1. INTRODUCTION
In Korea, bamboo forests cover approximately 22,998 ha, accounting for 0.36% of the total forest area. Among these forests, Jeonnam Province accounts for 36%, and Gyeongnam Province for 33%. Notably, the Geoje area is the predominant location, responsible for over 80% of moso bamboo cultivation (Yoo, 2018).
From a botanical perspective, bamboo is classified as a perennial Poaceae plant and exhibits wood-like material properties combined with the characteristics of grass, lacking a cambium. This versatile and eco-friendly reproductive material displays rapid growth, yielding bamboo shoots within three to five years. Its remarkable resilience, fertility, and diverse applications make it a promising plant (Park, 2007).
Giant timber bamboo (Phyllostachys bambusoides S. et Z., known as “wangdae” in Korea) and henon bamboo (Phyllostachys nigra var. henosis Stapf, referred to as “somdae” in Korea) are predominantly found in the Jeonnam province. These remarkable varieties have successfully transformed bamboo forests into vibrant recreational spaces and valuable tourism resources. In this region, key products derived from giant timber and henon bamboo are utilized as essential raw materials for crafting bamboo salt, bowls for liquor and rice, and various other exquisite bamboo crafts.
In contrast, moso bamboo (Phyllostachys pubescens Mazel) stands out as a thicker and softer culm than giant timber bamboo or henon bamboo, making it unsuitable for split processing. This type of bamboo is primarily used as a raw material for bamboo shoots (which are abundant in starch) or bamboo charcoal (Park, 2007). The primary regions known for moso bamboo production, such as Geoje, Namhae, and Jinju, face challenges, including overcrowding, an aging bamboo population, low-temperature damage, and snowfall damage. These issues have arisen because of the recent suspension of bamboo shoot production caused by an increase in imported bamboo shoots and a decline in young people’s preference for bamboo shoots, leading to its deterioration and emergence as a pressing social problem (Yoo, 2018).
Giant timber and henon bamboo boast a rich history of cultivation spanning generations in Damyang, which is renowned as the birthplace of bamboo. This locale flourished with a thriving bamboo-crafting industry. In contrast, moso bamboo, imported from Japan in 1926 primarily for bamboo shoots, has a much shorter history in Geoje and regrettably lacks an established bamboo crafting tradition. Moreover, this newer introduction struggled to harness its potential as a prominent tourist attraction due to limited support from the local government.
Bamboo has a distinctive cylindrical shape that provides a well-suited internal space. Furthermore, its outer skin tissue is renowned for its hardness and high density (0.70), whereas the innermost tissue is soft and has low density (0.50) (So et al., 1999). Lee et al. (2001) ranked the dry weight of 3-year-old bamboo bases in the order of hennon bamboo (0.67) > giant timber bamboo (0.61) > moso bamboo (0.57). The green bamboo’s moisture content ranged from 48.9% to 84.2% for giant timber bamboo, 84.0% to 193.4% for henon bamboo, and 42.8% to 96.9% for moso bamboo.
Numerous studies have been conducted to prevent the splitting of cylindrical green bamboo. One approach proposed by Lee et al. (2004) involves using a moisture barrier film, such as Korean paper, for sealing, followed by kiln drying. Kang (2018) reported successful crack prevention by impregnating bamboo with polyethylene glycol and drying it. Park (2008) sought a patent for a technique that entailed removing the nodes formed inside the bamboo prior to drying, effectively averting cracks. Recently, research on hybrid cross-laminated timber (CLT) has been reported (Ahn et al., 2021; Atmawi et al., 2023; Choi et al., 2021; Fujimoto et al., 2021; Yang et al., 2021). In order to use bamboo as a material for hybrid CLT as a substitute for wood, drying of bamboo must be prioritized.
Reviewing recent bamboo drying studies conducted abroad (Dan et al., 2023; Han et al., 2022; Maulana et al., 2021; Sumardi et al., 2022; Yan et al., 2022; Yuan et al., 2022; Zhao et al., 2022), researchers subjected moso bamboo to heat treatment at several different temperature levels (ranging from 100°C to 220°C). Notably, when treated at 140°C, the modulus of rupture (MOR) and modulus of elasticity (MOE) demonstrated improvements in comparison to that of the control sample. However, it became evident that excessive heat treatment adversely affected the mechanical properties of the bamboo. Above 160°C, there were significant reductions in the flexural strength and MOE. For instance, when the sample was heated at 180°C for 30 minutes, the MOR and MOE dropped by 47% and 20%, respectively, when compared to the control.
Despite numerous studies focusing on preventing the splitting of cylindrical green moso bamboo, there is a notable lack of empirical research on the large-scale production of thoroughly dried bamboo poles with exceedingly low moisture content and no splitting. In particular, there is a lack of research on achieving these results solely through heat treatment devoid of any chemical additives or wrapping treatments. Furthermore, this research gap includes information on long (3.7 m) and thick (9–10 cm diameter) moso bamboo poles.
The primary objective of this study was to elevate the importance of domestically underutilized moso bamboo poles by transforming them into high-value products such as fences, interior materials, lighting fixtures, and accessories. A meticulous investigation into the heat treatment of moso bamboo poles was conducted at 140°C, considering previous reports of improved physical properties in comparison to the control (Ya et al., 2013), to achieve this. This study focused on analyzing changes in various physical and drying properties, including color, dimensional changes, specific gravity, moisture content, and splitting, during heat treatment.
2. MATERIALS and METHODS
Green moso bamboo poles (P. pubescens) aged 3–4 years were selected as the raw material for the heat treatment of bamboo. These bamboo poles were sourced from Hacheong, Geoje, Gyeongsangnam-do, Korea, and were precisely cut to a length of 3.7 meters from the base. The average bamboo diameter at the butt end was 9.1 cm, with an average thickness of 8.6 mm. The characteristics of the moso bamboo samples are listed in Table 1.
Species | Height (m) | Clear length (m) | Diameter (cm)1) | Thickness (mm)1) |
---|---|---|---|---|
Phyllostachys pubescens | 13.5 ± 0.5 | 4.4 ± 0.6 | 9.1 ± 0.34 | 8.6 ± 0.25 |
The untreated green bamboo poles were gently wiped with water along the longitudinal fiber direction to begin the thermal treatment process. These bamboo poles were then subjected to thermal treatment without the use of steam pressure. A cylindrical commercialized heat-treatment kiln (dimensions:1.8 meters in width, 1.8 meters in height, and 8 m in length) was used for this purpose (Fig. 1). The processing time was meticulously adjusted through various stages, including pretreatment (6–8 hours at 60°C), cooking (8–10 hours at 100°C), steaming (26–30 hours at 120°C), heating (4–6 hours at 140°C), and finally, cooling (below 80°C). 500 bamboo poles across three experiments were organized into two bundles and thermally treated.
Test pieces for assessing the physical properties were carefully cut and collected from the green and heat-treated moso bamboo, specifically from the region between the base and the first node, as illustrated in Fig. 2.
The dimensional change (DC) in the length (L) of the bamboo samples (20 poles) was assessed using a tape measure, whereas the dimensional change (DC) in the thickness (T) was measured at the butt end of the bamboo using a Vernier caliper.
Lg: length of green moso bamboo
Lht: length of heat-treated moso bamboo
Dg: diameter of green moso bamboo
Dht: diameter of heat-treated moso bamboo
Tg: thickness of green moso bamboo
Tht: thickness of heat-treated moso bamboo
The weight loss (WL) of the samples after the heat treatment was determined using the following formula:
Wg: weight of green moso bamboo
Wht: weight of heat-treated moso bamboo
The moisture content was measured on a dry-weight basis using a convection-type oven dryer and a precision balance. The moisture content was calculated using the following equation:
Wg: weight of green moso bamboo
Wo: weight of oven-dried green moso bamboo
The MC of heat-treated bamboo (%)
Wht: weight of heat-treated moso bamboo
Whto: weight of oven-dried heat-treated moso bamboo
The specific gravities (SG) of the samples were determined using the common water displacement method. Specific gravity was calculated using the following equation:
W0: weight of oven-dried green moso bamboo
V0: volume of oven-dried green moso bamboo
Whto: weight of oven-dried heat-treated moso bamboo
Vhto: volume of oven-dried heat-treated moso bamboo
Surface color measurements were conducted on both the green and heat-treated bamboo samples using a spectrophotometer (CM-2660d, Konica Minolta, Osaka, Japan). The L*a*b* values and color difference △E were determined using Equation (9). Four measurements were recorded for each sample surface to ensure accuracy.
The color measurements involved the L* value, representing lightness; a* value, indicating the red/green coordinate; and b* value, denoting the yellow/blue coordinate. Notably, the deltas (Δ) for L* (ΔL*), a* (Δa*), and b* (Δb*) can be either positive (+) or negative (–). In contrast, the total difference, Delta E (ΔE*), is consistently positive.
Visual observations were conducted to detect instances of cracks, collapses, or bursts that might have occurred during the heat treatment process. Measurements were taken from ten replicate samples to ensure accuracy. Defects such as cracks were visually observed using a 20 × magnifying glass after heat treatment.
3. RESULTS and DISCUSSION
Table 2 summarizes the change rates of weight, diameter, thickness, and length obtained as a result of heat treatment of the green moso bamboo samples.
Figs. 3–6 illustrate the dimensional changes in the bamboo poles after heat treatment. The initial average length of green moso bamboo samples (average moisture content, 51.6%) measured 3.70 m, while the average length of heat-treated moso bamboo samples (average moisture content, 2.6%) was slightly reduced to 3.69 m, resulting in a negligible length reduction rate of only 0.1%. (Fig. 3).
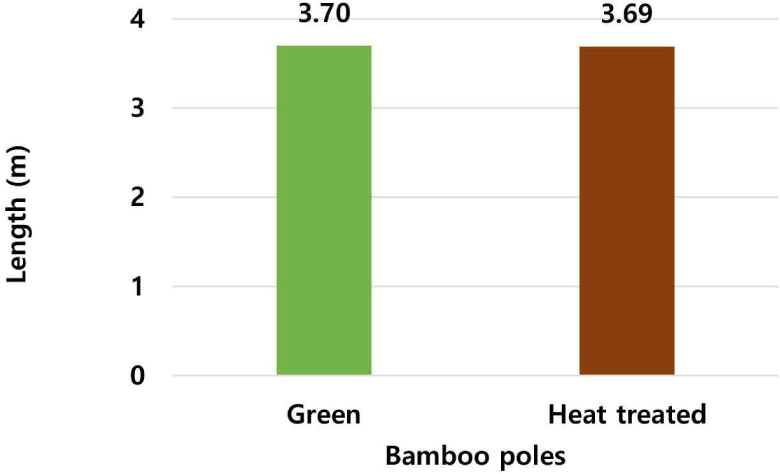
Similarly, the average thickness of the green moso bamboo samples was 8.88 mm, which was reduced to 8.53 mm after heat treatment, accounting for a thickness reduction rate of 3.9% (Fig. 4).
Furthermore, the average diameter of green moso bamboo samples measured 9.06 cm, and the diameter of heat-treated moso bamboo samples decreased to 7.76 cm, representing a diameter reduction rate of 14.3% (Fig. 5).
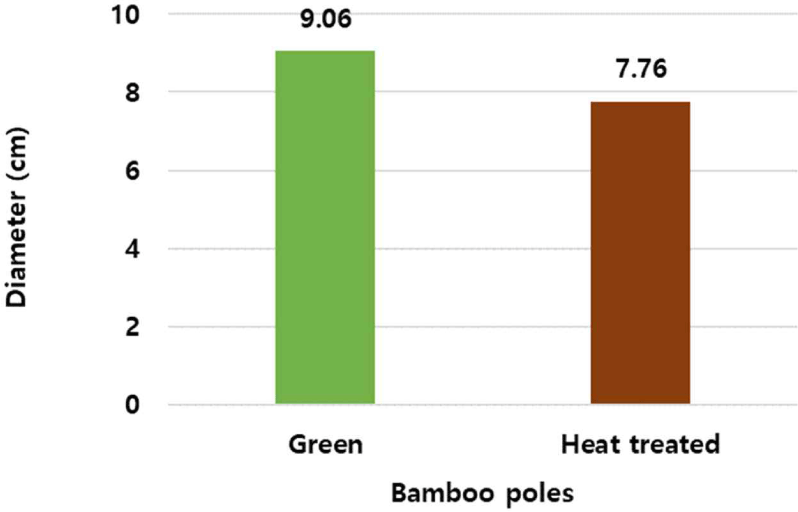
Fig. 6 shows the weight changes of the bamboo poles after heat treatment. Initially, the average weight of green moso bamboo samples was recorded at 8.68 kg. However, after undergoing heat treatment, the weight of heat-treated moso bamboo samples decreased to 5.82 kg, resulting in a weight loss rate of 32.6%. This weight loss at 140°C can be attributed primarily to the evaporation of water, free phenol, and free formaldehyde (Shangguan et al., 2016).
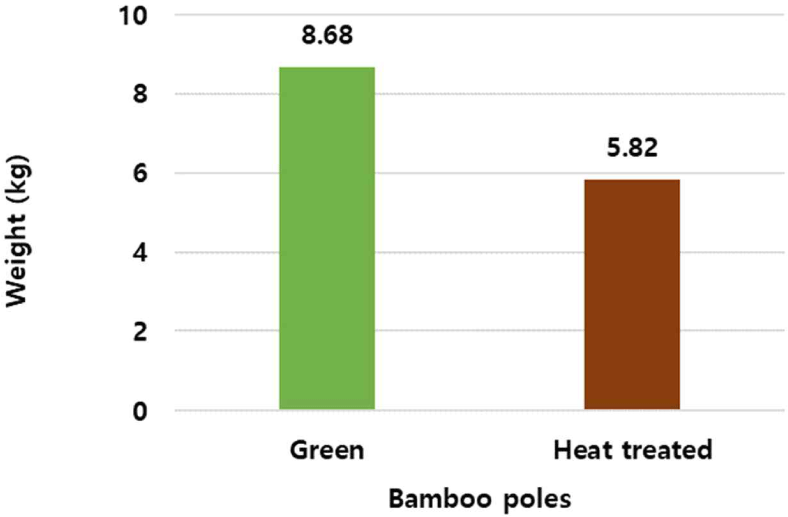
The moisture content and specific gravity changes in the bamboo poles after heat treatment are shown in Table 3.
Bamboo | Moisture content (%) | Specific gravity |
---|---|---|
Green moso bamboo | 51.56 (± 2.20) | 0.62 (± 0.02) |
Heat-treated moso bamboo | 2.58 (± 0.07) | 1.05 (± 0.03) |
Initially, the average moisture content of the green moso bamboo samples was 51.6%. However, after heat treatment, the moisture content of the heat-treated moso bamboo samples decreased significantly to 2.58%. This resulted in a substantial moisture reduction of 94.5%.
Zhang and Yu (2015) reported that the moisture content decreased after undergoing a 4-hour heat treatment. When bamboo samples were subjected to heat treatment in the temperature range of 100°C to 140°C, no significant changes in equilibrium moisture content (9%–10%) were observed. Within the temperature range of 100°C to 140°C, the chemical components in the bamboo exhibited minimal changes. Nonetheless, this study highlighted the significance of meticulous adjustments during heat treatment. By following specific stages, including pretreatment (6–8 hours at 60°C), cooking (8–10 hours at 100°C), steaming (26–30 hours at 120°C), heating (4–6 hours at 140°C), and cooling (below 80°C), researchers were able to achieve a remarkable reduction in moisture content to approximately 3%. Remarkably, this reduction remains stable even under constant temperature and humidity conditions.
The decomposition of hemicellulose decreased the equilibrium moisture content. Furthermore, during the high-temperature saturated steam treatment, the ‘bridge’ reaction occurred between the hydroxyl groups in the cellulose molecular chains of the cellulosic cell wall of bamboo, which releases water and produces ether bonds. The crystallization in quasicrystalline (“paracrystalline”) regions of cellulose may also contribute to the low EMC (Ying et al., 2020).
The average specific gravity of the green moso bamboo samples was 0.62, whereas that of the heat-treated moso bamboo samples significantly increased to 1.05. This represents an impressive increase of approximately 41% in the specific gravity owing to the high-temperature heat treatment. The study findings indicated that as the temperature increased to 140°C, the specific gravity rose from 0.62 to 1.05. This phenomenon is attributed to the shrinking of bamboo cells under external pressure and the plasticization of materials caused by high-temperature steam. Consequently, the treated bamboo became more compact, leading to a higher density than that of the untreated control samples (Wang et al., 2020).
Fig. 7 illustrates the color changes in the bamboo poles following heat treatment. The original green color of the samples transitioned to a dark brown shade, resembling wood. The lightness stability, denoted by L*, showed a significant decrease, indicating the tendency of the bamboo surface to darken during treatment. Initially, raw moso bamboo was green with an L* value of 59.6. The a* value reflects the reddish and greenish tendencies on the surface, whereas the b* value indicates yellowish and bluish characteristics. Shangguan et al. (2016) reported that color change rates were less intense below 170°C than at above 170°C, a trend consistent with the mass loss observed. The initial a* value was –0.61, and the b* value was 16.6. After heat treatment, the moso bamboo acquired a brown color with L*a*b* color values of 24.3, 6.3, and 8.0. The color difference (△E) before and after treatment was quite substantial at 59.5. Lee et al. (2023) presented the color analysis results for giant timber bamboo before and after heat treatment. The L*a*b* color values for green bamboo were reported as 57.95, –1.20, and 19.60, whereas for heat-treated bamboo, the values were measured as 27.78, 4.48, and 3.04, respectively. This color change at 140°C might be attributed to the thermal degradation of hemicellulose’s carbohydrates (such as mannose, xylose, and glucuronic acid) and starch through Maillard reactions (Umemura and Kawai, 2008; Weenen, 1998) and caramelization (Lee and Lee, 2021; Sharma et al., 2018), similar to the color changes observed during coffee roasting.
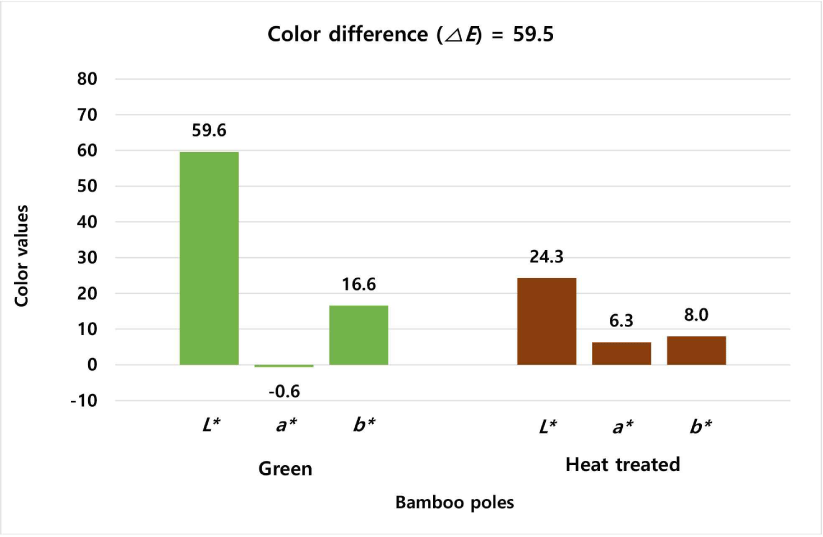
During the evaluation, end checks were observed at both ends of the 1-year-old bamboo, accounting for approximately 19% of the samples (Fig. 8). Additionally, a few instances of collapse (Fig. 9) and V-shaped splits or surface checks (Fig. 10) were observed in the middle of certain juvenile bamboo samples (under one year), comprising only 1% of the total bamboo samples. However, it is worth noting that cracks or splits rarely occurred in mature bamboos older than 3 years. Moreover, a significant number of microsplits were observed in the longitudinal direction around the bamboo nodes (Fig. 11). These microsplits are believed to occur because of the inner diaphragm of the nodal part, which resists drying shrinkage during the heat treatment process.
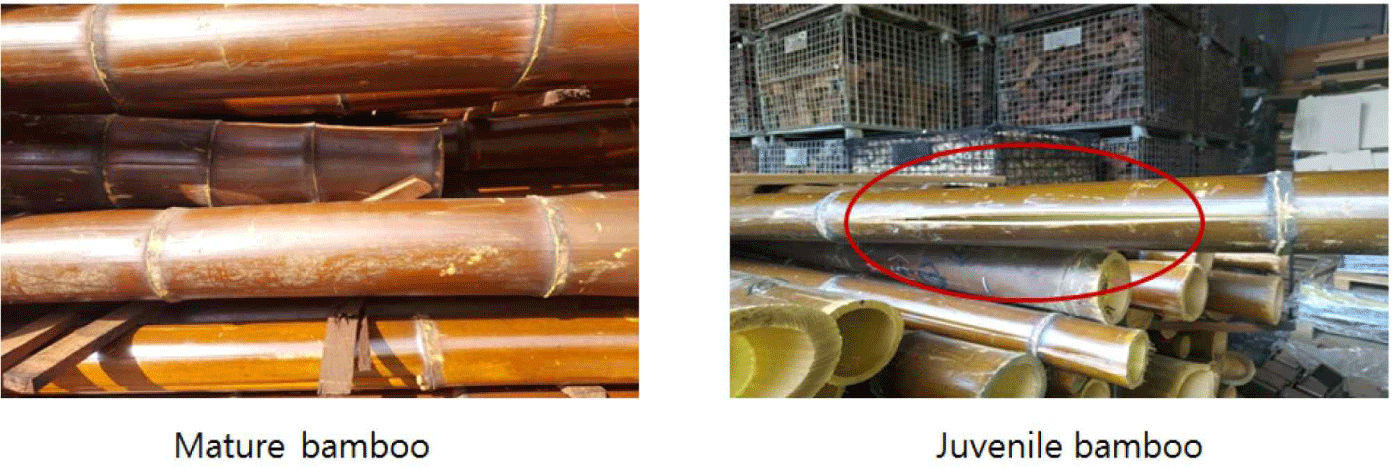
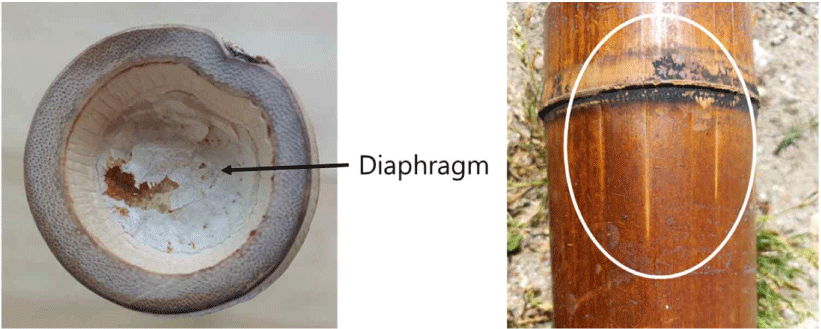
4. CONCLUSIONS
To produce high-value products, such as fences, interior materials, lighting, and accessories, domestically sourced moso bamboo poles with a large diameter of approximately 9 cm and a length of 3.7 m were subjected to heat treatment at 140°C using a commercial large-scale kiln. By applying a well-controlled heat treatment schedule, mass production of moso bamboo poles in an optimally dry state with almost no internal splitting and a moisture content of 3% was possible. Physical properties such as dimensional stability and specific gravity were significantly improved by heat treatment of the green moso bamboo poles. It was confirmed that heat treatment is a useful technology for developing moso bamboo poles as indoor and outdoor building materials. Furthermore, this technology is expected to enable the establishment of a virtuous-cycle management system for moso bamboo forests.
Future research will focus on investigating the changes in physical, mechanical, and chemical properties based on different heat treatment temperatures. This evolving approach to the heat treatment of moso bamboo poles holds significant potential, offering a range of innovative applications and sustainable practices for the times ahead.