1. INTRODUCTION
Fuel is required to produce energy, and its supply is a major problem today. Every year, the consumption increases along with the increasing population in worldwide (Budiawan et al., 2014). As a developing country, Indonesia has many resources that have great potential for development as renewable fuels for daily needs (Pratiwi, 2020). One energy source that is both abundant and renewable is biomass. Biomass is organic material obtained from the photosynthetic process, both in the form of products and waste (Putri and Andasuryani, 2017). Using biomass as fuel has the advantage of reducing carbon dioxide levels in the atmosphere because biomass produces carbon neutral from combustion, so it is more easily absorbed by plants (carbon neutral; Jang, 2022; Mustamu et al., 2018) and also several studies reported that wood-based fuels are the best for reducing air pollutant production during combustion and calculating average annual greenhouse gas emissions by tree species and products for charcoal (Jeoung et al., 2020). In addition, the use of biomass can minimize environmental impacts of energy production by replacing fossil fuels and thus reducing greenhouse gas emissions, carbon sequestration, climate change mitigation, waste management, energy production (Heo and Choi, 2018; Wu et al., 2021). Biomass can be obtained from various sources, including agricultural waste and wood waste, but it tends to have a high moisture content and poor flammability (Kansai et al., 2018; Lee et al., 2019), the biomass based on wood consists of cellulose, hemicellulose, and lignin (Hwang et al., 2021). Bio pellet technology offers a solution to improve the quality of biomass for burning (Mustamu et al., 2018; Pratiwi, 2020).
Bio pellets are created by processing biomass in combination with adhesives in a pressing system. The technology is simple, and it can relatively quickly produce bio pellets with a diameter of 6–12 mm and a length of 10–20 mm (Fikri and Sartika, 2018; Mustamu et al., 2018). The pelletization of biomass provides consistent quality, high energy content, and uniform size and shapes of solid energy (Lee and Kim, 2020).
One type of biomass that is abundant in Indonesia is spent coffee grounds (SCGs). Coffee consumption in Indonesia is increasing by an average of more than 7% every year, and with the higher coffee consumption, a greater amount of coffee waste is generated from cafes and households (Limantara et al., 2019). However, SCGs contain aromatic and aliphatic compounds and high levels of nitrogen and sulfur (Yang et al., 2018), which cause SCGs to produce a lot of smoke when they are burned (Khusna and Susanto, 2015). Therefore, modifications are necessary to increase the potential of SCGs as a fuel source by mixing it with other materials that are sustainable and have a high calorific value such as using wood, the wood itself is one of the renewable eco-environmental resources (Ahn et al., 2021; Ghani and Lee, 2021; Hadi et al., 2022; Han and Lee, 2021; Jang, 2022; Park et al., 2020a, 2020b). The Intergovernmental Panel on Climate Change (IPCC) recognizes wood as a representative carbon-neutral material and advocates using wood as an essential material for building a carbon-neutral society (Brunet-Navarro et al., 2018; Jang, 2022). Wood that contains a high calorific value according to Martinez et al. (2019) is pine wood, it contains resin which can affect to increase the calorific value. However, in this study the pine wood would burn into charcoal, according to Jeoung et al. (2020) the wood charcoal causes the higher of fixed carbon.
In addition to the materials used, particle size is another factor that affects the pressing and burning process. A larger particle size causes larger cavities in bio pellets because a larger particle makes the adhesive will be more difficult to stick. Owing to the larger cavities, more oxygen can enter into the pellets, allowing the oxidation reaction to occur more rapidly (Lisowski et al., 2019) and Ju et al. (2020) reported that a carbonized biomass below 100 mesh had the lowest ash content and the highest heating value, carbon content, and fixed carbon content. Reducing particle size is an important part of pre-processing associated with the use of biomass in energy production and other industries. The design and the technology used for size reduction process very important for the consideration in bio-energy making process (Lee and Eom, 2021). The technology for making powders or particles is continually advancing. One type of technology that is currently being promoted in various countries is the use of ball milling. Ball milling in the manufacture of bio-char is carried out to produce better characteristics and functionality of the product (Kumar et al., 2020). Recent studies have shown that ball milling can increase the surface area and volume of pores in biochar, as well as enable a reduction in the particle size (Lyu et al., 2017; Naghdi et al., 2017).
The aim of this study was to investigate the characteristics of bio pellets made from a mixture of SGCs and pine wood charcoal mixed at different ratios. The quality of the bio pellets was assessed according to Indonesian National Standard (SNI) 8021-2014 (Badan Standardisasi Nasional, 2014), which includes tests for moisture content, ash content, density, carbon content, calorific value, and volatile matter content (Mustamu et al., 2018; Peudada et al., 2020).
2. MATERIALS and METHODS
This study used matchsticks and a drum to burn the pieces of pine wood, and the main equipment included a hammer mill (HM) to grind pine wood charcoal to obtain micro-sized particles and a ball mill (BM) to grind micro-size pine wood charcoal to obtain nano-sized particles.
The HM grinder was a type of disk mill that basically grinds material using a rotating disc on a stationary surface (Nandiyanto et al., 2020). The BM grinder was a mixer milling type based on vibration ball-milling (vibration type). In vibration ball-milling, a cylinder containing a ball and the material to be milled is vibrated at high frequencies and small amplitudes (Kumar et al., 2020; Xing et al., 2016).
The tools used for analysis were a peroxide bomb calorimeter to determine the heating value of pellets, a furnace for determining ash content, volatile matter test equipment, an analytical balance, a desiccator, a measuring cup, a caliper, and an oven. The main materials were pine wood and SCGs. The pellet formula also included tapioca as an adhesive.
Samples of SCGs were dried in an oven for 24 hours at 105°C, while pieces of pine wood were burned to produce charcoal. The burning process was conducted by putting the pine wood into a drum and burning it on a fireplace for 30 minutes. The resultant pine wood charcoal was ground using an HM grinder, and the pine wood charcoal powder was then sieved and trapped at 125 μm. The charcoal ground by HM is shown in 9 1. A portion of the BM pine wood charcoal powder was sieved at 60 μm and then ground again by BM for 30 minutes. The BM pine wood charcoal powder is shown in Fig. 1.
Tapioca flour at a weight of 5% of the raw material per pellet unit was mixed with hot water to a concentration ratio of 1:20 between adhesive and water. The mixture was stirred until it produced a gel. HM or BM SCGs to pine wood charcoal were respectively mixed at a ratio of 6:4 or 4:6 to produce four types of pellets.
Samples of SCGs were dried in an oven for 24 hours at 105°C, while pieces of pine wood were burned to produce charcoal. The burning process was conducted by putting the pine wood into a drum and burning it on a fireplace for 30 minutes. The resultant pine wood charcoal was ground using an HM grinder, and the pine wood charcoal powder was then sieved and trapped at 125 μm. The charcoal ground by HM is shown in Fig. 2. A portion of the HM pine wood charcoal powder was sieved at 60 μm and then ground again by BM for 30 minutes. The BM pine wood charcoal powder is shown in Fig. 1.
Tapioca flour at a weight of 5% of the raw material per pellet unit was mixed with hot water to a concentration ratio of 1:20 between adhesive and water. The mixture was stirred until it produced a gel. HM or BM SCGs to pine wood charcoal were respectively mixed at a ratio of 6:4 or 4:6 to produce four types of pellets.
Homogeneous briquettes, each weighing 2 g, were placed in a manual pellet press (Fig. 3) for the molding process. Afterward, the pellets were dried in an oven at 120°C for 24 hours.
The bio pellet characteristics were tested based on SNI 8021-2014 to evaluate density, moisture content, ash content, volatile matter content, fixed carbon, and calorific value which follows to previous research by Mustamu et al. (2018). Additional characteristics were done based on physical analysis of the bio pellets to determine their compressive strength (Mustamu et al., 2018), flame duration (Tongcumpou et al., 2019), combustion rate (Afif Almu et al., 2014), and physical appearance (Rusdianto, 2018).
The density of the pellets was determined by measuring the weight of the briquette sample and dividing it by the sample volume. The briquette density is expressed by the formula:
where ρ = density (g/cm3); M = mass (g); and V = volume of cylinder (cm3).
Determination of the moisture content (MC) was carried out by placing 1 g of the sample in an oven at a temperature of 103 ± 2°C for 24 hours until the weight was constant. The sample was then cooled in a desiccator for 15 minutes and weighed according to SNI 8021- 2014, using the following formula:
where w = weight before drying in the oven (g), and d = weight after drying in the oven (g).
Ash content was determined by placing 1 g of the sample on a porcelain plate of known weight in a muffle furnace at 600°C–900°C for 5 to 6 hours. The sample was cooled in a desiccator and then weighed. The ash content of the sample was calculated according to SNI 8021-2014, using the following formula:
where y = weight of pellet (g) w = weight of ash (pellet after ash) (g), and d = weight of porcelain cup (g).
Volatile matter was measured by placing a porcelain cup containing ± 1 g of the sample into the muffle furnace, heating it at 900°C for 7 minutes, and then putting it in a desiccator to cool for 1 hour. After that, the porcelain dish was weighed, and the amount of volatile substances was calculated according to SNI 8021-2014, using the formula:
The fixed carbon fraction of the material does not include the moisture, volatile matter, and ash content. The fixed carbon content was calculated according to SNI 8021-2014 with the formula:
One gram of the sample was placed in a silica cup, which was put into a peroxide bomb calorimeter tube. The calorific value was calculated according to SNI 8021-2014 with the formula:
The flame duration test was carried out following to previous study by Tongcumpou et al. (2019), the bio pellets burned on an alcohol burner and a tripod, and the length of ignition time was calculated using a stopwatch.
For calculating the combustion rate, the weight mass of the pellets before burnt divided to the weight mass of pellet after burnt. The combustion rate was calculated using the formula according to Afif Almu et al. (2014) and Oyelaran et al. (2018):
where w = the weight of pellets before burnt (g), d = the weight of pellets after burnt (g), and t = total time taken (minute).
The compressive strength test was carried out on the Universal Testing Machine (UTM) and was calculated using the formula (Mustamu et al., 2018):
where P = compressive strength of pellets (kgf/cm2); Mb = load received by pellet until it breaks (kgf); and A = pellet surface area (cm2).
The physical appearance of the bio pellet was carried out based on research from Rusdianto (2018), by looking at the color, diameter, and smell of each variation.
The treatment used in this study was the difference in the ratios of the pine wood charcoal powder to SCGs, 4:6 and 6:4. Another treatment was the different methods used to grind the pine wood charcoal, HM and BM. Each treatment was carried out three times. Data in this study were analyzed by using independent sample t-tests. Bio pellets were compared in terms of the different ratios of components, as well as the different grinding methods used for pine wood charcoal.
3. RESULTS and DISCUSSION
The bio pellets made with SCGs and pine wood charcoal were tested for the parameters included in SNI 8021-2014: density, moisture content, ash content, volatile matter content, fixed carbon, and calorific value. Physical analysis of bio pellets consisted of evaluating their compressive strength, burning time, burning rate, and physical appearance.
Bio pellets can absorb water or moisture the moisture content was calculated to determine the nature of the absorption of moisture, which can affect the other chemical test values of the bio pellet. Measurement of moisture content was carried out after the bio pellets were compressed and dried in oven for 24 hours (Muzakir et al., 2017; Putri and Andasuryani, 2017). The results of the moisture content test can be seen in Fig. 4.
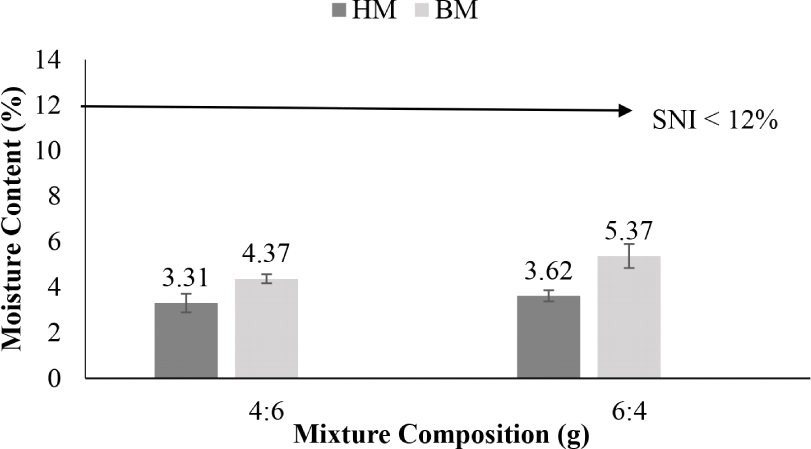
Based on the test result, the moisture content differed significantly between variations in HM and BM (two- tailed ρ-value ≤ 0.005). Fig. 4 shows that the BM bio pellet has a higher moisture content than the HM variation bio pellet, likely because the charcoal particles produced by BM have a smaller size. According to Priyanto et al. (2018) and Ruslan (2020), the moisture content value of a pellet is influenced by its density and pores density; the finer the particle size, the higher the moisture content value. Thus, the finer the particle size, the more moisture will be absorbed.
The test results show that the moisture content percentages of the 6:4 pine wood charcoal–SCGs combinations were significantly different from those of the 4:6 combinations (two-tailed ρ-value < 0.005). Fig. 4 shows that the 6:4 combinations had a higher moisture content value than the 4:6 combinations. This finding is in line with the research of Jeguirim et al. (2014), who reported that the moisture content in pure SCGs bio pellets was 11.78%, while the moisture content value in pine wood pellets was only 7.90% and that of pellets made from a mixture of SCGs and pine was 6.65%. The high moisture content in SCGs occurs because the moisture content in coffee grounds before brewing is around 42% (Colantoni et al., 2021). In the research of Atabani et al. (2018), the moisture content in SCGs after drying at a temperature of 105°C was found to be 55%. The high moisture content value greatly affects the chemical and mechanical test values of bio pellets (Cubero-Abarca et al., 2014; Rusdianto, 2018). The high moisture content can also reduce the quality of bio pellets, for example, through the growth of microorganisms, and cause pellets to be difficult to ignite and to produce a lot of smoke (Putri and Andasuryani, 2017; Tun et al., 2020).
According to SNI, good-quality bio pellets have a moisture content value ≤ 12%. Therefore, all variations of bio pellets in this study had a moisture content value in accordance with SNI 8021-2014.
Density reflected the ratio between mass and volume of briquettes. The high- and low-density values were influenced by pressure at the time of pressing, particle size, and the homogeneity of the bio pellet constituent materials (Damayanti et al., 2017; Priyanto et al., 2018). The results of the density test are presented in Fig. 5.
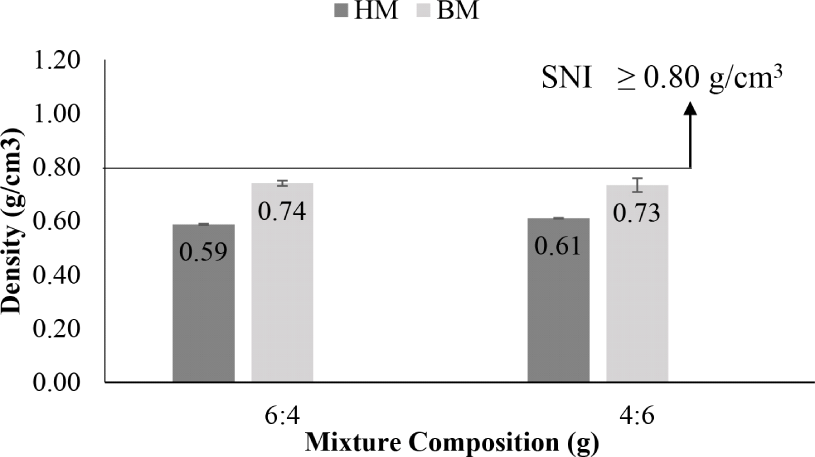
The density was significantly different between the bio pellets made with HM and BM (two-tailed ρ-value < 0.005). Fig. 5 shows that the density of BM pellets was higher than that of HM pellets, indicating that the BM particles were smaller than the HM particles. The density of the material is influenced by its specific gravity, which is determined in part by the particle size of the material. Coarser or larger particles in the bio pellet lead to a lower specific gravity, and thus a lower density (Damayanti et al., 2017). This pattern accords with a previous study by Priyanto et al. (2018), who reported that the smaller the particle size, the higher the density value. This association is explained by small particle sizes resulting in stronger bonds between charcoal particles.
With regard to the variation in the ratios of pine wood charcoal and SCGs, the test results were non- significant (two-tailed ρ-value ≥ 0.005). This outcome indicates that the material used to create the bio pellets had no effect on their density. The density was only affected by the pressure during the compression process and the particle size of the materials used (Prabawa and Miyono, 2017). Based on SNI 8021-2014, a good bio pellet density is ≥ 0.80 g/cm3), and none of the variations of bio pellets in this study met this standard.
Ash is what remains following the combustion of bio pellets. It does not have carbon elements or calorific value, and its main components are calcium, potassium, magnesium, and silica. The silica content in biomass has an unfavorable effect on the calorific value and carbon content value; that is, the smaller the ash content value, the higher the calorific value and carbon content value of the biomass (Iskandar et al., 2019; Muzakir et al., 2017; Putri and Andasuryani, 2017). The ash content of the bio pellets can be seen in Fig. 6.
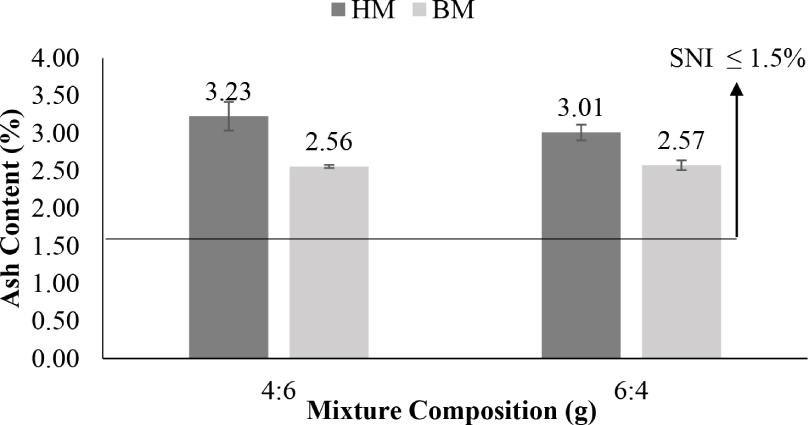
The results (ρ-value ≤ 0.005) indicated that the ash content was significantly different between HM and BM charcoal, and the variation introduced based on different combinations of SCGs and pine wood charcoal did not have a significant effect to the ash content. According to Colantoni et al. (2021) the ash content reflected to the calorific value, a higher percentage of ashes implies a greater quantity of unburnt products and consequently a lower calorific value (Fig. 7). The high value of ash content of this study caused by the mixture of SCGs, Limousy et al. (2013) found that the ash content of SCGs was high because contain several element includeing potassium (3.5 mg/g), phosphorus (1.5 mg/g), magnesium (1.3 mg/g), and calcium (0.8 mg/g; Jeguirim et al., 2014; Mussatto et al., 2011).
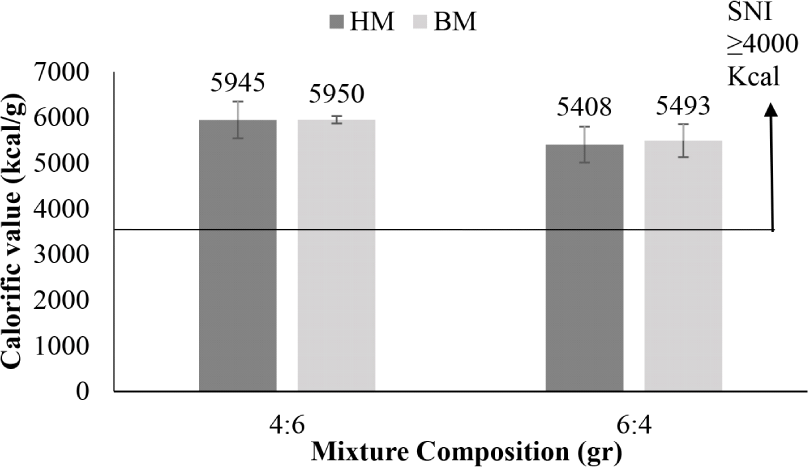
Based on SNI 8021-2014, the ash content of the bio pellets in this study exceeds the standard (≤ 1.5%). Therefore, the bio pellets of each variation in this study do not meet the quality standard for ash content according to SNI.
Volatile matter is associated with the amount of smoke that is produced during combustion. The level of volatile substances in the components of bio pellets affects the carbon content of the bio pellets. The greater the volatile matter, the lower the value of the carbon content, which causes the intensity of the fire of the bio pellet to decrease and also affects the calorific value (Iskandar et al., 2019). The value of volatile matter is influenced by the organic compounds in the materials used, including carbon, hydrogen, and oxygen (Ajimotokan et al., 2019; Kawale and Kishore, 2020). The value of the volatile matter in bio pellets can be seen in Fig. 8.
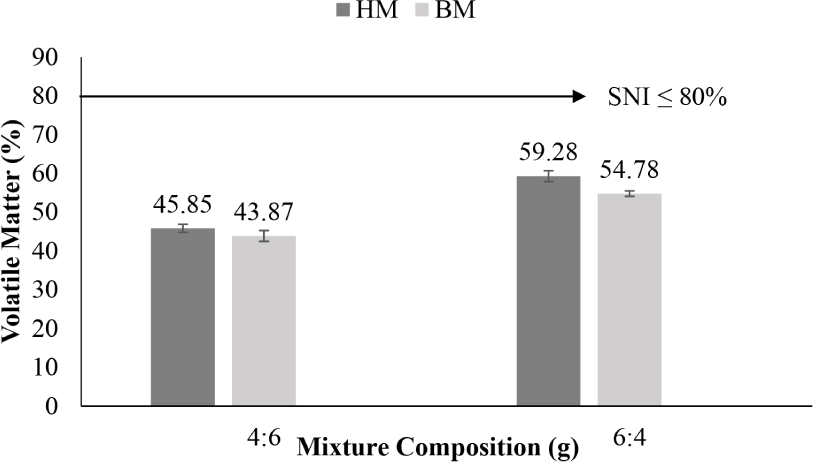
Based on the test results comparing HM and BM, the volatile matter values were not significantly different between the two types (two-tailed ρ-value ≥ 0.005). Meanwhile, the ρ-value for the comparison of the different ratios of pine wood charcoal to SCGs showed significant differences between 4:6 and 6:4 (two-tailed ρ- value ≤ 0.005). As illustrated in Fig. 8, the more of SCGs mixture, the higher the value of the volatile matter. According to Ajimotokan et al. (2019) the volatile matter of charcoal particles was lower when compared to the other raw materials. This could be due to its production process (carbonization), wherein a degree of devolatilization could have occurred. Even so, the volatile matter content of the bio pellets in this study met the standard of SNI 8021-2014, which was ≤ 80%.
The carbon content, or fixed carbon, is the carbon fraction (C) contained in materials; it is what remains after the water, ash, and volatile substances are removed. The carbon content in bio pellets is strongly influenced by the ash content and volatile matter content (Iskandar et al., 2019; Putri and Andasuryani, 2017). Based on the test results of fixed carbon value of the bio pellets presented in Fig. 9.
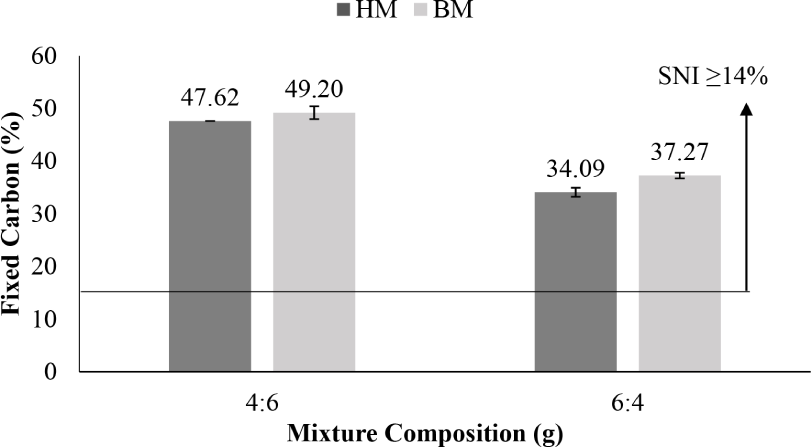
According to Sunardi et al. (2019), the increase of fixed carbon is influenced by the amount of volatile matter and the ash content. The higher the volatile matter and the ash content, the lower the fixed carbon. The test results for fixed carbon values based on HM and BM showed no significant difference (two-tailed ρ-value ≥ 0.005). In contrast, 4:6 and 6:4 mixed combinations were significantly different (two-tailed ρ-value ≤ 0.005).
Fig. 9 shows that the fixed carbon value increases with the amount of the pine wood charcoal in the mixture, which could have been because pine wood had a higher lignin content than SCGs. According to Jeguirim et al. (2014), a high lignin content in the raw material for making bio pellets is associated with a high value of fixed carbon. A high level of fixed carbon indicates that a fuel tends to burn more slowly than a fuel with a lower level of fixed carbon (Martinez et al., 2019). The fixed carbon in this study was in accordance with SNI, its ≥ 14%).
The calorific value is determined by the combustion of the activated carbon or fixed carbon (Patandung, 2014). The calorific value is the main parameter in determining the quality of bio pellets (Iskandar et al., 2019). The higher the calorific value, the better the quality of the pellets (Budiawan et al., 2014). The calorific value of the bio pellets created in this study can be seen in Fig. 7.
The calorific values associated with the different treatments did not differ significantly (two-tailed ρ-value < 0.005). However, all bio pellets regardless of variation met SNI 8021-2014, which was ≥ 4,000 kcal/g. The low calorific value of each variation (Fig. 7) was not in accordance with the findings reported by Kale et al. (2019), indicating that a lower moisture content (Fig. 4) is associated with a higher calorific value because bio pellets with a higher moisture content have a lower calorific value owing to non-combustibility.
The quality of bio pellets was also observed physically. In addition to detecting possible damage to the bio pellets, the physical analysis also included evaluation of the flame duration and combustion rate of the bio pellets. The results are presented in Table 1.
Testing | HM | BM | ||
---|---|---|---|---|
4:6 | 6:4 | 4:6 | 6:4 | |
Flame duration (minute) | 24.30 | 23.01 | 29.10 | 26.06 |
Combustion rate (g/minute) | 0.0407 | 0.0375 | 0.0379 | 0.0427 |
Compressive strength (kgf/cm2) | 1.3309 | 0.9760 | 2.9005 | 2.3960 |
Flame duration is one of the parameters or factors to be considered in the manufacture of solid fuels. The longer the burning time to ashes (burnt-out), the better the quality and vice versa (Ashar et al., 2020). The test results of this study showed that the bio pellets did not have significant differences (two-tailed ρ-value < 0.005) based on treatment with respect to the burning time of bio pellets.
Table 1 shows that the flame duration associated with the pine wood charcoal ground with the BM grinder was longer than that produced with the HM grinder. This finding indicates that the smaller the particle size, the longer the duration required for a bio pellet to burn out. Smaller particle sizes are associated with denser material of the pellets, which extends the burning time of the bio pellet (Ashar et al., 2020). A larger particle size causes larger cavities within pellets because the adhesive does not stick as well as with smaller particles. Oxygen can easily enter the cavities, which causes the oxidation reaction to occur faster.
In addition, a comparison between pellets with different ratios of pine wood charcoal powder to SCGs showed that pellets with a ratio of 6:4 had a longer flame duration than those with a ratio of 4:6. According to Jamilatun (2008), flame duration is influenced by the calorific value (Fig. 7); specifically, the higher the calorific value, the longer the bio pellet can burn. This can be explained by the fact that pine wood contains natural resin (Martinez et al., 2019).
The combustion rate was assessed to determine the feasibility of the bio pellets as an effective fuel (Afif Almu et al., 2014). A smaller burning rate indicates a longer burning time due to the lower mass of bio pellet that burns for each increment of time.
As shown in Table 1, all bio pellets in this study had almost the same combustion rate regardless of treatment. The combustion rate was influenced by the amount of the volatile matter (Fig. 8), with higher combustion rates being associated with higher amounts of volatile matter (Jamilatun, 2008). Pine wood naturally contains a volatile compound called turpentine (spirits of turpentine), which caused high volatilization in the bio pellets in this study.
Compressive strength is the ability of a material to have durability, defined as the strength to withstand external pressure that could cause the material to break or crumble (Mustamu et al., 2018). Compressive strength tests are carried out to determine the resistance of bio pellets to possible damage caused by storage, transportation, or handling (Brunerová et al., 2018). The results of the compressive strength testing in this study are presented in Table 1.
The test results showed that all variations of the bio pellets in this study were essentially the same in terms of compressive strength, with no significant differences based on treatment (two-tailed ρ-value < 0.005). However, Table 1 shows that the compressive strength value in the BM variation was greater than the HM variation, which can be explained by the BM particle size being smaller than the HM particle size. Previous studies by Hendra (2012) and Mustamu et al. (2018) revealed that compressive strength is inversely related to particle size, and a particle composition that tends to be smoother and more uniform strengthens bonding between particles. In addition, Priyanto et al. (2018) reported that a higher compressive strength is associated with a higher combustion rate.
According to Lisowski et al. (2019), as lower moisture content is linked to higher compressive strength. The moisture content values in this study are presented in Fig. 4. The high moisture content affects the low compressive strength of the 6:4 mixture composition. This is because SCGs can absorb moisture easily, according to Cubero-Abarca et al. (2014) and Fasina (2008) that SCGs moisture content ranging from 3% to 5%.
Fig. 10 shows the physical appearance of the bio pellets. They have a cylindrical shape with a diameter of 1.2 cm and a length ranging from 1.2 to 1.4 cm. The aroma of coffee is more pronounced in the 6:4 SCGs to pine wood charcoal mixture in each variation of the bio pellet.
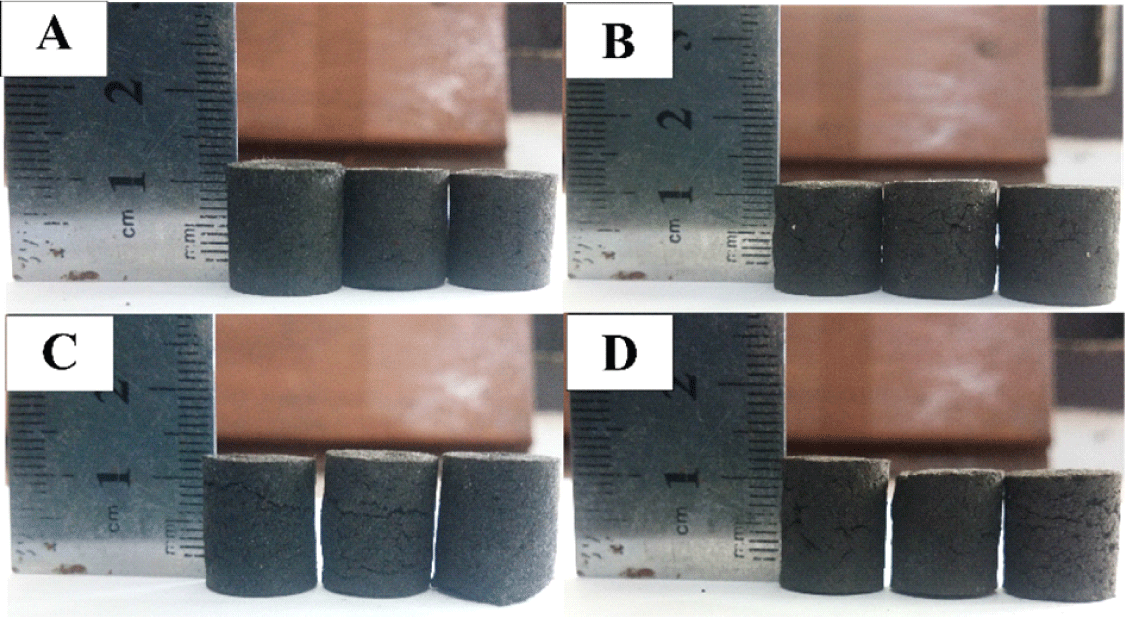
Physically, the pellets with the 6:4 had a slightly brownish color. In each variation of pellets with HM pine wood charcoal, the pores in the pellet were more clearly visible than in those with BM; however, in the pellets with HM, the bio pellets were more difficult to compact in 6:4 mixture, which made uneven surfaces. According to Priyanto et al. (2018), a larger particle size makes bonding more difficult because of the presence of empty voids. As for variations in BM, the briquette dough is easier to compact, but there are more cracks on the surface of the bio pellet [(Fig. 10(A) and (B)]. This could be due to the less of adhesive composition used in this study. If more adhesive compositions are used, then the composition of the particles will likely be better, more regular, and denser.
4. CONCLUSIONS
From the results of the study, the following conclusions were obtained:
1. The characteristics moisture content, volatile matter, fixed carbon, and calorific value of bio pellets composed of 4:6 and 6:4 pine wood charcoal to SCGs were in accordance with the standards. However, the ash content and density of bio pellets in this study were not in accordance with SNI.
2. Composition of 4:6 SCGs to pine wood charcoal provided a longer flame duration, higher compressive strength, and a more compact physical appearance with smoother surfaces compared with the composition of 6:4. However, the combustion rates of both compositions were almost the same.
3. The bio pellets that were produced with pine wood charcoal that underwent BM compared with HM had higher density and moisture content, and lower ash content and volatile matter due to the different particle sizes.