1. INTRODUCTION
The availability of raw materials by natural forests and community forests is no longer able to meet the needs of the wood processing industry. This is caused by deforestation and slow growth of wood. These conditions encourage efforts to use fast-growing plants as wood substitutes to continue to meet needs. One of the fast-growing plants that has a high level of production in Indonesia is bamboo.
Indonesia is one of the biggest bamboos producing countries in Asia. As many as 37% of bamboo production in Indonesia comes from Java (Central Bureau of Statistics, 2016). Bamboo is a fast-growing species that can be harvested after 3–4 years. Characteristics the direction of the fiber end of the bamboo end parallel has good mechanical properties and high elasticity in fiber direction (Galih et al., 2020). However, bamboo has sections and nodes that are not homogeneous and there are cavities with a certain diameter related to the dimensions in their use (Dungani et al., 2016; Kim et al., 2003; Sharma et al., 2014). Therefore, modifications are needed to use bamboo as a substitute for wood, both structural and non-structural. One dimensional modification that can enhance bamboo by bamboo laminate boards.
Lamination is the process of combining two types of material or more that are not the same type. Bamboo laminates can be composed of several sheets of zephyr and crushed before being arranged into boards (Nugroho and Ando, 2001). Bamboo composites can be arranged parallel to the fibers and bonded using isocyanates and cold pressing (Subyakto et al., 2016). The results showed that the composition of bamboo has properties and mechanics that can meet the requirements as raw materials for use in an environmentally friendly room.
The use of bamboo layers as the outer layer of boards can improve mechanical quality (Galih et al., 2020; Maulana et al., 2019). However, the resulting board has a high weight. As needed, there is a layer in the core of the board using other fast-growing wood, such as falcata wood (P. falcataria (L) Nielsen). To maximize the use of falcata wood, falcata veneer can be used as a raw material.
In the preparation of bamboo laminate boards, if the raw materials of the compilers are bonded in the direction of the fiber parallel, the resulting product will tend to become curved or uneven. This certainly can complicate the use of the product. To overcome this problem, in making bamboo laminate boards it is necessary to arrange perpendicular to the layers. Kariuki et al. (2015), has conducted research on laminated bamboo with variations in orientation of the fiber. The results showed that the arrangement of the fiber direction could influence the mechanical properties of bamboo laminates.
In addition to the raw material making up the board, the adhesive is an important factor determining the mechanical properties of the laminated board (Dunky et al., 2002; Roh et al., 2004). The choice of adhesive type in the manufacture of laminated board will be easier if it has a short pressing time, while still producing good product quality. The isocyanate type adhesive is an adhesive that meets these criteria (Wen et al., 2020).
The objective of this study was to determine the effect of the arrangement of the direction of the fibers and constituent materials on the hybrid bamboo laminate board on physical and mechanical properties.
2. MATERIALS and METHODS
The materials used in this study were 4-years-old tali bamboo (G. apus (J.A. & J.H. Schultes) Kurs) and falcata veneer (P. falcataria (L) Nelsen) with a thickness 2 mm. Bamboo was obtained from smallholder plants in Tanjungsari, Sumedang, West Java. Falcata veneer was produced from plywood industry in Tangerang, Banten, Indonesia and water-based isocyanate polymer (WBPI) with two components was used as an adhesive.
Fresh bamboo culms were cut along around 40 cm. Bamboo is preserved by soaking using 5% borax solution (Na2B4O7 · 5H2O) for 7 days. The preserved bamboo culm is crushed first to form flat sheets with an axe. Bamboo zephyr is planned on the outside and inside with a planer machine. Furthermore, zephyr is dried at room temperature to reach 20% of moisture content. The target thickness of the zephyr layer is 0.7 cm. Then, cut and arranged into zephyr bamboo sheets of length and width of 40 cm.
Bamboo laminate boards were made with size of 40 cm × 40 cm × 1.6 cm (length × width × thickness) with variation fiber direction and core layer as shown in Table 1 and Fig. 1. Zephyr and hybrid bamboo laminate boards are arranged in 3 layers. In the hybrid laminate board, 2 layers of falcata veneer cores are used which are arranged parallel to each other. The WBPI were used as adhesive with a ratio of adhesive to hardener is 100:15 (g). The glue spread rate is 300 g/m2 for zephyr bamboo and 170 g/m2 for the falcata veneers. The bamboo laminate board is then cold pressed with a pressure of 22.2 kgf/cm2 for 1 hour. The bamboo laminate board is conditioned for 7 days before testing.
Fiber direction | Face/back | Core | Layers |
---|---|---|---|
Parallel (LBL) | Bamboo Zephyr | Bamboo zephyr | 3 |
Falcata veneer (Hybrid) | 4 | ||
Perpendicular (Ply-bamboo) | Bamboo zephyr | 3 | |
Falcata veneer (Hybrid) | 4 |
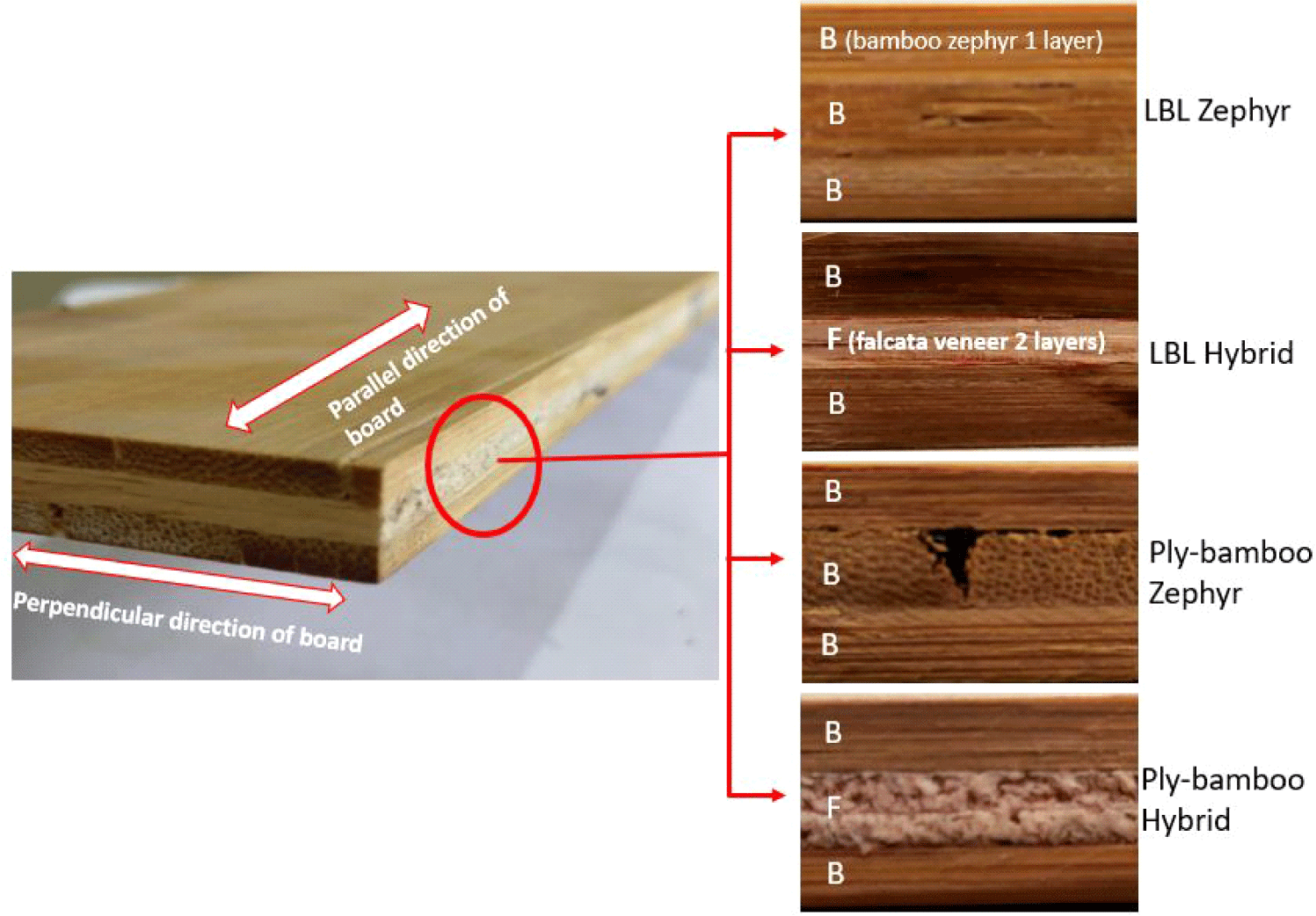
Before testing, the samples were conditioned in a room at a relative humidity of 65% and a temperature of 25°C. Moisture content, density and delamination were evaluated according to Japanese Agricultural Standard (JAS 003, 2014). Whereas, dimensional stability is measured using 3 ways namely dimensional changes, water absorption (WA) and thickness change (TC). Dimension changes were carried out by immersing the sample for 24 hours and then drying in an oven at a temperature of 103 ± 2°C to constant (Equation 1 and 2), while the WA test was determined based on changes in weight for 72 hours measured every 2 hours in the first 6 hours and every 24 hours. The TC was caried out by the thickness after pressing and thickness after condition at room temperature (Equation 3).
Where Sw is thickness swelling (%), Sr is thickness shrinkage (%), T0 is board thickness before water soaking, T1 is board thickness after water soaking for 24 hours, T2 is board thickness after oven at temperature 103 ± 2°C to constant.
Where TC is thickness change (%), Tc0 is board thickness after pressing (cold pressed with a pressure of 22.2 kgf/cm2 for 1 hour), Tc1 is board thickness after conditioning at room temperature for one week.
Mechanical test include modulus of rupture (MOR), modulus of elasticity (MOE), screw withdrawal strength and shear strength. The determination of MOE/MOR LBL was completed on the flat and edge tests (Fig. 2) of the sample according to JAS (2013) for laminated veneer wood. Then, the determination of the MOE/MOR of the bamboo-ply-board according to JAS for plywood in the long (parallel with face layer direction of board) and cross (perpendicular with face layer direction of board) directions of the sample follows JAS (2014) for plywood. The shear strength test of ply-bamboo with size 81 mm × 25 mm according to JAS for plywood standard. Whereas, the Laminated Bamboo Lumber (LBL) Horizontal shear strength was carried out in two directions of testing, edge direction (99 mm × thickness) and flat direction (81 mm × 39 mm) according to the JAS standard for laminated veneer lumber. The withdrawal strength was conducted with a sample size of 5 × 10 cm and a screw depth of 0.7 mm according to SNI 03-2105-2006 (SNI, 2006).
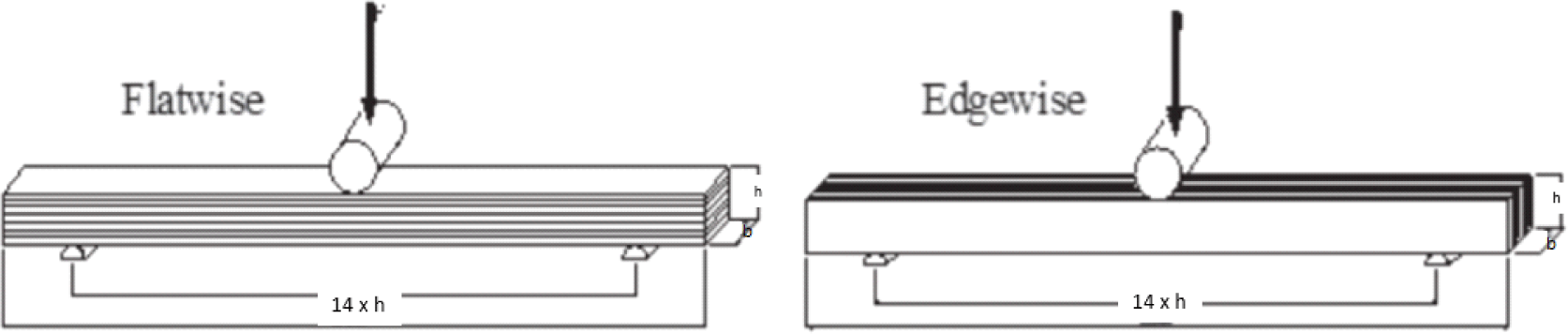
3. RESULTS AND DISCUSSION
The physical properties of bamboo laminated boards resulting from moisture content, specific gravity, weight, thickness, TC, and delamination are presented in Table 2.
Based on Table 2. it can be seen that the bamboo laminate board has a moisture content range of 11.63%–13.13%. The moisture content meets the minimum requirements for laminated board products permitted by JAS (2014), that is 14%. The density of zephyr and hybrid bamboo laminated boards has a value range of 0.69–0.80 (g/cm3). It can be seen that the hybrid bamboo laminate board has a lower density value than zephyr. This is due to the composition of the cores on the laminate board using falcata veneer which has a lower density than bamboo which is 0.33 g/cm3 (Kabe et al., 2012). The final density of the product is influenced by the density of the constituent, the adhesive, and the pressing process (Sulastiningsih et al., 2016), and the compressing process there is a compaction process which is also influenced by gluing (Supriadi et al., 2017). Therefore, the laminate board has an increased density compared to the raw material. Based on the wood strength class (SNI, 2013), the density of zephyr and hybrid bamboo laminated boards is included in strong class II, namely in the range 0.6–0.9.
The use of falcata veneer as the core of the laminate board is expected to reduce the weight of the bamboo laminate board, where the use of bamboo has a weakness, which is to produce a high weight board. The results showed that the hybrid bamboo laminate board has a lower weight than the zephyr bamboo laminate board.
The TC on the bamboo laminate board is determined from the thickness of the laminate board after pressing with after conditioning. Based on the results obtained, it can be seen that the substitution of falcata veneers as a core (hybrid) has a greater TC than zephyr. This is due to the cores material in the form of falcata veneer which has a lower density than bamboo. So, after receiving pressure when pressed it will change thicker than bamboo. Based on the tests that have been done, it can be seen that the preparation of ply-bamboo has a TC value that is smaller than the LBL. The arrangement of layers perpendicular to the layers will have better dimensional stability (Jung et al., 2003).
Dimensional stability is measured using 2 ways namely dimensional changes and WA. Dimension changes were carried out by immersing the sample for 24 hours and then drying in an oven at a temperature of 103°C to constant (swelling and shringkage), while the WA test was determined based on changes in weight for 72 hours measured every 2 hours in the first 6 hours and every 24 hours. The test results are shown in Fig. 3 (dimensional change) and Fig. 4 (WA).
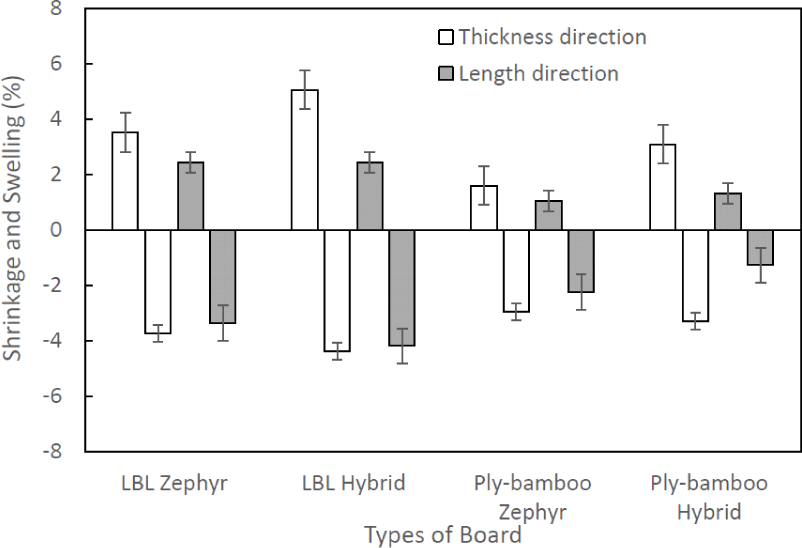
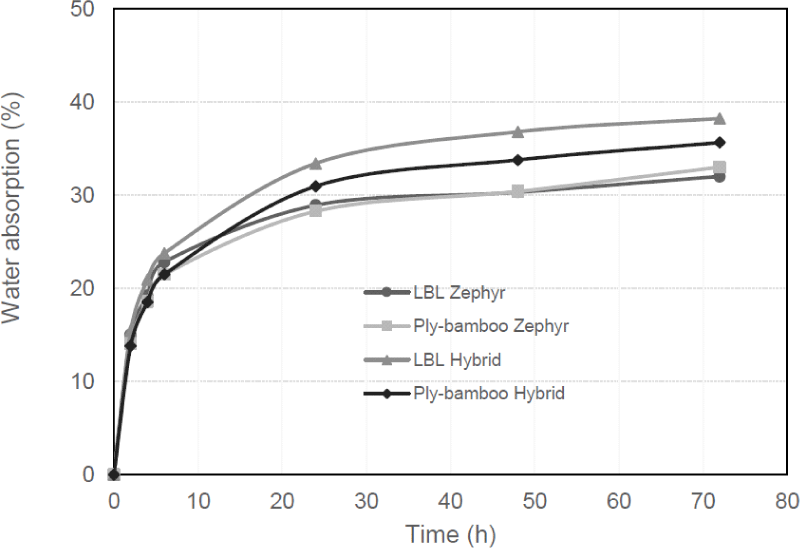
Based on Fig. 3, the substitution of the core layer with falcata veneer (hybrid) resulted in a decrease in dimensional stability on LBL and an increase in dimensional stability in the ply-bamboo. In addition, the expansion and shrinkage of ply-bamboo is smaller than LBL. This is related to the TC that occur. Laminate boards with perpendicular arrangement experience a change in thickness due to lower compression compared to parallel arrangement as shown in Table 2. The arrangement of perpendicular fiber directions between layers on laminated bamboo can withstand the expansion and shrinkage process due to swelling and shrinkage that occurs in the same direction of the fiber so that, mutually canceling between layers (Agustina et al., 2015; Zhang et al., 2018). Independent-sample T-test shows that there are differences LBL and Ply in length shrinkage based on the arrangement of the fiber direction while based on the constituent material the not significant (Table 3).
Treatments | t-value | df | Sig. (2 tailed) |
---|---|---|---|
Fiber direction | 4.522 | 4 | 0.011* |
Core materials | 3.057 | 2 | 0.092** |
WA is an indicator that can indicate the quality of a composite board based on its dimensional stability. WA can occur due to the adsorption force or the attraction of water molecules (hydrogen bonds) on cellulose, hemicellulose, and lignin. Based on Fig. 4, the hybrid bamboo laminate board has a higher WA than zephyr. The hybrid laminate board is composed of falcata veneer as a core layer. This is a factor that causes the WA capacity of hybrid laminated boards to be higher than zephyr laminates. It indicated that bamboo has good dimensional stability than wood material (Iswanto et al., 2020). WA can be influenced by the characteristics of the constituent materials as well as the release of stress due to compression (Lee et al., 1996; Sumardi and Suzuki, 2014).
Based on Fig. 4, the bamboo laminated boards experienced a significant increase in WA in the first 2 hours and tended to stabilize after 48 hours. This is due to the release of stress due to pressing and causes thick expansion (Zhang et al., 2018). Where a thick expansion indicates more WA. WA will continue until the cell cavity is saturated. On the bamboo laminate board, saturation of the cell cavities occurred after 48 hours of immersion.
The results of the modulus of rupture (MOR) on ply-bamboo (Fig. 5a) with the long test direction indicated that the hybrid laminate (54.45 MPa) had a higher value than the zephyr laminate (42.81 MPa). Whereas in the cross test direction hybrid laminated board (5.09 MPa) has a lower value than zephyr laminated board (17.37 MPa). Based on Japanese standards (JAS, 2014), MOR ply-bamboo zephyr and hybrid with long test directions are able to meet the minimum bending strength standard of 24 MPa. However, it cannot meet the minimum standard value in the cross test direction which is equal to 20 MPa. In some of the ply-bamboo zephyr MOR test samples there is damage as shown in Fig. 6. The existence of damage to the adhesive line and shear failure during testing can result in the resulting firmness value which is not optimal in holding the maximum load (Sumawa et al., 2019).
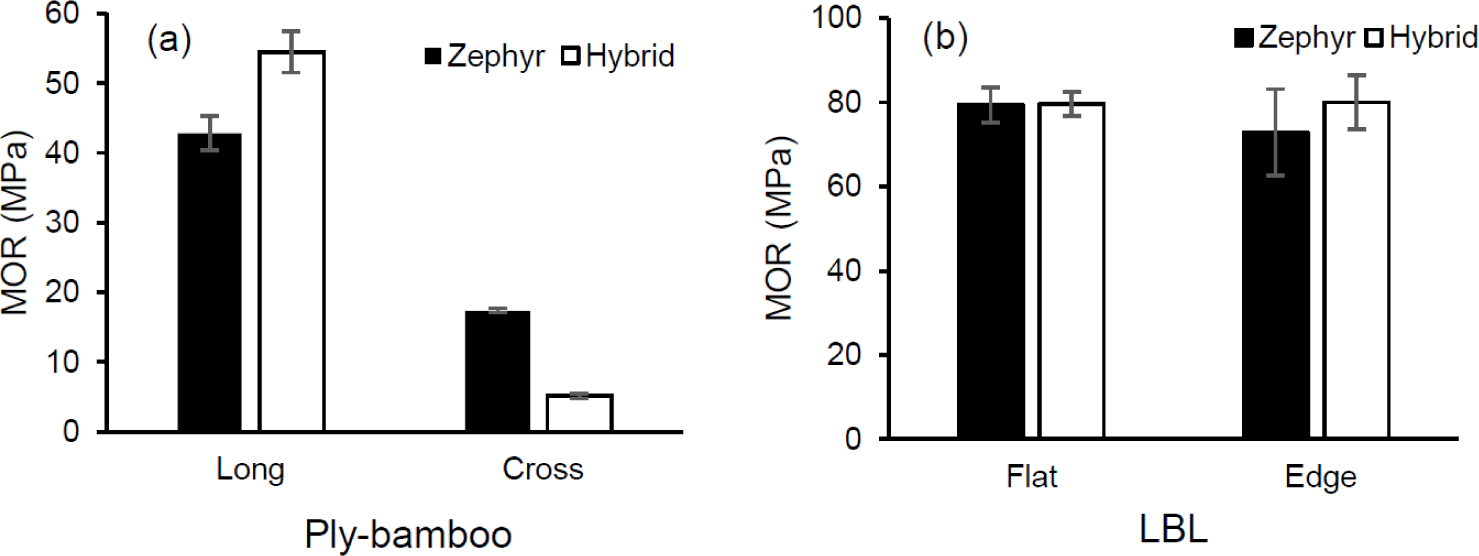
Testing the long direction (parallel with face layer direction of board) has a higher value than the cross test direction. This is because in the fracture strength test conditions, the test sample will experience tensile stress at the bottom of the sample. This condition will result in the tensile strength of the bamboo in the direction parallel to the fiber. Therefore, if the test is carried out in the cross-test direction, it will have a lower fracture strength. Based on the Independent-samples T-Test that has been conducted, it shows that the MOR value between ply-bamboo zephyr and hybrid laminated boards is significantly different. The same is true for core and long (Table 4).
Test | Treatments | t-value | df | Sig. (2 tailed) |
---|---|---|---|---|
MOR | Fiber direction | 4.522 | 4 | 5.536** |
Core materials | 3.057 | 2 | 3.675* |
The MOR value on the LBL (Fig. 3b) the flat test direction shows that the hybrid and Zephyr laminate board was similar with value approximately of 79 MPa. However, In the edge test direction of hybrid laminated board (80.03 MPa) has a higher value than zephyr (72.91 MPa). Based on Japanese standards (JAS, 2013), MOR LBL zephyr and hybrid can be categorized into class 180E which is the highest class. The damage is in the adhesive line which can cause the resulting firmness value to be not optimal.
The arrangement of the laminate board with the fiber direction perpendicular to the layers (ply-bamboo) has a lower MOR value compared to the arrangement of parallel fibers (LBL). This is in accordance with the research of Sulastiningsih et al. (2016) that the MOR value of lamina bamboo blocks from andong bamboo slats glued with isocyanate, has a lower value in the arrangement of the middle layer perpendicular to the outer layer compared to parallel arrangement.
Substitution of the core layer (core) with falcata veneer (hybrid) has a higher value than Zephyr laminated board. Both on ply-bamboo and LBL. This is different from the research conducted by Roh (2007) which shows that the use of wood layers on laminated bamboo boards arranged parallel can reduce the fracture modulus value.
In the fracture test that has been done, hybrid laminated boards have higher values than zephyr except in the direction of the cross test on ply-bamboo. Based on the classification of Indonesian Wood Construction Planning (SNI, 2013), ply-bamboo zephyr is equivalent to strong class IV (300–500 kg/cm2) and ply-bamboo hybrid is equivalent to strong class III (500–725 kg/ cm2). Meanwhile, the LBL zephyr and hybrid are equivalent to strong class II (725–1,100 kg/cm2).
The result of MOE on ply-bamboo (Fig. 7a) with the long test direction shows that the hybrid laminate board (7,267.39 MPa) has a higher value than the zephyr laminate board (6,967.86 MPa). Whereas in the cross test direction the hybrid laminate board (215.73 MPa) has a lower value than the zephyr laminated board (661.77 MPa). Based on Japanese standards (JAS, 2014), MOE ply-bamboo zephyr and hybrid with long test directions are able to meet the minimum standard of young modulus of bending, which is 5,000 MPa. However, it cannot meet the minimum standard value in the cross test direction which is 4,000 MPa.
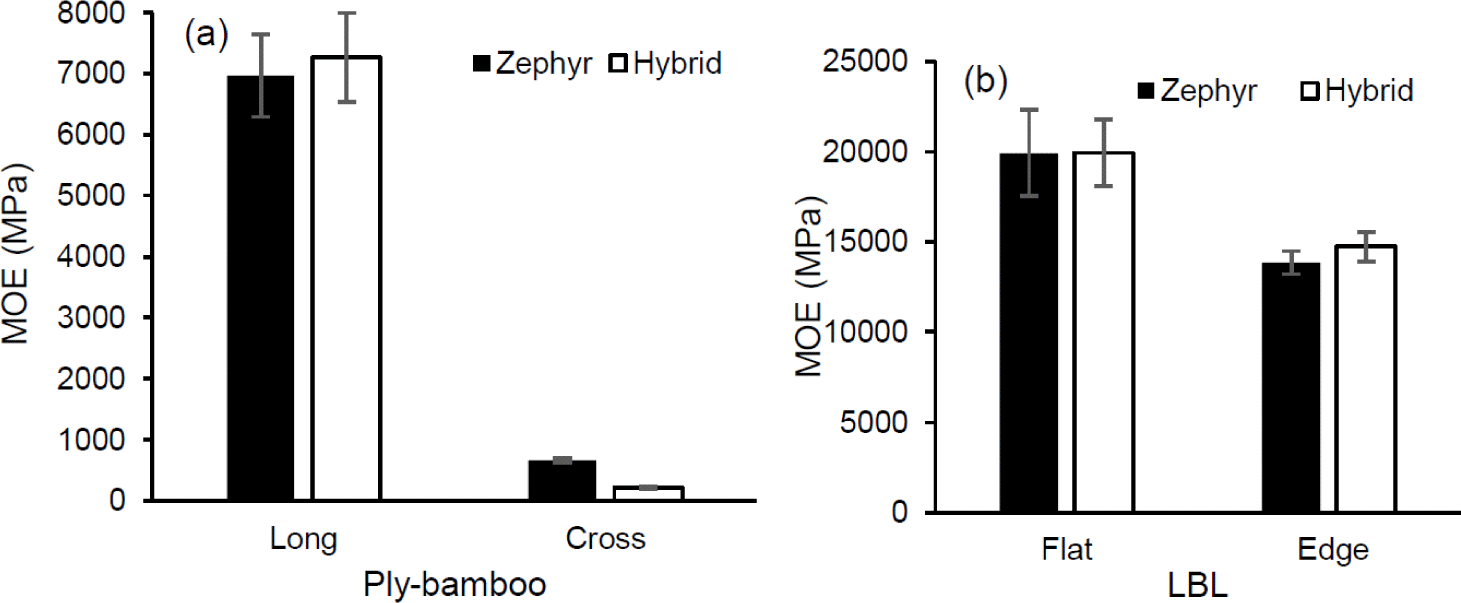
The similar trend with MOR, the MOE value on the LBL (Fig. 7b) for flat test direction of ply-bamboo hybrid and zypher had a similar value approximately 19,930 MPa. The same thing happened to edge test of zephyr and hybrid. Based on Japanese standards (JAS, 2014), MOE LBL zephyr and hybrid can categorized into class 140E. The MOE value based on its constituent materials between zephyr and hybrid laminate boards is not significantly different in flat and edge testing.
Based on Fig. 7, the arrangement of the laminate board with the fiber direction perpendicular to the outer layer (ply-bamboo) has a lower MOE value than parallel fiber arrangement (LBL). According to Nugroho (2000), giving a load to the board can decrease the flexural strength value along with the increasing angle of direction of the fibers between layers. So that the planks arranged perpendicularly will have a lower bending strength value than arrangement.
The shear strength was to determine the gluing ability of the board. The test results in Table 5 that the shear strength value of hybrid laminated boards (1.09 MPa) is higher than zephyr (0.89 MPa). The shear strength can be affected by the strength of the adhesive and the material being bonded (Sulastiningsih, 2014). The differences in the constituent materials which have different densities affect stickiness.
Based on Japanese standards (JAS, 2014) for plywood, the shear strength value of ply-bamboo meets the minimum standard, namely 0.7 MPa. In some samples of the ply-bamboo shear strength test, there is damage as shown in Fig. 8. The test samples show a silica layer which causes damage to the adhesive line.
The shear strength value on the LBL with a flat test direction shows that the hybrid laminate board (7.44 MPa) has a lower value than the zephyr laminated board (8.59 MPa). In the test direction the hybrid laminated board edge (9.73 MPa) also has a lower value than zephyr (10.67 MPa). Based on Japanese standards (JAS, 2013), LBL can be categorized into 65 V–55 H class, that is the highest class.
The test results show that the arrangement of the fiber direction perpendicular to the outer layer (ply-bamboo) on the bamboo laminate board can reduce the value of shear strength. The shear stress is strongly influenced by the composition of the layer direction, while the glued face/back combination does not have a significant effect (Sulastiningsih et al., 2014). The layers that are perpendicular to each other allow the formation of gaps from imperfections in the bonding process thus reducing the firmness.
The shear stress test has a correlation with the physical properties test in the form of delamination. The delamination testing on laminated boards can indicate the quality of adhesion (Darwis et al., 2014). Based on the test results in Table 2, the bamboo laminate board with WBPI did not experience delamination in all test samples according to the JAS for plywood standard (2014), which does not exceed 10%. This shows that the isocyanate polymer is able to work well in binding bamboo laminates to produce laminated boards with good adhesion quality. That result also was supported by Sulastiningsih et al. (2018) that bamboo composite lumber which is composed of strips of bamboo and zephyr bamboo as a face / back and falcata wood as a core with 250 g/m2 isocyanate adhesive, resulting in a delamination value of 0%.
The results of the screw withdrawal strength test (Table 5) show that the hybrid board screw toughness has a lower value than the zephyr both for Ply-board and LBL-board. Based on SNI 03-2105 (SNI, 2006) standards, ply-bamboo meets the minimum requirements, namely 500.14 N, while LBL is not able to meet these minimum requirements. In general, the arrangement of the laminae layers affects the screw withdrawal strength of the boards, and the cross-layer (Ply-bamboo) is higher than that of the unidirectional layer (LBL) (Ahn et al., 2021; Yang et al., 2021).
The screw withdrawal strength test was done on the face layer as shown in Fig. 9, perpendicular to the first layer. The next layer depends on the arrangement of the direction of the fibers and the constituent materials of the core layer, i.e., falcata veneer or bamboo. Generality, the screw withdrawal value of zephyr and ply-board ware higher than hybrid and LBL-board, respectively. The use of falcata veneer as a core substitution can reduce the firmness of removing the screw by 7.23% (LBL) and 3.28% (ply-bamboo). This is related to the density of the bamboo laminate board building material that density is a factor affecting the firmness of pulling out the screw (Erdil et al., 2002). The firmness value will increase with the density of the constituent material. Low density will also have a low firmness in holding a given screw load.
The value of ply-bamboo screw pulling firmness has a higher value than LBL. This is related to the orientation of the fiber which affects the firmness value. In addition, the firmness of pulling out the screws is also influenced by the density of the laminate board (Suhaily et al., 2019). Bamboo has the characteristic of parallel fiber direction. This can be a drawback of bamboo in testing the strength of screw pulls if the composite board is arranged in a direction parallel to the fibers in all layers. Thus, it will be easy to split without anyone holding the screw load as shown in Fig. 9. The results of Verma and Chariar (2012) research on Laminate Bamboo Composite using epoxy adhesive, have the value of the firmness of pulling out the screw which decreases along with the decreasing angle of the composition between layers. This is caused by the reduced angle of lamina will reduce the strength of the fiber that will withstand the load.
4. CONCLUSIONS
The arrangement of perpendicular fiber directions between layers (ply-bamboo) influences dimensional stability, MOR / MOE, shear strength and screw pull strength. Bamboo hybrid laminate board can produce lower board weight, increase stability on ply-bamboo, increase the value of fracture firmness (MOR) and flexural strength (MOE) and increase the adhesiveness of ply-bamboo and is able to meet the testing standards of all tested physical and mechanical properties (except for MOE / MOR, the cross-test direction, and the tightness of pulling out the screw on the LBL).