1. INTRODUCTION
As the increase in greenhouse gas emissions caused by industrial development accelerates global warming, the 21st-century architecture has shifted to satisfying not only structural stability but also energy performance and eco-friendliness. In order to reduce the amount of carbon generated during the construction process, a carbon reduction plan is being proposed throughout various fields of architectural construction. The Korea Forest Service promotes the carbon absorption function of forests and carbon storage function of wood as a carbon-neutral strategy, and such strategy is already recognized internationally. Therefore, there is an increasing interest in wood as a carbon reservoir and a major material for renewable, eco-friendly architecture. In particular, engineering wood is a construction material that can be designed to improve dimensional stability by minimizing the effects of the anisotropy of wood and is used as a major structural material in med- and high-rise wooden buildings. In the 1970s and 1980s, a wooden construction material called Cross-Laminated Timber (CLT) was first developed in Austria (Li et al., 2019). CLT is a structural face material in which graded layers are orthogonally stacked, providing high dimensional stability, low air permeability, and unique specific storage capacity for relative humidity and thermal energy (Brandner et al., 2016). Currently, the number of high-rise building designs using CLT is increasing in the developed countries such as North America, Europe, and Japan, and many studies are being conducted in the academe and industry on the fire resistance, sound insulation, thermal characteristics, and structural performance for the commercialization of CLT. In order to secure better performance of CLT, studies are also being conducted to manufacture hybrid CLTs that combine the composition conditions of CLT with other tree species such as plywood, bamboo, and FRP (Choi et al., 2020; Choi et al., 2021; Galih et al., 2020; Jang and Lee, 2019; Jung et al., 2020; Kang et al., 2019; Yang et al., 2021).
For the feasibility of hardwood CLT, Kramer et al. (2014) showed that the CLT using hybrid poplar with a specific gravity of 0.34 had a bending performance equivalent to the E3 class as suggested by ANSI/APA PRG 320, an American standard, and suggested its applicability as a structural material. In addition, Mohamadzadeh and Hindman (2015) reported that yellow poplar CLT showed superior strength performance in terms of bending strength and bending rigidity than the criteria for Class V1 and V2 in ANSI/APA PRG 320. As the allowable bending stress is higher than the design value of pine, it is judged that yellow poplar can be used as a structural material (Lim et al., 2010). Therefore, broad-leaved yellow poplar as a CLT layer material seems to be sufficiently applicable. Not only the strength performance but also the quality of the durability performance should be considered. During the durability test, the adhesive performance as specified by the quality standard is affected by various factors, which also affect the strength performance, and it is necessary to study the optimal manufacturing conditions. According to a study by Yusof et al. (2019), it was found that among the specimens made of phenol-resorcinol-formaldehyde (PRF) and polyurethane (PUR) of the Acacia species, the specimen made of PRF with a lower delamination rate showed better strength performance in bending, shearing, and compression. Knorz et al. (2017) reported that the pressure of bonding and the thickness of the layer do not affect the delamination result, and Han et al. (2019) proposed the use of a layer with a moisture content of less than 15% because the use of a high moisture content causes delamination defects when manufacturing CLT. Song and Hong (2016) reported that the direction of the annual ring of the layer affects the adhesion performance of CLT. In North America and Europe, PUR adhesives, which are eco-friendly and fast-curing adhesives, are mainly used. PUR adhesives have flexibility, good low-temperature adhesive performance, high cohesive strength, and easily controlled curing speed (Kim, 2003). Gong et al. (2016) reported that it is economical to apply a PUR adhesive with a pressure of 1.2 MPa and an application amount of 200 g/m2 as the optimal bonding conditions for larch CLT. However, it has been reported that excessive temperature or relative humidity deteriorates the adhesive strength of PUR adhesives (Künniger et al., 2019; Na et al., 2017). Therefore, as shown in Fig. 1, when domestic climate conditions vary in temperature and humidity depending on the season, it is thought that the PUR adhesive will affect the adhesive performance of CLT depending on the manufacturing environment of CLT.
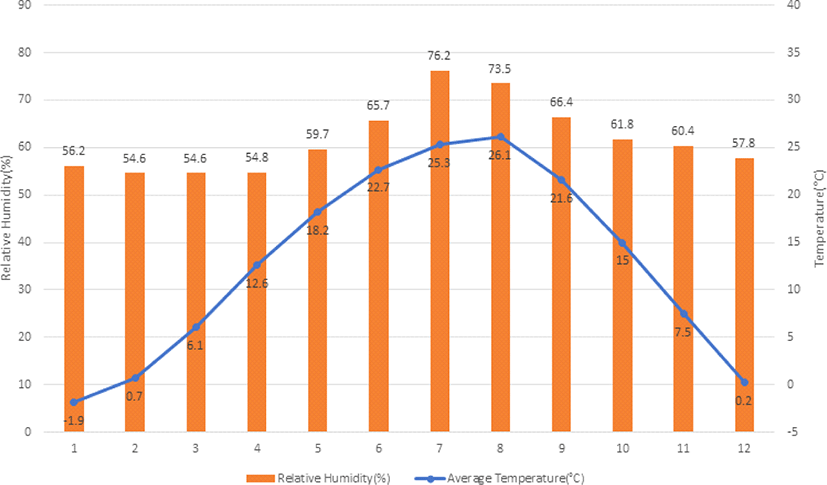
In this study, an adhesion performance test was conducted to explore factors affecting the adhesive performance of the domestic manufacturing environment to establish the manufacturing conditions for a mixed CLT of larch and poplar using a PUR adhesive. The PUR adhesive performance of CLT was compared according to temperature and humidity conditions that vary according to seasonal changes in Korea and the pressure conditions during CLT manufacturing.
2. MATERIALS and METHODS
Japanese larch (Larix kaempferi (Lamb.) Carrière) and yellow poplar (Liriodendron tulipifera L.) were used for the production of mixed CLT. The size of the larch and yellow-poplar layers was 100 mm wide, 25 mm thick, and 500 mm long. A non-defective layer material with no visually noticeable knots or cracks of 17 mm or less was selected as the layer material. The layer material was purchased from the Jungbu Distribution Center in Yeoju, Gyeonggi-do, and the average dry density and average values of moisture content were 0.54 g/cm3 and 10.5% for larch, and 0.59 g/cm3 and 12.2% for poplar, respectively. As the adhesive for manufacturing CLT, a commercially available G10(A) one-component PUR adhesive (Kiilto, Turku, Finland) was used. In general, it is recommended to use K company’s PUR adhesive in an environment with a temperature of 18°C–20°C and relative humidity of 40%–75%. Since the pot life of the adhesive must be secured according to the degree of automation of the CLT manufacturing process, the G10 adhesive (G10B) with an increased pot life was additionally selected and used to reflect the domestic manufacturing process (Table 1).
Product name | Open time | Viscosity | Pressing time | Density | Compression pressure | Mix ratio | |
---|---|---|---|---|---|---|---|
Kestopur G10 | G10A | 10 min | 15,000 mPas | Minimum 20 min | 1.2 kg/dm3 | 0.6–1.0 N/mm2 | 1-Component |
G10B | 30 min |
For the composition of mixed CLT, larch was used for the external layer and middle layer, and yellow poplar was used for the internal layer (Fig. 2). The amount of PUR adhesive applied was 200 g/m2 for one-sided application, and the pressing pressure was applied at 1 MPa using a hydraulic press (Anjeon hydraulic machinery (AJ), Kimpo, Korea). Mixed CLT was prepared based on the type of adhesive, pressing time, temperature and relative humidity, and moisture supply method (Fig. 3).
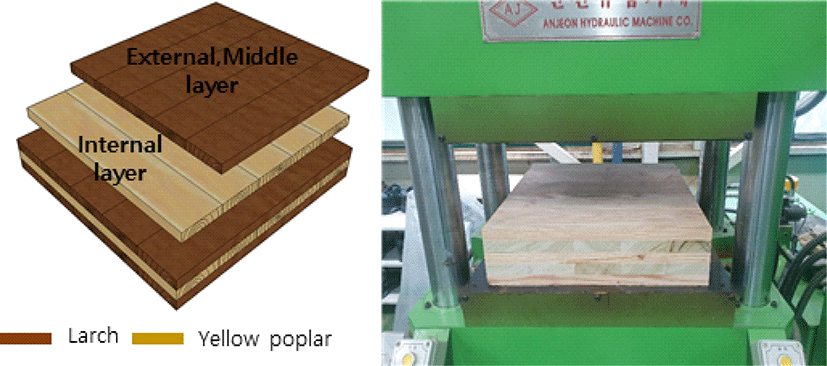
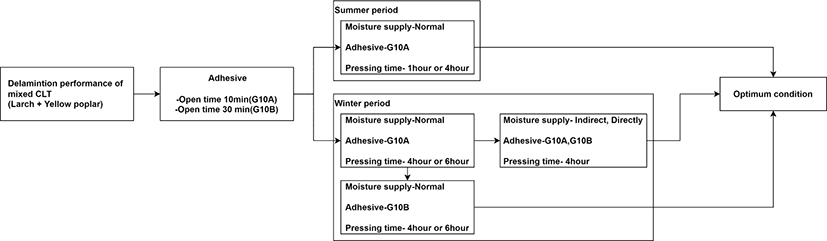
The CLT test piece was manufactured by applying a pressing time of 4 hours in both summer and winter by referring to the TDS (Technical Data Sheet) of the adhesive under laboratory conditions. Tankut et al. (2016) reported that the pressing time was affected not only by the type of adhesive but also by the temperature and humidity of the surrounding environment. Therefore, the temperature and humidity inside the laboratory were on average 24.2°C and 64.1% in summer, respectively, and 15.3°C and 20.8% in winter. To compare the adhesion performance according to the pressing time, a CLT test piece was prepared by applying the pressing time of 1 hour (LY1) and 6 hours (LY6) based on the recommended pressing time (LY4). The LY1 type was selected in consideration of the high-temperature and high-humidity manufacturing environment and the productivity in summer, and the LY6 type was selected in consideration of the low-temperature and dry manufacturing environment in winter and the faster curing property of the adhesive than that of resorcinol adhesives. In addition, a mixed CLT was prepared by applying a pressing time of 4 hours (LYB4) and 6 hours (LYB6) using the G10B adhesive with an increased pot life.
To improve the dry manufacturing environment during the winter period, mixed CLT was prepared according to the moisture supply method. Galvez et al. (2020) reported that the maximum value of mechanical properties could not be reached only by mixing the adhesive component, and the adhesive had to be exposed to appropriate relative humidity and temperature. And it was said that humidity was necessary for curing and that an increase in temperature increased the degree of cross-linking of the polymer, but a long exposure time caused the decomposition of the polymer. Therefore, PUR adhesives have an adhesion mechanism that is affected by moisture. Mixed CLT was manufactured through a method of directly supplying moisture to the surface of the layer material before adhesive application and a method of supplying moisture indirectly to the CLT manufacturing space. When moisture was directly supplied, the surface moisture content of the layer material increased by 2.5%. In the indirect moisture supply method, humidification was performed with a target of 60% relative humidity. Table 2 shows the CLT adhesion conditions and nomenclature.
5ply mixed CLT was manufactured in the dimension of 500 (b) × 500 (l) × 125 (h) mm and was cured at room temperature for one week after production.
The cured CLT was cut to a size of 100 (b) × 100 (h) × 125 (l) mm and used as 24 boiling water soak delamination test specimens. For the adhesion performance test of mixed CLT, a boiling water soak delamination test was performed based on Korean Standards Association (2021). In the boiling water soak delamination test, the test piece was immersed in boiling water for 4 hours, in water at room temperature (10°C–25°C) for 1 hour, and then placed in a constant-temperature dryer at 70 ± 3°C (Fig. 4). The delamination rate was measured after drying so that the mass was in the range of 100% to 110% of the mass before the test. For delamination, a delamination length of 3 mm or more was measured, and cracks in wood due to drying or knots were excluded from the measurement. The delamination rate of all the test pieces was measured based on the adhesive layer on the 4 sides, and the said rate was calculated using equation (1).
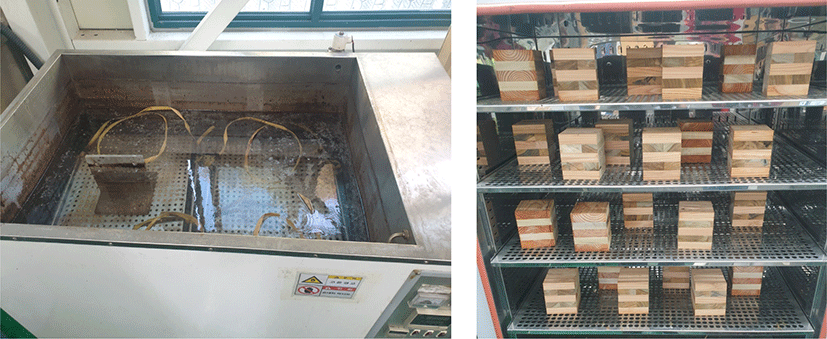
Here, LD is the sum of the delamination lengths of the parallel adhesive layer in the cross-section of the specimen while LG is the sum of the lengths of all adhesive layers in the cross-section of the specimen, including the parallel adhesive layers and the orthogonal adhesive layers on the four sides, except for the front and back surfaces.
According to KS F 2081, the standard for adhesion performance of CLT, the delamination rate when boiled is specified to be less than 10%. Manufacturing conditions for performance improvement were selected according to the results of the boiling water soak delamination test. The average delamination rate by region was compared as shown in Fig. 5 to examine the adhesive performance distribution of mixed CLTs depending on the manufacturing environment.
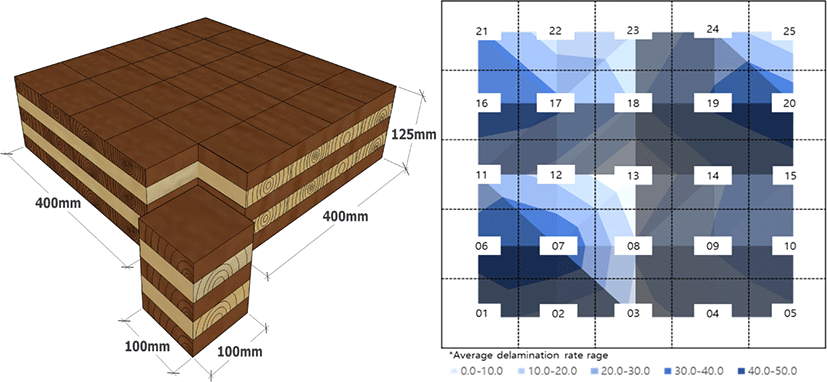
3. RESULTS and DISCUSSION
To identify the CLT adhesive performance of PUR adhesives according to the manufacturing environment, test pieces were prepared and compared for each pressing time. The average delamination rate of the test piece, LY-A4SN, produced by applying a pressing time of 4 hours in summer was 5.3%, which satisfied the KS quality standards. The LY-A1SN specimen produced by shortening the pressing time to 1 hour to improve the productivity of CLT did not satisfy the KS quality standard with an average delamination rate of 14.1%. LY-A4WN, manufactured in winter with a pressing time of 4 hours, showed an average delamination rate of 25.8%, which did not satisfy the KS standard. When the pressing time was increased, LY-A6WN showed an average delamination rate 2.3% higher than LY-A4WN. Comparing the delamination for each part according to the season in Fig. 6, the LY-A4SN specimen produced in summer showed good adhesion performance in all parts, while the LY-A4WN specimen in winter conditions showed a high delamination rate in a specific part. Thus, when the PUR adhesive is applied in the domestic production of mixed CLT in the future, it is necessary to find a suitable pressing time depending on the ambient temperature and humidity.
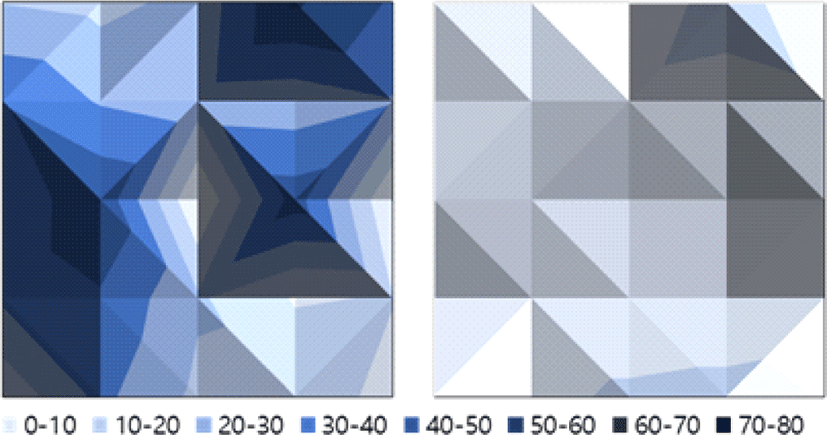
To improve the adhesive performance of mixed CLT manufactured in winter, the optimal pressing time was determined using the G10B adhesive with an increased pot life. The test piece, LY-B4WN, using the G10B adhesive with an increased pot life did not satisfy the KS standard with an average delamination rate of 22.9%. However, when the pressing time was increased, the rate of delamination improved by 7.9% as in the case of LY-B6WN. When the delamination rates of LY-A4WN and LY-A6WN using an adhesive with a short pot life (G10A) were compared, the specimen with an increased pressing time also showed better adhesion performance. When the test pieces of adhesives with different pot life were compared under the same conditions, the adhesive performance of the test pieces made with G10B, which had a long pot life, was found to be better. Tankut et al. (2016) reported that many adhesion failures occurred beyond the pot life. Therefore, the appropriate pot life should be considered when manufacturing mixed CLT using a PUR adhesive.
The adhesion performance of the mixed CLT using the PUR adhesive was verified according to changes in moisture content due to direct and indirect moisture supply in winter. The mixed CLT LY-A4WD and LY-B4WD produced by directly supplying moisture to the layer material did not satisfy the KS quality standards. According to Sterley et al. (2012), the higher the water content, the faster the curing rate was for PUR adhesives. LY-A4WI and LY-B4WI, which were produced by indirectly supplying moisture, varied in average delamination rate at 14.1% and 11.2%, respectively, compared to the specimens produced by direct moisture supply, and showed better adhesion performance. Comparing the delamination for each part in Fig. 7, it is believed that the test piece of LY-B4WD produced by directly supplying moisture showed the highest delamination because the adhesive line between the wood and the adhesive could not be formed due to the rapid curing of the adhesive itself. The LY-B4WI specimen showed better adhesion performance than that of LY-B4WN and LY-B4WD. When the test pieces using adhesives with a different pot life were compared under the same conditions, it was confirmed that the test pieces with an increased pot life showed better adhesion performance (Table 3).
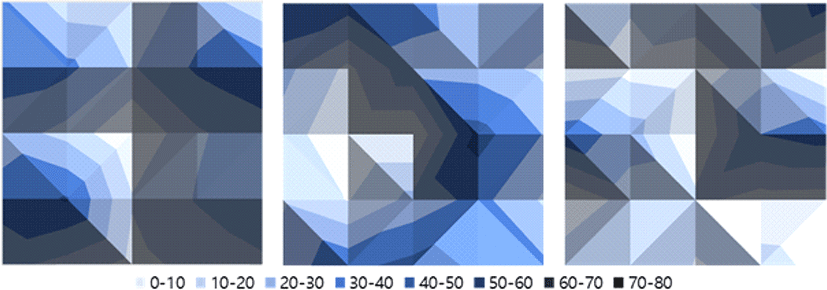
To investigate the effect of the temperature of the PUR adhesive, two specimens, LY-A4SN and LY-A4WI, were compared with a similar relative humidity of 60%. The average delamination rate appears to vary by 21.1%, and a clear difference was observed in the delamination for each part, as seen in Fig. 8. Therefore, the temperature was also found to be a factor affecting PUR. Thus, in order to manufacture mixed CLT using a PUR adhesive, it is necessary to take measures to maintain an optimal bonding environment in response to seasonal temperature and humidity changes.
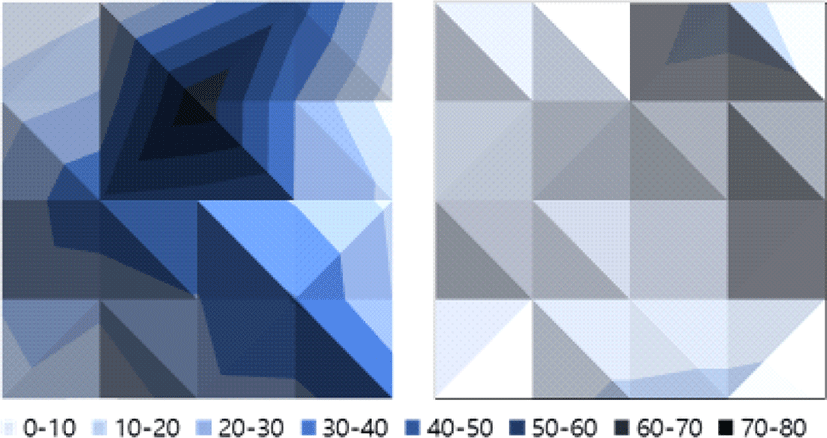
After the boiling water soak delamination test of mixed CLT, the typical delamination shapes appeared as shown in Fig. 9 and Fig. 10. As shown in Fig. 9, in the specimen that satisfied the KS boiling delamination criteria, the wood was fractured because the adhesive suppressed the deformation of the layer material due to drying. Fig. 10 shows a specimen that did not meet the KS quality standards, and the adhesive could not suppress the cupping or crowning phenomenon caused by drying, and delamination occurred in the adhesive layer [Fig. 10(b)]. In the case of the specimen under the summer conditions set in this experiment, the adhesion between the wood and the adhesive was excellent, so more fractures were observed between the wood than the delamination of the adhesive layer.
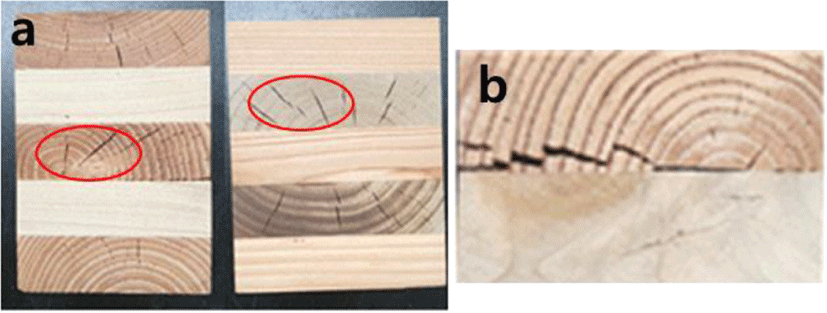

4. CONCLUSIONS
To determine the optimal bonding conditions for structural mixed CLT using PUR in the seasonal manufacturing environment, a boiled water soak delamination test was performed by manufacturing a mixed CLT according to the adhesive pot life and its pressing time, the temperature and humidity conditions of the manufacturing environment, and the moisture supply method. The conclusions from the delamination test according to each parameter are as follows:
-
In summer manufacturing conditions (average temperature of 24.2°C, relative humidity of 64.1%), the delamination rate of the mixed CLT satisfied the KS adhesive performance standards by using the PUR adhesive with a short pot life and applying a pressing time of 4 hours.
-
In winter manufacturing conditions (average temperature 15.3°C, relative humidity 20.8%), the boiling delamination rate of mixed CLT made with PUR did not satisfy the KS standard. However, it was observed that the adhesive performance of mixed CLT was improved when the pot life and pressing time of the adhesive were increased and when the relative humidity was increased through indirect moisture supply. When the average delamination of the mixed CLT manufactured under the summer and winter manufacturing conditions at similar relative humidity was compared, the CLT under the summer manufacturing conditions showed better adhesive performance. Hence, it can be presumed that temperature also affects the adhesive performance.
We conclude that this study provides the fundamental data to determine the manufacturing time and optimal temperature and humidity conditions based on the adhesive properties as manufacturing conditions for structural CLT using PUR.