1. INTRODUCTION
Due to the serious noise problem in the residential environment and growing interest in improving the quality of the living environment, the demand for noise control in the residential environment has been increasing. Methods to reduce noise in a building or residential space include directly blocking or removing external noise or absorbing the sound generated in the space, but it is difficult to directly block or remove sound (Godshall and Davis, 1969). Currently, the noise problem is controlled using sound-absorbing materials or interior materials with sound absorption performance (Kang et al., 2010; Lee et al., 2014).
Sound-absorbing materials most commonly used indoors include porous sound-absorbing materials, which are dominated by products that use rock wool and glass wool or foam sponges processed from polyurethane (Wassilieff, 1996). These materials have been widely used as sound absorption finishing materials in spaces, such as music rooms, piano rooms, performance rooms, and other industries, due to easy installation, low cost, and high soundproof performance. Their application, however, is limited due to their toxicity, durability, incombustibility, and economic efficiency (Kang et al., 2010).
Sound absorption performance varies depending on the material. This is because each material has different friction resistance depending on its porosity and sound waves are reduced by friction resistance rather than being reflected (Godshall and Davis, 1969). Studies on sound absorption performance have been conducted using various materials (Jang, 2022; Jung et al., 2021). Porous materials are generally known to have high sound absorption performance. Among them, charcoal has an excellent porous structure. Its range of applications, however, is limited compared to cutting-edge carbon materials because it is affected by the temperature and moisture content during the manufacturing process and its properties significantly vary depending on the skill of the manufacturer, including twists and cracks after manufacturing (Oh et al., 2011). Woodceramics, which are porous carbon materials, were developed to complement these shortcomings.
Woodceramics are new porous carbon materials made by impregnating wood or wooden materials with thermosetting resin and carbonizing them at high temperature in vacuum condition. Since they were developed and named by Okabe and Saito, basic research has been conducted on various manufacturing methods and applications (Oh and Hwang, 2009; Won et al., 2014). They are porous, light, and hard with high thermal conductivity and such characteristics as the electromagnetic shielding effect and far-infrared radiation. Since they are also cheaper than other C-C compounds, they are expected to be used in various industrial fields, such as the raw materials of electromagnetic devices, friction materials, and automobile components (Okabe and Saito, 1995a, 1995b; Okabe et al., 1995a, 1995b). The properties of Woodceramics vary depending on manufacturing conditions, such as the type of raw materials and carbonization temperature. In particular, the carbonization temperature is known to have a significant impact on the density of Woodceramics (Hirose et al., 2002).
In addition, the density profile is generated in the thickness direction during the board manufacturing and carbonization process. It is a typical property for sheet materials made of wood and an important indicator of the properties of boards. Meanwhile, the sound absorption coefficient increases as density decreases. This is because low density leads to low surface stiffness, which absorbs energy and reduces sound through the deformation caused by the air flow generated from the incoming sound (Kang et al., 2012). Measurements of the density profile of ceramics can be useful in analyzing the sound absorption coefficient because the density and average density of the surface and center can be identified. Park et al. (2014) measured the density profile of the carbonized boards made by carbonizing particles boards, MDFs, plywood, and wood in a study on the performance improvement of wood-based carbonized boards. Oh et al. (2011) conducted research on the density profile of the woodceramics manufactured by recarbonization.
In this study, mixed boards were fabricated by adding charcoal to chaff and sawdust, which are agricultural and forestry by-products, and they were impregnated with resin. They were then carbonized at different carbonization temperatures and mixing ratios to manufacture woodceramics, and their density profile and sound absorption characteristic were compared under different manufacturing conditions.
2. MATERIALS and METHODS
Only the sawdust generated during the sawing of large (Larix kaemferi C.) was used. The chaff used was purchased from a rice mill in Deokjin-dong, Jeonju City, Korea and then ground using a mill (Hanshin, J-NCM; Hwang and Oh, 2023). The particle size of the sawdust and chaff was selected by –18 mesh, and the moisture content was adjusted to be 6% or lower (Hwang and Oh, 2023). The oak charcoal in a –100 mesh size was purposed from Geumhanpam in Imsil-gun.
Powdered phenol resin (KNB-100PL, Kolon Chemical, Gimcheon, Korea) was used for board manufacturing and liquid phenol resin (KPD-L777, Kolon Chemical, Gimcheon, Korea) for resin impregnation. The characteristics of the resins are shown in Table 1 (Hwang and Oh, 2023).
To manufacture boards, the powdered phenol resin and materials were added into a steel container and sufficiently mixed. They were then placed into a mold on the heat plate of a thermo-presser (DYMSP-001-026, Daeyang Machinery, Daegu, Korea), and the height of the upper part of the sample was controlled to be constant. After that, hot-press molding was applied to produce a 260 mm × 260 mm × 11 mm board. As for the manufacturing conditions of boards, the resin content was fixed at 10% of the board weight and the density was fixed at 0.6 g/cm3. Four types of boards were manufactured by varying the contents of the sawdust, chaff, and charcoal to 50:35:5, 50:30:10, 50:25:15, and 50:20:20 (Hwang and Oh, 2020). In this instance, the hot pressing temperature was set to 170°C, and the pressure was set to 40, 30, and 20 kgf/cm2 considering the hardening of the adhesive and spring back. 10 to 30 sec/mm is usually required as pressurization time for manufacturing with amino resin, but more than 50 sec/mm is required for phenol resin. In addition, since the boards were manufactured through powdered phenol resin, more time was required for hardening after the liquefaction of the resin and thus hot pressing was performed for 12 minutes (nine, two, and one minutes). In addition, thickness bars were used to maintain a constant thickness for the boards. A Teflon plate was used to prevent the adhesion between the board and the heat plate in the thermo-presser.
For the manufactured boards, the size of the cross section was cut into 120 mm × 120 mm, and specimens with ± 0.03 g/cm3 for the density were selected under each condition by calculating the density for constant test conditions (Hwang and Oh, 2021). The prepared specimens were placed in a decompression-impregnation device containing liquid phenol resin, and the impregnation rate was adjusted by performing both decompression (1 atm) and ultrasonic treatment (frequency: 28 kHz, power: 564 W) and then leaving the specimens unattended under atmospheric pressure (Hwang and Oh, 2021). After impregnation, the specimens were subjected to air drying for eight hours and then drying and hardening for eight hours at 60°C and 130°C in a drier, respectively (Hwang and Oh, 2021).
Among the hardened boards with a resin impregnation rate of 40 ± 2%, the boards with sawdust, chaff, and charcoal mixing ratios of 50:35:5, 50:30:10, 50:25:15, and 50:20:20 were carbonized using a vacuum carbonization furnace (KOVAC KSF-200V, Korea Vacuum, Incheon, Korea) at a carbonization temperature of 800°C to manufacture ceramics (Hwang and Oh, 2021). In addition, specimens with a resin impregnation rate of 40 ± 2% were selected among the impregnated boards with a mixing ratio of 50:20:20, and they were carbonized using the vacuum carbonization furnace at 600°C, 800°C, 1,000°C, and 1,200°C to manufacture ceramics (Hwang and Oh, 2021). The temperature was increased from room temperature to the set temperature at a rate of 4°C/min. After the specimens were maintained at the set temperature for two hours, they were cooled by circulating coolant around the carbonization furnace (Hwang and Oh, 2021).
The sound absorption coefficient was measured based on the transfer function method using B&K’s impedance tube, pulse analyzer, and spectrum analyzer as shown in Fig. 1 (Kang et al., 2015). During the measurement of the sound absorption coefficient, the change in sound absorption coefficient caused by the frequency change in the 100–6,400 Hz section was measured using a small impedance pipe with a diameter of 29 mm (Kang et al., 2015).
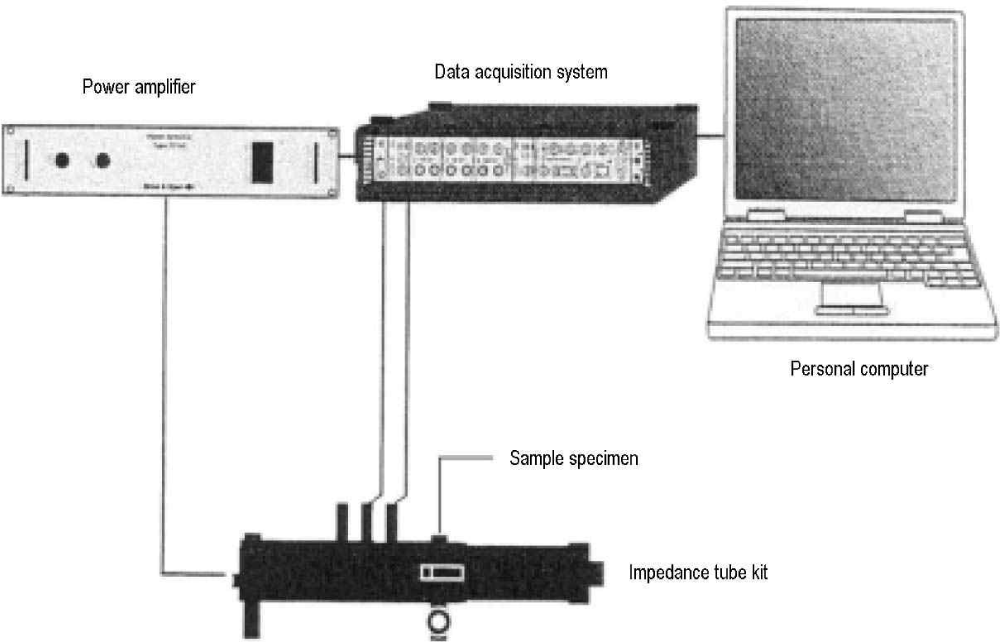
During the test, the temperature, relative humidity, and air pressure were set to 24.5°C, 47%, and 1,005.5 hPa, respectively, as external conditions. In addition, the speed of sound, air density, and acoustic impedance were set to 345.86 m/s, 1.175 kg/m3, and 406.3 Pa/(m/s), respectively.
3. RESULTS and DISCUSSION
Table 2 shows the density profile of the ceramics manufactured under different mixing ratios. The ceramics manufactured under a mixing ratio of 50:25:15 exhibited the highest average density (679.8 kg/m3) and the highest density profile (91%). Although the ceramics were manufactured using the boards with the same density, the impregnation process for the same impregnation rate, and the same temperature, the density of the manufactured ceramics was different depending on the proportions of the sawdust, chaff, and charcoal. This is believed to be because the structural changes of the components were different in the carbonization process depending on the mixing ratio. It appears, however, that the density of the ceramics manufactured under a ratio of 50:20:20 decreased because the increased content of charcoal powder reduced shrinkage in the length and thickness directions during carbonization. In addition, in the experiment, the density profile tended to increase as the chaff content decreased and the charcoal powder content increased. This is thought to be due to the uniform density distribution of the manufactured boards.
In a study on the performance improvement of wood-based carbonized boards by Park et al. (2014), the density profile of the carbonized boards manufactured using particle boards was approximately 74%. In the experiment of this study, however, the ceramics manufactured under each mixing ratio showed a high average density profile of approximately 89%. This seems to be because the resin impregnation process contributed to the more uniform density distribution of the manufactured ceramics.
Fig. 2 shows the sound absorption coefficients of the ceramics according to the mixing ratio. For the specimens with mixing ratios of 50:30:10 and 50:35:5, the sound absorption coefficient increased for a frequency of up to 1,000 Hz and then remained between 0.3 and 0.4. In the case of the other specimens, the sound absorption coefficient increased for a frequency of up to 1,000 Hz and then remained between 0.2 and 0.3. The sound absorption performance increased as the chaff content increased, and the density of the manufactured ceramics tended to decrease as the chaff content increased. In general, the sound absorption coefficient was higher for boards with lower specific gravity. This is because low specific gravity leads to low surface stiffness, which absorbs energy and reduces sound through the deformation caused by the air flow generated from the incoming sound (Kang et al., 2012). It is believed that the ceramics manufactured under mixing ratios of 50:30:10 and 50:35:5 exhibited higher sound absorption performance because their surface density was lower than that of the other two types.
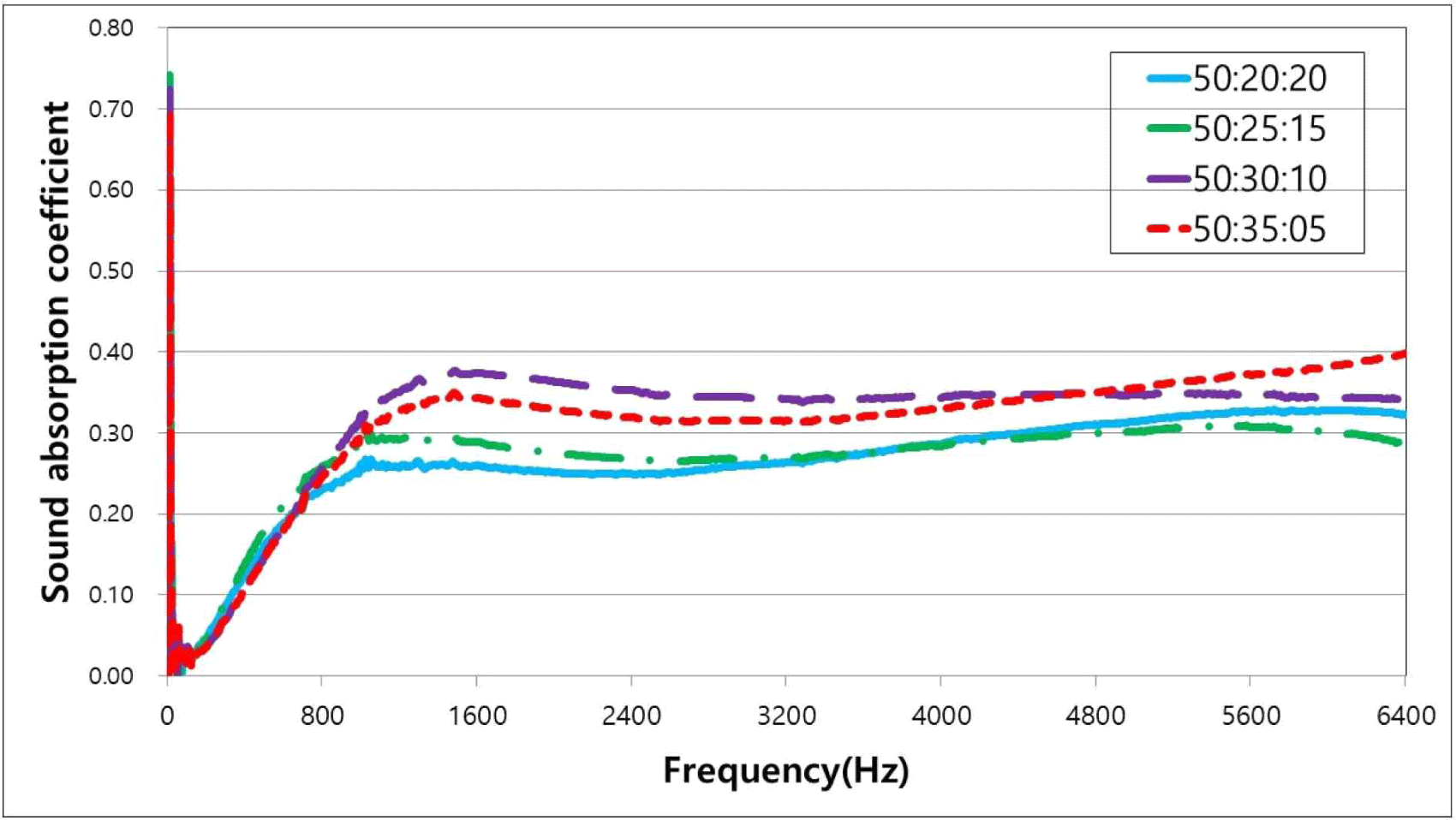
Table 3 shows the density profile of the ceramics manufactured at different carbonization temperatures after fixing the mixing ratio at 50:20:20. The average density and minimum density showed the highest values (687.8 and 588.8 kg/m3, respectively) at a carbonization temperature of 1,000°C. Okabe et al. (1996) reported that the change in density according to the carbonization temperature is attributed to the structural change caused by the carbonization reaction of wood and resin, and that the rapid density change under 600°C is mainly caused by the desorption reaction of the components and the density change under 1,000°C is caused by the change in structure by the carbonization of wood and resin. They also reported that density slightly decreases above 1,000°C due to the carbonization of phenol resin. Similar tendencies were also observed in this study.
The density profile was highest (88.0%) at 800°C and lowest (81.4%) at 1,200°C. This appears to be due to the change in the structures of the materials and resin for ceramic manufacturing caused by the temperature. Park et al. (2014) reported that the density profile of the carbonized boards manufactured using particle boards is less affected by the carbonization temperature, and similar results were also observed in this study.
Fig. 3 shows the sound absorption coefficients of the ceramics manufactured at different carbonization temperatures after fixing the mixing ratio at 50:20:20. The specimen manufactured at a carbonization temperature of 1,200°C showed higher sound absorption performance as the frequency increased, and it exhibited a sound absorption coefficient of 0.3 or higher at almost all frequencies. The other specimens showed a sound absorption coefficient between 0.2 and 0.3. It is thought that the specimen manufactured at 1,000°C showed the lowest sound absorption performance due to high surface density and average density. Overall, the sound absorption coefficient showed no significant tendency according to the density change caused by the carbonization temperature.
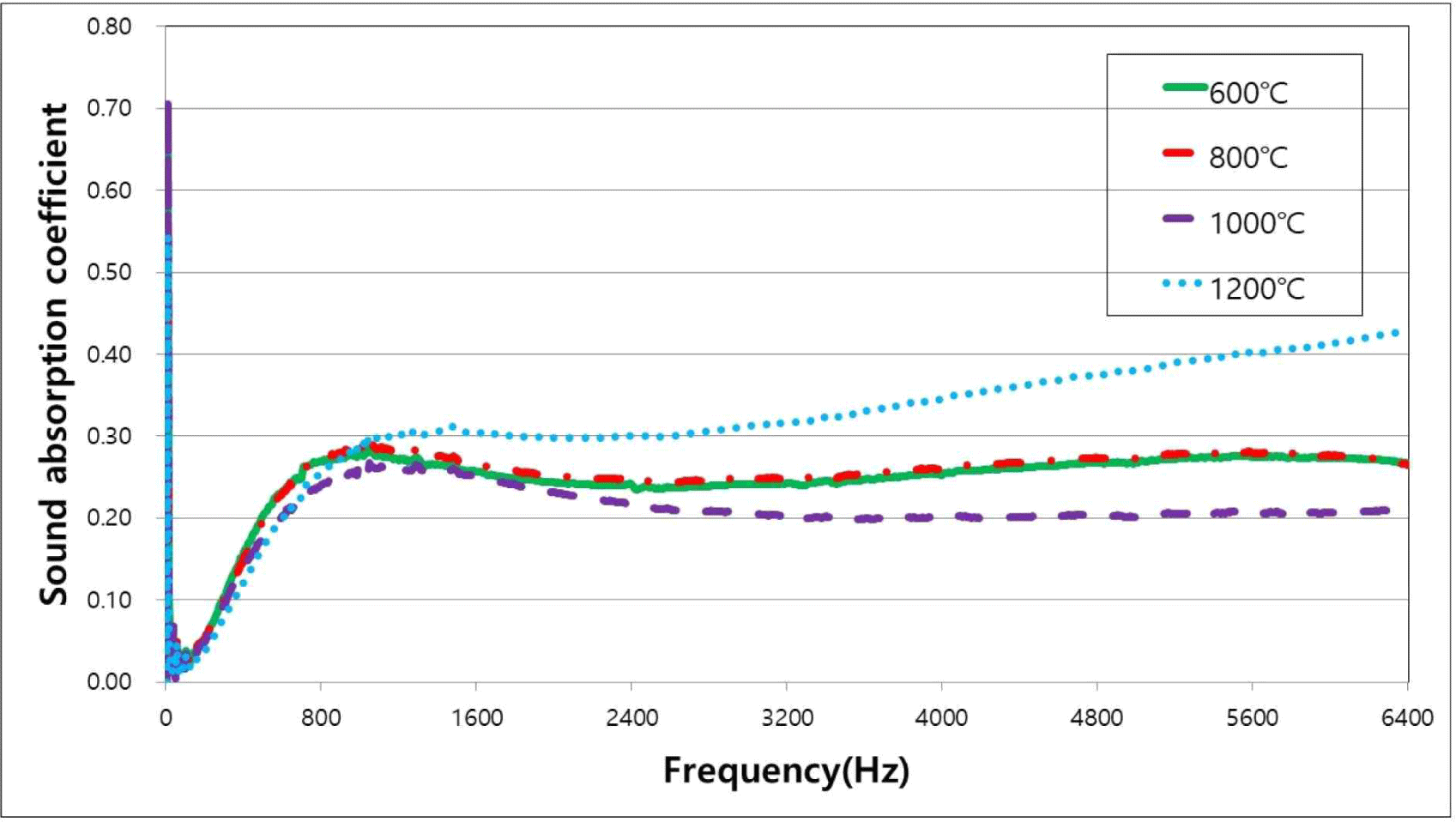
4. CONCLUSIONS
In this study, ceramics were manufactured at different carbonization temperatures and mixing ratios of chaff, sawdust, and charcoal. The density profile and sound absorption performance were then investigated to examine whether the ceramics can be used as sound-absorbing materials.
The density profile of the manufactured ceramics was highest (91.00%) when the mixing ratio of sawdust, chaff, and charcoal was 50:25:15, but the difference was not significant depending on the mixing ratio. As for the density profile of the ceramics manufactured at different carbonization temperatures, the highest value (88.06%) was observed at 800°C but no significant tendency was observed, indicating that the carbonization temperature has little impact on the density profile.
Meanwhile, the sound absorption coefficients of the manufactured ceramics were between 0.3 and 0.4 at almost all frequencies when the mixing ratios were 50:30:10 and 50:35:5. This appears to be because the average density and surface density of the ceramics decreased as the content of chaff increased. As for the sound absorption performance of the ceramics manufactured at different carbonization temperatures, the ceramics manufactured at 1,200°C showed the highest value.
It is believed that the sound absorption coefficient is more affected by the surface density than the density profile for the ceramics manufactured at different mixing ratios. It appears, however, that the surface density has little impact on the sound absorption coefficient for the ceramics manufactured at different carbonization temperatures.
In this study, sound absorption performance was observed in a relatively wide frequency band, but it was evaluated to be low. Therefore, further research is warranted to improve sound absorption performance in the future. In addition, various experiments on the utilization of the properties of porous materials (e.g., moisture absorption and insulation) will be required for the manufactured ceramics to be used in the residential environment.