1. INTRODUCTION
Indonesia has conducted genetic experiments since 1983 to increase timber production (Seta et al., 2023). One of the their most productive studies is the production of the fast-growing “Biotrop Teak.” In comparison with conventional teak, the fast-growing teak will have double the diameter at the same age (Rakhmawati, 2019). Teak is considered a very important wood in Indonesia due to its high-quality with fancy decoration and durability, especially that of wood from old trees (Savero et al., 2020). Several people use teak wood because it has a beautiful pattern and luxurious golden-brown color, is easy to work with, and has natural durability that makes it resistant to wood-destroying organisms. The advantages of teak wood also led to it being favored by national and international markets for a variety of uses (Lukmandaru and Sayudha, 2011). Due to the high demand of teak wood and several material-related flaws, various studies have been conducted in Indonesia to shorten the cutting rotation time and maintain the quality of teak wood. On the other hand, utilization of sapwood to increase its value is very rare and has not been developed.
The sapwood part of the wood product of fast-growing teak is mostly ignored, due to its inferior quality. Sapwood cells are assumed to be more dominated by nutrients such as sugar compounds or glycosides, so their durability is lacking (Lukmandaru et al., 2012). Sapwood is less preferred because it has lower durability than that of heartwood (Darwis et al., 2005). Sapwood has less extractive content than heartwood (Berrocal et al., 2020); thus, a higher proportion of heartwood is more desirable than a higher proportion of sapwood in the timber industry (Tewari and Mariswamy, 2013). Sapwood waste has potential to become raw materials of activated carbon. Sapwood waste can be used as a new resource for the production of different materials for creating new economic products. It can also be utilized in various wood industries because it consists of cellulose, hemicellulose, and lignin (Hwang et al., 2021; Ju et al., 2020; Setiawan et al., 2023). The production of charcoal and activated carbon is thought to have increased due to the increased use of fossil fuel and its impact (Kwon et al., 2018).
Activated carbon is charcoal which can be produced by either chemical or physical treatment (Pari et al., 2005). Activated carbon has a large surface area which contributes to its high adsorption capacity for pollutants and dirt (Aini et al., 2021). Furthermore, activated carbon has high adsorption for anions, cations, and molecules in the form of organic and inorganic compounds (Lubis, 2021). Prior literature documented that activated carbon has been used since the prehistoric age and plays an important role in various utilizations (Dungani et al., 2022). On an industrial scale, activated carbon is generally used for adsorbents, liquid and gas separators, and catalyst support materials (Sadir et al., 2022). Carbonization temperature would be a very important aspect in assessing the quality of charcoal (Park et al., 2018). Prior research documented that the quality of activated carbon is influenced by the activation temperature, which ranges from 500°C to 1,000°C and that the best iodine adsorption was achieved with an activation temperature of 700°C to 1,000°C (Idrus et al., 2013). Another study documented that the heating duration is also used to determine the quality of activated carbon (Hartoyo, 1988). Therefore, in this research, the authors would like to investigate the quality of activated carbon from fast-growing teak sapwood (FTS) waste. Based on previous research, this study aims to investigate the effect of activation temperatures of 750°C, 850°C, and 950°C and heating durations of 30 min, 60 min, and 90 min. Finally, the quality properties of FTS activated carbon will be compared to the Indonesian activated carbon quality standard (SNI 06-3730-1995; Badan Standardisasi Nasional, 1995).
2. MATERIALS and METHODS
The study aimed to evaluate the influence of activation temperature and heating duration on the adsorption properties of FTS activated charcoal. The activation temperature consisted of three temperature variations: 750°C, 850°C, and 950°C. The heating duration consisted of three variations: 30 min, 60 min, and 90 min. Furthermore, the data obtained were statistically analyzed.
The raw materials used in this research were sapwood of 14-year-old FTS waste taken from three trees from community forests in Wonosari, Gunungkidul, Yogyakarta Special Region. FTS waste was taken from the bottom of the tree up to 1.3 m height. Sapwood chips with a thickness of 0.5–0.9 cm and 8–10 cm length were then formed by separation (Fig. 1). The chips were then air-dried to a moisture content (MC) of 10%–15%.
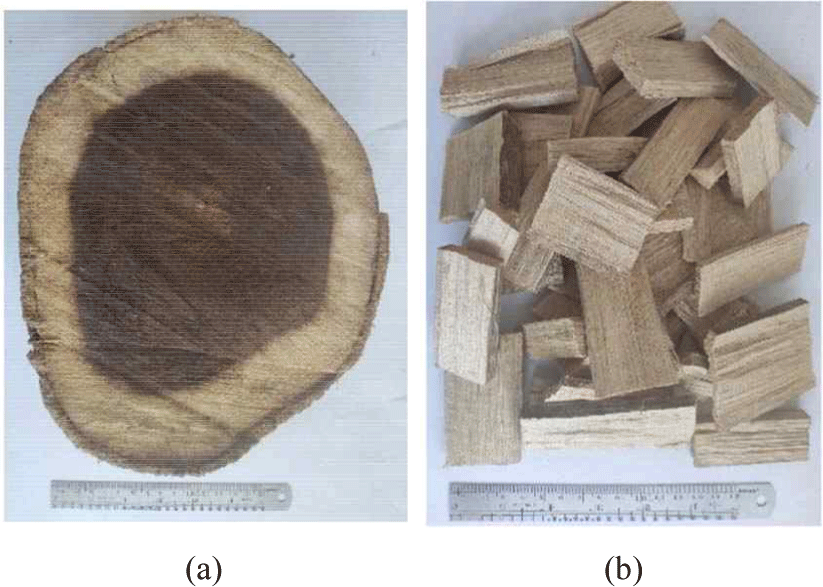
Chemical materials consist of sodium thiosulfate (Na2S2O3), sodium hydrogen carbonate (NaHCO3), potassium iodide (KI), benzene (C6H6), distilled water, methylene blue, starch indicator.
The research equipment included a furnace (FB 1410M-33, single setpoint with a capacity of 2.1 L, power consumption of 1,520 W, temperature range of 100°C to 1,100°C, temperature stability of ± 5.0 at 1,000°C, and electrical requirements of 240 V 50/60 Hz), oven (memmert UN 55, power consumption 2,000 W, electrical requirement 230 V 50/60 Hz), scale (Ohaus PAJ 2003), hot plate (Shindo 188CT, power consumption 200 W, electrical requirement 240 V), spectrophotometer (WP S800+, electrical requirement 90–265 V, 50/60 Hz), magnetic stirrer, pipette, filter paper, porcelain cup, mesh-screen, desiccator, beaker glass, and burette.
The carbonization process is conducted by electric retort with a temperature of 500°C for 4 hours. The carbonized charcoal is grounded into charcoal powder and followed by filtering through a 10-mm mesh-screen then stuck on the size of 20 mesh.
Twenty-three grams of FTS waste charcoal was put into a porcelain cup before being thermally activated in the furnace.
The quality evaluation parameters of activated carbon include yield, MC, volatile matter content (VMC), ash content (ASH), fixed carbon content (FC), adsorption capacity of benzene (ACB), adsorption capacity of methylene blue (ACM), and adsorption capacity of iodine (ACI).
Yield was determined by activated carbon produced after the activation process. Yield was calculated using the following formula:
Remark: W1, charcoal’s weight before activation (g); W2, activated carbon’s weight (g).
MC is the amount of water in activated carbon. The procedure for calculating the MC was done following ASTM D1762-84 (ASTM, 2007). Activated carbon (2 g) as the initial weight sample was dried in the oven at a temperature of 103 ± 2°C and weighed every two hours until it reached a constant weight. MC was calculated with the following formula:
Remark: W1, initial sample’s weight (g); W2, sample’s weight after heating (g).
VMC is the amount of volatile content in activated carbon. The procedure for calculating the VMC was carried out following the ASTM D1762-84 (ASTM, 2007) standard and done by heating the sample in a furnace until a temperature of 950°C was reached. VMC was calculated with the following formula:
Remark: WL, weight loss; W1, sample’s weight (g); W2, sample’s weight after heating (g).
ASH is the amount of ash in activated carbon. The procedure for calculating ASH was conducted following the ASTM D1762-84 (ASTM, 2007), by heating the sample in a furnace at a temperature of 750°C for 6 hours. ASH was calculated with the following formula:
Remark: W1, sample’s weight (g); W2, sample’s weight after heating (g).
FC is the amount of carbon after the activation process. The procedure for calculating the FC was conducted following the ASTM D3172-89 (ASTM, 2002) and using the following formula:
ACB is the amount of benzene which is adsorbed by activated carbon. The procedure for calculating the ACB was carried out following the SNI 06-3730-1995. One gram of activated carbon (passed 60 mesh) was left in a desiccator saturated with benzene vapor for 24 hours. ACB was calculated with the following formula:
Remark: W1, sample’s weight before benzene adsorption (g); W2, sample’s weight after benzene adsorption (g).
ACM is the amount of methylene blue which is adsorbed by activated carbon. The procedure for calculating the ACM was carried out following the SNI 06-3730-1995. Briefly, 0.2 grams of activated carbon with a pass size of 320 mesh was then mixed with 25 mL of 1,200 ppm methylene blue by shaking for 45 minutes, then filtered, and then left for 24 hours. Then, 10 mL was taken for measuring the methylene blue concentration resulting from the adsorption of activated carbon using a spectrophotometer at a wavelength of 665 nm.
ACM was calculated with the following formula:
Remark: C, blue methylene concentration; Fp, dilution factor; B, sample’s weight (g).
ACI is the amount of iodine which is adsorbed by activated carbon. The procedure for calculating ACI was carried out following the SNI 06-3730-1995. The iodine solution resulting from the reaction of 25 g of KI and 30 mL of distilled water was stirred for 15 min, then diluted to 1,000 mL with distilled water. A sodium thiosulfate (Na2S2O3) solution was made by reacting 24.8 g of sodium thiosulfate with 0.2 g of sodium hydrogen carbonate (NaHCO3). Then, 200 mL of distilled water was added and the mixture was stirred for 15 min and diluted to 1,000 mL with distilled water. After, 0.5 grams of activated charcoal with a passing size of 320 mesh was mixed with 25 mL of iodine (I2) by shaking for 30 min then filtered and left for 24 hours. Next, the filtered iodine solution was titrated using sodium thiosulfate (Na2S2O3) in a solution of iodine (I2) resulting from the absorption of activated carbon with a starch indicator. ACI was calculated with the following formula.
Remark: V, sodium thiosulfate solution required; N, sodium thiosulfate normality; W, sample’s weight; 12.69, amount of I2 (Iodine) in the solution of 1 mL 0.1 N sodium thiosulfate.
3. RESULTS and DISCUSSION
Fast growing teak sapwood is yellowish brown, and lighter in color than heartwood (Fig. 1). For the local furniture industries, a high percentage of sapwood is less desirable than trees with a high percentage of heartwood. Due to its inferior quality, sapwood is categorized as waste in several cases. However prior studies documented that a higher proportion of sapwood gives the advantage of being easy to preserve because preservatives easily penetrate sapwood (Oteng-Amoako, 2004). The penetration ability of preservatives indicates that sapwood has more open pores than heartwood. This is because the extractive material closes the pores in heartwood (Gartner and Meinzer, 2005). This porous part of wood is in accordance with sapwood function for tree transpiration (Gartner, 1995). Utilization of this FTS waste for activated carbon is one solution that could increase the added value of the wood.
The quality parameters used to analyze the characteristics of activated carbon from FTS waste included MC, VMC, ASH, FC, the ACB, the ACM, and the ACI. Data from the analysis of activated carbon from FTS waste was compared to that reported in SNI 06-3730-1995.
The results showed that the yield value in this study tends to decrease along with the increase in temperature and heating duration (Fig. 2). From the activation process, the average activated carbon yield obtained was 75.94% (Table 1). This result is in accordance with earlier research findings that increasing heating duration caused decreasing yield value (Jun, 2010; Malik and Syech, 2013). Compared to other research, the activated carbon yields in this study are higher than that reported on activated carbon from teak wood sawdust (35.66%). This trend is in accordance with previous findings that increasing activation temperature tends to decrease activated carbon yield (Komarayati et al., 1997). However, this activated carbon yield value is lower than that reported for the activated carbon yield of teak sawdust using chemical activation (89.63%) as reported by Erawati and Afifah (2019). Decreasing yield of activated carbon is caused by initial VMC that can be easily removed with higher temperatures in the activation process (Chandra et al., 2009). This occurs as a result of the higher temperature which causes a faster rate of reaction between carbon and water vapor, resulting in the conversion of carbon into H2O and CO2 so that the remaining carbon was less (Sudradjat et al., 2005). Based on the yield of FTS waste to charcoal (35.5%) and yield of charcoal to activated carbon (75.94%), it was found that 1,000 kg of FTS waste can be converted to 262.5 kg activated carbon. This result is in accordance with the findings of Priyambodo (2023).
Treatment | Yield (%) | |
---|---|---|
Temperature (°C) | Heating duration (min) | |
750 | 30 | 78.58 |
60 | 77.42 | |
90 | 76.97 | |
850 | 30 | 77.55 |
60 | 75.64 | |
90 | 75.61 | |
950 | 30 | 74.41 |
60 | 74.87 | |
90 | 72.40 | |
Average | 75.94 |
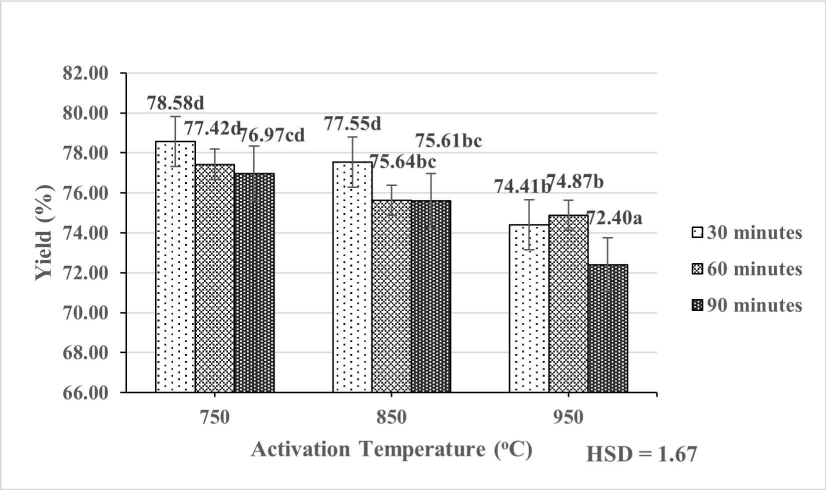
The MC of activated carbon of FTS waste ranged between 0.99% and 1.26% (Table 2). The highest MC (1.26%) was produced by activated carbon with an activation temperature of 850°C and heating duration of 30 min, whereas the lowest MC (0.99%) was obtained by activated carbon with an activation temperature of 850°C and heating duration of 60 min (Fig. 3). The highest iodine adsorption of activated carbon in this research has a MC of 1.27%. This MC is lower than that reported in other studies for the activated carbon of ketapang seed shells (8.06%). Furthermore, the MC of FTS waste is also lower than that of teak sawdust (3.70%) reported by Nusratullah and Aminah (2020), and 7.40% reported by Ismadji et al. (2005). This MC is also lower than that obtained for durian shell at 11.27% (Jun, 2010) and iroko wood at 7.32% (Onwumelu, 2022). The MC affects the ability of activated carbon to adsorb liquids and gases. The amount of water that covers the pores depends on the MC, that is, a lower MC indicates less water covering the pores (Imawati and Adhitiyawarman, 2015). Therefore, a greater number of pores increases the surface area of activated carbon, which subsequently increases adsorption capacity. The result showed that the MC of the activated carbon of FTS waste at activation temperatures of 750°C, 850°C, and 950°C and with heating durations at 30 min, 60 min, and 90 min, ranged from 0.99% to 1.26%; this result already fulfilled the SNI standard (≤ 15%). The produced activated carbon of FTS waste showed that its MC increases with increasing carbon activation temperature and heating duration. This result is in accordance with other activated research results on coconut shells, which reported that higher temperature and longer heating duration will increase MC (Jamilatun et al., 2014; Surest et al., 2010).
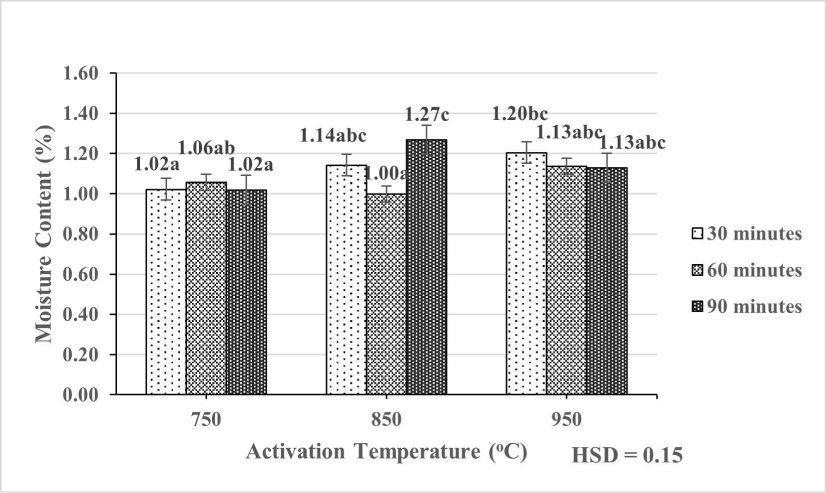
The VMC of activated carbon of FTS waste ranges between 9.55% and 13.60% (Table 2). Table 3 shows the significant interaction between activation temperature and heating duration at the 5% test level. The highest iodine adsorption of activated carbon had a VMC of 9.98%. This number is higher than that of activated carbon of teak sawdust at 7.83% (Komarayati et al., 1997) and palm oil shell of 3%. VMC tends to decrease with increasing activation temperature and heating duration (Fig. 4). This result is in line with the trend that increasing activated temperatures were followed by decreasing VMC (Hartanto and Ratnawati, 2010). On the other hand, the volatile matter in this study is lower than that of the activated carbon of iroko wood at 19.01% (Onwumelu, 2022). The low VMC is caused by the reaction of sulfur and nitrogen with hot water vapor (Hendra and Pari, 1999). A large amount of volatile matter is removed sequentially from the materials during pyrolysis when the pyrolysis temperature is elevated from 700°C to 900°C (Danish and Ahmad, 2018). A high number of VMC values are affected by the attachment of non-carbon compounds to the surface of the activated carbon, which reduces the adsorption capacity of activated carbon (Suherman et al., 2021). The lower content of volatile matter due to materials such as CO2, CO, CH4, and H2 came out during the activation process (Hendra and Pari, 1999). Ju et al. (2020) emphasized that the lower VMCs of the carbonized samples are caused by the removal of volatile compounds in the form of gases during the carbonization process. VMC of activated carbon of FTS waste at 750°C, 850°C, and 950°C for heating duration at 30 min, 60 min, and 90 min ranged from 9.55% to 13.60%; this result already fulfilled the SNI quality standard (≤ 25%).
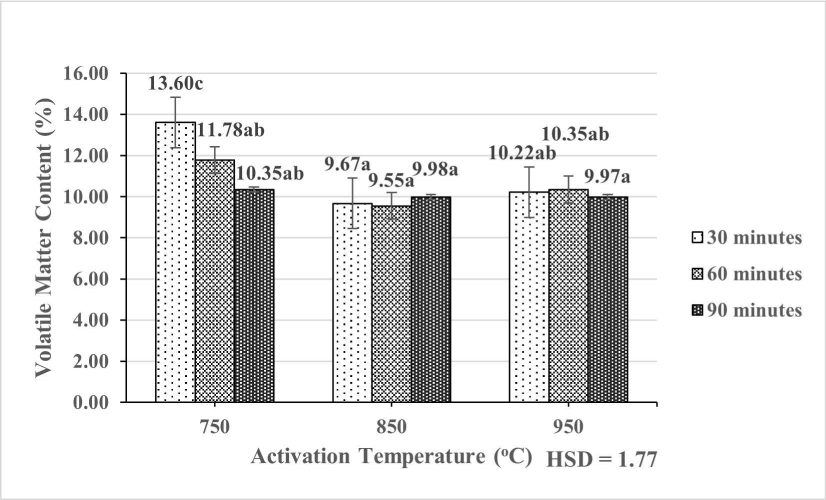
Investigation of the ASH of activated carbon aims to determine the amount of minerals contained in activated carbon that have no calorific value (Suherman et al., 2021). The ASH of activated carbon of FTS waste ranged between 4.67%–6.43% (Table 2). The results showed that activation temperature provides significant differences of ASH at the 5% test level (Table 3).
The highest iodine adsorption activated carbon obtained has an ASH of 5.43%, this number is higher than that of the activated carbon of teak sawdust at 1.95% (Ismadji et al., 2005; Nusratullah and Aminah, 2020). Furthermore, this is also higher than the ASH of activated carbon of acacia stump at 4.22% (Aprianis, 2012), ASH of durian shell (4.84%; Jun, 2010), and activated carbon of iroko wood (5.42%; Onwumelu, 2022). The ASH of FTS waste activated carbon tends to rise with an increase in activation temperature (Fig. 5). Higher temperature activation results in higher ASH obtained due to the influence of the oxidation process, which the ASH affects the adsorption capacity of activated carbon both in gas and solution (Jamilatun et al., 2014). The remaining minerals block activated carbon pores which affects the adsorption process (Imawati and Adhitiyawarman, 2015). The ASH of activated carbon of FTS waste at 750°C, 850°C, and 950°C for heating durations at 30, 60, 90 min ranged from 4.67% to 6.43%; this result fulfilled the SNI standard (≤ 10%).
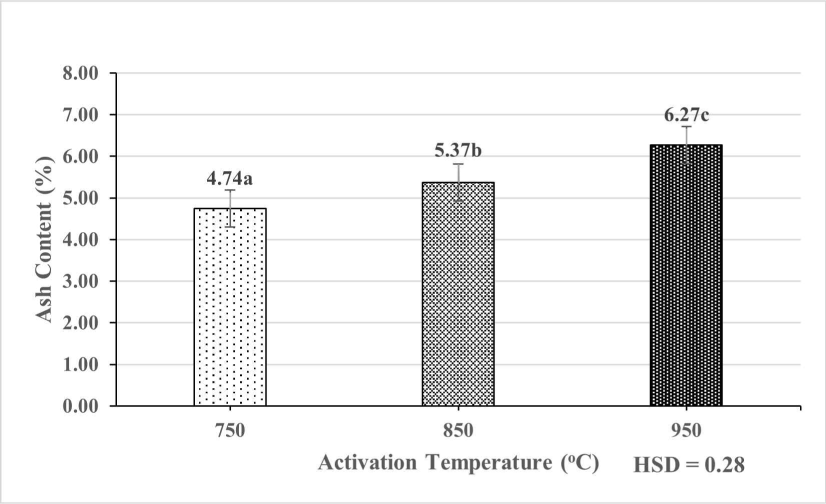
The FC is defined as the carbon fraction (C) contained in materials; that is, what remains after the water, ash, and volatile substances are removed (Cahyani et al., 2023). The results showed that the FC of FTS waste ranges between 81.73%–85.15% (Table 2). There was a significant interaction between the activation temperature and heating duration at the 5% test level (Table 3).
The highest iodine adsorption activated carbon in this research has a FC of 84.58%. This is higher than that of the activated carbon of iroko wood (29.25%; Onwumelu, 2022) and teak sawdust (28.9%; Ismadji et al., 2005). However, the FC was slightly lower than that of the activated carbon of stump acacia at 88.41% (Aprianis, 2012). The FC of FTS tends to rise in line with the increasing heating duration (Fig. 6). FC is strongly influenced by VMC and ASH which lowers VMC and ASH, resulting in higher FC (Hendra and Pari, 1999; Suherman et al., 2021). Furthermore, FC is also influenced by the content of cellulose and lignin that can be converted into carbon atoms during the activation process (Pari et al., 2008). The FC of the activated carbon of FTS waste at 750°C, 850°C, and 950°C for heating durations at 30 min, 60 min, and 90 min fulfilled the SNI quality standard ≥ 65%).

The ACB determines the ability of active carbon to adsorb gases. The activated carbon of FTS waste ACB ranges between 8.26%–9.15% (Table 4). Activation temperature has a significant influence on the ACB at the 5% test level (Table 3). It was shown that the ACB tends to rise along with the increase in temperature activation (Fig. 7). The average ACB (8.67%) of FTS waste activated carbon is lower than the activated carbon of teak wood sawdust at 38.85% (Erawati and Afifah, 2019). The ACB FTS waste activated carbon is also lower than that of activated carbon from bagasse at 13.40% (Sujarwo, 2009). Hendra and Pari (1999) reported that the low ACB is caused by activated carbon pores that still contain many non-carbon compounds attached to the surface. However, the high adsorption of activated carbon to benzene describes the surface of the activated carbon is more non-polar, which has higher capacity to adsorb non-polar solvents but lower in adsorbing polar solvents (Pari et al., 2008). The ACB of activated carbon of FTS waste at 750°C, 850°C, and 950°C and heating durations of 30 min, 60 min, and 90 min ranged from 8.26% to 9.15%, which does not comply to the SNI quality standard (≥ 25%).
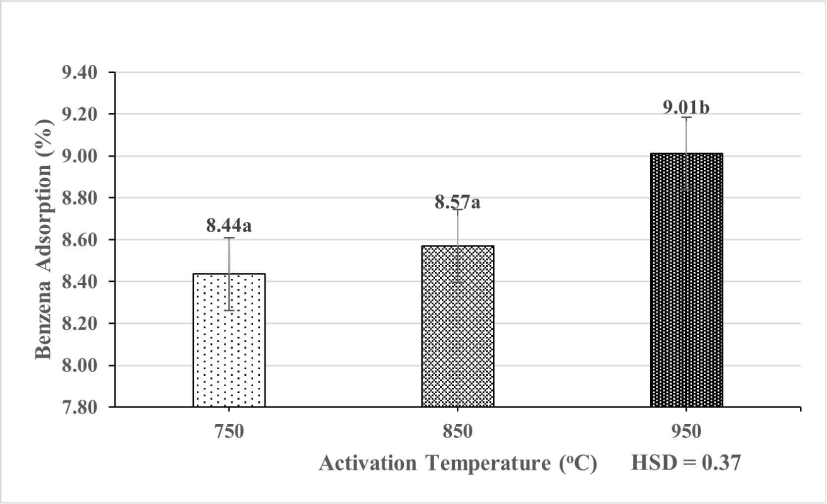
The identification of the ACM aims to determine the ability of activated carbon in colored liquids. The amount of methylene blue adsorbed indicates the adsorptive capacity of carbon to larger molecules (Noszkó et al., 1984). Methylene blue is a dye which can be used as a model for visible pollution and as an indicator of microporosity, hence its adsorption is frequently used to evaluate adsorbents quality (Bestani et al., 2008). The results showed that activated carbon of FTS waste adsorption to methylene blue ranges between 72.34 mg/g–100.23 mg/g (Table 4). There was a significant interaction between activation temperature and heating duration at the 5% test level (Table 3). The average ACM of FTS waste activated carbon is 83.84 mg/g. This ACM is higher than that reported by Yusop et al. (2022) for the activated carbon of teak wood waste (66.69 mg/g). However, the ACM is lower than the prior work on gumitir-activated carbon of 199.93 mg/g (Sahara et al., 2017) and adsorption capacity of bagasse (121.91 mg/g–124.80 mg/g; Sujarwo, 2009) and activated carbon of bamboo (183.3 mg/g; Liu et al., 2010). The lower ACM of FTS waste activated carbon indicates that the formed pores is not effective at adsorbing molecules with more than 1.5 nm dimension. The pore size of activated carbon affects the adsorption mechanism of methylene blue (Duy Nguyen, 2019). The ability of activated carbon to adsorb methylene blue shows the number of micropores formed during the activation process (Imawati and Adhitiyawarman, 2015). The adsorption of activated carbon of FTS waste to methylene blue tends to rise with an increase in temperature activation and heating duration (Fig. 8). The ACM of activated carbon of FTS waste at 750°C, 850°C, and 950°C for heating duration at 30, 60, and 90 min ranged from 72.34 mg/g to 100.23 mg/g; this does not comply with the SNI quality standard (≥ 120 mg/g).
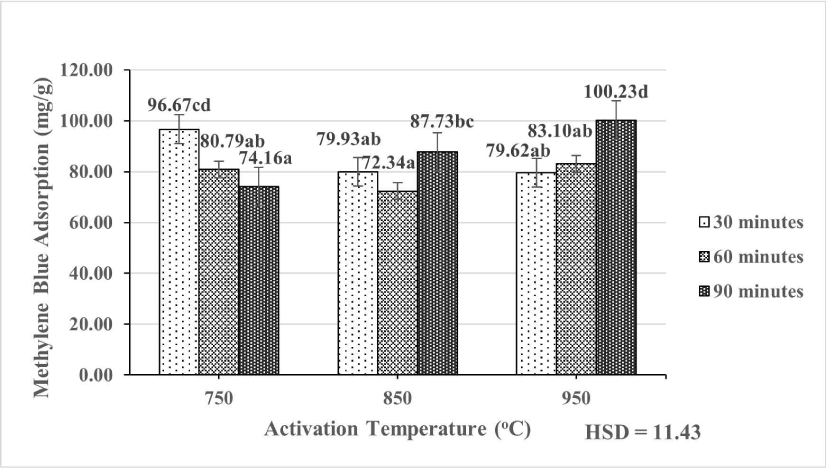
The ability of an adsorbent to remove colors can be estimated through the adsorption of iodine from aqueous solutions using the iodine number determination test (Bestani et al., 2008). Therefore, the identification of the adsorption capacity of activated carbon against iodine aims to determine the ability of activated carbon to absorb a colored solution. The results showed that the ability of FTS waste activated carbon adsorption of iodine ranged between 702.62 mg/g–948.18 mg/g (Table 4). The data and analysis of the variance of the ACI of FTS waste activated carbon showed a significant interaction between activation temperature and heating duration at the 5% test level (Table 3). The highest activated carbon ACI (948.19 mg/g) was higher than that of sawn teak-activated carbon, at 837 mg/g (Erawati and Afifah, 2019); the activated carbon content in palm oil fronds (888.55 mg/g; Maulina et al., 2020) was lower than that in bagasse (1,036.18 mg/g; Sujarwo, 2009). Adsorbents with a high iodine number can be utilized for adsorbing small amounts of substance because they have a large potential surface area (Noszkó et al., 1984).
This research showed that the iodine adsorption capacity of FTS waste activated carbon tends to increase with increasing activation temperature and heating duration (Fig. 9). Prior research reported that increasing the heating duration will increase the iodine adsorption until the optimum time is reached (Hudaya and Hartoyo, 1990). Moreover, increasing the activation temperature will increase the iodine adsorption of activated carbon (Hudaya and Hartoyo, 1990).
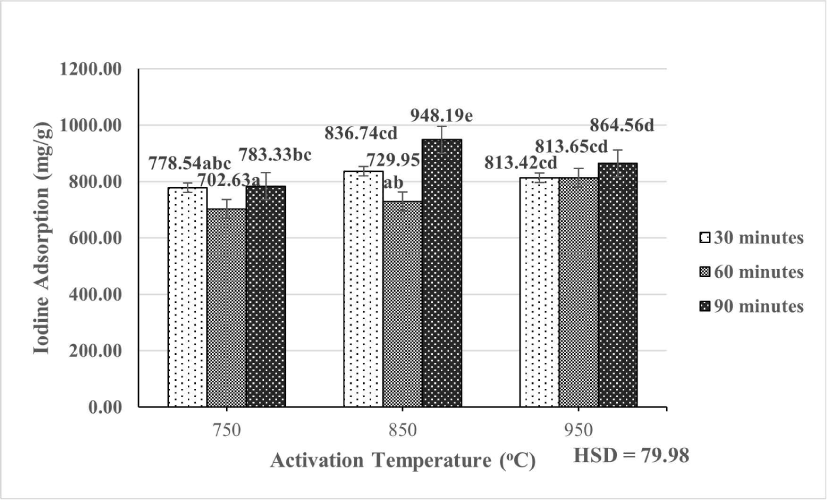
The iodine adsorption capacity of activated carbon depends on the surface area of the activated carbon and the adsorption process is related to the number of micropores (Hartanto and Ratnawati, 2010); therefore, the number of micropores formed affects the level of iodine adsorption of activated carbon (Imawati and Adhitiyawarman, 2015). Furthermore, during the activation process the bond between C and H is completely released, so that there is a shift in the crystallite carbon plate to form new pores and develop pores that have been formed so that the capacity of activated carbon adsorption to iodine indicates the number of micropore structures formed (Hendra and Pari, 1999). The formation of more micropores reflects an increase in the surface area of activated, which also increases the iodine adsorption capacity of activated carbon. The ability to adsorb iodine of activated carbon indicates that activated carbon is a suitable material in wastewater treatment. A higher adsorption capacity of activated carbon for iodine can adsorb or remove pollutants in wastewater (Etris and Ekawati, 2022). Due to its iodine adsorption capacity, FTS waste activated carbon could be categorized as a potential material which can be further developed as an absorbent. The average iodine adsorption capacity of activated carbon of FTS waste was 807.89 mg/g and the highest was 948.19 mg/g, which was obtained using an activation temperature of 850°C and heating duration of 90 min. This result complies with the SNI quality standard (≥ 750 mg/g).
4. CONCLUSIONS
Based on the characteristics of FTS waste activated carbon, especially the ACI, FTS waste is categorized as a potential raw material for activated carbon production. From this research, it is concluded that the best quality of FTS waste activated carbon was obtained from the combination of an activation temperature of 850°C and a heating duration of 90 min. The activated carbon produced has the following quality parameters: yield of 75.61%; MC of 1.27%; VMC of 9.98%; ASH of 5.43%; FC of 84.58%; benzene absorption capacity of 8.58%; methylene blue absorption capacity of 87.73 mg/g; iodine adsorption capacity of 948.19 mg/g. Due to the ability of FTS waste activated carbon to adsorb iodine, the conversion of FTS waste to activated carbon is categorized as a potential method to increase the value of FTS waste.