1. INTRODUCTION
In the early 20th century, Indonesia’s forests “boomed” with long rotation logs (aged > 40 years) with an average diameter of > 45 cm. Since then, the degradation of natural forests due to extensive forest exploitation has caused a decline in the production of conventional old-aged, large-sized timber. This has motivated the wood-processing industry to utilize small-diameter wood from fast-growing plants. Currently, almost 90% of the wood used in the wood processing industry is supplied from fast-growing plantation forests, such as short-rotation teak, jabon, sengon, and rubberwood (KLHK, 2021). The age shift of logging activity from long-rotation to short-rotation trees of 5–15 years impacts the quality of the resulting processed wood (Basri et al., 2022a; Martha et al., 2021). The wood from short-rotation crops has poor physical and mechanical properties, as well as low resistance to biologically degrading organisms (Arsyad et al., 2019; Basri et al., 2021; Hadi et al., 2022a; Vidaurre et al., 2018). However, with the development of wood-processing technology, it is now possible for the industry to improve the inferior properties of wood, including densification technology and chemical modification. Wood densification is an effort to reduce the volume of wood cavities such that wood becomes denser, more stable, and stronger (Basri et al., 2022b; Budakçı et al., 2016; Choowang and Hiziroglu, 2015; Darwis et al., 2017). The chemical modification of wood involves the reaction between an active chemical and OH functional groups (hydroxyl groups) in the wood cell walls (Ross, 2021), thus forming strong covalent bonds (Gérardin, 2016; Hill, 2006; Rowell, 2013; Sandberg et al., 2017). Modifying wood by mixing diluted resin with teak sawdust extract can increase the density, strength, and durability of young teak and rubberwood (Balfas, 2019; Basri and Balfas, 2015). Wood chips, bark, and small pieces of wood from logging activities in the forest are extensive and can be higher than 10% for every m3 of wood produced (Soenarno et al., 2018; Suhartana and Yuniawati, 2018). Thus, the amount of wood produced from Indonesian plantation forests alone, which averages 36,722,147.48 m3/year (KLHK, 2021), has generated approximately 3,672,147 m3 of biomass waste. These waste products could be used to improve the inferior properties of wood (Trisatya et al., 2023) and as a modifying agent in the wood modification process.
This study is a continuation of previous research in which the impregnation of materials fabricated from a mixture of wood vinegar (WV) and animal waste increased the resistance of jabon wood to subterranean and drywood termites (Arsyad et al., 2019). The animal waste used in our previous study was used as a solidified material called kak, which melts when dissolved in hot water. Kak or gum is known as mini glue and is commonly used for making glass/crushed glass coatings on kite strings, as well as for liquid glue ingredients (Anonymous, 2015). This material is composed mostly of collagen proteins, which easily dissolve in hot water (Arsyad et al., 2019). Kak is extracted from cow skin, and bone waste contains the main chemical components, which are a mixture of protein, fat, and lipid polymers (Arsyad et al., 2019; Wulandari, 2016). When it cools, the material hardens to create a strong bond that becomes even stronger in the subsequent drying process. Kak lowers the pH of the mahogany tannin adhesive ingredient and increases its solid content and viscosity (Santoso et al., 2020). Because the physical and mechanical properties of this impregnated wood have not been investigated, this recent study aimed to scrutinize the physical and mechanical properties of jabon wood impregnated with animal-based adhesives dissolved in WV or water, with or without the addition of borax.
2. MATERIALS and METHODS
Five-year-old jabon stems were harvested from the host trees, which grew in community forests located in Sukabumi, West Java. Jabon stems were sawn into several boards and air-dried to a moisture content (MC) of approximately 12% to test the physical and mechanical properties of the wood samples. These boards then underwent specific impregnation treatments as well as non-impregnation (control). WV was first obtained by dry distilling (pyrolyzing) a mixture of wood shavings and sengon wood bark in a modified drum equipped with an intricate condenser (cooling system). Concurrently, the smoke generated by the pyrolyzing drum was channeled to the cooling system, which condenses it into a liquid distillate or WV.
After undergoing various manipulated impregnating treatments, the sawn wood boards (at 12% MC) and the control were cut into several samples with varying dimensions based on the intended tests on physicomechanical properties. The following physical properties were measured using the specified samples: MC (2.5 cm × 2.5 cm × 2.5 cm section), dimensional stability in the radial [1 cm in tangential (T) × 10 cm in radial (R) × 1 cm in longitudinal (L)] and tangential [10 cm (T) × 1 cm (R) × 1 cm (L)] direction, wood density (2.5 cm × 2.5 cm × 2.5 cm), mechanical properties, i.e. modulus of elasticity (MOE) as well as modulus of rupture [MOR; 2.5 cm (T) × 2.5 cm (R) × 42 cm (L)], and compression strength [CS; 2.5 cm (T) × 2.5 cm (R) × 10 cm (L)]. Five replicates were used for each treatment and the no treatment (control). As supporting data, the crystallinity of the impregnated wood and the control was tested in the form of their corresponding wood sawdust. The degree of crystallinity (CD) was determined using an XRD-7000 instrument (Shimadzu, Kyoto, Japan). The Equation (1) for CD calculations is as follows:
where CD = crystallinity degree (%), Acryst = area of the crystalline region, and Atotal = total area of the crystalline region + amorphous region.
Kak resin in the form of solid granules, which contained mostly animal protein, was extracted from hides, bones, cartilage, and tendons, as previously described (Arsyad et al., 2019). The resin was dissolved in distilled water with a temperature of around 65°C–70°C, then mixed with WV as an impregnating liquid. The formulation of the impregnating liquid/solution used in our previous research is presented in Table 1 (Arsyad et al., 2019).
Prior to impregnation, all the board samples were oven dried at 65°C to reach 10% of MC, weighed and measured the dimensions. The impregnation of each formulated solution (Tables 1 and 2) into the wood structure was initiated by applying a vacuum for 30 min, followed by a pressure of 12 kPa for 60 min. The basis for determining and using those quantitative figures was based on the preliminary trial, where the optimum temperature used for jabon woods was 65°C, above which the wood sustained the end-check-in defects. Furthermore, the use of 12 kPa pressure for 60 min was regarded as optimal, referring to a previous experiment (Basri and Balfas, 2015). Furthermore, all the samples were dried again until the water content reached 10%, weighed, and measured.
Each impregnation solution in Table 1 was characterized in terms of its viscosity, density, pH, and solid content by referring to SNI 06-4567 (1998).
Based on various manipulated impregnation solutions (Table 1), each of the impregnated jabon woods, including the control, was tested for physical [e.g., MC, density, weight percent gain (WPG), water uptake (WU), swelling, and crystallinity] and mechanical properties [e.g., bending strength, MOE, MOR, and compression strength parallel to grains (CS)]. The degree of crystallinity of the treated and untreated wood samples was analyzed using an X-ray diffraction instrument (XRD 7000, Shimadzu).
The MC, density, MOE/MOR, and compressive strength were determined according to ASTM D143-22 (2022). The dimensional stability was measured as the anti-swelling efficiency (ASE). Dimension development (swelling) of the test sample in the radial and tangential directions refers to Basri and Balfas (2015), carried out by observing changes in the dimensions of the impregnated sample immersed in a specific chamber with the immersion periods of 5 minutes, 10 minutes, 30 minutes, 1 hour, 4 hours, and 24 hours. The swelling value of the sample owing to immersion can be calculated using an Equation (2) below:
where S is the swelling percentage, D1 is the sample dimensions under wet conditions (mm), and D0 is the sample dimensions under dry conditions (mm).
The effectiveness of the dimensional stabilization treatment under certain conditions was determined by calculating the anti-swelling efficiency (ASE) value using the Equation (3) below:
where ASE is the percentage of anti-swelling efficiency, S0 is the swelling value of the untreated wood (control), and S1 is the swelling value of the treated wood.
A completely randomized design with a single factor was used to evaluate the tested data on the physicomechanical properties of impregnated wood, as well as the control, using SPSS ver. 22. There were five replicates of the eight combinations of impregnating solutions and one control (untreated) sample each. Analysis of variance (ANOVA) was used to determine the influence of the treatment on density, swelling, MOE/MOR, and CS. Duncan’s test was performed to determine whether the factors were significantly different.
3. RESULTS and DISCUSSION
The characteristics of the impregnation solution based on the composition of the materials used are presented in Table 2.
WV derived from the pyrolysis of sengon wood waste (bark and wood particles) exhibited a pH of 3.32. This pH was in line with the pH of WV commonly obtained from the pyrolysis of wood or other lignocellulosic materials, which ranges from 2.90 to 3.50 (Theapparat et al., 2018). The acidic nature of WV could be due to the presence of weak organic acids, such as formic acid, acetic acid, and phenol (Sjöström, 1993; Theapparat et al., 2018). Further, with the incorporation of kak resin and (+) distilled water, the pH value of the impregnating solution from WV and (+) kak resin were raised to 4.40–4.74 from pH 3.32 (Table 2). The increase in pH could have been caused by dilution with water (pH neutral or approximately 7.0) and kak incorporation. This indicates that the kak resin was acidic because the pH of hide glue, of which the kak resin is an example, normally ranged from 6.5 to 7.4 (Blomquist et al., 1983). Meanwhile, the pH value of kak resin and (+) water (without WV) was 8.00–8.46, strengthening the acidity of kak resin and WV. The addition of 4% borax to the impregnating solution of WV and (+) kak resin raised the pH of the solution to 5.30–6.15 and in aqueous solutions to 9.00–9.46 (Table 2). This is because borax is a strong acidic salt (Na2B4O7.10 H2O) with a pH value of 9.5 (Suheryanto, 2012), which further affected the pH of the solution.
The viscosity of the impregnating solution with a WV solvent was 2.87–4.89 poise, higher than that with an aqueous solvent, which was 1.24–1.87 poise (Table 2). Verdiana et al. (2018) reported organic resins dissolve more easily in phenol and methanol solvents than water because organic resins (including kak resin) are more hydrophobic. In our previous study (Arsyad et al., 2019), liquid chromatography-mass spectroscopy analysis showed that the chemical components of pure WV were dominated by phenolic groups (rather weak acids), making it easy to dissolve the kak resin. Interestingly, the addition of 4% borax into the impregnating solution containing WV solvent increased the viscosity of the solution to 4.50–8.06 poise, while the viscosity reached only 1.24–2.36 poise when the impregnating solution was water only. The increase in viscosity of the impregnating solution in the WV solvent could be due to the basic conditions derived from borax addition, which could react through a mild salting (acid-basic) reaction with either kak or WV, improving the interaction of the kak-WV-borax mixture and increasing the viscosity of the solution. In a previous study, the pH of kak was 7.02 (Santoso et al., 2020). Related to the adhesive function, this material can be used as a substitute agent for resorcinol, which can lower the pH of the mahogany tannin adhesive ingredient, thereby accelerating the copolymerization reaction between different tannin monomers and phenolic compounds and increasing its solid content and viscosity (Santoso et al., 2020). This also occurred when the solid content and viscosity in the impregnating solution of WV, kak (8%–10%), and borax were greater than those in the impregnating solution of water and kak (8%–10%; Table 2). Furthermore, these results indicate that the kak resin particles, especially protein and WV compounds, especially phenolic compounds in the former impregnating solution of WV, became more copolymerized, larger in size, and more hydrophobic colloidal than those in the latter impregnating solution (Atkins, 1986). Notably, the copolymer derived from kak has the potential to promote environmentally friendly resin-impregnated fast-growing wood.
The weight percentage gain (WPG) of each impregnated wood sample is shown in Fig. 1. WPG was determined by calculating the differences between the oven-dry weight of the impregnated wood and the oven-dry wood before impregnation. The WPG of impregnated wood is important because an increase in WPG is commonly correlated with a decrease in the equilibrium moisture content and the resistance of wood to fungal decay (Hill, 2006; Hosseinpourpia and Mai, 2016).
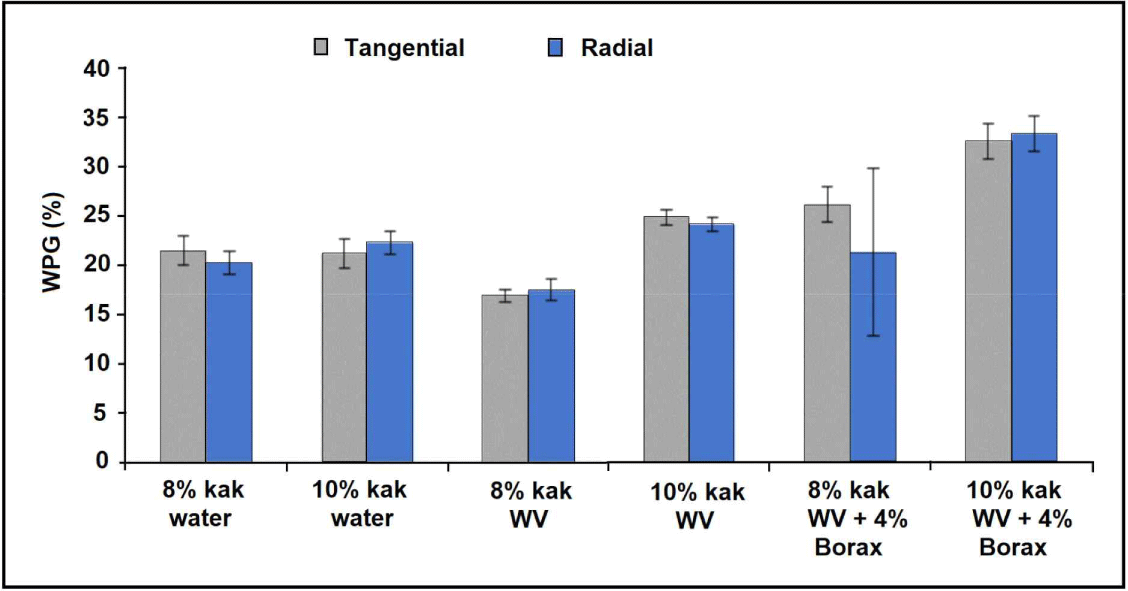
Wood impregnation with a mixture of kak, WV, and borax resulted in significantly higher WPG values than the others (Fig. 1). This might be attributed to the weak acidic mixture (pH 5.30–6.15), high viscosity, and high solid content, especially the mixture of WV, 10% kak, and 4% borax (Table 2). Such high viscosity strengthened the indication that the incorporation of borax and WV in the impregnation mixture promoted the presumed intensive copolymerization between the kak monomers and WV compounds into a higher molecular weight, larger size, and longer-chained copolymerized kak resin, thereby causing a significant increase in WPG. The greater the kak concentration, the greater the increase in the WPG of the impregnated wood. These WPG values were relatively and proportionally similar in the radial and tangential directions of the wood fibers. The only exception was the mixture of 8% kak, WV, and 4% borax, where the WPG in the tangential direction was remarkably greater than that in the radial direction. This is because, there were more materials in the wood cell walls in the tangential direction, which could absorb more of the impregnated kak resin (Hoadley, 2000). Likewise, Hadi et al. (2022b) studied the use of furfuryl to impregnate jabon wood and found an increase in the WPG compared to unimpregnated wood.
The highest WPG value (30%) was obtained from a mixture of 10% kak resin and 4% borax impregnated in WV (Fig. 1). However, the use of at least 8% kak in a mixture of WV and 4% borax has been effective in increasing the resistance of jabon wood from class IV (untreated wood) to class I against both subterranean and dry wood termites (Arsyad et al., 2019). This is because the addition of borax to a mixture of WV and 8% kak significantly increases the percentage of phenolic moieties (Arsyad et al., 2019). These phenolic moieties are toxic to termites (Tascioglu et al., 2012).
The high solubility of the impregnation solution using the vinegar solvent, especially with the addition of 4% borax, resulted in a high density, viscosity, and solid content of the impregnation solution (Table 2). These changes in the physical properties of the impregnation solution have a direct effect on the changes in the WPG of the impregnated wood.
WU is the water-absorbing ability of wood. The lower the WU value, the lower the wood’s ability to absorb water, indicating that the wood is more hydrophobic and dimensionally more stable. The WU values of the impregnated wood based on the type of solvent (WV or water) are presented in Table 3, while the WU values of the impregnated wood based on the type of impregnation solution are presented in Fig. 2. This shows that the wood impregnated with the WV solvent had a lower WU value than the wood impregnated with water or untreated wood (Table 3).
Solvent | Water uptake (%)1) |
---|---|
Wood vinegar + kak | 64.96a |
Water + kak | 93.92b |
Without treatment (control) | 140c |
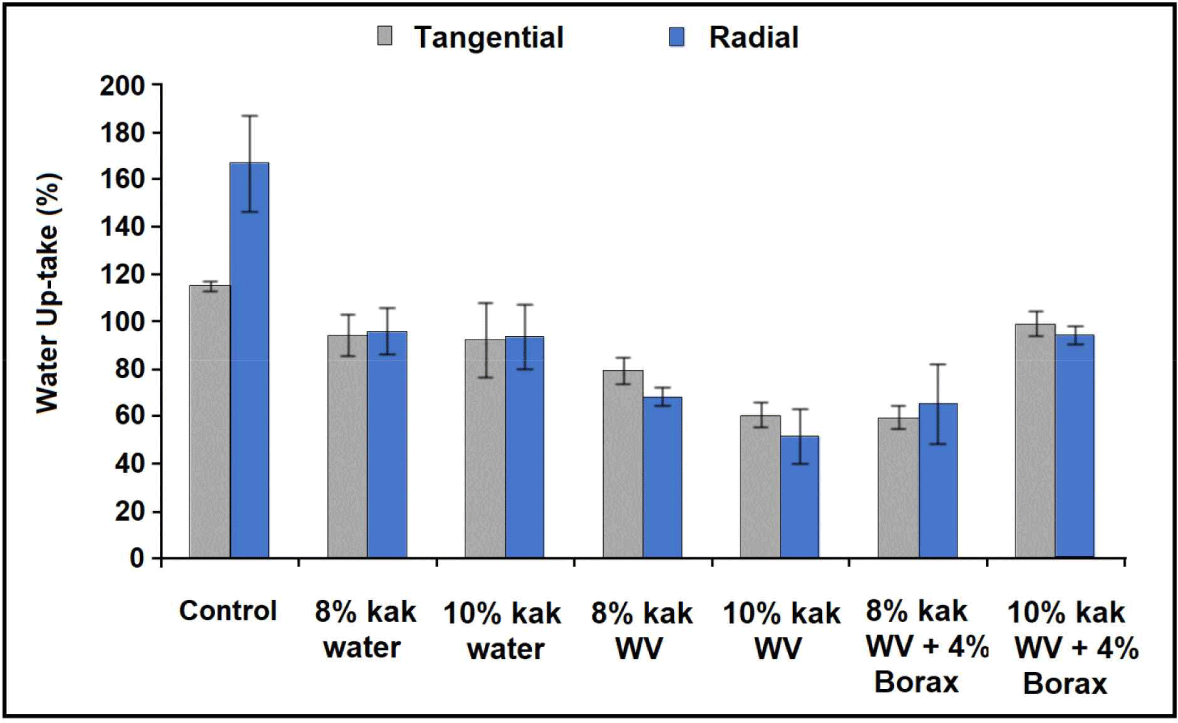
The table shows that the control wood exhibited the highest WU. The lowest WU was obtained when impregnating jabon with the mixture of WV and kak. Such a low value indicates that copolymerization occurred between kak monomers and WV compounds, resulting in longer-chained, larger-sized, and greater molecular weight copolymerized kak products, which could enter the wood structures, thereby creating strong fiber-kak-fiber or cellulose-kak-cellulose bonds and increasing the wood hydrophobicity through hydrogen and strong covalent bonds, especially within the long-chained kak-WV copolymer. The second lowest WU (93.92%) suggests that the kak resin that penetrated the wood did not undergo copolymerization without the presence of WV and, therefore, did not provide a strong bond with the wood fibers because only hydrogen bonds without covalent bonds were applied (Hoadley, 2000).
Statistical analysis showed that the WU values were not significantly different (p > 0.05) between the 8% and 10% kak concentrations or between the tangential and radial directions, except for the control wood. The WU of the control wood in the radial direction was much greater than that in the tangential direction, which could be due to more lumen being available in the radial direction, thereby being easily filled by water. However, the combination of 8% and 10% kak concentrations for the types of mixtures showed highly significant WU values (p < 0.01). The wood control had the highest WU value of all the other impregnation treatments (Table 3, Fig. 2). The lowest WU values, especially for the mixture of WV and 10% kak (Table 3, Fig. 2), could be attributed to the roles of aqueous WV, which contained methanol, acetic acid, and phenol compounds (Theapparat et al., 2018) that all of which lowered the surface tension of the impregnating WV and 10% kak mixture (Atkins, 1986). This lowering enhances the wettability of the mixture, thereby easily bringing the inherently more hydrophobic kak resin into the wood structure and imparting wood hydrophobicity.
ASE indicates dimensional stability, implying that wood becomes more hydrophobic. The results of the ASE test, which were obtained from the swelling percentage of the impregnated wood based on different impregnation solutions compared with that of the untreated wood, are presented in Figs. 3 and 4. Statistical analysis showed that there was no interaction (p > 0.05) between the two applied treatments (wood fiber orientation and type of concentration).
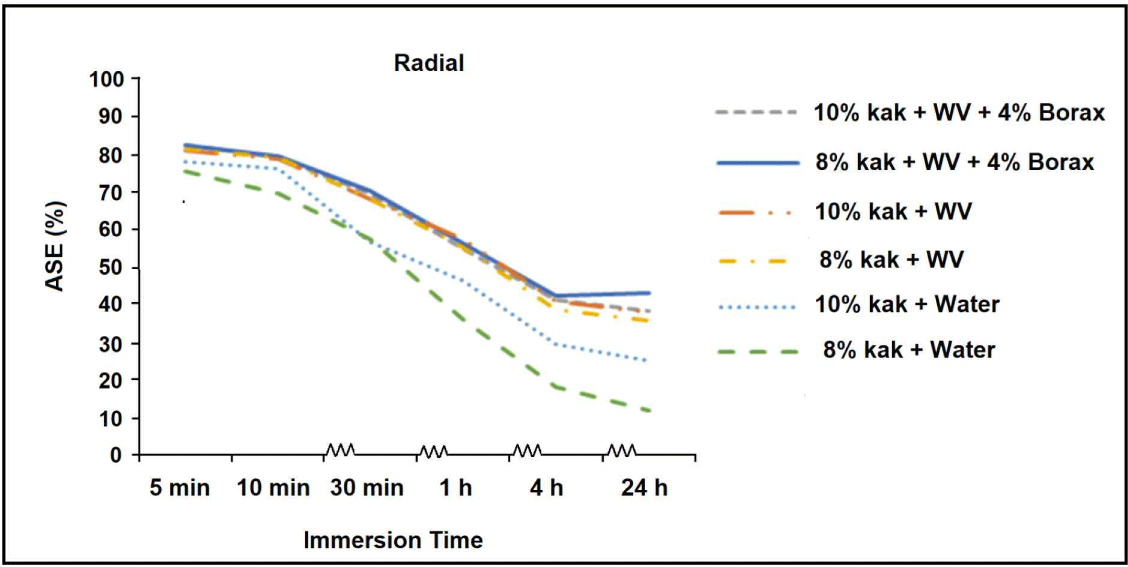
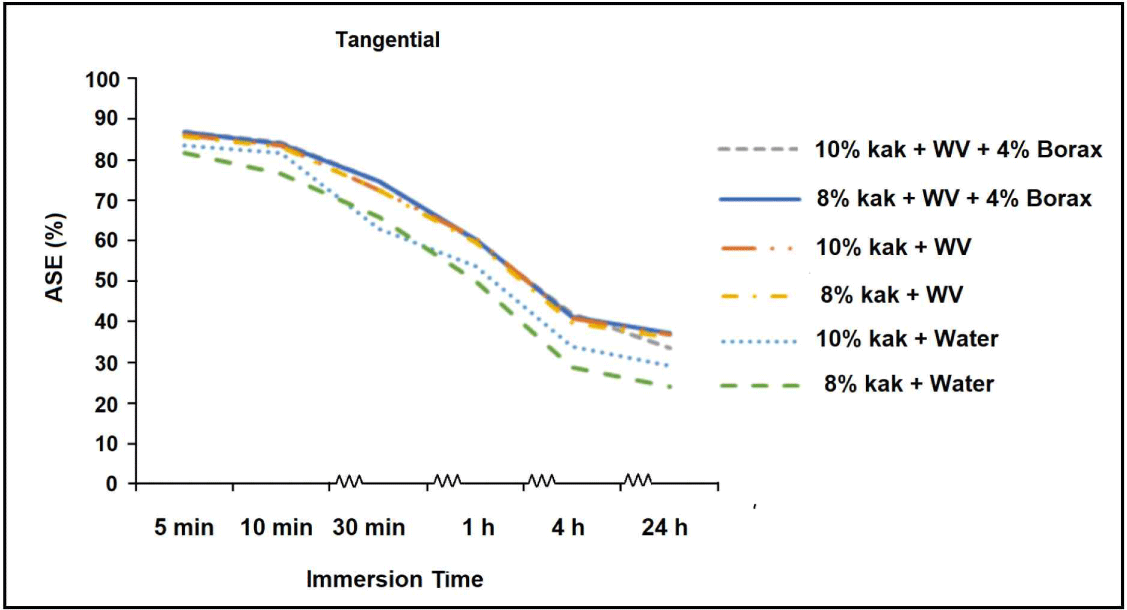
As shown in Figs. 3 and 4, the ASE values tended to decrease with increasing immersion time in water. This is because the longer the immersion time, the greater the chance of the more hydrophobic kak resin entering the wood. The ASE values in the tangential direction were relatively similar to the ASE values in the radial direction, except for the wood impregnated using the WV solvent, whereby the ASE in the tangential direction was slightly higher than that in the radial direction. This is because more materials of the wood cell wall and fewer lumens were present in the tangential direction; therefore, after the impregnation treatment with WV and borax, a more hydrophobic barrier was provided for the water or aqueous solution to enter deeper into the wood. Furthermore, the ASE value of the woods impregnated with a mixture of WV, 8%–10% kak, and 4% borax appeared to be the highest in the tangential and radial directions. This also strengthened the presumed occurrence of copolymerization between the kak monomers and WV compounds into larger, more hydrophobic kak copolymers, thereby increasing the wood ASE. The impregnated wood that used water as the solvent had a lower ASE value than that impregnated with the WV solvent. This is because of the capillary nature of water, which interacts more easily with wood cell wall molecules because of its polarity and rich hydroxyl groups. Therefore, the wood can easily swell, decreasing the ASE values of the impregnated wood. The decrease in water uptake (WU) was followed by an increase in the ASE value after treatment. Similar to jabon wood, the impregnation of furfuryl adhesive, coupled with Fe3O4 as a penetrating inorganic electrolyte into sengon wood as a fast-growing species, resulting in an increase in wood ASE and a decrease in WU (Laksono et al., 2023).
The WU and ASE values are also supported by the crystallinity data for the impregnated wood samples (Table 4). The wood impregnated in the WV solvent had a crystallinity of 29.81%, which was higher than that of the wood impregnated in water (25.52%). The lowest crystallinity (18.73%) was obtained for the untreated jabon wood. Thus, these crystallinity values had a positive impact on the ASE values and a negative impact on the WU values.
Sample | Crystallinity (%) |
---|---|
Untreated jabon wood | 18.73 |
Water + kak 8% | 25.52 |
WV + kak 8% | 29.81 |
WV + kak 8% + borax 4% | 32.56 |
The untreated jabon wood structure (control) was dominated by amorphous structures, which comprised mostly hemicellulose as shorter-branched polymers and other non-cellulosic polymers. Wood with an amorphous structure is more hygroscopic because of the presence of more free OH groups, rendering its dimensions unstable (Rowell, 2013). Therefore, even though the structure of the jabon wood impregnated with an 8% kak formula using a water solvent is more crystalline than the structure of the unimpregnated jabon, it is still susceptible to microorganisms, such as blue stains. In this study, WV as an impregnation solution and solvent provided impregnated wood with better properties than water. This is because the phenolic-rich molecules in WV (Arsyad et al., 2019) can also function as adhesives. The density of the jabon wood impregnated with various treatments was much higher than that of the untreated/control wood (Table 5). The impregnation solution containing kak resin, especially WV and 4% borax, significantly increased the density of Jabon wood (Table 5). This was presumably owing to the higher viscosity, solid content, and density of the impregnating solution dissolved in the WV and 4% borax solution compared to that dissolved only in water (Table 2). Cahyani et al. (2023) stated that wood density is affected by, among others, the wood porosity, chemical content (lignin, cellulose, and extractives), characteristics of wood fibers (cell wall thickness, crystallinity, wood species, and age), and types of impregnated materials (natural glues and manufactured adhesives). The increase in density was also followed by an increase in the bending strength (MOE and MOR) and CS of the impregnated wood (Table 5). Similarly, in an experiment on the manufacture of particleboards from particular wood species bonded together with a resin, it was found that the density of particleboards correlated positively with their mechanical strength properties (Hwang et al., 2021). Furthermore, the bending strength of jabon wood impregnated with WV was significantly greater than that of jabon wood impregnated with water or untreated wood. The greater the MOE, MOR, and CS of the wood species, the more rigid and stronger the ability of the wood to withstand the load.
The impregnated wood, supported by ANOVA and Duncan’s test (Table 5), using WV solvent provided a density increase of 44%–58%, MOE increase of 46%–57%, MOR increase of 29%–34%, and CS increase of 40%–76% compared to the unimpregnated wood. Meanwhile, the wood impregnated with water generated a density increase of 32%–47%, MOE increased by 28%–31%, MOR increased by 14%–27%, and CS increased by 38%–72% compared with the unimpregnated wood. The improvement in the physical and mechanical properties of jabon wood impregnated using WV solvent could be due to the fixation of the impregnated compounds (kak, WV, and/ or borax) in wood cell walls through possible cross-linking as well as copolymerization reactions, especially between kak as an animal-based protein and the rich phenolic-based compounds of the WV.
4. CONCLUSIONS
The physical and mechanical properties of jabon wood can be improved by vacuum-pressure impregnation of animal-based adhesives (kak) in WV or water. Based on these results, the best solvent used for this impregnation system was WV, which provided better physical and mechanical properties for the impregnated wood.
Impregnated wood using WV as a solvent with or without the addition of borax 4% provided a density increase of 44%–58%, ASE radial-tangential of 38%–40% in 24 h immersion, crystallinity increased by 59%–74% MOE increased by 46%–57%, MOR increased by 29%–34%, and CS increased by 40%–76% compared to untreated wood. The wood impregnated with water solvent with or without the addition of borax 4% generated density increased by 32%–47%, ASE radial-tangential increased by 15%–28% after 24 h of immersion, crystallinity increased by 36%, MOE increased by 28%–31%, MOR increased by 14%–27%, and CS increased by 38%–72% compared to the unimpregnated wood.
The incorporation of WV and 4% borax into the impregnating mixture that contained 8%–10% kak resin produced impregnated jabon wood with the best WPG, density, ASE, crystallinity, MOR, MOE, and CS.