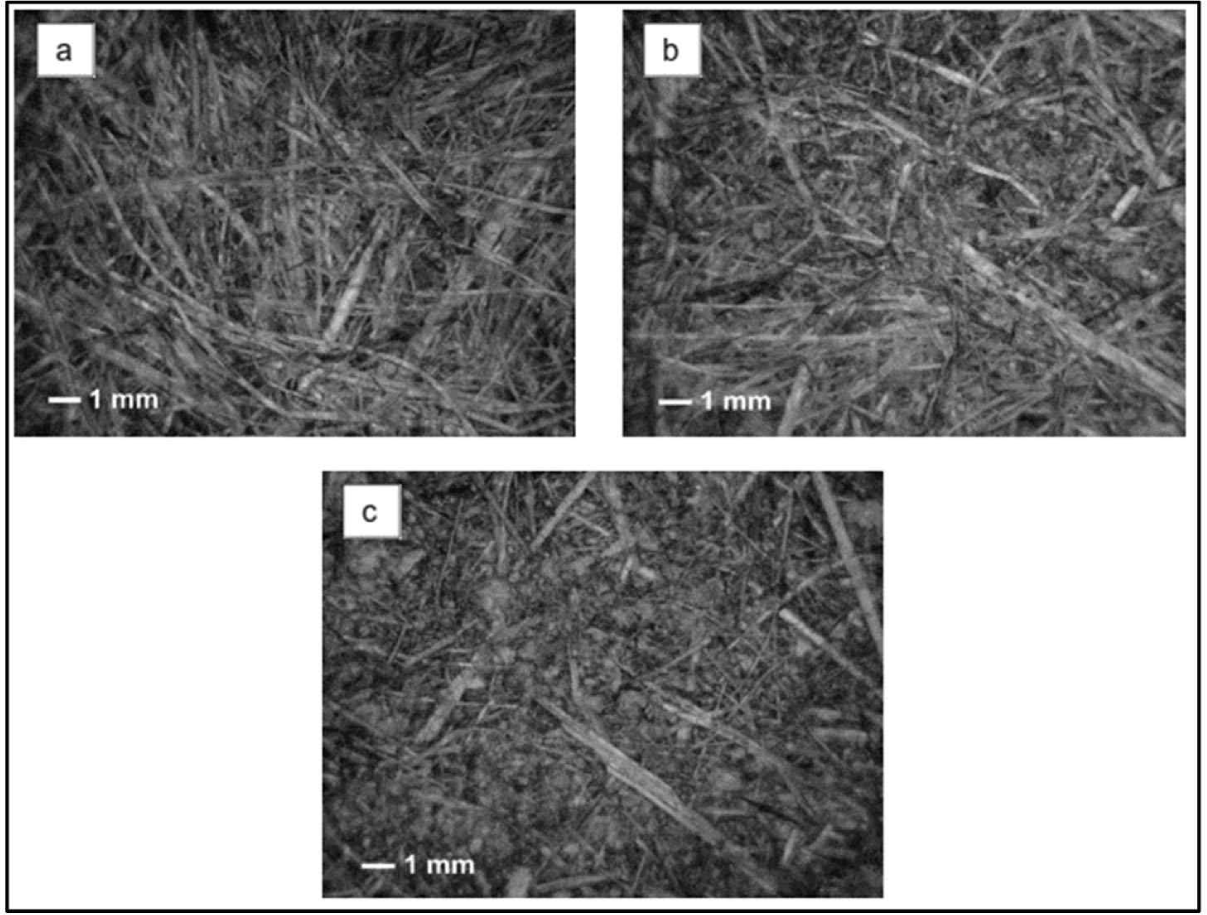
Fig. 7 shows the MOR and MOE values of the particleboard made from sugar palm dregs with various fiber/ fine particle ratios and resin contents. The MOR values were in the range 13.6–25.2 MPa, while the MOE values were in the range 2.5–4.7 GPa. The results showed that the bending strength of the particleboard increased with increasing fiber and resin content, as mentioned by Iswanto et al. (2020) and Widyorini et al. (2016b). All boards meet the requirements for Type 13 (min. 13 MPa for the MOR and 2.5 GPa for MOE) of JIS (2003). In addition, some boards with fiber/fine particle ratio (75:25) with 15% and 20% adhesive contents, as well as the board with fiber/fine particle ratio (100:0) with 20% adhesive content, met the JIS A 5908 requirement of type 18 (min. 18 MPa for MOR and 3 GPa for MOE). Under the same adhesive and pressing conditions, these boards had higher bending strengths than teak particleboards (Widyorini et al., 2016a), and were similar to softwood particleboards (Umemura et al., 2015). The MOR and MOE values of teak particleboards were around 10 MPa and 2.5 GPa, respectively, while that of softwood particleboards were around 20 MPa and 4.5 GPa, respectively (Umemura et al., 2015; Widyorini et al., 2016a). The MOR and MOE values for the isocyanate-bonded boards made from bamboo particles (Karlinasari et al., 2021) were also lower than those obtained in this study. This indicated that the dregs of A. pinnata starch industry could be a prospective material for particleboard.
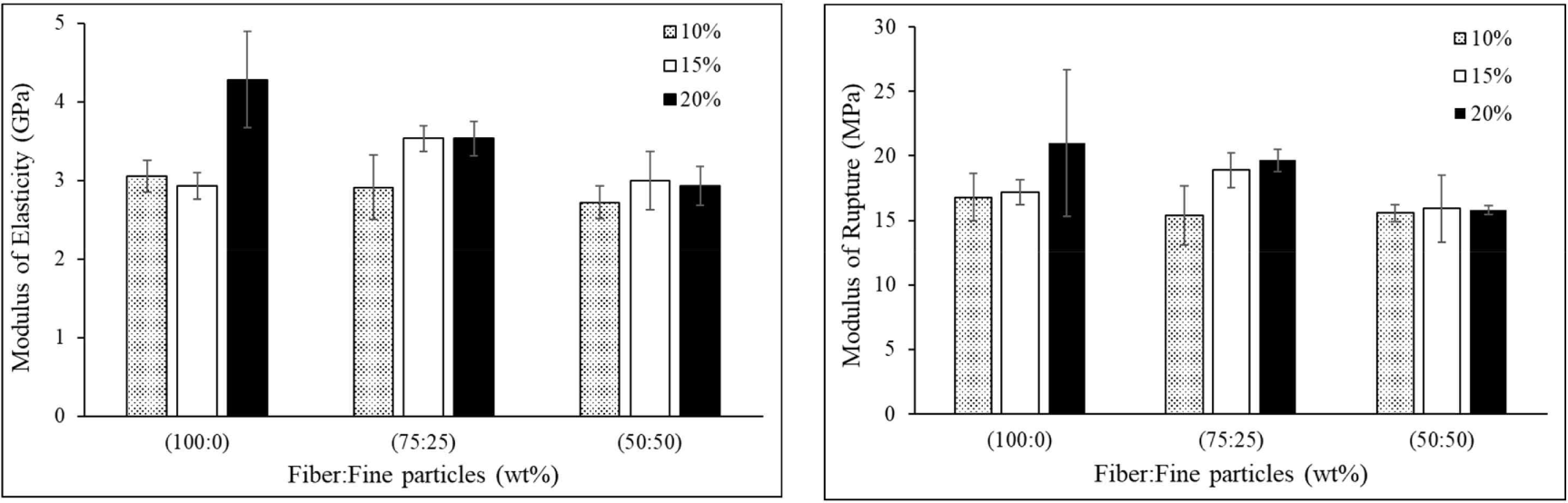
4. CONCLUSIONS
In this study, sugar palm dregs were used as the material for creating particleboard. The dregs consisted of short fibers and powder/fine particles. The properties of particleboards made from different compositions of fiber and fine particles, as well as different resin contents, were evaluated. Increasing the fine particle and resin content could reduce the TS and WA values and increase the IB strength of boards made from sugar palm dregs. The fine particles appeared to fill the gaps between the fibers in the particleboard, resulting in good compatibility. However, the fibers exhibited a higher bending strength than the fine particles. Therefore, a high-performance particleboard can be produced by combining the composition ratio of fiber/fine particles and resin content. In this study, particleboards made from fiber/fine particles (75:25 wt%) and adhesive content of 15 wt% and 20 wt% had mechanical properties that met the requirements of JIS A 5908 type 18.