1. INTRODUCTION
Bamboo has been widely used as the material for industries in construction, furniture, household goods, musical instruments and handicrafts (Zhang et al., 2018). Recently, Shin et al. (2018) developed bamboo/PLA bio-composites for 3D printer filament. Galih et al. (2020) evaluated the possibility of cross-laminated timber (CLT) with bamboo laminated board as the core layer. However, bamboo is lignocellulosic material and rich in sugar and starch, which leads to its high moisture absorption and poor biological durability. Therefore, enhancing the durability of bamboo is needed (Yuan et al., 2020).
There are mainly two methods of modifying the bamboo, chemical and physical methods. The chemical methods generally include the addition of fungicides and flame retardants, while the physical methods include various types of heat treatments. Qi et al. (2019) investigated the effects of a novel mold inhibitor specially for bamboo on the properties of bamboo fiber-based composites (BFBCs). Kang et al. (2017) developed a new drying technology in order to quickly and massively dry bamboo tubes without crack and check. They impregnated bamboo tubes with the solution of PEG-1000 before high-temperature drying.
The culm of bamboo is covered by its hard epidermis with a wax-coated skin which has a function of preventing moisture loss from the bamboo (Ariffin and Sukri, 2019). Chang et al. (2015) found that giant bamboo (Dendrocalamus giganteus Munro) culm waxes are composed of saturated and unsaturated hydrocarbons, including alkanes, alcohols, ketones, aldehydes, fatty acids, and minor aromatic compounds. Therefore, several results have revealed that bamboo is difficult to treat with preservatives (Kamarudin and Sugiyanto, 2012). Moreover, environmental concerns are encouraging the search for new methods of preservation of bio-materials such as wood and bamboo. Thermal treatment has been investigated since the middle of 20th century for the purpose of avoiding toxic effects of chemical treatment which involves chemical substances. Shin et al. (2004) investigated physical and mechanical properties of Phyllostachys pubescens bamboo treated with hot water (95℃) and microwave irradiation (700 W). Maulana et al. (2017) evaluated the effects of steam treatment on physical and mechanical properties of bamboo oriented strand board.
High-temperature treatment of bamboo changes its structure and chemical composition because of decomposition of hemicelluloses, ramification of lignin, crystallization of cellulose, and removal of certain extractives. Thus, bamboo becomes less hygroscopic and these changes decrease water re-absorption, improve the dimensional stability, and increase weathering durability. Meng et al. (2016) investigated the effect of heat treatment (180℃ and 200℃) on the chemical composition of bamboo slivers. Their results showed a decrease in the content of holocellulose, as well as an increase in the contents of lignin and extractives.
Color is an attribute of visual perception, which can be one of the important factors that influence customers when choosing bamboo and wood products. Color preferences survey conducted by Hidayat et al. (2017) revealed that their respondents expressed a stronger preference for the darker color of heat-treated woods than the original wood color. Thermal treatment is also a suitable method for color homogenization and colorization (Varga and Van Der Zee, 2008). Zhang et al. (2013) found that the color of bamboo was darkened and all three color parameters (L*a*b*) were significantly changed after the heat treatments at seven temperature levels (100 ~ 220℃) for four duration times (1 ~ 4 hours).
In this study heat treatment was performed under different temperatures and duration times to investigate the color changes on the outer surfaces of bamboo. To determine optimum conditions of heat treatment for the color desired, the method to predict the color change of bamboo surface after the heat treatment was developed. The results are expected to be able to provide valuable information for increasing the added value of domestic bamboo products.
2. MATERIALS and METHODS
The culms of Phyllostachys bambusoides bamboo used for this study were collected around Damyang-gun, Jeollanam-do, Republic of Korea. Bamboo species was verified according to the producer information. The bamboo culms were cut into 15 cm-long cylindrical specimens with no node on both ends. One hundred specimens were selected and the average circumference, thickness and moisture content of these specimens were 76.64 mm, 5.54 mm and 80.4%d.b., respectively.
These specimens were immersed into plastic tub filled with tap-water, where they remained for ten days. The tap-water was changed each day to avoid attacks from bacteria and the fermentation of the material. This water immersion was performed to extract starch from specimens, making them less susceptible to biological attacks and discoloration. The specimens extracted by water were exposed to the open air over seventeen days to dry. Average moisture content of air-dried specimens was 26.3%d.b..
All the samples were oven-dried at 105℃ before the heat treatment. Out of all one hundred specimens, thirty-six specimens with similar sizes and weights were selected for heat treatment test. The specimens were thermally treated at three temperature levels (180, 200 and 220℃) with three duration times (60, 90 and 120 min.) for each assay.
For the torrefaction of biomass, a severity factor (SF) is used to integrate the effects of reaction times and temperatures into a single variable (Lee et al., 2012). The SF used in this study is defined as the following equation:
where SF is the severity factor, the heat treatment time in minutes,
the heat treatment temperature in ℃, and
the reference temperature (= 100℃). The severity factors applied in this study were calculated as Table 1.
Temperature | Heat treatment time | |||
---|---|---|---|---|
30 min. | 60 min. | 90 min. | 120 min. | |
180℃ | 3.83 | 4.13 | 4.31 | 4.43 |
200℃ | 4.42 | 4.72 | 4.90 | 5.02 |
220℃ | 5.01 | 5.31 | 5.49 | 5.61 |
Three specimens for each assay were put into the forced convection drying oven (HB-502M, Han Baek Scientific Co.). In the preliminary tests, it was recognized that rapid cooling after heat treatment induced severe cracks on bamboo. Bamboo undergoes the thermal expansion during the heat treatment. And rapid cooling of this heat treated bamboo induces rapid shrinkage and stress. Therefore, the stepwise heat treatment schedule was adapted to minimize these thermal stresses in specimens (Fig. 1). In the preheating stage oven temperature was set at 100℃ and a temperature of 100℃ was maintained for 30 min. Then the oven temperature was increased to 150℃ and was maintained at 150℃ for 30 min. In the heat treatment stage oven temperature was set at each heat treatment temperature and this temperature was maintained for each heat treatment duration time. After the heat treatment stage was finished, cooling stage was started. Oven temperature was lowered to 150℃ and 100℃ in sequence and each set temperature was maintained for 30 min., respectively. Finally, heater of oven was turned-off, while fan was running until the oven temperature reached room temperature.
The surface color changes of specimens due to drying and heat treatment were measured by a portable colorimeter (NR100, 3nh) fitted with a measuring aperture diameter of 8 mm. The CIE ,
and
color parameters (according to the international Commission on Illumination) of the specimens were obtained directly from the colorimeter and were used for color evaluation. Three positions on the outer surface of each specimen were selected and marked with a circle of diameter of 12 mm to measure the color changes at each identical position. The overall color changes (
) of the specimens were calculated according to the following equation:
where is the overall color change and
,
and
represent the changes in
,
and
of specimens, respectively. A lower
means lower color change.
3. RESULTS and DISCUSSION
Table 2 shows the surface color changes of bamboo due to air- and oven-drying. All the three color parameters, ,
and
, increased as bamboo dried. Dark green surface color of green bamboo turned into light green color after air-drying, and then into yellow color after oven-drying at 105℃. As bamboo dried, lightness (
) increased gradually. Besides, the bamboo surface showed a tendency to turn reddish and yellowish by increases in chromaticity parameters
and
. Color parameter
was kept lower than 0 value after air-drying. This means green color of bamboo surface was maintained even after the air drying indoor. However, after oven-drying color parameter
exceeded over 0 value, and the color of bamboo surface lost green color completely. Overall color changes
of air-dried bamboo surface due to oven-drying was 13.62, which was much higher than that of green bamboo surface due to air-drying, 1.97. In the meantime wax layers on the bamboo outer surfaces melted and became sticky during oven-drying. After cooling these melted wax layers were hardened again and shiny outer surfaces appeared.
Color parameters |
![]() |
![]() |
![]() |
![]() |
---|---|---|---|---|
Green | 43.00 | -5.70 | 17.50 | - |
Air-dried | 44.70 | -4.90 | 18.10 | 1.97 |
Oven-dried | 45.80 | 8.10 | 22.00 | 13.62 |
Fig. 2 demonstrates that surface color of oven-dried bamboo gets darker as heat treatment temperature increases. All the average color parameters ,
and
decreased as heat treatment temperature increased, except at 180℃ for 60min. As expected, the average overall color changes
increased as severity factor increased (Table 3). This results are in a good agreement with the findings of Lee et al. (2018), who observed that all the color parameters decreased as heat treatment temperature increased when they treated moso bamboo at 150 ~ 210℃ for 1 ~ 2 hours.
According to the measured (lightness coordinate) values of the bamboo specimens, the heat treatment was decreasing the
as the severity factor increased, indicating the bamboo has a tendency to change to darker colors due to the severer heat treatment. Schulz et al. (2021) suggested that the well-known darkening of the wood color due to thermal treatments is related to the thermal degradation in hemicellulose and cellulose, which normally reflect visible light with high wave numbers, leading to a perception of a light color.
The measured (yellow/blue coordinate) values of the bamboo specimens implied that the heat treatment caused
value reduction, indicating the surface color of the bamboo tended to change from yellow to blue color.
The results also indicate minor increase of the (red/green coordinate) values when the duration time increased at the heat treatment temperature of 180℃, but decreases occurred when the temperatures and duration times for heat treatment increased further. Zhang et al. (2021) presented the oxidation of phenolic compounds, the presence of reduced sugars and amino acids or the caramelization of holocelluse components as the main causes of color changes of bamboo with the increasing of the temperature.
Table 4 shows the average weight losses induced by heat treatment. At the heat treatment temperature of 180℃, weight loss rates did not exceed 1%. However, as the severity factor increased weight loss rates increased. Specimens lost 9.1% of oven-dry weight by heat treatment at 220℃ for 120min.
As mentioned previously, all the three color parameters ,
and
decreased as the severity factor increased. Therefore, it is expected to pre-estimate the final surface color of bamboo after heat treatment with a certain severity factor. However, the integration of three color parameters into one parameter is needed to simplify the pre-estimation process. Fig. 3 shows the values of
×
×
were highly related to severity factor as the following regression equation (R2 = 0.9976).
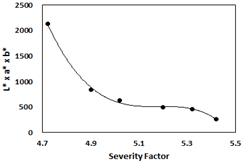



where means the value of
×
×
and
means severity factor, respectively.
It would be possible to pre-determine the optimal conditions of heat treatment for the desired bamboo surface color after heat treatment if that color could be pre-estimated. In this study the algorithm was developed to pre-determine the optimal duration time at a certain temperature for heat treatment as Fig. 4. Firstly, the desired values of the three color parameters ,
and
for the surface color of bamboo after heat treatment are determined respectively. Then, the desired value of
×
×
is calculated to estimate the severity factor for this color using equation (3). Finally, the optimal duration time are estimated using equation (1) after selecting the temperature for this heat treatment process. Table 5 shows the results estimated for the heat treatment temperature of 200℃.



![]() ![]() ![]() |
Severity factor | Duration time (min.) |
---|---|---|
900 | 4.898 | 90 |
800 | 4.925 | 96 |
700 | 4.960 | 104 |
600 | 5.010 | 116 |
500 | 5.285 | 219 |
400 | 5.369 | 266 |
300 | 5.410 | 292 |
200 | 5.440 | 313 |
100 | 5.464 | 331 |
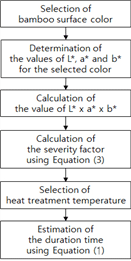
There were various contradictory reports on the resistance of weathering of heat-treated wood, and other reports proclaimed the necessity of painting with UV resistance (Kim, 2018). Therefore, more advanced studies are necessary to develope the methods for maintaining the color of heat-treated bamboo.
4. CONCLUSION
Heat treatment tests were conducted to investigate the effects of temperature (180, 200 and 220℃) and duration time (60, 90 and 120 min.) on the change of the surface color of Phyllostachys bambusoides bamboo. All the three average color parameters ,
and
decreased and the average overall color changes
increased as the severity factor increased. Through the analysis of the results the algorithm was developed to estimate the optimal duration time for the desired bamboo surface color at a certain heat treatment temperature.