1. INTRODUCTION
Biomass is a carbon-neutral raw material with a low sulfur content, thereby reducing air pollution, particularly greenhouse gas emissions (da Silva et al., 2018; Jang, 2022; Jeoung et al., 2020; Zafar et al., 2019). Biomass is a renewable energy source that can support energy fulfillment and promote economic growth (Foong et al., 2020; Foong et al., Ge et al., 2020). In line with the increasing demand for energy and intensifying global warming, the use of biomass as an energy raw material can effectively reduce energy and environmental problems (Foong et al., Heo and Choi, 2018; Foong et al., Li et al., 2017; Mostafa et al., 2019; Song et al., 2018). However, the use of biomass as a raw energy material has caused problems such as low heating value, low energy density, and low hydrophobicity. Therefore, the biomass must be processed to improve its quality and appearance. One model of biomass processing is densification in the form of wood pellets, followed by torrefaction to increase the density of calorific value.
Torrefaction is a mild thermochemical treatment which comprises heating biomass to moderate temperatures between 200°C and 300°C (Prins et al., 2006). This process improves the characteristics of the processed biomass by reducing the moisture content (Arias et al., 2008) and increasing the hydrophobicity of the material. Furthermore, it stabilizes the product (Bridgeman et al., 2008). This study used Calliandra wood (Calliandra calothyrsus) and its bark as raw materials to manufacture wood pellets. This Calliandra species is a fast-growing species that can be harvested annually for up to 15–20 years (Hendrati and Hidayati, 2014). Calliandra wood has a calorific value of approximately 4,600 kcal/ kg of dry wood (Mannetje and Jones, 1992). Furthermore, previous research indicated that the best combination material for producing Calliandra wood pellets was 92.5% and 7.5% for wood and bark, respectively, densified (pelletizing) with a pressure load of 100 kg/cm2 using a single-pelletizer, which provided a calorific value of 4,581.40 cal/g (Hidayatullah, 2022). This study aimed to determine the effect of torrefaction on improving the quality of Calliandra wood pellets to produce high- or premium-quality pellets. Experiments were conducted using the single-pellet method. Single-pellet press technology allows fast, low-cost, and small-scale tests to investigate pelletizing characteristics (Lee and Kim, 2020). The quality of the torrefied Calliandra wood pellets was investigated by evaluating the characteristics of wood pellets without sulfur content, according to the Indonesian National Standard for pellets for household utilization (Badan Standarisasi Nasional, 2018) and Deutsche Industrie Norm (DIN) 51731.
2. MATERIALS and METHODS
The raw material was Calliandra wood with a diameter of 5–10 cm which grows in community forest areas. Calliandra leaves are used as food for Etawa goats of the Pangestu Farmer Group in Girikerto Village, Turi District of Sleman Regency, Yogyakarta Special Province. This study was conducted using a completely randomized design with two treatment factors and five replicate samples. Varian analysis was performed, followed by Tukey’s honestly significant difference follow-up test to determine the differences in the average values of the data.
Pelletization of the raw material by mixing Calliandra wood and its bark was conducted in the Forest Product Biomass Laboratory of Universitas Gadjah Mada. The raw material was sieved to 0.18–0.25 mm. Wood and bark powders were mixed at a ratio of 92.5:7.5%, then densified (pelletizing) with a compressive load of 100 kg/cm2 using a single-pelletizer with hydraulic power. The die hole was 8 mm in diameter and 55 mm in height with a die pusher of 100 mm.
Torrefaction was performed at temperatures of 250°C and 300°C for 30, 45, and 60 min. Pellets without torrefaction were used as controls. Torrefaction was conducted in a furnace with the following specifications: Thermolyne FB 1410M-33, single setpoint with a capacity of 2.1 L, power consumption of 1,520 W, temperature range of 100°C to 1,100°C, temperature stability of ± 5.0 at 1,000°C, and electrical requirements of 240 V 50/60 Hz.
The quality of torrefied Calliandra wood pellets was assessed by measuring compressive strength, moisture content, volatile matter content, ash content, carbon content, and calorific value according to the ASTM D4179-01, ASTM D1762-84, ASTM D1762-84, ASTM D1762-84, ASTM D3172-89, and ASTM D5865 2010 standards, respectively.
The compressive strength tests followed the ASTM D4179-01 standard (ASTM, 2001). The pellet samples were placed between two flat surfaces on a Unit Testing Machine and then subjected to a pressure load and force to test the compressive strength of the pellets.
The proximate analysis of the sample involved measuring its moisture content (MC), volatile matter content (VMC), and ash content (ASH) according to ASTM D1762-84, and fixed carbon content (FC) in accordance with the ASTM D1762-84 standard (ASTM, 2006).
Equations for proximate evaluation are presented below:
where:
w = air-dried mass (g).
x = mass after drying at 105°C (g).
where:
y = mass after heating in a furnace at 950°C (g).
where:
z = mass after heating in a furnace at 750°C for 6 h (g).
3. RESULTS and DISCUSSION
The average values of the parameter analysis of compressive strength and proximate characteristics of the torrefied Calliandra wood pellets are presented in Table 1, and the results of the appearance of the torrefied Calliandra wood pellets are presented in Fig. 1.
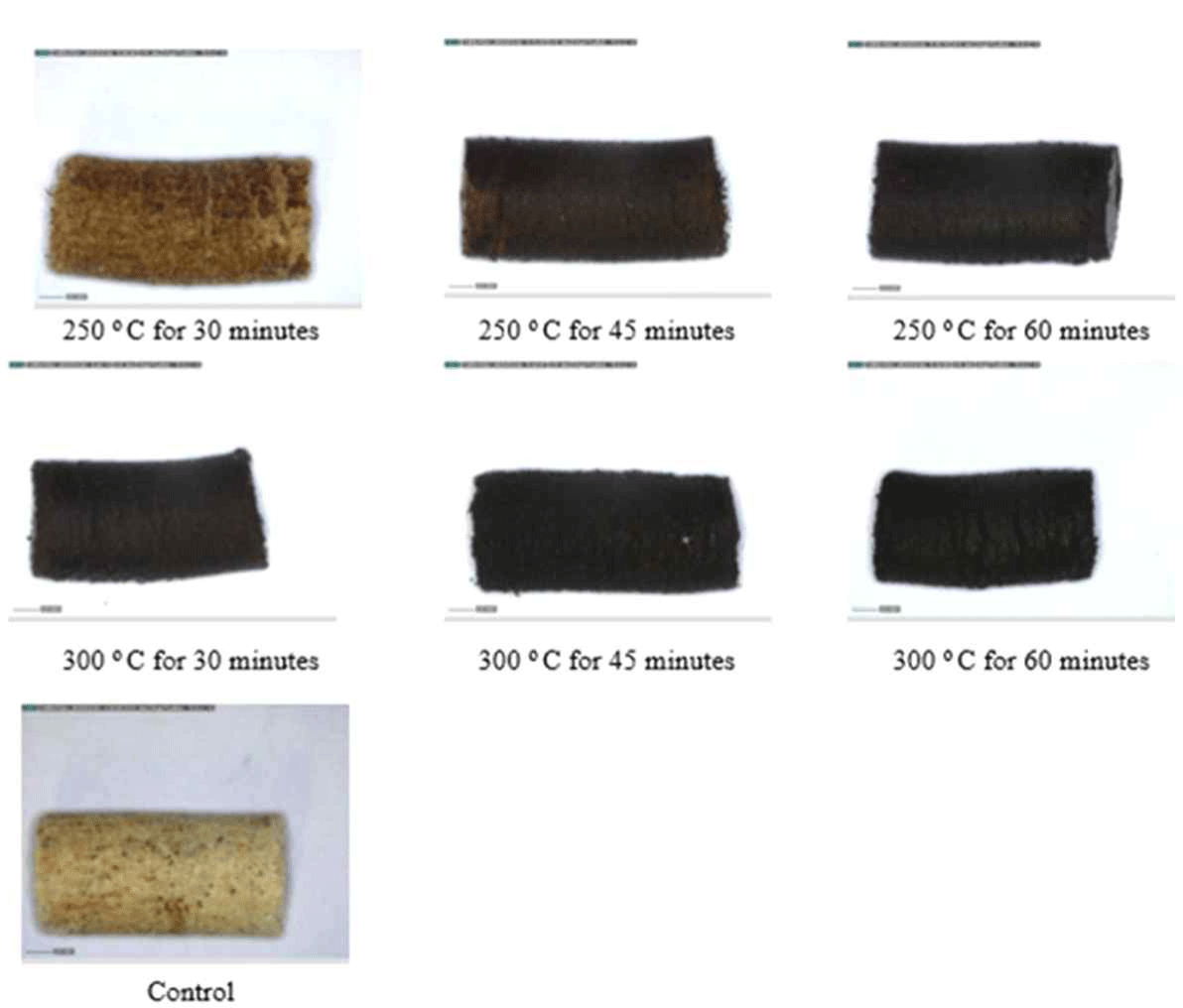
The strength of torrefied Calliandra wood pellets with an interaction of torrefaction temperature (T) and duration (W) ranged from 130.76 to 738.60 N. Based on analysis of variance (ANOVA), the compressive strength of torrefied Calliandra wood pellets from the interaction of torrefaction temperature and duration had significant differences at the 1% precision level. The results of the study showed an increase in torrefaction temperature and duration, followed by a decrease in the compressive strength of torrefied Calliandra wood pellets (Fig. 2). The produced torrefied Calliandra wood pellets were in accordance with Manouchehrinejad and Mani (2018) using a torrefaction temperature of 230°C–290°C for 30 min; the compressive strength of pellets decreased from 477.10 N to 103.27 N due to the formation of cavities between the particles in the pellets, thereby reducing the compressive strength and density of the pellets. Cross-linking and polycondensation of lignin in the pellet cavity results in decomposition due to temperature, such that the pellet cavity diversifies and the hardness of the pellet decreases (Boonstra et al., 2007). The decrease in compressive strength of torrefied Calliandra wood pellets was still acceptable with the lowest compressive strength at 130.76 N at a torrefaction temperature of 300°C for 60 min. However, this lower compressive strength is beneficial for crushing and grinding the pellets before burning, owing to the lower energy required for grinding or crushing if the pellets are used for co-firing with coal in conventional pulverization (Stelte et al., 2013).
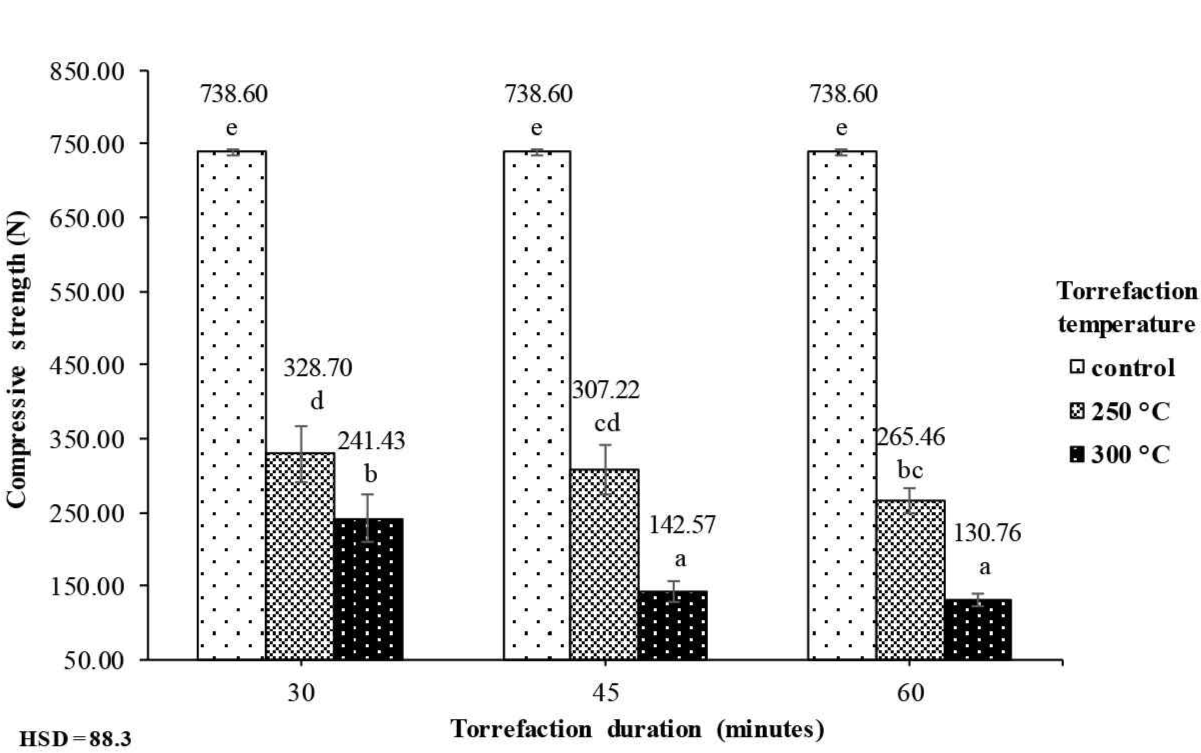
The moisture content of torrefied Calliandra wood pellets ranged from 3.39% to 10.84% (Table 1). Based on ANOVA, the interaction between torrefaction temperature and duration had significant differences at the 1% precision level. The lowest moisture content of 3.39% occurred at a torrefaction temperature of 300°C for 60 min. A greater temperature and longer torrefaction duration can significantly reduce the moisture content (Fig. 3). A decrease in moisture content of 59.32%, 66.51%, and 68.73% occurred at a torrefaction temperature of 300°C and a torrefaction duration of 30, 45, and 60 min, respectively. This corresponds to the drying stages of the biomass torrefaction process, namely the non-reactive (50°C–150°C), reactive drying (150°C–200°C), and destructive drying (200°C–300°C) stages. During the heating period from 50°C to 150°C, the moisture content evaporates, and no chemical changes occur resulting in decreased biomass and reduced moisture content (Shankar Tumuluru et al., 2011). The moisture content of torrefied Calliandra wood pellets at 250°C and 300°C for 30, 45, and 60 min ranged from 3.39% to 6.21%; the moisture content fulfilled the SNI (< 12%) and DIN 51731 (< 12%) standards.
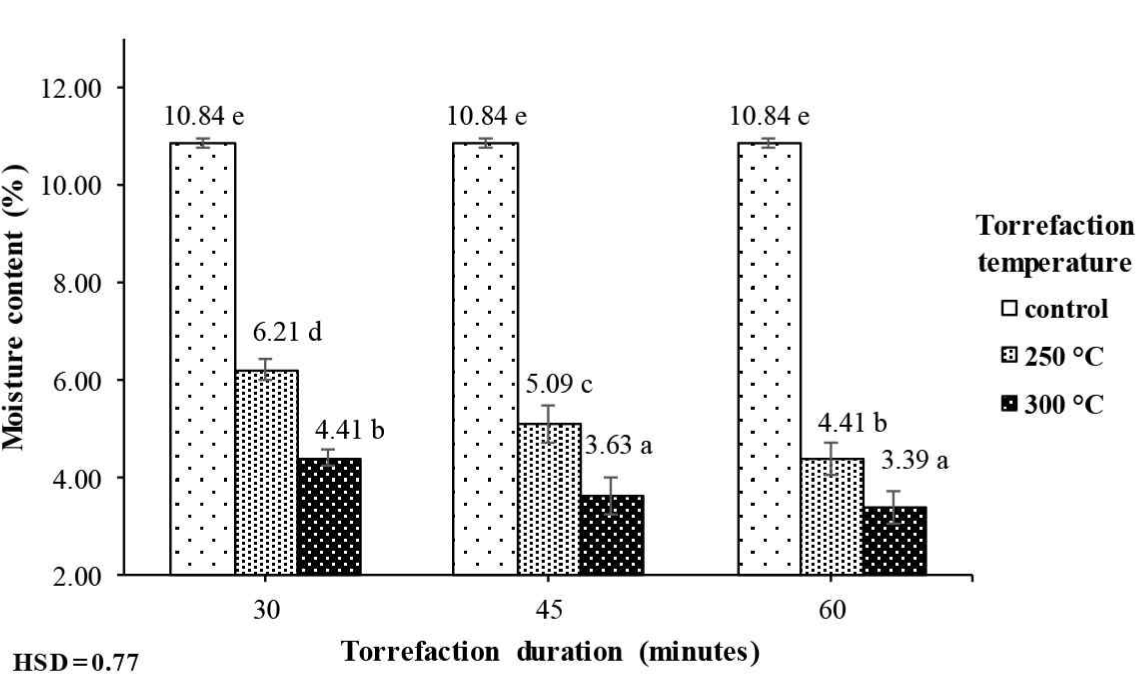
Volatile substances comprise components (excluding water vapor) that evaporate in the absence of air at high temperatures, whereas fixed carbon can be defined as the solid carbon remaining in the charcoal after the devolatilization process (Speight, 2015). Volatile substances are associated with the amount of smoke produced during combustion. The amount of volatile matter in the bio-pellet components affects or transforms the carbon content of the bio-pellets (Cahyani et al., 2023). Table 1 shows the volatile matter content of the torrefied Calliandra wood pellets ranging from 61.14% to 87.56%. Based on ANOVA, the interaction between torrefaction temperature and duration showed a significant difference at the 1% precision level. The results showed the lowest volatile matter content of 61.14% at a torrefaction temperature of 300°C and a torrefaction duration of 60 min (Fig. 4). Volatile matter content values decreased significantly by 27.95% and 28.77% at the torrefaction temperature of 300°C and a torrefaction duration of 45 and 60 min, respectively. A higher torrefaction temperature and longer torrefaction duration results in a lower volatile matter content (Bridgeman et al., 2008). This occurs because water vapor is evaporated and there is loss of volatile materials during torrefaction (Ju et al., 2020). The results showed the volatile matter of torrefied Calliandra wood pellets with at 250°C for 60 min was 78.68%, and that at 300°C for 45 and 60 min was 61.97% and 61.14%, which fulfilled the SNI standard (≤ 80%).
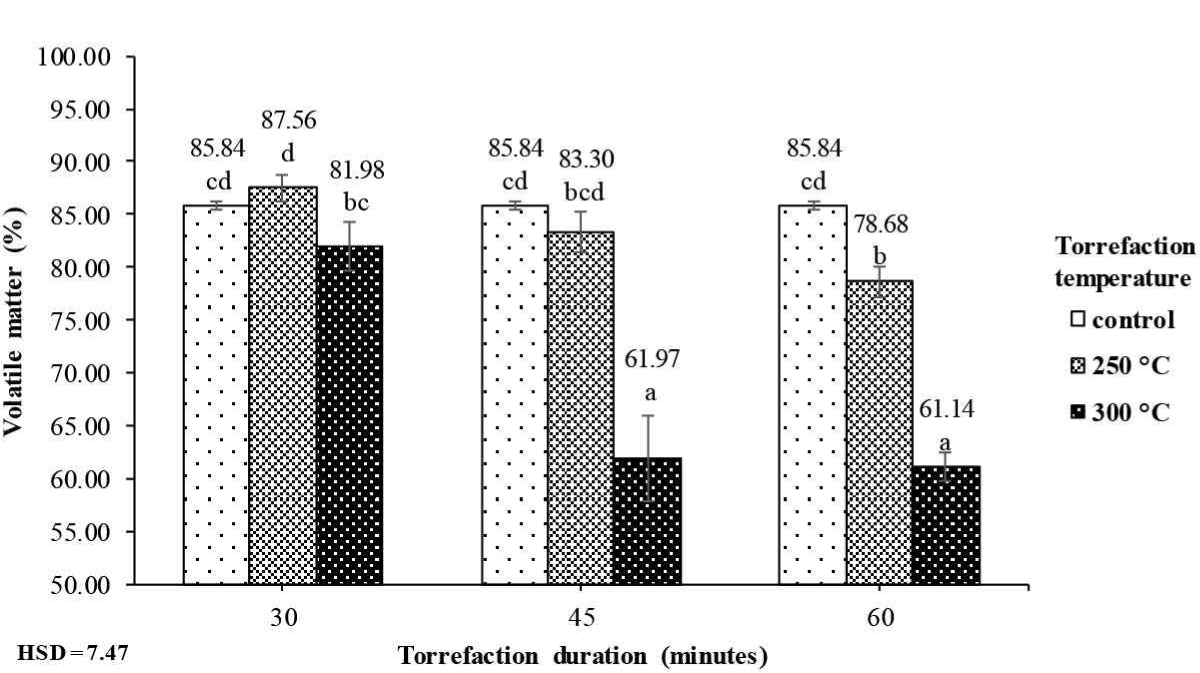
Ash content is the substance remaining after burning bio-pellets that has no carbon or calorific value, and its main components are calcium, potassium, magnesium, and silica (Cahyani et al., 2023). The ash content affects the heat energy produced; the lower the ash content, the greater the energy produced (Poddar et al., 2014). The ash content of torrefied Calliandra wood pellets ranged from 0.9% to 1.68% (Table 1). The ANOVA showed that there was a significant difference at the 5% precision level for torrefaction temperature and a significant difference at the 1% precision level for torrefaction duration. The effect of a torrefaction temperature of 300°C reduced the ash content by 35.12%. A torrefaction duration factor of 60 min reduced the ash content by 41.66% (Fig. 5). The ash content of torrefied Calliandra wood pellets at 250°C and 300°C for 30, 45, and 60 min with a value range of 0.90%–1.29% fulfilled SNI (< 1.5%) and DIN 51731 (< 1.5%) standards.
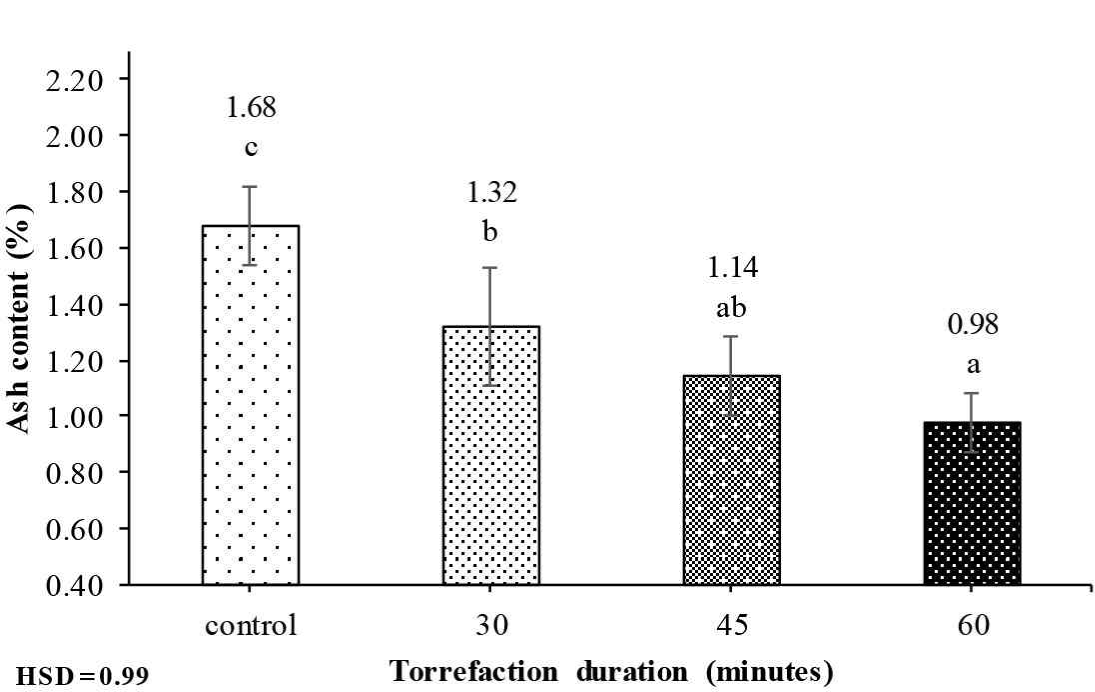
The fixed carbon content of torrefied Calliandra wood pellets ranged from 12.48% to 37.96% (Table 1). Based on ANOVA, the interaction between the torrefaction temperature and torrefaction duration had a significant difference at the 1% precision level. Fig. 6 shows the highest fixed carbon content in wood pellets at a torrefaction temperature of 300°C and a torrefaction duration of 60 min. Fixed carbon content increased significantly by 25.14%, 66.27%, and 67.11% at 300°C and a torrefaction duration of 30, 45, and 60 min, respectively. Because the volatile matter and moisture contents decreased with torrefaction, the fixed carbon content of the torrefaction results increased (Aytenew et al., 2018). In addition, in the torrefaction of Larix kaempferi wood chips, the carbon content increased with temperature and torrefaction time owing to the decrease in O/C and H/C ratios caused by the torrefaction process (Lee et al., 2015). The increase is similar to the results of Yue et al. (2017), who reported an increase in fixed carbon content from sweet sorghum bagasse after torrefaction at 250°C, 275°C, and 300°C. The fixed carbon contents from Calliandra wood pellets at 250°C for 45 and 60 min was 15.43% and 20.26%, respectively, and those at 300°C for 30, 45, and 60 min were 16.68%, 37.01%, and 37.96%, respectively, which fulfilled SNI standards (minimum 14%).
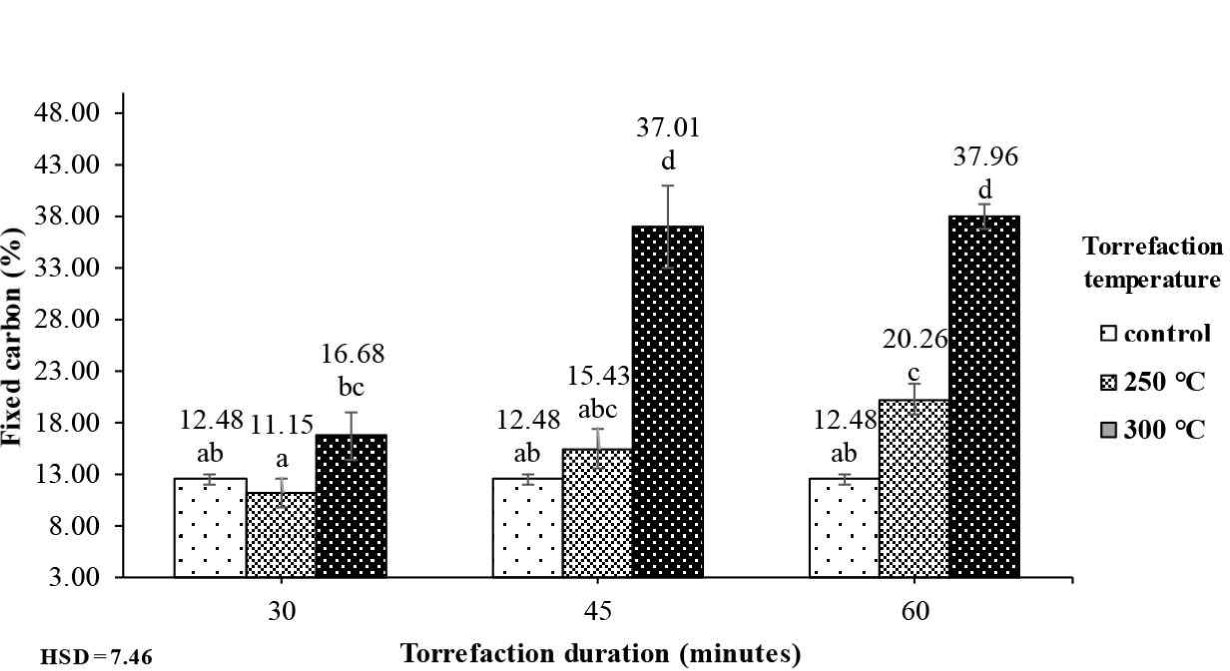
Increasing the temperature and torrefaction duration can increase the calorific value (Lee et al., 2015; Matali et al., 2016). The calorific value of the torrefied Calliandra wood pellets ranged from 4,581.40 to 6,303.80 cal/g. Based on ANOVA, the interaction between torrefaction temperature and duration was significantly different at the 1% precision level. Torrefaction treatment at 300°C increased the caloric value by 11.36%, 29.10%, and 37.60% at torrefaction durations of 30, 45, and 60 min, respectively. The results of this study are in accordance with the torrefaction research of Lau et al. (2018), who reported an increase in the calorific value of palm fronds. The calorific value of the palm fronds increased by 29.58% at a torrefaction temperature of 300°C for 30 min. This study shows that the calorific value of torrefied Calliandra wood pellets increases with increasing torrefaction temperature. The calorific values of torrefied Calliandra wood pellets at 250°C and 300°C ranged from 4,591.00 to 6,303.80 cal/g and fulfilled SNI (> 4,000 cal/g) and DIN 51731 (3,705–4,661 cal/g) standards. The highest calorific value of torrefied Calliandra wood pellets was obtained with a torrefaction duration of 60 min at 300°C (Fig. 7).
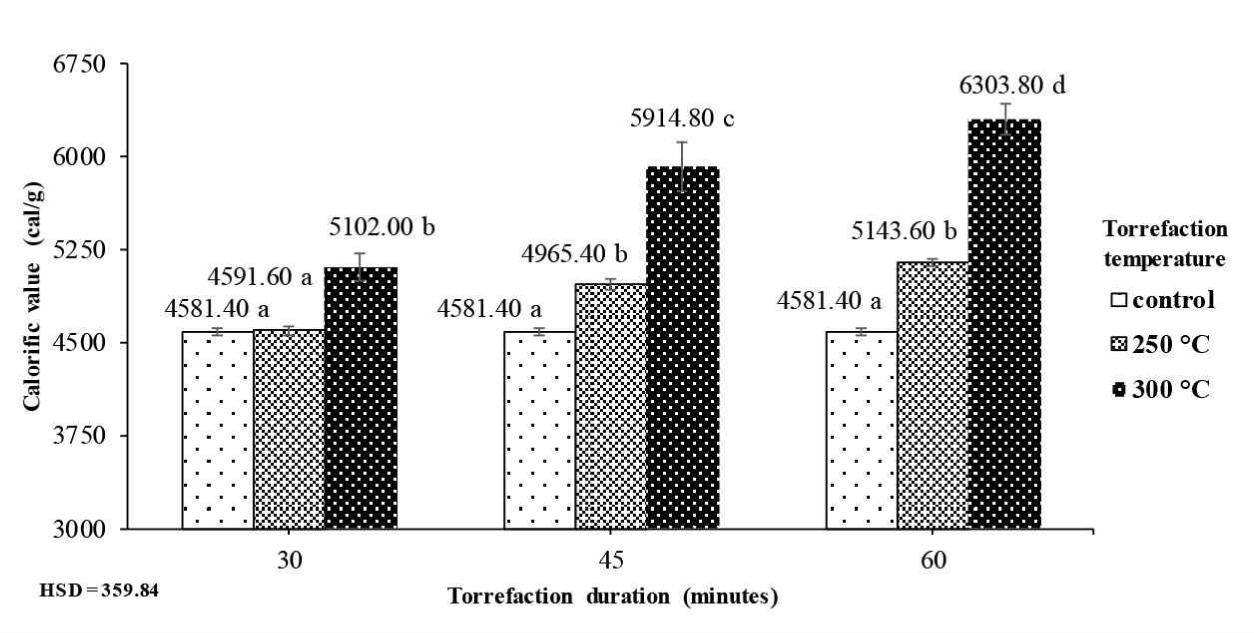
4. CONCLUSIONS
Based on these results, it can be concluded that the interaction between torrefaction temperature and duration significantly affects the calorific value, compressive strength, and proximate value of torrefied Calliandra wood pellets. As the torrefaction temperature increased with a longer torrefaction duration, the compressive strength, moisture content, volatile matter content, and ash content of the torrefied Calliandra wood pellets decreased. However, the calorific value of the torrefied Calliandra wood pellets increased with increasing torrefaction temperature and duration. The best torrefaction treatment of Calliandra wood pellets as a renewable energy source is obtained at a torrefaction temperature of 300°C and a torrefaction duration of 60 min which produce a low ash content of 0.90% and a high calorific value of 6,303.80 cal/g; these quality parameters already fulfilled SNI 8675:2018I and DIN 51731 standards.