1. INTRODUCTION
Plant fibers have the potential to be implemented extensively in materials engineering applications because of increasing public awareness of environmental sustainability (Jamaludin et al., 2020; Sumardi et al., 2022). There are various natural plant fibers, such as kapok (Purnawati et al., 2018), flax, sisal, banana, coconut, bamboo, and kenaf. Recently, kenaf fibers have become one of the most sought-after materials (Azwa and Yousif, 2013) and has been extensively investigated and developed (Lee et al., 2008). Kenaf is the general name given to fibers from the bark of plants of the genus Hibiscus, family Malvaceae, particularly Hibiscus cannabinus L. Typically, this plant is grown in tropical and subtropical areas (Azwa and Yousif, 2013), including Indonesia. From an environmental perspective, these plants can absorb nitrogen and phosphorus from the soil and carbon dioxide from the air at high levels (Hamidon et al., 2019). Kenaf plants produce fibers with appealing mechanical and chemical properties compared with other natural fibers (Hamidon et al., 2019; Khan and Khan, 2015; Tajvidi et al., 2006) and can produce composites with good mechanical properties (Tajvidi et al., 2006).
There are some studies on the development of kenaf fiber composites using several types of adhesives, such as polypropylene (Rashdi et al., 2009, 2010; Tajvidi et al., 2006), epoxy (Davoodi et al., 2010; Ghori and Sreenivas Rao, 2021; Saba et al., 2016; Setyayunita et al., 2022), polyester (Aziz and Ansell, 2004; Aziz et al., 2005; d’Almeida, 2006; Osman et al., 2011; Yousif et al., 2007), polyurethane (El-Shekeil et al., 2012a, 2012b), polyethylene (Paul et al., 1997), phenol formaldehyde (Hwang and Oh, 2020), isocyanate (Iswanto et al., 2020), urea-formaldehyde (Wibowo et al., 2021), melamine-urea formaldehyde (Jeong et al., 2020), and elastomers (Anuar and Zuraida, 2011). Epoxy exhibits a low molecular weight, and its monomers exhibit low shrinkage during curing (Davoodi et al., 2010; Ghori and Sreenivas Rao, 2021; Saba et al., 2016). Previous studies have shown that kenaf fiber composite boards using epoxy possess good mechanical properties and dimensional stability (Setyayunita et al., 2022).
The strength of the natural fiber is an important factor affecting the properties of the composite board (Yahaya et al., 2015). Fiber treatment is recommended to increase the properties of the fiber (Mardin et al., 2016; Nosbi et al., 2011) and its composite board (Ishak et al., 2009; Mardin et al., 2016; Setyayunita et al., 2022). Several studies have reported different treatment methods. Chemical treatment is employed to prepare fibers for composite board applications to produce single fibers of higher quality (Anuar and Zuraida, 2011; d’Almeida, 2006; El-Shekeil et al., 2012b; Iswanto et al., 2020; Saba et al., 2016; Tajvidi et al., 2006). Chemical treatments, such as bleaching, acetylation (Tajvidi et al., 2006; Yahaya et al., 2015), and alkali (Maulana et al., 2021) increase the surface roughness. However, chemicals that have been widely used have a pH that is far from neutral, causing metal oxide dissolution reactions in manufacturing equipment (Horváth et al., 1994). Therefore, the use of materials for fiber treatment with a nearly neutral pH is employed to solve this problem. One of the approaches that has been investigated is the use of seawater for fiber treatment, which has a nearly neutral pH (8.08–8.33; Marion et al., 2011).
Seawater has been shown to increase the tensile strength of fibers and interlock them with adhesives (Mardin et al., 2016). Seawater contains 89.86%–92.24% NaCl (Sumada et al., 2017), which is higher than the other components (sulfur and carbonate). Mardin et al. (2016) suggested that NaCl in seawater affects the characteristics of natural fibers. Furthermore, the soaking time in seawater also affects the properties of the fiber (Mardin et al., 2016). Setyayunita et al. (2022) reported that composite boards made from NaCl-treated kenaf fibers exhibit better properties than those made from untreated fibers. The results indicated that the characteristics of the natural fiber significantly affected the properties of the composite board. However, to the best of our knowledge there are no studies on the effects of NaCl treatment on the characteristics of natural fibers.
The evaluation of fiber characteristics using fiber bundles is faster, easier, and more practical in application (Munawar et al., 2007). Therefore, this study focuses on the effect of different conditions of NaCl treatments on the characteristics of kenaf fiber bundles, such as tensile properties, fiber bundle diameter, weight change, and contact angle between the fiber bundle and adhesive. Additionally, the surfaces of the untreated and treated fiber bundles are observed by using scanning electron microscopy.
2. MATERIALS and METHODS
Kenaf bast fiber bundles from Bogor, West Java, Indonesia, were harvested after 150 days of seeding, and used as raw materials. Subsequently, NaCl (99%, Sigma- Aldrich, St. Louis, MO, USA) was used for the chemical treatment of the kenaf fiber bundles, whereas epoxy and hardener produced by Alfatama Inticipta (Jawa Tengah, Indonesia) were used as adhesives for contact angle testing.
Kenaf fiber bundles were initially collected and immersed in 1, 3, and 5 wt.% NaCl for 1, 2, and 3 h at room temperature. They were immersed in the NaCl solution and then washed with water at a solution to fiber bundle ratio of 20:1 (w/w). After soaking, the fiber bundles were rinsed with water until the pH reached 7, before drying in an oven at 80°C for 6 h.
Fiber bundle tensile tests were performed using a universal testing machine (Instron 3360 Series Dual Column Table Frames, Instron, Norwood, MA, USA) with a crosshead speed of 5 mm/min. The samples were glued between two rectangular pieces of cardboard. The cardboard contained a rectangular hole with dimensions of 15 × 90 mm2 at the center. A minimum of 50 samples were tested for each kenaf fiber bundle, and the failure force and cross-head displacement were reported by the testing machine. Untreated fiber bundles were also tested.
Fiber bundle diameters were collected from 50 random fiber bundles, and images were selected using a Dino- Lite Digital Microscope (AM413ZT, Dino Lite, New Taipei City, Taiwan) for each fiber bundle. Furthermore, the measurements were performed using ImageJ at 36 different angles (Munawar et al., 2007). The average of five diameters was calculated for each measurement. The diameters of the untreated fiber bundles were also measured. The weight changes in the fiber bundles treated with NaCl were determined by measuring the difference in weight before and after treatment. A minimum of three samples were tested under each condition.
The untreated and treated fiber bundles (5 wt.% NaCl, 3 h) were observed using field-emission scanning electron microscopy (FE-SEM; JEOL JSM 650 LA, JEOL, Tokyo, Japan). Prior to observation, the samples were covered with a thin layer of platinum. Observations were performed in electron mode at a beam current of 10 mA and an accelerating voltage of 1.5 kV. The morphologies of the untreated kenaf fiber bundles and those treated with 5 wt.% NaCl for 3 h were observed.
Fiber bundle samples were conditioned at room humidity and temperature for one week. The epoxy solution was dropped onto the surface with a micropipette, and a photograph was taken after 10 s using a Dino-Lite Digital Microscope (AM413ZT, Dino Lite). The contact angle was calculated using the height and chord of the droplet, and five measurements were made for each sample. The contact angles of the untreated and treated fiber bundles were measured.
3. RESULTS and DISCUSSION
The fiber bundle treatment using NaCl at different concentrations and soaking durations affected the mechanical properties of the fiber bundles. The tensile strength and Young’s modulus of the treated fiber bundles are shown in Fig. 1. Kenaf fiber bundles treated with 5 wt.% NaCl for 3 h yielded the highest average tensile strength and Young’s modulus of 481.78 MPa and 50.61 GPa, respectively. The lowest tensile strength and Young’s modulus were obtained for the fiber bundles treated with 1 wt.% NaCl for 1 h, 421.83 MPa and 41.47 GPa, respectively. The tensile strength and Young’s modulus of the untreated kenaf fiber bundles were 415.08 MPa and 40.72 GPa, respectively. The tensile strength and Young’s modulus increased with increasing NaCl concentration and soaking duration. The increase in tensile strength and Young’s modulus was likely owing to the infiltration of sodium into the fiber, which may cause a decrease in lignin and increase in cellulose contents, which strengthens the treated fiber, as reported by Mardin et al. (2016). The strain of the untreated kenaf fiber bundles was 1.1%. The fiber bundles treated with NaCl exhibited strains 0.75%–2.55% higher than that of the untreated kenaf fiber bundles. Typically, the strain of the treated kenaf fiber bundles decreased with increasing NaCl content and soaking duration. The decrease in strain is attributed to the viscoelastic shearing of the fiber, indicating that recovery is linked to an induced crystallization of amorphous cellulose components and to a microfibril alignment with the loading axis (Perremans et al., 2018). As reported by Sarjadi et al. (2018), NaCl, which is the most abundant salt found in seawater, can affect the strain of fibers under different treatment conditions.
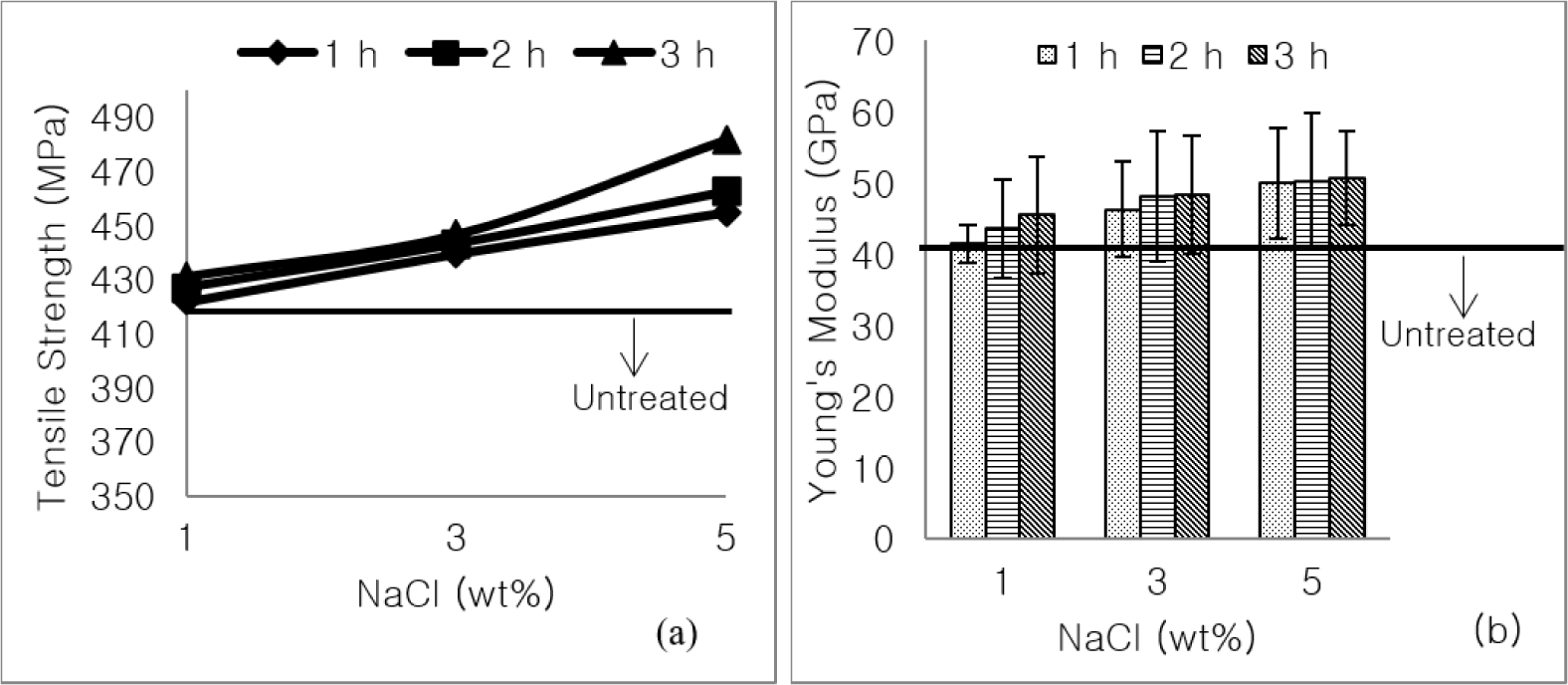
NaCl treatment of kenaf fiber bundles increased its tensile strength and Young’s modulus. The stress–strain curves of the untreated kenaf fiber bundles and those treated with 5 wt.% NaCl for 3 h are shown in Fig. 2. Treatment with 5 wt.% NaCl for 3 h increased the tensile strength and Young’s modulus by 16.06% and 24.29% compared to the untreated fiber bundles, respectively. Mahjoub et al. (2014) reported the tensile strength of kenaf fiber bundles after alkaline treatment. Kenaf fiber bundles treated with 5% and 7% for 3 and 24 h decreased the tensile strength. When the soaking duration was 3 and 24 h in 7% NaOH, the tensile strength decreased by 9% and 33%, respectively, in comparison with the untreated kenaf fiber bundles. Increasing the concentration of NaOH from 5% to 7% for 3 and 24 h decreased the tensile strength by up to 15% and 20%, respectively. Guo et al. (2019) investigated the effect of treatment on the tensile strengths of kenaf fiber bundles. The results indicated that treatment with alkaline, alkaline-potassium permanganate, alkaline-potassium dichromate, and alkaline-hydrogen peroxide increased the tensile strengths by 2.46%, 0.47%, 2.13%, and 18.91%, respectively, compared to untreated kenaf fiber bundles.
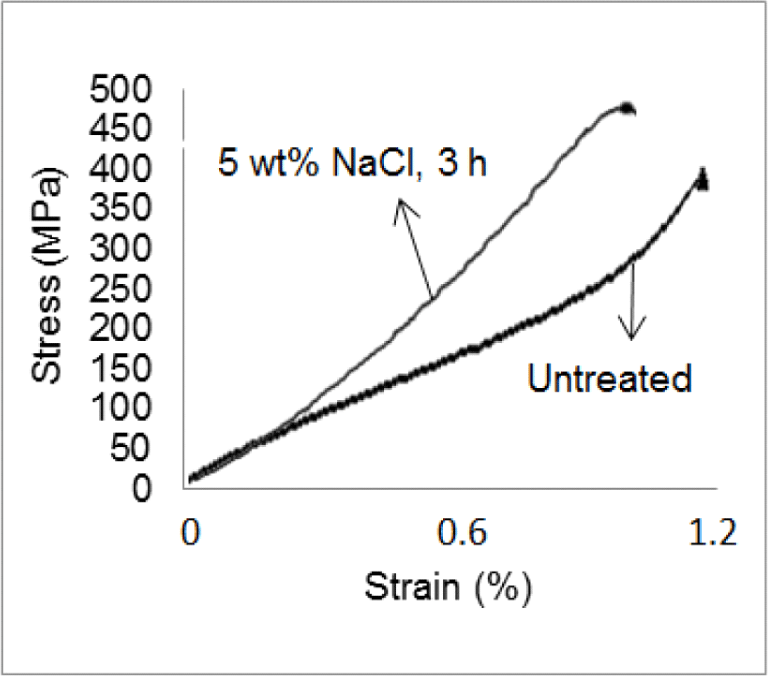
Treatment with 5 wt.% NaCl resulted in a higher tensile strength and Young’s modulus compared to using 1 and 3 wt.% NaCl. These treated kenaf fiber bundles have the potential to be used in composite boards. In a previous study, the bending values, such as the modulus of elasticity and modulus of rupture, of the composite board met the requirements of 18 types of JIS A 5098 (JIS, 2003; Setyayunita et al., 2022).
The NaCl treatment decreased the fiber bundle diameters. Fig. 3. shows the diameters of the treated fiber bundles under various conditions and Fig. 4. shows an image of a kenaf fiber bundle. The results indicated that the diameters of the fiber bundles were decreased by the NaCl treatment. The untreated fiber bundle diameter was 69.2 μm higher than that of the treated fiber bundles under all conditions. The kenaf fiber bundle treated with 5 wt.% NaCl for 3 h exhibited the most significantly decreased diameter of 45.5%. Treatment with 3 wt.% NaCl for 1 and 2 h resulted in a narrow difference in the fiber bundle diameter compared with fiber bundles treated with 1 wt.% NaCl for 3 h. The fiber bundle treatments with 5 wt.% NaCl for 1 and 2 h resulted in a similar diameter. Treatment with 1 wt.% NaCl for 1 h resulted in a decreased fiber bundle diameter of up to 19.9% compared to the untreated fiber bundles. The use of 5 wt.% NaCl resulted in the highest change in the fiber bundle diameter compared to the other percentages of NaCl for all soaking durations. The decreased fiber bundle diameter was suggested to be owing to removal of the substance from the fiber surface. Mardin et al. (2016) reported that NaCl in seawater treatment of fibers attracted impurity molecules, consisting of OH-groups, by the Na+ component.
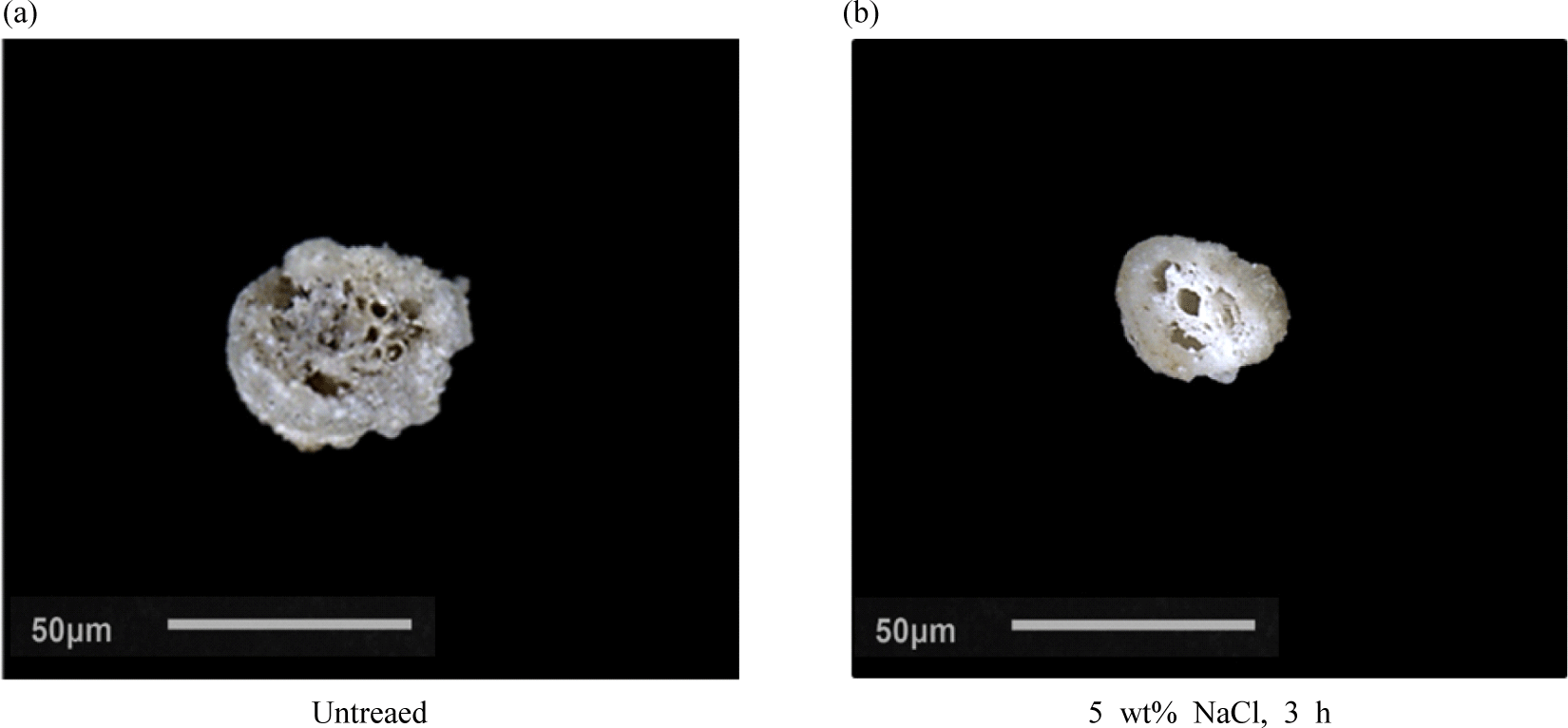
A decreased kenaf fiber bundle diameter was also observed in fiber bundle treatments using alkaline media. Mahjoub et al. (2014) reported that treatment with 5% and 7% NaOH for 3 h decreased the diameter of kenaf fiber bundles by 1.92% and 3.40%, respectively, compared to untreated kenaf fiber bundles. Increasing the soaking duration from 3 to 24 h using 5% and 7% NaOH resulted in a decrease in kenaf fiber bundle diameter of up to 3.99% and 5.33%, respectively, in comparison with untreated kenaf fiber bundles. Munawar et al. (2008) reported that the diameter of ramie fiber bundles treated with 2% (w/v) NaOH for 2 h at 95°C decreased by 33% compared to untreated ramie fiber bundles. This study also indicated that the diameters of sansevieria and ramie fiber bundles were slightly decreased by alkali and mild steam treatments and increased by chitosan treatments. The diameters of treated fiber bundles using 3 wt.% NaCl for 2 h at room temperature decreased by 31.4% compared to untreated fiber bundles. Guo et al. (2019) determined that treatment with alkaline, alkaline-potassium permanganate, alkaline-potassium dichromate, and alkaline hydrogen peroxide decreased kenaf fiber bundle diameters by up to 4.29%, 9.54%, 6.42%, and 24.33%, respectively, compared to untreated kenaf fiber bundles.
The tensile strength versus fiber bundle diameter is plotted in Fig. 5. The tensile strength tended to increase with decreasing fiber diameter. Increasing the soaking duration from 1 to 2 h did not result in a significant decrease in the fiber bundle diameter and an increase in the tensile strength. A further increase in the soaking duration from 2 to 3 h resulted in a considerable decrease in the fiber bundle diameter and an increase in the tensile strength. Using mild steam and chitosan treatments, a similar relationship was observed in ramie, pineapple, and sansevieria fiber bundles. Munawar et al. (2008) reported that the plot of mechanical properties exhibited a decreasing tensile strength with increasing fiber diameter of the treated fiber bundles. The increase in tensile strength was accompanied by a decrease in the surface area owing to the degradation caused by the treatment (Hakim et al., 2022). Furthermore, the trend implied that the decrease in the fiber bundle diameter could be owing to the weight change.
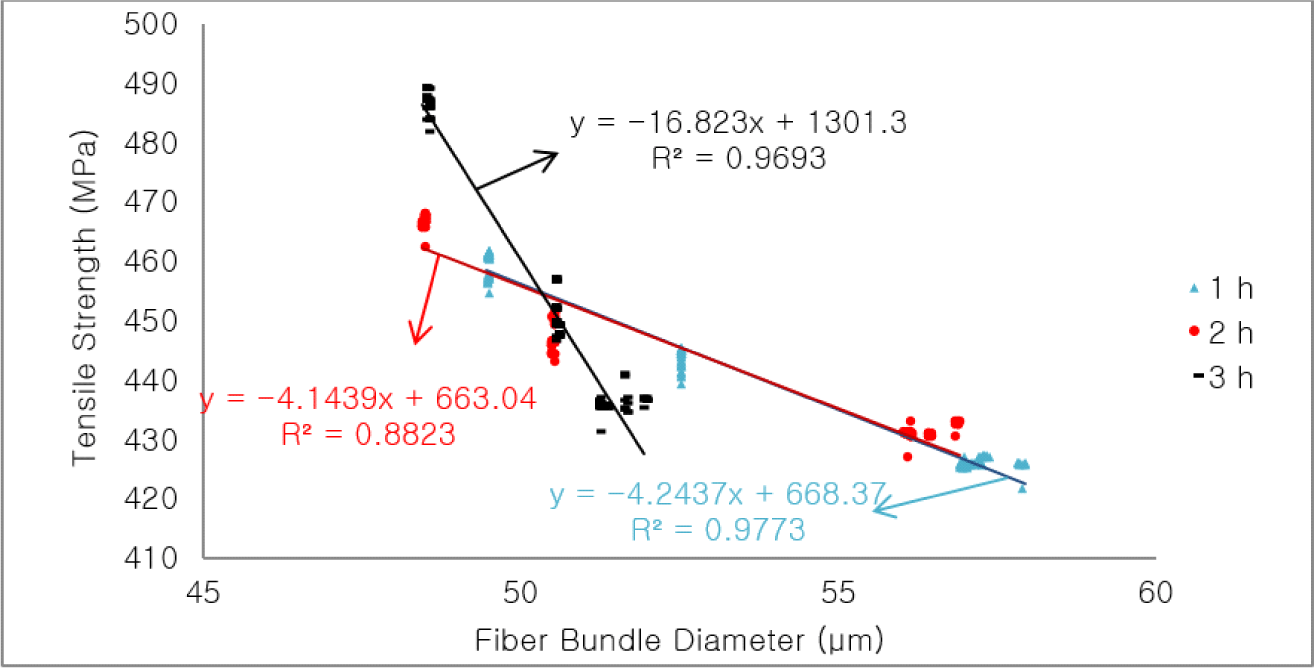
The weight change results exhibited an increase under all NaCl treatment conditions, with the highest change observed at 5 wt.% NaCl for 3 h (Fig. 6). The weight change value of all treatment conditions was approximately 21.31%, with a maximum value of 27.64% compared to that of the untreated fiber bundles. Treatment with 5 wt.% NaCl for 3 h resulted in a significant weight change in comparison with other treatment conditions. Treatment with 1 wt.% NaCl for 3 h did not result in any difference in weight change compared to treatment with 3 wt.% NaCl for 1 h. The fiber bundle treatment with 3 wt.% NaCl for 3 h also did not result in any significant change in weight. The weight change of the kenaf fiber bundle exhibited an incremental pattern with increasing NaCl concentration and soaking duration. This indicated that the increased weight change resulted in decreased fiber bundle diameters.
The weight change of the fiber bundle treated with 3 wt.% NaCl for 2 h at room temperature decreased by 20.0% compared to that of the untreated fiber bundle. Munawar et al. (2008) reported that weight changes in pineapple, sansevieria, and ramie fiber bundles treated with 2% NaOH (w/v) for 2 h at 95°C decreased by 28.9%, 23.4%, and 21.5%, respectively, compared to untreated ramie fiber bundles. Furthermore, it was reported that the weight change of treated ramie, sansevieria, and pineapple fiber bundles exhibited decreases of 10.1%, 6.0%, and 4.4%, respectively, using mild steam treatment for 2 h. Samaei et al. (2022) investigated the effect of alkaline treatment on kenaf natural fibers. They determined that treatment with 4%, 6%, 8%, and 10% NaOH for 4 h resulted in fiber weight changes of up to 14%, 18%, 20%, and 21%, respectively, compared to untreated fibers.
The surface morphologies of the untreated kenaf fiber bundles and those treated with 5 wt.% NaCl for 3 h were observed using FE-SEM (Fig. 7). The surfaces of the kenaf fiber bundles treated with 5 wt.% NaCl for 3 h were rougher than those of the untreated samples. Fig. 7 shows that the surface of the treated fiber bundle changed. The surface of the treated kenaf fiber bundle is not smooth and has longitudinal ridges, and is expected to enhance the mechanical interlocking with the adhesive. The change in the morphology of the kenaf fiber bundles owing to NaCl treatment caused changes in the weight and fiber bundle diameters, exhibiting an increase in weight and a decrease in fiber bundle diameter. These changes in the fiber bundles also increased the mechanical properties of the kenaf fiber bundles, such as tensile strength, as shown by the relationship between the kenaf fiber bundle diameters and tensile strengths. The morphology of the fiber bundles also affects the compatibility between the fiber bundle and adhesive. This can be observed in the contact angle between the fiber bundle and adhesive.
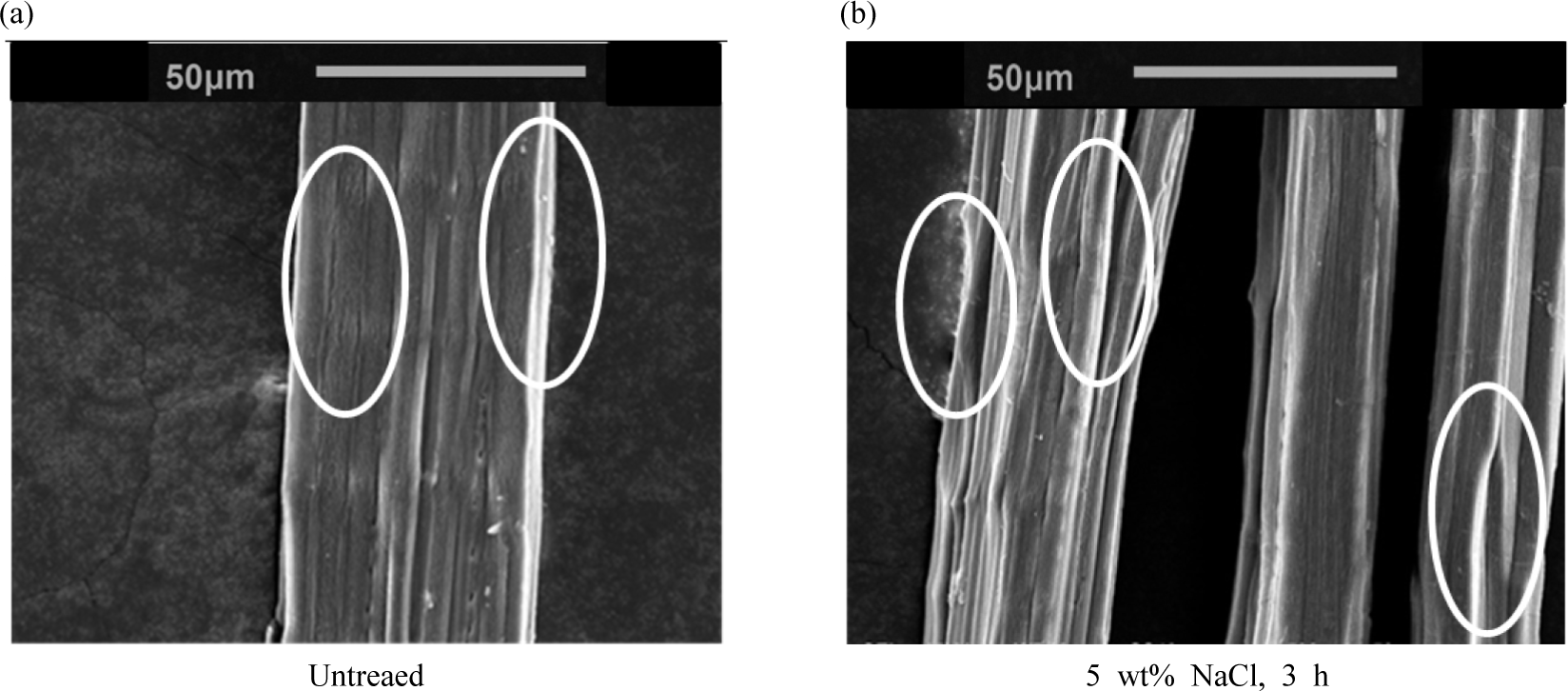
The contact angles of the kenaf fibers tended to decrease with increasing NaCl concentration and soaking duration (Fig. 8). Untreated kenaf fiber bundles exhibited a contact angle of 104°, which decreased to 73° when treated with 5 wt.% NaCl for 3 h. The results indicated that NaCl treatment decreased the contact angle between the epoxy and fiber bundle, indicating that the wetness of the epoxy on the treated kenaf fiber bundle is better than that on the untreated bundle. The smaller contact angle indicated that the surface could absorb the adhesive to cover the surface of the fiber bundles optimally. Setyayunita et al. (2022) reported that increasing the NaCl concentration and soaking duration significantly increased the internal bonding strength. This clearly indicates that the decrease in the contact angle after treatment could improve the internal bonding strength of the corresponding composite board. Furthermore, treatment with 5 wt.% NaCl for 3 h resulted in the highest internal bonding strength on the composite board using epoxy as an adhesive. NaCl treatment under various conditions also increased the physical and mechanical properties of the composite board by increasing the epoxy content (Setyayunita et al., 2021). Therefore, treating kenaf fiber bundles with NaCl improves the compatibility between the fiber bundles and adhesives.
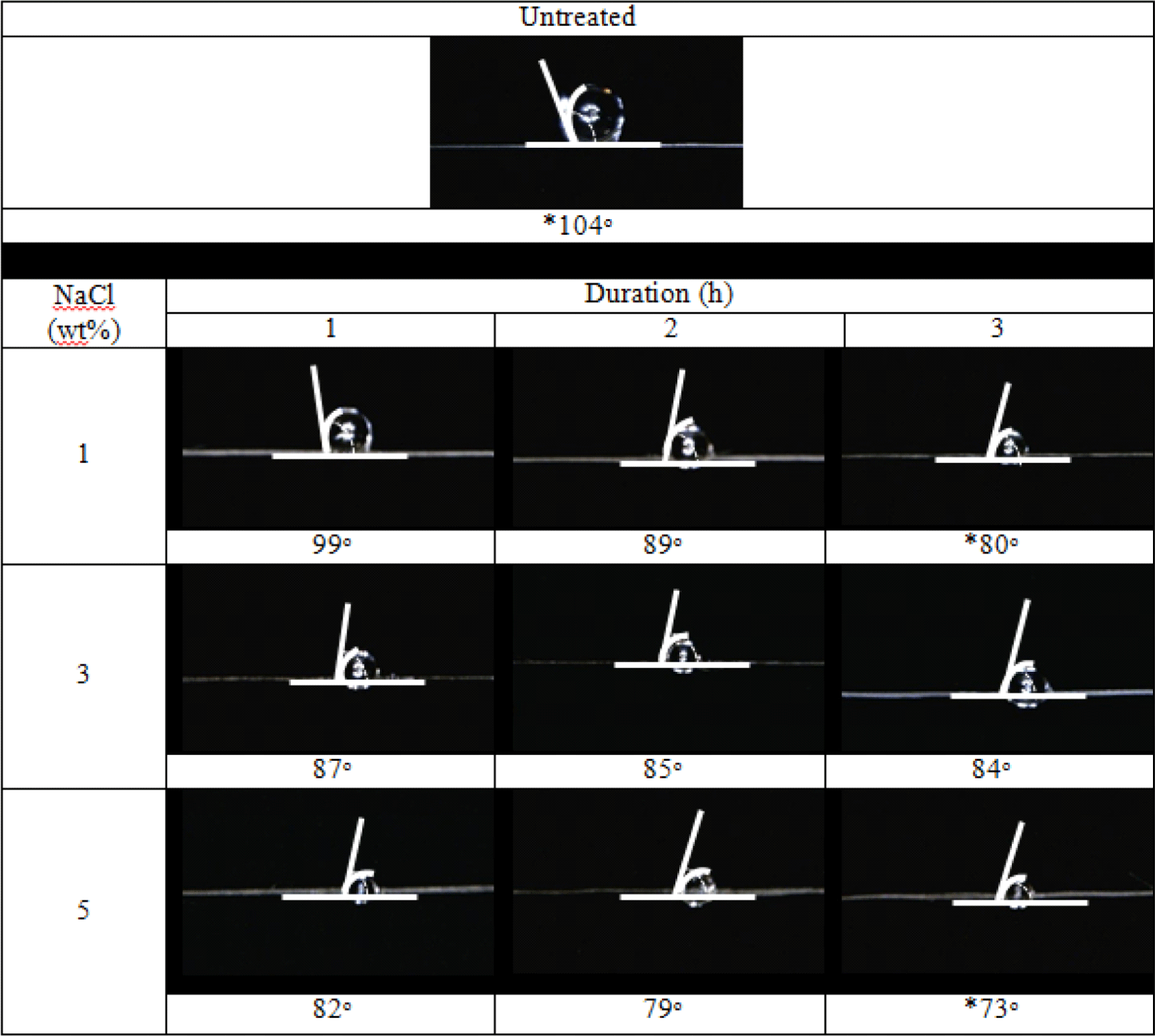
4. CONCLUSIONS
This study determined that kenaf fiber bundles treated with 5 wt.% NaCl for 3 h exhibited the highest tensile strength and Young’s modulus. The treatment increased the tensile strength and Young’s modulus of the kenaf fiber bundles by 16.06% and 24.29%, respectively, compared to untreated fiber bundles. The fiber bundles treated with 5 wt.% NaCl exhibited decreased fiber bundle diameters of 45.5%, compared to the untreated fiber bundles. Increasing the soaking duration from 1 to 2 h did not significantly decrease the fiber bundle diameter or increase the tensile strength. However, the increasing the soaking duration from 2 to 3 h resulted in a significant decrease in the fiber bundle diameter and an increase in the tensile strength. The average weight change was 21.31%, with a maximum of 27.64%. The surface of the kenaf fiber bundles treated with 5 wt.% NaCl for 3 h was rougher than that of the untreated fiber bundles. Furthermore, the treatment decreased the contact angle between the fiber bundle and adhesive by up to 30% compared to the untreated bundles. NaCl treatment was determined to be an effective method for enhancing the mechanical properties and wettability of fiber bundles, which can be applied to high-performance plant fiber composites.