1. INTRODUCTION
In general, ceramics are sintered bodies, such as pottery or porcelain that are made of clay or minerals, while a broader definition includes inorganic materials with ionic and covalent bonds. According to this, carbon is certainly included in the category of ceramics. Therefore, porous carbon materials obtained by carbonizing composite materials, such as wood and thermosetting resin or ceramics obtained from wood, were named “wood ceramics” (Okabe, 1996).
Various studies on the manufacturing of ceramics have been conducted since Okabe and Saito (1995) developed a new porous carbon material by impregnating a wooden material with phenolic resin and thermoforming it in a vacuum (Hirose et al., 2002; Iizuka et al., 1999; Zhao et al., 2002). The physical properties of wood ceramics vary depending on the type of raw material, impregnation rate of the thermosetting resin, and manufacturing conditions such as carbonization temperature and rate of temperature increase. Especially, resin impregnation rate and carbonization temperature are known to greatly affect the density of wood ceramics (Hirose et al., 2002; Oh et al., 2004, 2010).
Meanwhile, the insufficiency of wood resources led to the research on using nonwood resources for board manufacturing and ceramicization, and one prominent example of such research involved the development of a new material using a mixture of rice husk and lignocellulosic materials (Lee and Han, 2000; Lee, 1999; Oh and Byeon, 2005; Hwang and Oh, 2020a). Research was also conducted on utilizing various byproducts and wastes (Hwang and Oh, 2019; Hwang and Oh, 2020b; Ju and Roh, 2019; Ju and Roh, 2020).
Among them, Miscanthus sinensis var. purpurascens is a lignocellulosic material with a high porosity and low specific gravity, and being a renewable resource like wood, it can be used as a highly valuable resource in terms of resource use and circulation. In addition, the M. sinensis var. purpurascens boards produced with liquid phenolic resin had similar flexural strength but superior peel strength when compared to the boards made of powdery phenolic resin (Oh et al., 2012). Because of these advantages, the effective use of M. sinensis var. purpurascens is being actively studied (Kim et al., 2012; Oh et al., 2012; Park et al., 2012; Oh et al., 2014).
In this context, this study used M. sinensis var. purpurascens, which could be a valuable resource for realizing green growth in the 21st century, in manufacturing particle boards. The boards were then impregnated at various ratios and carbonized at a constant temperature for each resin impregnation rate for ceramicization, after which their density and mechanical properties were examined.
2. MATERIALS and METHODS
M. sinensis var. purpurascens used to manufacture the boards was obtained from the Bioenergy Crop Center, National Institute of Crop Science, Rural Development Administration located at Muan, Jeollanam-do, Korea. To ensure uniformity of samples, particle size was selected from 10 mesh to 20 mesh and moisture content was adjusted to 7% or less, as shown in Fig. 1.
Powdered phenolic resin (KNB-100PL from Kolon Chemicals Co., Ltd.) was used for manufacturing M. sinensis var. purpurascens board, and liquid phenolic resin (KPD-L777 from Kolon Chemicals Co., Ltd.) was used for impregnation. Table 1 shows the characteristics of each resin.
The manufacturing process for the boards is as follows. The powdered phenolic resin was sufficiently mixed with the uniformly selected M. sinensis var. purpurascens particles, and the mixture was then put into a stainless square mold on the heating plate of the hot press, where the height of the top part of the sample was adjusted to be even. Then, a board with the dimensions of 26 cm × 26 cm × 1.4 cm was produced by hot press molding. In terms of manufacturing conditions for the board, the density was set to be 600 kg/m3 and amount of added adhesive was fixed at 10%. The hot press temperature was 190℃, pressing pressure was 3.9 MPa → 2.9 MPa → 1.9 MPa (3-stage pressing), and pressing time was 3 min → 2 min → 1 min (3-stage pressing time). A stopper (distance bar) was used to keep the thickness of the board constant during the hot pressing process, and a Teflon plate was used to prevent the attachment of the top and bottom of the board to the hot plate by heat.
The M. sinensis var. purpurascens boards were cut to the size of 12 cm × 12 cm × 1.4 cm, put in a pressure-reducing impregnation device containing liquid phenolic resin (KPD-L777 from Kolon Chemicals Co., Ltd.), and impregnated at 1 atm with impregnation rates of 30 ± 2%, 40 ± 2%, 50 ± 2%, and 60 ± 2%. After impregnation, the samples were placed in a dryer to be dried and cured for 10 h at 60℃, and at 100℃ and 135℃ for 8 h each. After drying, the ceramics were produced via carbonization at a carbonization temperature of 800℃ using a vacuum carbonization furnace (KOVAC KSF-200V from Korea Vacuum Co., Ltd.). At this time, the rate of temperature increase was 4℃/min, and the temperature was maintained at the target temperature for 2 h before cooling down. Fig. 2 shows pictures of the finished boards and ceramics.
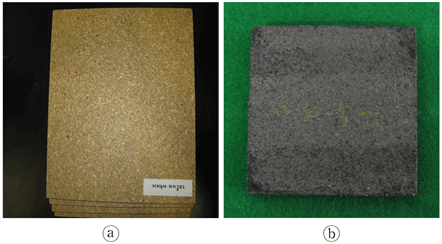
For flexural strength performance test, the specimen was cut in 110 mm × 10 mm × 10 mm and humidified in a thermo-hygrostat (temperature at 20 ± 1℃, humidity at 65 ± 5%), after which we selected 10 pieces for each test condition of the flexural strength performance test. The flexural strength test was performed by using a universal strength tester (model TSU-2 from TAESHIN) at the loading rate of 0.5 mm/min to measure the flexural modulus and flexural strength in compliance with the KS F 2208 standard. For the Brinell hardness test followed the KS F 2212 standard by using a universal strength tester in pressing a 10 mm-diameter iron bead into three points on the surface of the samples of wood ceramics with the size of 40 mm × 40 mm × 10 mm at the loading rate of 0.5 mm and pressing depth of 1/πmm. In accordance with the KS F 2206 standard, the compressive strength test was performed on a 30 mm × 10 mm × 10 mm specimen at a loading rate of 0.5 mm/min using a universal strength tester.
3. RESULTS and DISCUSSION
As for the densities of the resin-impregnated ceramics boards with resin impregnation rates of 30 ± 2%, 40 ± 2%, 50 ± 2%, and 60 ± 2% before carbonization which then went through carbonization at 800℃, Table 2 and Fig. 3 show them to be 558.57, 617.08, 627.10, and 649.10 kg/m3, respectively. This indicates that the density after carbonization increased as the resin impregnation rate increased at the fixed carbonization temperature.
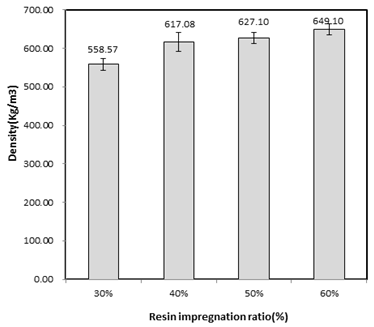
Oh and Piao (2004) also reported that when the resin impregnation rate before carbonization of the board made of thinned logs was 40%, the density values of wood ceramics of Pinus densiflora, Larix kaempferi, and Pinus koraiensis were 760, 730, and 750 kg/m3, respectively. When the resin impregnation rate before carbonization was higher (at 80%), the densities of wood ceramics made from thinned logs of Pinus densiflora and Larix kaempferi were higher at 830 and 840 kg/m3, respectively, thus showing a similar trend to the results of this study. In addition, it was also reported that the density tended to increase following the increase in the resin impregnation rate in the manufacture of wood ceramics using medium-density fiberboard (MDF) made from Pinus radiata (Oh and Byeon, 2002; Oh, 2005). The positive correlation between the resin impregnation rate before carbonization and the density of wood ceramics thereafter is believed to be stemming from the fact that the large amount of resin impregnated in the cell walls is converted into vitreous carbon during the carbonization process to strengthen the cell walls, thus resulting in the density increase (Okabe and Saito, 1995).
Table 2 and Fig. 4 show the flexural strength values depending on the resin impregnation rate of ceramics carbonized at 800℃ carbonization temperature. When the resin impregnation rate was 30 ± 2%, 40 ± 2%, 50 ± 2%, and 60 ± 2% at the carbonization temperature of 800℃, the flexural strength values were 2.76, 3.25, 3.30, and 3.74 MPa, respectively, indicating that the flexural strength tended to increase almost linearly as the resin impregnation rate increased, similar to the trend in density.
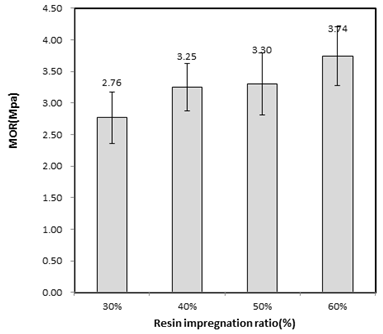
This trend is consistent with the previous reports that the flexural strength increased linearly as the resin impregnation rate increased even in the manufacture of wood ceramics using MDF made from Pinus radiata (Oh and Byeon, 2002; Oh, 2005). In addition, there was a difference in the resin impregnation rate and carbonization temperature conditions depending on the density of the tree species. The flexural strengths of Pinus radiata at the carbonization temperature of 600℃ under the similar resin impregnation rate conditions of 40%, 60%, and 80% were 6.96 MPa, 8.04 MPa, 13.44 Mpa, respectively, and these values were higher than those of this study with M. sinensis var. purpurascens particles.
Moreover, Oh and Byeon (2005) reported that when the phenolic resin impregnation rates were 40%, 50%, 60%, and 70% at the carbonization temperature was 600℃ for the mixed ceramics made of sawdust and rice husk, their flexural strength values were 4.70, 4.90, 5.98, and 6.08 Mpa, respectively, which were slightly higher than the values of the ceramics in the current study. These results were interpreted as the effect of insufficient bonding strength due to the nonuniform structure of rice husks and particles during the carbonization process, and a similar reason could be behind the low strength value of the ceramics in this study.
Table 2 and Fig. 5 show the flexural modulus values depending on the resin impregnation rate of ceramics carbonized at 800℃. The resin impregnation rates of 30 ± 2%, 40 ± 2%, 50 ± 2%, and 60 ± 2% resulted in the flexural modulus of 1.21, 1.63, 1.66, and 1.82 GPa, respectively. The flexural modulus values in this study were lower than the values reported for the thinned logs of Pinus densiflora, Pinus koraiensis, and Larix kaempferi reported in Byeon et al. (2004), which were approximately 2.64 GPa − 7.85 GPa. This difference is believed to be caused by the difference in the characteristics of raw materials.
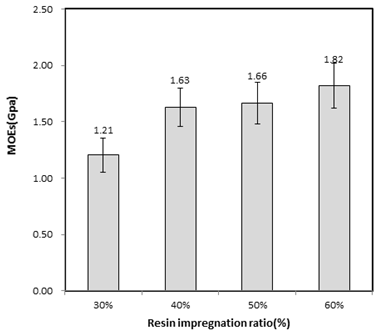
Table 2 and Fig. 6 show the values of compressive strength depending on the resin impregnation rate of ceramics carbonized at 800℃. When the resin impregnation rates were 30 ± 2%, 40 ± 2%, 50 ± 2%, and 60 ± 2% at the carbonization temperature of 800℃, the compressive strength values were 3.44, 5.09, 6.73, and 8.65 MPa, respectively, showing that the compressive strength increased as the amount of impregnation increased. Byeon et al. (2004) also reported that the compressive strength of wood-ceramics manufactured at 70% resin impregnation rate and 600℃ carbonization temperature using thinned logs of Pinus densiflora, Pinus koraiensis, and Larix kaempferi were 3.24, 7.15, and 4.12 MPa, respectively, which were lower than the values found in this study.
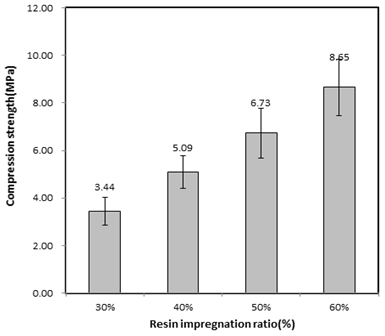
Table 2 and Fig. 7 show the Brinell hardness values depending on the resin impregnation rate at the carbonization temperature of 800℃. The resin impregnation rates of 30 ± 2%, 40 ± 2%, 50 ± 2%, and 60 ± 2% at the carbonization temperature of 800℃ resulted in the Brinell hardness values of 5.11, 7.15, 6.85, and 7.55 MPa, respectively, showing that the hardness also increased as the amount of impregnation increased.
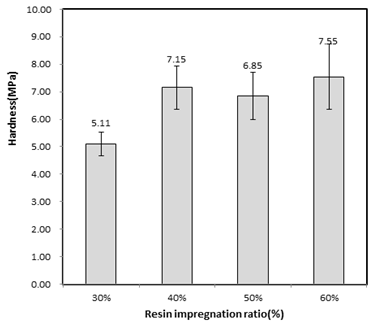
Byeon et al. (2004) showed that the hardness values of phenolic resin-impregnated wood-ceramics manufactured with thinned logs of Pinus densiflora, Larix kaempferi, and Pinus koraiensis with carbonization temperature of 600℃ were 15.59, 11.86, and 16.76 MPa, respectively, showing greater hardness values than those found in this study. It is surmised that this is because the resin injected into the raw materials has a weaker penetration into the nonwood material of M. sinensis var. purpurascens when compared to wood with more air gaps.
4. CONCLUSION
In order to find a way to utilize M. sinensis var. purpurascens in the waterfront area, this study manufactured boards with M. sinensis var. purpurascens particles, impregnated them with resin, and then carbonized them to produce ceramics, after which their density and mechanical properties were examined for each resin impregnation rate.
1) The density increased from 558.57 kg/m3 to 649.10 kg/m3 as the resin impregnation rate increased from 30 ± 2% to 60 ± 2% when carbonized at the carbonization temperature of 800℃.
2) Flexural strength performance, Brinell hardness, and compressive strength increased almost linearly as the resin impregnation rate increased at the same carbonization temperature, indicating that the resin impregnation rate had a significant impact on the mechanical properties of the ceramics made of M. sinensis var. purpurascens.
The wood-ceramics produced in this study showed lower strength than that of the wood-ceramics produced from Pinus densiflora, Pinus koraiensis, and Larix kaempferi. It appears that additional research would be required to improve upon this part, such as those on the manufacture of wood ceramics using a mixture of M. sinensis var. purpurascens and lignocellulosic. There is also a need for further research on deodorization rate, hygroscopicity, and other functional performances for the utilization of M. sinensis var. purpurascens ceramics.