1. INTRODUCTION
The depletion of finite resources including fossil fuels and the environmental load caused by the non-degradability of plastic materials continue to threaten human life (Ahn et al., 2021; Ghani and Lee, 2021; Hadi et al., 2022; Jang, 2022; Park et al., 2020b). From the point of view of carbon-based eco-friendly alternative materials, wood-derived materials are strongly attractive because of their abundance, excellent strength, and various application possibilities (Calvo-Flores and Dobado, 2010; Kai et al., 2016; Lee et al., 2021). These wood-based materials have been actively used in various processing from the beginning to pulp and paper, construction, and furniture materials in human’s common life. However, most lignocellulose-based materials, including wood, paper, and wood particle board, have been limited in their use because they have weak structural stability against moisture, among various external environments (Fabiyi et al., 2011; Park et al., 2020a; Rowell and Bongers, 2017). Water molecules accelerate wood material deterioration and shorten its service life. Wetting protection is, therefore, a key issue in wood finishing. Ideally, the wood finish should effectively prevent the ingress of external water while preserving the inherent bio-based properties of wood-originated versatile materials.
Various methods such as chemical modification, heat treatment, and the use of coatings and finishes have been proposed to prevent deterioration of wood from moisture exposure (Bekhta and Niemz, 2003; Esteves et al., 2006; Esteves and Pereira, 2009). However, the use of fluorine compounds, inorganic substances (Li et al., 2010; Liu et al., 2013), or toxic chemicals as coatings or penetrating finishes can overcome the moisture vulnerability of wood, but greatly undermine the environmental friendliness of wood materials (Cho et al., 2011; Park and Jo, 2020; Wang et al., 2021). Therefore, the need for a natural material-based hydrophobic coating that can improve the moisture vulnerability while ensuring the eco-friendliness of wood is increasing day by day. In this respect, lignin, which is a wood-based biopolymer and the second most abundant on earth after cellulose (Azadfar et al., 2015; Calvo-Flores and Dobado, 2010; Fatriasari et al., 2020; Qian et al., 2015), has great potential as a raw material used as a hydrophobic material for wood protection. Because lignin is composed of phenol propane monomer, it contains hydrophobicity due to benzene ring and at the same time, it is possible to realize strong interaction with wood surface based on abundant phenolic and aliphatic hydroxyl groups (Lee et al., 2019). However, the chemical modification process, such as esterification, which is most attempted to increase the hydrophobicity of lignin (Alwadani et al., 2021; Liu et al., 2021), consumes energy for the chemical reaction, and at the same time contains a disadvantage of using an additional organic solvent. Therefore, a more environmentally friendly and efficient lignin-based hydrophobizing agent manufacturing process should be proposed.
The main purpose of this study is to propose a hydrophobic wood coating agent by blending kraft lignin, representative technical lignin, and carnauba wax, an eco-friendly and edible plant-based hydrophobic agent. The chemical properties and morphology of the coating agent when lignin/carnauba wax blends, were observed through fourier transform infrared (FTIR) and field emission scanning electron microscopy (FE-SEM). Finally, the effect of the lignin addition on the coating performance of the lignin/carnauba wax blend coatings was confirmed through contact angle (CA) measurement, durability test, and micro-roughness analysis.
2. MATERIALS and METHODS
Kraft lignin was kindly provided by Moorim P&P (Ulsan, Korea). Carnauba wax was purchased from the local market. Ethanol was an analytical grade reagent and was purchased from Daejung chemicals and metals (Siheung, Korea).
The preparation of the kraft lignin/carnauba wax blend coating solution proceeds in the following order: First, 2 g of carnauba wax is put in 20 mL of ethanol, and then heated to 80°C and stirred for 20 minutes. And 2 g of kraft lignin is put in 20 mL of the previously prepared solution, and then heated to 80°C and stirred for 20 minutes.
The kraft lignin/carnauba wax blend coating solution was applied using an airbrush. A certain amount of the coating solution is poured into the solution reservoir of the airbrush. After that, it was applied to plywood or slide glass using an air pressure of 50 psi at 30 cm. After the coating solution was applied, it was dried in an oven at 60°C for 24 hours.
The morphological properties of kraft lignin/carnauba wax blends were characterized using FE-SEM (SUPRA 55VP, Carls Zeiss, Oberkoche, Germany). The sample was prepared by spraying the coating solution on the silicon wafer and drying. The dried silicon wafer was placed on carbon tape and coated with platinum using a sputter coater (EM ACE200, Leica, Wetzlar, Germany). The surface morphology of kraft lignin/carnauba wax blends was imaged with beams at a voltage of 2 kV. A 3D non-contact surface profiler (NANO View-E1000, Nanosystemz, Daejeon, Korea) was used to compare the roughness of the wax coating layer and the kraft lignin/ wax blend coating layer. Each sample was measured after spraying the coating solution on the slide glass and drying it in an oven at 60°C for 24 hours. FTIR (NicoletTM Summit FTIR Spectrometer, Thermo Fisher Scientific, Waltham, MA, USA) was measured after drying to confirm the functional group change of the wax coating solution and the kraft lignin/wax blend coating solution. The FTIR spectra were obtained in the spectral range of 4,000–700 cm–1, and the number of scans and scan resolution were 64 and 4 cm–1, respectively, in ATR mode. To evaluate the wettability of the coating layer, a contact angle analysis was performed. To test the durability of the coating solution, the coating solution was sprayed on paper and dried in an oven at 60°C for 24 hours. After that, using scotch tape, peeling and attaching was repeated 10 times, and contact angles and pictures were taken.
3. RESULTS and DISCUSSION
Carnauba wax is a naturally derived ester wax extracted from the leaves of the carnauba palm tree. This wax is consisted of multiple chain length fatty acid esters, fatty alcohols, acids and hydrocarbons. Among them, C26 acid and C32 alcohol are predominantly present (Bayer et al., 2011). In this study, to explore the potential and role of lignin as a hydrophobic coating, technical kraft lignin was blended with carnauba wax, an eco-friendly conventional coating. The mixing ratio of wax and lignin was fixed at 1:1 (wt/wt). Fig. 1 shows the FTIR spectra of kraft lignin, carnauba wax as raw materials, and kraft lignin/carnauba wax blend to be used as a hydrophobic wood coating. As shown in the figure, in the case of carnauba wax, strong peaks indicating alkyl chains at 2,900 and 2,800 cm–1 are observed. Otherwise, kraft lignin exhibits small peak intensities for 1,272 and 1,033 cm–1 denoted G units and moderate absorbances for (1,324 and 1,125 cm–1) denoted S units (Shi et al., 2019). In addition, a broad peak at 3,500–3,000 cm–1 is also observed due to the presence of hydroxyl groups in lignin. Meanwhile, in the case of the prepared hydrophobic coating, not only the characteristic peaks indicated by the alkyl chain of the wax but also the peaks indicating the G and S units of lignin and the hydroxyl group can be observed. A chemical shift of the characteristic peaks of lignin and wax occurred without the occurrence of new characteristic peaks, indicating that the interaction between lignin and carnauba wax occurred by hydrogen bonding. In addition, it can be predicted that hydrogen bond-based interaction with the wood surface and kraft lignin/wax coating is possible through the presence of hydroxyl groups (3,500–3,000 cm–1) that are expressed relatively strongly compared to kraft lignin.
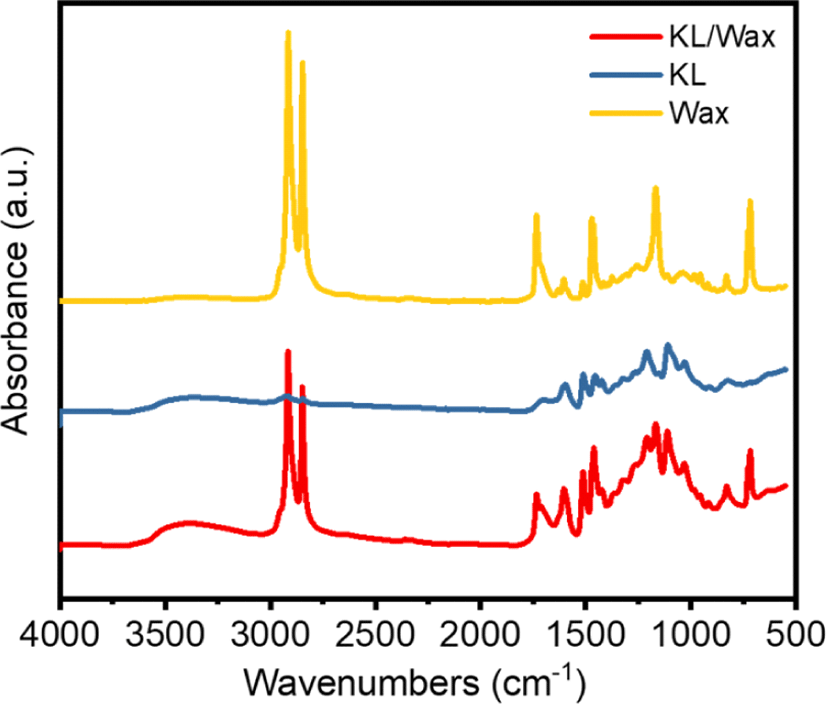
To impart hydrophobicity to the object in the coating process, not only the hydrophobicity of the coating reagent itself but also the surface morphology after the coating process is important (Coffinier et al., 2013; Nguyen et al., 2021; Quéré, 2008). Hydrophobic effect due to surface roughness can be realized by introducing hierarchical micro-and nano-scale structures. This surface morphology can affect not only the short-term contact angle of the coating surface but also the long-term moisture wettability (Quéré, 2008). The carnauba wax/lignin coating was sprayed on the silicon wafer substrate, and the morphology of the applied coating was observed through FE-SEM, and the results are shown in Fig. 2. The surface of the silicon wafer was smooth as shown in the figure, and sub-micron-sized particles present everywhere are expected to be impurities. On the other hand, when carnauba wax is sprayed, it is applied as an emulsion and is present in the form of microparticles on the silicon wafer surface, which means that it is difficult to form a uniform coating layer. On the other hand, when carnauba wax/lignin blend coating was sprayed, the particle size was significantly reduced compared to the pristine carnauba wax emulsion. In addition, continuous microparticle connection was observed, and as a result, a coating layer was uniformly formed on the silicon wafer substrate. The formation of such a uniform coating layer means that the lignin can act as a stabilizer of the wax emulsion to reduce the particle size, and the lignin present around the wax particles can implement a continuous micro-scale rough surface.
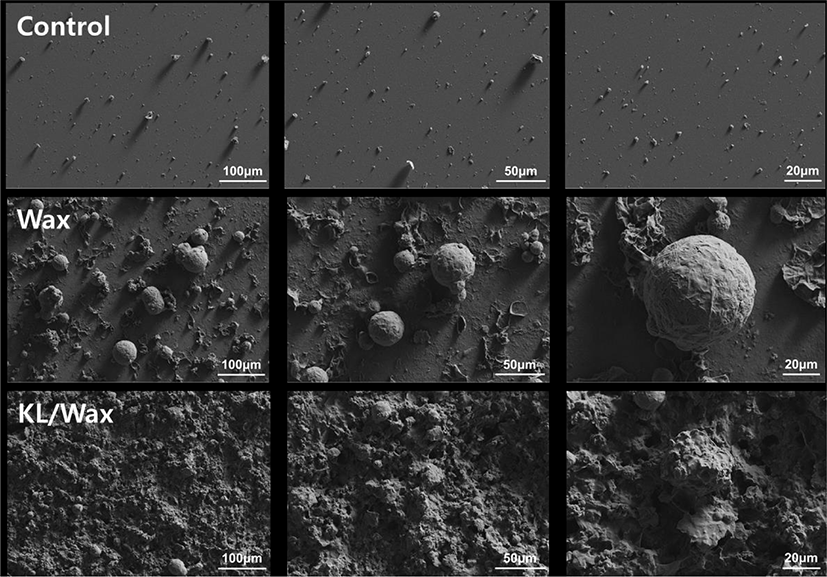
Wettability is the most important evaluation item for hydrophobic coatings. To evaluate the hydrophobicity of the lignin/carnauba wax coating, the initial contact angle, and the change in contact angle with residence time was evaluated by sessile drop technique, and the results are shown in Fig. 3. The uncoated wood raw material showed a low contact angle of 80 degrees, which means that the surface has a relatively hydrophilic property. The carnauba wax-coated wood surface showed a contact angle of 145 degrees, which is attributed to the change in surface energy and surface roughness due to the presence of alkyl chains (Budnyak et al., 2018; Vidal et al., 2019), a component of carnauba wax. On the other hand, in the case of the lignin/carnauba wax blend coating, it can be seen through the contact angle of 144 degrees that the hydrophobization effect caused by the carnauba wax is not inhibited even though the blend ratio is 50:50. On the other hand, in the case of the carnauba wax-coated surface, the contact angle decreased by 17% for 1 minute, whereas in the case of kraft lignin/wax, only a decrease of 3% occurred. This means that the addition of lignin can help suppress the wetting of the wood surface over time. Since lignin has a relatively hydrophilic characteristic compared to carnauba wax, it can be expected that the wetting inhibitory effect by the addition of lignin is probably due to the change in the roughness of the coating layer.
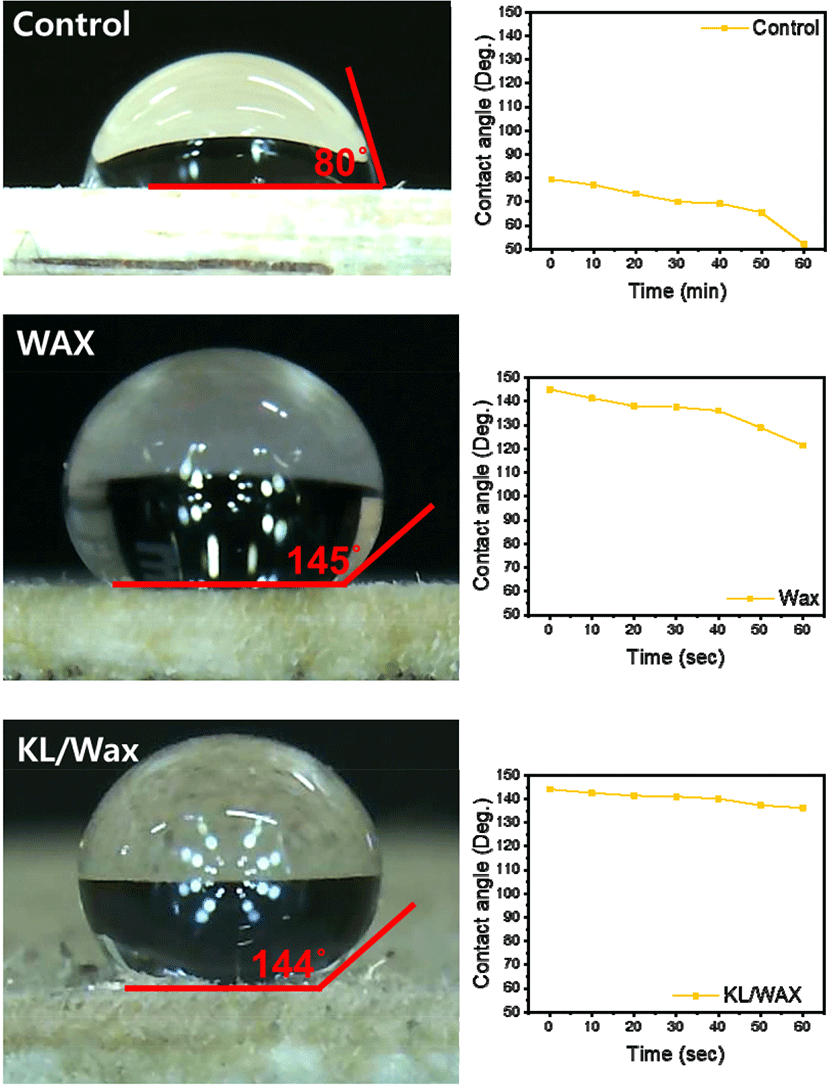
In order to examine the morphology, change of the kraft lignin/wax blend coating layer according to the addition of lignin, the coating layer was observed with a 3D non-contact surface profiler. Fig. 4(a) and (c) shows a 3D image (0.14 mm × 0.10 mm) of the surface of the coating layer, so that the 3D morphology can be directly understood through the height change. Fig. 4(b) and (d) are two-dimensional line scan routes along the x-z axis. In the case of the carnauba wax coating layer of Fig. 4(a) and 4(c), micrometer-scale surface roughness was observed locally, but the smooth surface of the substrate was maintained overall. This is similar to the FE-SEM result, because the wax-coated surface did not form a uniform layer and the wax micro-particles were discontinuously covering the surface. On the other hand, in the case of kraft lignin/wax, the surface roughness was increased compared to the wax coating layer, and in particular, a rough surface of a micrometer scale was formed. This is similar to the results of surface morphology results from the SEM images, and this increase in surface roughness is probably the main reason for the increase in wetting resistance mentioned above (Le et al., 2016; Quéré, 2008).
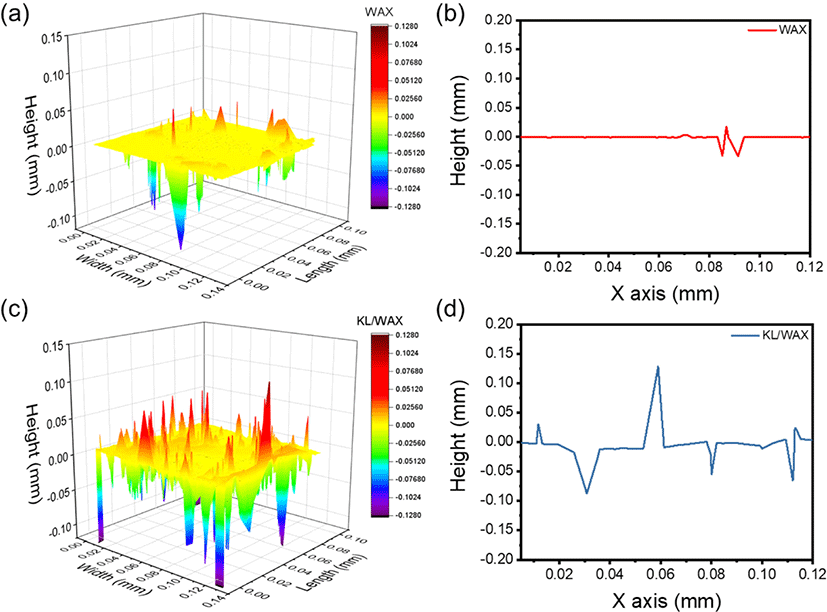
Resistance to external stimuli, including heat and friction, as well as hydrophobicity, are important factors in the properties of wood coatings. In order to evaluate the stability of the coating layer according to external friction, repeated adhesion and detachment using an adhesive tape were performed, and changes in the surface and contact angle of the coating layer were evaluated. As shown in the Fig. 5, in the case of the wax coating layer, damage to the coating layer on the surface can be easily observed with the naked eye as the number of adhesion and desorption increases, and the surface contact angle is also greatly reduced from 145 degrees to 122 degrees. On the other hand, in the case of the kraft lignin/wax coating layer, damage to the surface coating layer was significantly reduced, and a high contact angle of 136 degrees was maintained even after repeated attachment and detachment 5 times. This proved that kraft lignin can be an effective additive capable of enhancing the physical stability of a single coating composed of general wax. The enhancement of the physical stability of the kraft lignin/wax coating layer is because kraft lignin is capable of hydrophobic interaction with carnauba wax as well as strong hydrogen bonding with the wood surface (Jiang et al., 2016; Rowell, 2021).
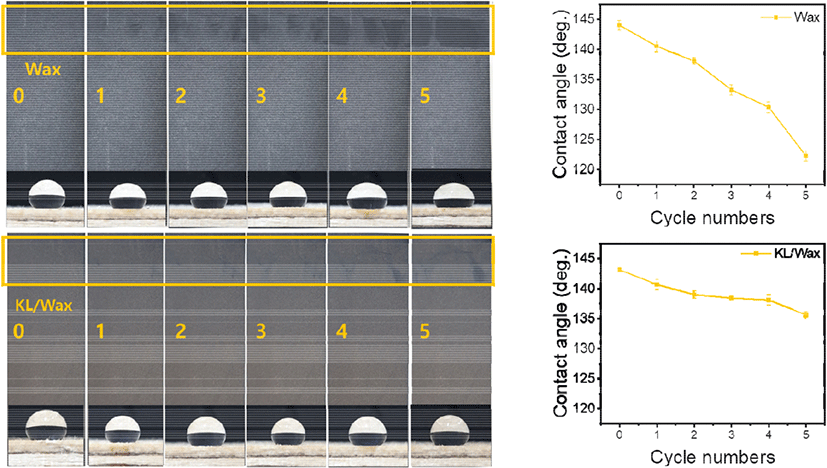
4. CONCLUSIONS
Bio-based coatings can be an excellent alternative to ensure the safe and sustainable requirements of the coating industry. To date, various oils and waxes have been used as traditional wood coatings, but they often lack sufficient durability. Meanwhile, lignin has been studied for application to hydrophobic coatings so far, but it has been accompanied by complex processing processes such as chemical modification and the introduction of inorganic particles. In this study, a bio-based wood surface coating was prepared using kraft lignin, representative technical lignin, and natural carnauba wax. It was confirmed that the kraft lignin/wax coating could be obtained through simple blending without any surface reaction, and the addition of lignin did not inhibit the unique hydrophobicity of wax. In addition to this, the addition of lignin increased the micro-roughness of the coating layer to achieve wetting resistance. It was found that the physical stability of the coating layer also increases because the finally added lignin can have a strong interaction with the wood surface layer. This study presents a fundamental potential for the future application of lignin as a bio-coating.