1. INTRODUCTION
Natural fibers have been established as sustainable materials to replace the current synthetic fibers (Asim et al., 2018; Yusoff et al., 2016), and it has received attention from different studies and industries due to the advantages of low cost, low density, biodegradable and renewable materials (Akhtar et al., 2016; Azwa and Yousif, 2013; Sharba et al., 2015; Sivakumar et al., 2018; Yousif et al., 2012). It is applied in many sectors such as automobiles, furniture, packaging, and construction. Furthermore, natural fibers such as sisal, jute, kenaf, coir, and flax are commonly used as reinforcing and filling materials for polymeric composites. The main concept of reinforcing the polymer with such fibers is to improve the mechanical properties of tensile, impact, and bending (Sivakumar et al., 2018; Yousif et al., 2012). Kenaf fibers are less abrasive and harmful when processing the materials, and they have good mechanical properties comparable to synthetic fibers (Azwa and Yousif, 2013).
Kenaf fiber is one of the natural fibers used as raw material for various industries such as fiberboard, pulp and paper, textiles, carpets, handicrafts, and others. Kenaf (Hibiscus cannabinus) is a warm-season annual fiber crop in temperate and tropical areas. It is a fibrous plant, consisting of an inner core fiber (75%–60%), which produces low-quality pulp, and an outer bast fiber (25%–40%) in the stem. The plant reaches a height of 2.7 to 3.6 m and the fibers are harvested for its stalks (Azwa and Yousif, 2013). Kenaf bast fibers are widely used in studies and industries because of their advantage in terms of chemical composition and higher cellulose content (Hamidon et al., 2019; Khan and Khan, 2015). Furthermore, they have a bast fiber that contains 75% cellulose, 15% lignin, and 10% pectin and offers the advantages of being biodegradable and environmentally safe. It is also believed that higher cellulose content can offer good mechanical properties to the end product in terms of flexural and tensile strength (Tajvidi et al., 2006). This was proven by previous studies conducted by Ishak et al. (2009) that compared the mechanical properties of polymer composites reinforced with kenaf bast and core. It was reported that kenaf bast increased the tensile, flexural, and impact strength of the composite (Ishak et al., 2009). The combination of good flexural and tensile strength makes these fibres a preferred choice for extruded, molded, and nonwoven products (Yahaya et al., 2015).
Kenaf has been used in commercial applications such as composite boards, automotive panels, insulation mats, and geotextiles, and the board is far stronger and lighter than plywood. There are several works of literature on the development of kenaf reinforced composite, and some studies are focused on the reinforced polymer composite using polypropylene (Rashdi et al., 2009, 2010; Sapuan et al., 2011; Tajvidi et al., 2006), epoxy (Ghori and Rao, 2021; Makinejad et al., 2010; Saba et al., 2016), polyester (Aziz and Ansell, 2004; Aziz et al., 2005; d’Almeida, 2006; Osman et al., 2011; Yousif et al., 2007), polyurethane (El-Shekeil et al., 2012a; El-Shekeil et al., 2012b), polyethylene (Paul et al., 1997), isocyanate (Iswanto et al., 2020), urea formaldehyde (Wibowo et al., 2021), and elastomer (Anuar and Zuraida, 2011). Meanwhile, epoxy has high mechanical and thermal properties compared to other resins. It is a polymer matrix widely used in advanced composites since it is good in stiffness, and has good dimensional stability with good chemical resistance. Epoxy is also quite low in molecular weight, and the monomers have low shrinkage during cure (Ghori and Rao, 2021; Makinejad et al., 2010; Saba et al., 2016).
However, poor adhesion between the fiber and the matrix has been found, since the mechanical properties of composite materials reinforced with natural fibers are highly dependent on the type of bond as reported by many studies (Anuar and Zuraida, 2011; d’Almeida, 2006; El-Shekeil et al., 2012b; Iswanto et al., 2020; Saba et al., 2016; Tajvidi et al., 2006). Natural fibers contain cellulose, hemicellulose, pectin, and lignin and are rich in hydroxyl groups. They are strongly polar and hydrophilic materials whilst polymer materials, which exhibit hydrophobicity. Therefore, the chemical modification of the natural fiber surface utilizing treatment is one of the largest fields of the latest study to increase the compatibility and strength of the interface bond (Hamidon et al., 2019; Ishak et al., 2009). Chemical treatment for bleaching, acetylation and alkali increases the adhesion of fibers by increasing roughness through the surface from dirt and by disrupting the process of absorption of moisture through the OH-group layer (Tajvidi et al., 2006; Yahaya et al., 2015). Some chemicals are used to dissolve the pectin and separate the components, and this method produces high-quality fibers. The use of chemicals that have been widely used for modification also creates problems in the composite industry. Modified materials often used have a high pH and can quickly damage supporting equipment in production. For example, NaOH solutions can decontaminate aluminum and iron materials. The reaction that occurs is a metal oxide dissolution at a faster rate because the pH is far from the neutral value (Horváth et al., 1994). Therefore, the use of chemicals with a pH that is relatively close to neutral is expected to be a solution to these problems, with the hope that modified natural fibers can have good compatibility with adhesives without giving other negative effects on industrial activities. In addition, seawater can be used as a fiber modification material which has pH close to neutral (8.3–9.2).
Natural fibers treated with seawater had higher tensile strength than untreated fiber (Nosbi et al., 2011; Mardin et al., 2016b) or even in acid treated fiber (Nosbi et al., 2011). According to scanning electron microscopy, the seawater treatment improved the interfacial bonding of matrix and fiber (Ishak et al., 2009; Mardin et al., 2016a; Mardin et al., 2016b). Based on Mardin et al. (2016b), the improvement of the interfacial bonding strength was suspected due to NaCl content of seawater. In other studies, fiber treated with seawater showed significant increase in density and tensile modulus (Mahjoub et al., 2014), compressive strength (Mwaikambo and Ansell, 2006), as well as dimensional stability (Geethamma and Thomas, 2005). It was supposed that Na+ of NaCl in seawater has an important point to create hydrophobic fiber resulted decreasing water sorption (Hamidon et al., 2019; Khan and Khan, 2015). In the other hand, seawater consisted not only NaCl but also other components like sulfur, carbonate, and etc (Geethama and Thomas, 2005; Mardin et al., 2016b). Other studies implied different location of seawater had different concentrations of NaCl that suspected affecting the different properties of composite board (Ishak et al., 2009; Mardin et al., 2016a; Mardin et al., 2016b). Variation of soaking time in seawater treatment affected the properties of fiber (Nosbi et al., 2011) and composite (Ishak et al., 2009; Mardin et al., 2016a; Mardin et al., 2016b). However, there are no studies focused on the effect of NaCl solution treatment on the fiber or composite board. Therefore, this study focused on the effect of different concentration of NaCl solution and soaking time to the characteristic of composite board.
2. MATERIALS and METHODS
Kenaf (Hibiscus cannabinus) bast fibers obtained from Bogor, West Java, Indonesia were used as raw materials. Kenaf stems were harvested after 150 days from seeding. The samples were air-dried to a moisture content of 12% to 13%, and cut into 25 mm long. The diameter of bast fiber bundles was ranged from 0.45 ± 0.013 to 0.692 ± 0.017 mm. Epoxy and hardener produced by Alfatama Inticipta were used as matrix. NaCl (99%) produced by Sigma Aldrich was used for chemical treatment of kenaf fiber.
The kenaf fibers were cut in 25 mm length, and the parts were chemically treated at 1, 3, and 5 weight percent (wt%) NaCl solutions for 1, 2, and 3 hours at room temperature. In the treatment process, the fibers were immersed in the solution and then washed with water. The ratio of the solution to fibers was 20:1 (w/w), and after the immersion, the fibers were rinsed using water until the pH of the water reach 7. Meanwhile, the untreated and treated fibers were fully dried inside oven at 80°C for 6 hours, and the moisture content was around 2% to 4%.
Epoxy resin and hardener were uniformly mixed at a ratio of 1:1 (g/g) for 15 minutes. Kenaf fiber and epoxy were mixed manually with the total epoxy loading at 20% by weight. In the manufacturing process, a mat with dimensions 250 mm × 250 mm × 150 mm was used for making the test sample. The composite was pressed with a hot-pressing machine (PCS-700, Riken, Wako, Japan) at 120°C for 10 minutes at a constant pressure of 3.5 MPa and the target of thickness was 10 mm. It was then cut based on the standard size of board evaluation, and each experiment was conducted in triplicate. Furthermore, the mean and standard deviation values were calculated.
The boards were evaluated according to JIS A 5908. The physical and mechanical properties tested were thickness swelling (TS), water absorption (WA), modulus of rupture (MOR), modulus of elasticity (MOE), and internal bond (IB) strength. In addition, the TS and WA tests were performed on a 50 mm × 50 mm × 10 mm specimen from each board after water immersion for 24 h at room temperature. The weight and thickness of the specimens were recorded for each specimen before and after immersion, and a similar size was used for the IB test. Furthermore, the bending properties were evaluated by conducting a static three-point bending test on a 200 mm × 50 mm × 10 mm specimen for each board in dry conditions. The support span was 150 mm, while the speed of testing was 10 mm/min. Each experiment was performed in triplicate, and the standard deviations were calculated and shown as error bars in each corresponding figure.
Wettability is expressed as the advancing contact angle of epoxy solution on the outer surface of fibers. Prior to contact angle measurement, fiber specimens were conditioned at room humidity (RH) and temperature for 1 week. Epoxy solution was dropped onto the surface of the fibers with a micropipette. A photograph was taken 10 s after the solution dropped. The contact angle was calculated with the height and chord of the droplet measured. Five measurements were conducted for each sample. In this study, the contact angles were tested for untreated and treated fiber with 1% and 5% NaCl for 3 h.
The measurement data obtained from the study were then arranged in an analysis of variance (ANOVA) was performed to determine the effect of the treatment given. Analysis of diversity was carried out on each parameter observed, namely the physical properties of composite board which include TS and WA and mechanical properties of composite board which include IB, MOR, and MOE.
3. RESULTS and DISCUSSION
The densities of composite boards range between 0.732–0.799 (g/cm3) and there is no significant difference of the values. The MOE and MOR of NaCl-treated kenaf composite board can be seen in Fig. 1. It showed that the kenaf treated at 5% NaCl concentration for 3 h was recorded with the highest flexural strength as 2.085 GPa for MOE and 19.77 MPa for MOR. It clearly seen that at 3 h treatment time produced relatively same of the MOE and MOR values at different NaCl concentrations, which all of the values meet the requirement of the 18 types of JIS A 5098. However, at the same NaCl concentration, longer treatment time produced higher MOE and MOR values. It can be seen that the bending properties significantly increased with increasing concentration of NaCl and duration of fiber soaking. From this research, the optimum bending strength could be achieved using fiber treated at the concentration of 1% NaCl for 3 h.
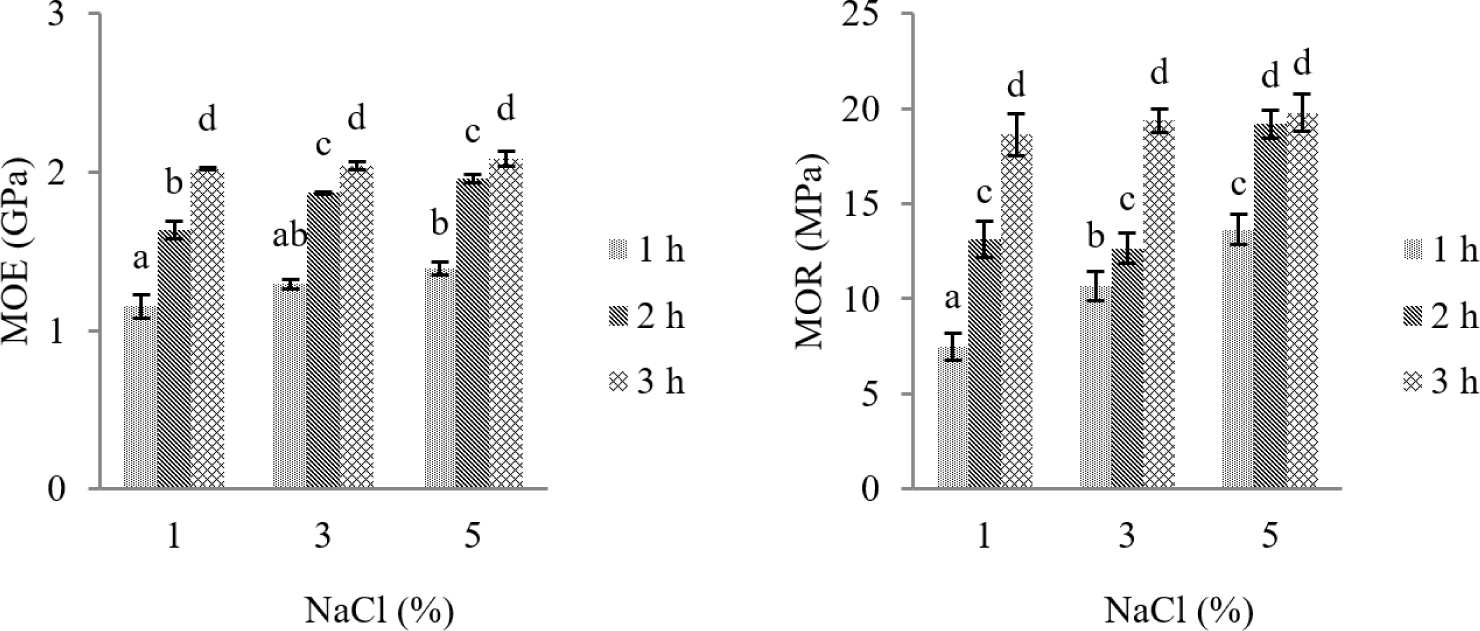
In another study, sugar palm fibers were soaked in seawater for the same duration to obtain a suitable replacement for the chemical treatment of natural fibers for enhancement of fiber-matrix interfacial adhesion. The effect and flexural strength of the treated sugar palm fiber/epoxy composites are higher than the untreated. Besides, the 30% fiber content treated with seawater had a higher flexural strength with 7.35% of upgrades. These discoveries suggest that the mechanical properties of sugar palm fiber composites have been improved. The improvement of interfacial adhesion of the sugar palm fiber was because of the evacuation of impurities and the impact of fibrillation, which made unsaturated polyester resin enter the sugar palm structure and expanded the surface contact region with the matrix (Yousif et al., 2007).
Van de Weyenberg et al. (2003) inspected the effect of flax and the fiber treatment using a combination of alkali and dilute epoxy on the mechanical properties of flax fiber reinforced epoxy composites. The most increasing of the flexural properties of the flax fiber reinforced epoxy composites can be sought by chemical treatment. There was an increment of transverse strength of up to 250% and transverse modulus of up to 500%. It is also found in alkali treatment on Indian grass fiber that improved the flexural qualities 40% compared to the raw fiber (Liu et al., 2004).
Fig. 2 shows that the value of the IB strength of boards is about 1.8–2.71 MPa. It is interesting that all of the composite boards have high IB strength values and meet the requirement of the 18 types of JIS A 5098. The highest IB values were obtained when the manufacture used kenaf fiber treated with 5% NaCl for 3 h. It can be seen that the IB significantly increased by increasing concentration of NaCl and duration of fiber soaking.
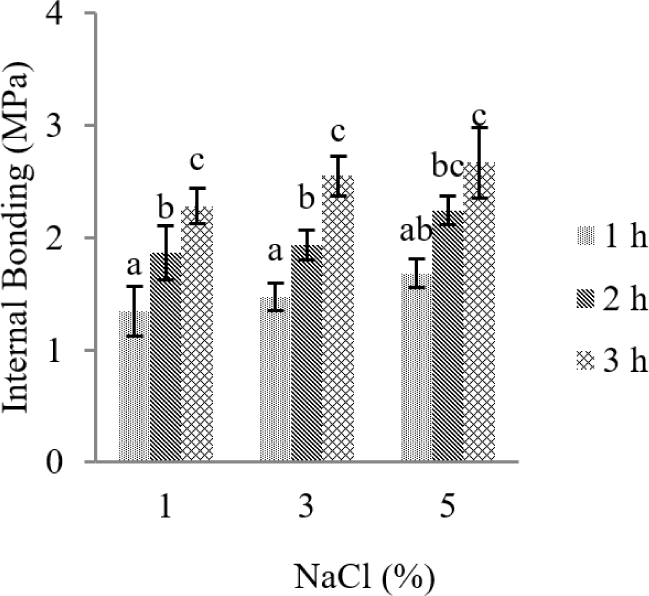
Generally, chemical modification or treatment of natural fibers containing kenaf is carried out using reagents containing functional groups capable of binding to the hydroxyl groups of the natural fibers. A few types of chemical modifications reported in previous studies of the literature have achieved some level of success in improving the adhesion of fiber matrices of natural compounds (Hong et al., 2008; John et al., 2008; Mardin et al., 2016a; Mardin et al., 2016b; Munawar et al., 2008). Chemical treatment creates multiple voids on the fiber surface, and mechanical bonding improves surface adhesion (El-Shekeil et al., 2012a). Chemical fiber treatment is very important for enhancing the adhesion between hydrophilic natural fibers and the hydrophobic polymer matrix at the interface (Chandrasekar et al., 2017; John et al., 2008; Mat Taib et al., 2009). Generally, chemical modification or treatment of natural fibers, including kenaf is conducted using a reagent, which contains functional groups that are capable of bonding with the hydroxyl group from the natural fibers.
Fig. 3 shows the contact angles in different kenaf fibers with increasing level content of NaCl and duration of fiber soaking. Kenaf fibers untreated had 104° for contact angle. And the contact angles were 80° and 73° on condition of 1% and 5% NaCl for 3 h, respectively. This angle provides optimal wetness as determined by the size between the surface of the fiber and the adhesive which is near zero. A near-zero contact angle indicated that the surface could absorb liquid with lower surface tension, allowing the matrix to optimally cover the surface of the fiber. An important reason for the low mechanical properties of natural fibers reinforced composites is their poor wettability with hydrophobic matrices. The finer surfaces of natural fibers have been adapted to a variety of chemical treatments, and the coarser surfaces and fibrillation allow for better mechanical interaction with the matrix (Tajvidi et al., 2006). The positive ions of the fiber and the negative ions of NaCl provide a more complete fiber-matrix bond (Mardin et al., 2016a; Mardin et al., 2016b).
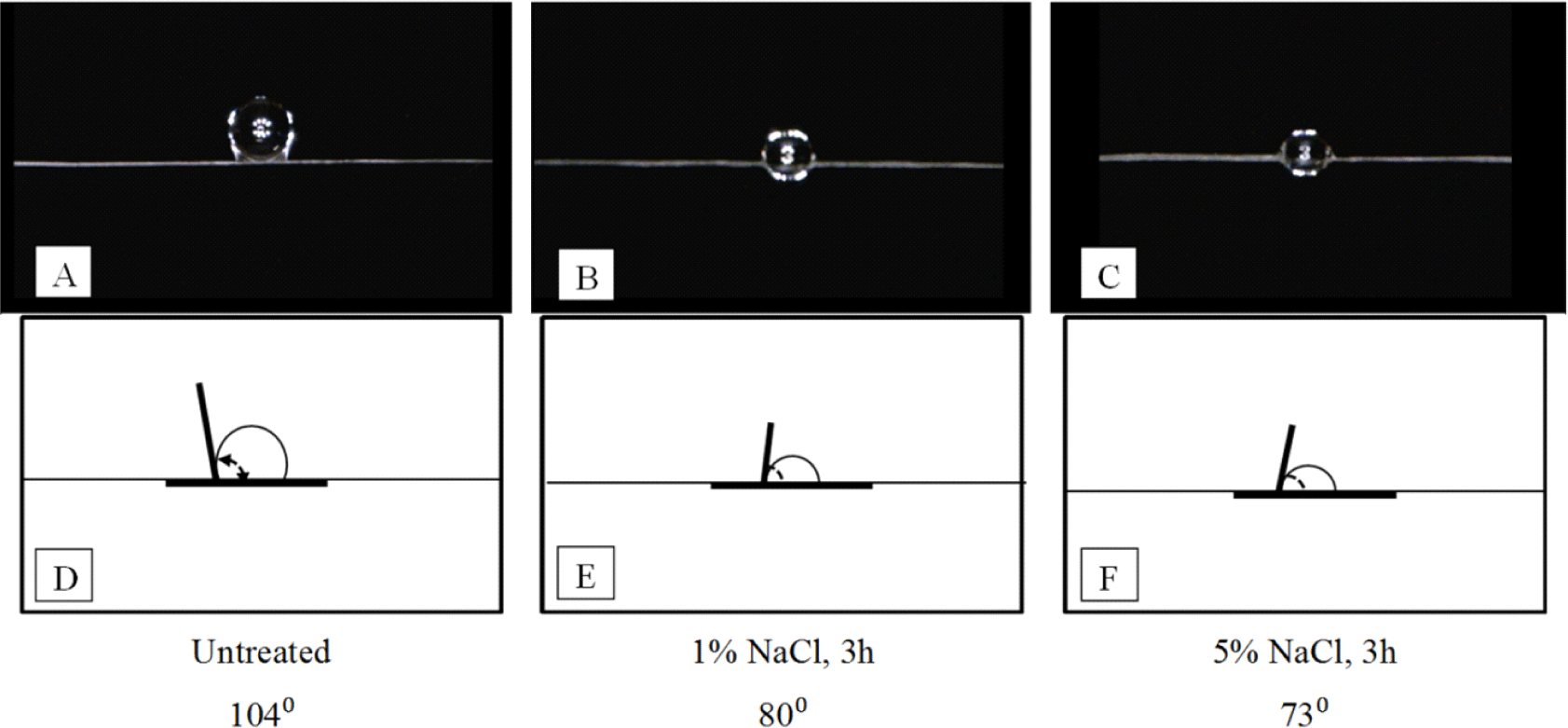
The TS after 24 h water immersing at room temperature was represented in Fig. 4. The range of TS values of treated kenaf composite boards was between 3.0%–4.3%. The kenaf fiber treated with all conditions of NaCl had the TS values that met the requirement of the JIS A 5908 standard (≤ 12%). The TS of untreated kenaf composite board was 7.66%. The TS values of the board made from untreated kenaf fiber was higher compared to those from treated kenaf fiber. The water molecules expand the board due to the weakening of interface adhesion and the result of the loss compatibility between natural material and matrices (Jamaludin et al., 2020). Decreasing of TS leads to an increase in dimensional stability (Hwang and Oh, 2020). The physical properties significantly improved by increasing concentration of NaCl and duration of fiber soaking. Therefore, the composite board made from treated kenaf presents a better performance in integration between fiber and resin.
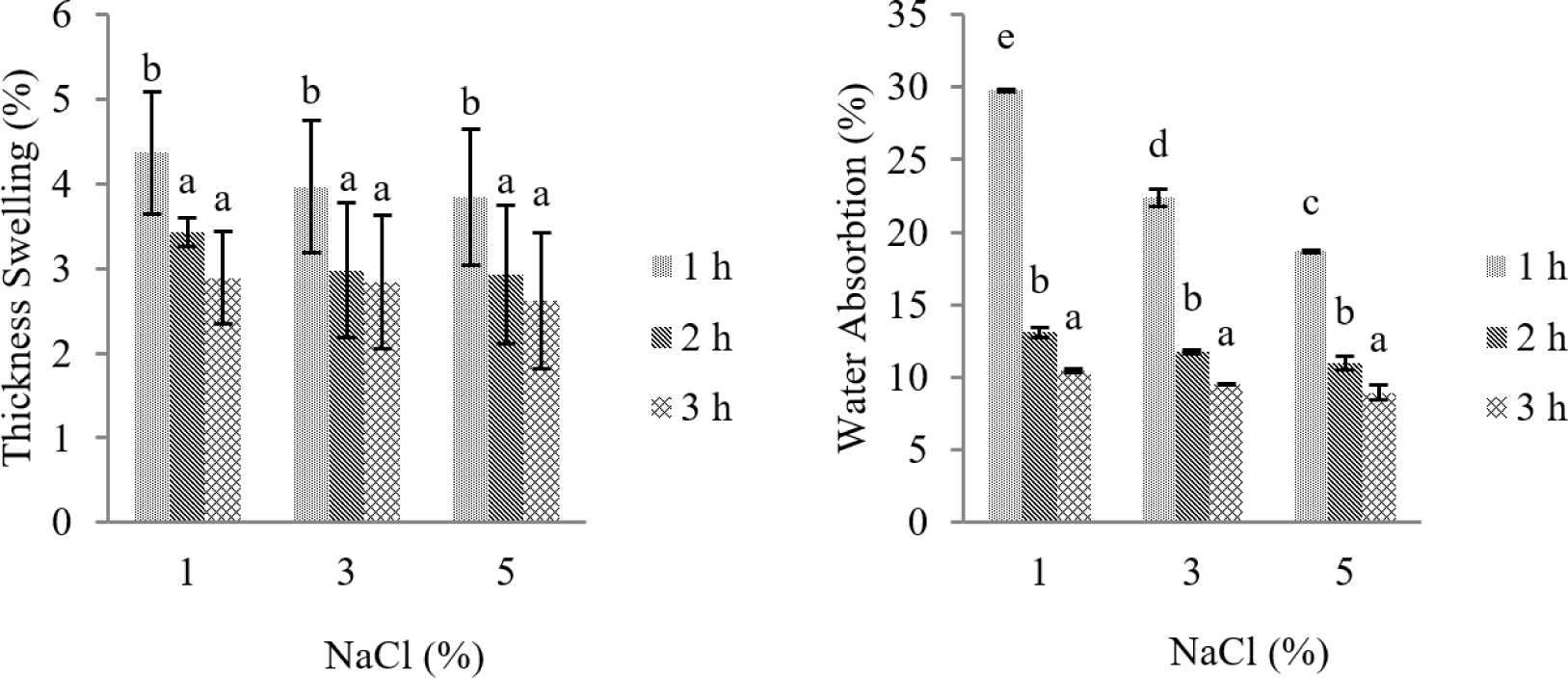
In contrast, the WA property of the board from NaCl treated fibers was decreased. The range of WA values of kenaf composite boards was between 10.9%–29.3% as shown in Fig. 4. The WA of NaCl treated kenaf composite boards decreased by increasing soaking time and level content of NaCl. NaCl treatment with the variation of concentration and soaking time manifested a positive effect on the WA. According to Khan and Khan (2015), the outer layer that consists of impurities molecules which contain group OH− were attracted by Na+ and different polarity bonded them to form ionic bonds. Furthermore, Na+ creates hydrophobic fiber to decrease WA (Hamidon et al., 2019).
In several studies, chemical treatment of fibers has a positive effect on WA and TS. Alkaline-treated banana fibers in a polyester banana fiber composite resulted in a 68% decrease in WA (Rai et al., 2011). An increase in moisture causes the fibers to swell, decreases its mechanical properties, provides the necessary conditions for biodegradation, and changes its dimensions. The penetration of moisture into the composite material occurs through three different mechanisms. The main process consists of the diffusion of water molecules within the micro-gaps between the polymer chains. Other mechanisms are capillary transport into the gaps and defects at the interface between the fiber and polymer due to wettability and incomplete impregnation, and transport by micro-cracks in the matrix, which are formed during the compounding process (Ramanaiah et al., 2012). The capillary mechanism involves the flow of water molecules into the interface between the fiber and the matrix. This is particularly significant when interfacial adhesion is weak and when fiber and matrix debonding has already begun (Ramanaiah et al., 2012).
4. CONCLUSIONS
The effects of NaCl treatment under different conditions on the properties of kenaf fiber composite were investigated. The IB, MOE, and MOR of kenaf fiber composite treated with NaCl solution increased and its TS and WA decreased. In addition, kenaf fibers treated with 5% NaCl for 3 h exhibited the highest mechanical properties. Nevertheless, the optimum condition of physical and mechanical properties was found on composite board with 1% NaCl treated kenaf fiber for 3 h. The NaCl treatment is an effective method for improving the mechanical properties to prepare high-performance natural fiber composite boards.