1. INTRODUCTION
Noise pollution is becoming more prevalent with urbanization and industrialization (He et al., 2021; Jang et al., 2018). Noise pollution is known to cause heart disease, as well as psychological harms such as stress and insomnia (Jariwala et al., 2017). Comprehensive and efficient noise management is required to solve these issues. The increased use of sound-absorbing materials is an easy and reliable alternative to noise reduction efforts (Kang et al., 2019; Sharma et al., 2020).
Traditional sound-absorbing materials include urethane foam, rock wool, and glass fiber (Jang and Kang, 2021a). While these materials reduce noise pollution, they also make to another environmental issue. Accordingly, eco-friendly sound-absorbing materials that use agricultural by-products have been suggested as an alternative that do not environmental problems (Jang and Kang, 2021b).
Quality eco-friendly sound-absorbing materials include coconut fiber (Rozli et al., 2010), kenaf fiber (Lim et al., 2018), rice straw (Kang et al., 2018), rice husk (Wang et al., 2019), and wood products (Jang and Kang, 2021c, 2021d; Kolya and Kang, 2021). Besides that, various agricultural by-products have also been studied recently as potential eco-friendly sound-absorbing materials.
Do et al. (2020) investigated the sound absorption performance of flexible cellulose aerogels derived from pineapple waste. As the concentration of pineapple fiber aerogels increased while height remained constant, the sound absorption coefficient increased, and an optimal noise reduction coefficient (NRC) value was found at 2.0 wt% content.
Soltani et al. (2020) investigated the sound absorption performance of Yucca gloriosa fibers. The sound absorption coefficient of their 15 mm thick sample increased up to a frequency of 4,000 Hz, reaching a peak value of 0.96, and then decreased sharply. For their 30 mm thick sample, the sound absorption coefficient increased up to 2,500 Hz, reached a peak value of 0.96, then decreased significantly at 4,000 Hz to near 0.75, then increased again after that.
Gadea Borrell et al. (2020) reported the sound absorption performance of four different varieties of fruit stone waste (olive, cherry, apricot, peach). The sound absorption performance of the fruit stones varied depending on their shape and size. The sound absorption coefficient at low frequencies tended to rise as the height increased. The maximum sound absorption coefficient of a peach stone was 0.74 at 1,610 Hz, while that of the olive stones was 0.7 at 725 Hz. For cherry stones it was 0.88 at 796 Hz. The apricot stone had the best sound absorption performance among the four species examined; 0.94 at 1,000 Hz.
Peanuts are a sustainable agricultural product that are estimated to be grown on over 26 Mha worldwide. The total production of peanuts is estimated to be over 45 Mt each year (Rachaputi et al., 2021). Previous studies have examined the use of peanut shells as lignocellulose biomass. Bai et al. (2020) reported that charcoal made from peanut shells had abundant oxygen-containing functional groups and hierarchical porous structures. As a result, peanut shell charcoal successfully removed 96.5% of Pb2+ and 97.1% of methylene blue from water. Wang et al. (2020) developed a porous carbon filter by impregnating copper in activated carbon made from peanut shells. This filter’s maximum absorption capacity was reached 97.63 mg/g and showed the optimum performance for H2S adsorption.
This study focuses on the use of peanut shells as an eco-friendly sound-absorbing material. Malawade and Jadhav (2019) investigated the sound absorption performance of boards made from peanut shells and yellow dextrin powder. The optimal sound absorption coefficient of 0.72 at 4,500 Hz was achieved with a 70:30 weight ratio of peanut shell and yellow dextrin.
To date, no study has been conducted on the sound absorption performance of pure peanut shells. The previously tested boards necessarily contained a binder that blocked some pores and negatively affected sound absorption. In contrast, this study analyzed the sound absorption performance of pure peanut shells. The aim of this study is to examine the possibility of using peanut shells as environmentally-friendly sound-absorbing materials.
2. MATERIALS AND METHODS
Fig. 1 shows the preparation of the peanut shell samples used in this study. Peanuts were purchased from a wholesale agricultural market (Incheon, Korea). The shells and grains were separated, and the shells were crushed in a mortar to increase their density.
To observe the surface properties of the peanut shells, a SEM (Genesis-1000, Emcraft, Gwangju, Korea) was used to image the external, internal, and cross-section surface of the peanut shell samples at 3,000×. The cross-section surface was additionally observed at 200×.
This study used an impedance tube (Type 4206, Brüel & Kjær, Nærum, Denmark) to which the transfer function method was applied based on ISO 10534-2 (ISO 10534-2, 2001). Fig. 2 shows a schematic diagram of an impedance tube being to measure the absorption coefficient of peanut shells. In general, an impedance tube is used horizontally (Kang et al., 2021). However, as a frame was not used to evaluate the sound absorption performance of pure peanut shells in this study, the sound absorption coefficients were measured by standing the impedance tube vertically.
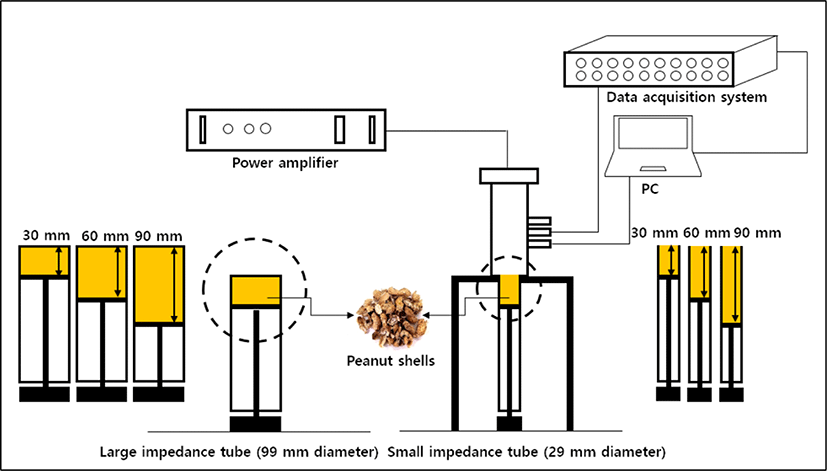
Typically, a small impedance tube with a diameter of 29 mm is used for the low-frequency region below 1,600 Hz, while a large impedance tube with a diameter of 99 mm is used for the high-frequency region between 500 Hz and 6,400 Hz. In this study, these two impedance tubes were used.
Peanut shells were placed into two impedance tubes with height of 30, 60, and 90 mm, respectively. Their bulk density was constant at 0.1 g/cm3. The NRC was calculated by averaging the sound absorption coefficients at 250, 500, 1,000, and 2,000 Hz. Sound absorption coefficients of 250, 500, and 1,000 Hz were obtained with the large impedance tube, while a sound absorption coefficient of 2,000 Hz was obtained when a small impedance tube was used. The sound absorption coefficient of all samples was measured three times, and the average value was recorded.
3. RESULTS and DISCUSSION
Fig. 3 shows SEM images of the surfaces of the peanut shell depending on their direction. The outer surface was rough with projections, while fibers were visible on the inner surface. Macropores were not observed on either the inner or outer surfaces, though void volumes were observed on the surface of the cross-section images. These spaces improved the porosity of the peanut shells.
Fig. 4 represents the results of the sound absorption coefficient measurements as assessed using the impedance tube. Fig. 4(a) depicts the result measured using the large impedance tube. Fig. 4(b) depicts the results measured using a small impedance tube. The sound absorption coefficients at 200, 500, 1,000, 2,000 Hz, and NRC are shown in Table 1.
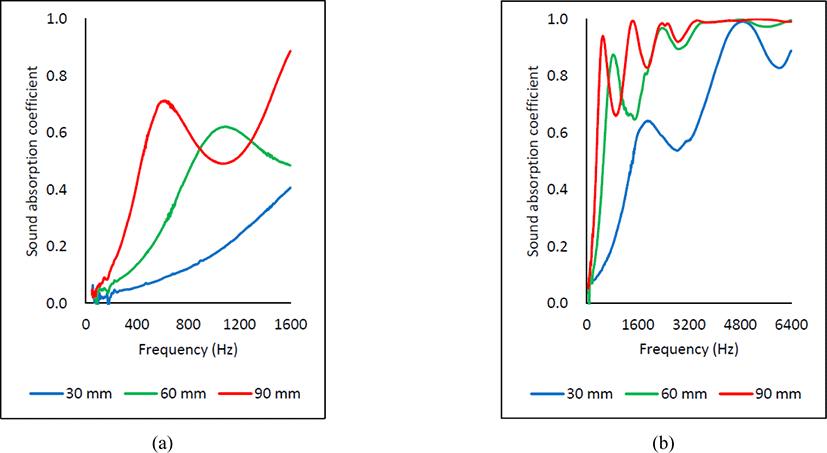
The sound absorption coefficient increased with filling height. The NRCs were 0.230 for the 30 mm height, 0.433 for the 60 mm height, and 0.544 for the 90 mm height. Peanut shells in the 60 and 90 mm filling height in impedance tubes achieved an average sound absorption coefficient of 0.9 above 2,000 Hz. The rough surfaces of peanut shells and the void volume of the cross-sections reduced sound energy. Moreover, the thicker the peanut shells, the better the sound absorption performance, particularly at low frequencies. Sound absorption is caused by the viscosity of air contained within the interconnected voids that separate the peanut shells. This complex void structure also affects sound energy absorption within the material. Therefore, the thicker the peanut shells, the more space the sound is able to penetrate, and the more improved sound absorption performance. This phenomenon is a typical characteristic of a fibrous sound-absorbing material (Cao et al., 2018).
Zhu et al. (2014) investigated the NRC of natural materials. This study compared the NRC of peanut shells with the results of Zhu et al. (2014), who investigated NRC at 50 mm height. As we did not test NRC at 50 mm height, NRC was inferred from a regression equation (Fig. 5).
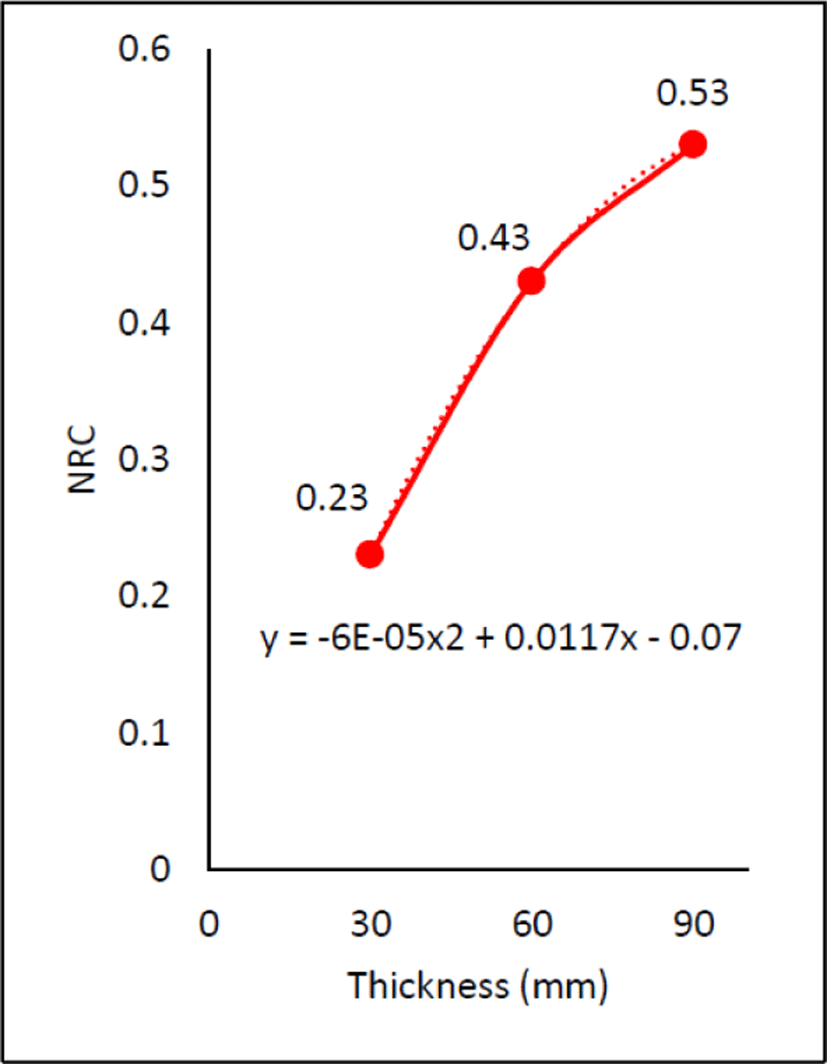
As reflected in Fig. 6, although peanut shells had lower NRC than ramie, flax, and cotton, they showed equivalent or improved sound absorption performance to bamboo, sisal, jute, and wool. In sum, the peanut shells investigated in this study may have a use as an environmentally friendly sound-absorbing material.
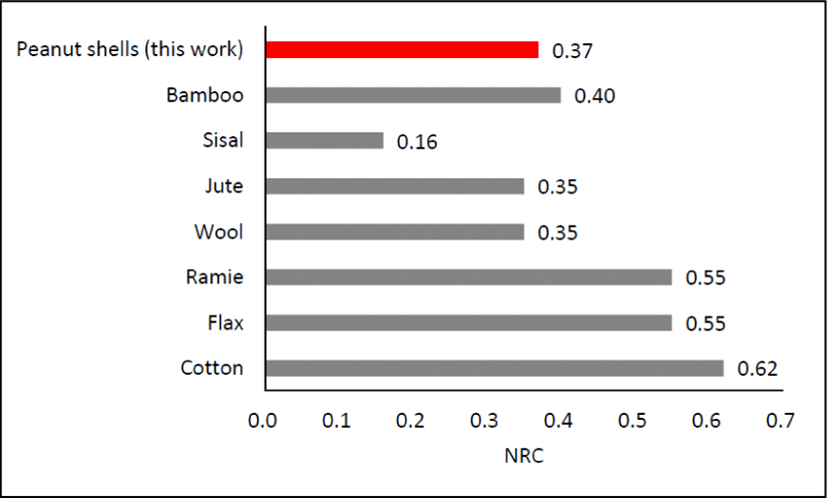
4. CONCLUSIONS
In this study, the sound absorption coefficients of pure peanut shells were investigated using the impedance tube technique. The sound absorption coefficient increased with height of impedance tube, and their NRCs were 0.23 for a 30 mm height, 0.43 for a 60 mm height, and 0.54 for a 90 mm height. Notably, above 2,000 Hz the sound absorption coefficient of peanut shells with a height of 60 mm and 90 mm reached an average of 0.9. The sound-absorbing performance was good enough to warrant their consideration as an environmentally friendly sound-absorbing material candidate. This study suggests that these sound-absorbing features may contribute to the high added value of peanut shells.