1. INTRODUCTION
Wood has an aesthetic pattern as well as the advantage of being easily processed into various shapes. Due to these characteristics, the use of wood is increasing in interior and exterior materials for buildings and furniture (Park et al., 2005). However, as wood is vulnerable to fire, it is necessary to develop effective flame retardants to reduce human and material damage caused by fire (Park et al., 2019; Kim et al., 2002).
Flame retardants are used in manufacturing of almost all industrial products and there are a wide variety of the retardants depending on its usage (Shin and Baek, 2013). The halogenated flame retardant contains a halogen element, and the highest flame retardancy is found in the order of fluorine (F) < chlorine (Cl) < bromine (Br) < iodine (I) (Cha et al., 2011). Fluorinated flame retardants are not practically used, and as iodinated flame retardants have a disadvantage in that the bond strength between iodine and carbon is too weak that the bond is broken even by low energy, in which leads to loss of the flame retardancy at a temperature below the pyrolysis temperature. With this reason, chlorinated and brominated flame retardants are mainly used among halogenated flame retardants. In particular, the brominated flame retardants are widely used around the world due to their high retardancy and low cost (Cho et al., 2002; Lee et al., 2007; Shin et al., 2009). Although the consumption amount of the halogenated flame retardants centered on the brominated flame retardant has continuously increased it was claimed that dioxin is generated during combustion of halogenated flame retarding materials and polymers in Germany. As a result, due to the concerns on the environmental problems, the use of the halogenated flame retardants that emit harmful HCl and HBr gases started to be regulated mostly in developed European countries (Jang and Choi, 2009). Phosphorus flame retardants mainly affect the reaction occurring in the condensed phase, and they are particularly effective for plastics containing oxygen or materials with a high oxygen content such as cellulose and cellulose substituents (Cha et al., 2011). Since inorganic compounds are generally inactive at 150~400 °C, which is a typical pyrolysis temperature for plastics, those that can be used as flame retardants are extremely limited (Choi et al., 2018). However, some inorganic compounds show flame retarding effect when mixed with halogenated flame retardants. For example, inorganic flame retardants containing aluminum hydroxide (Al(OH)3) and boron (B) are most widely used because they affect the combustion reaction through physical processes (Cha et al., 2011). Thus, in this study, we used inorganic compounds as an additive in a basic study for developing eco-friendly flame retardants and examined the flame retardancy.
Sodium silicate is one of the most useful inorganic compounds and it belongs to soluble silicates which are also known as water glass (Medina and Schledjewski, 2009). In general, sodium silicate is a viscous liquid which is composed of 21~34% of SiO2 and 6~18% of NaO2. It has been used for a long time in various materials such as paper, wood, and cement to give fire resistance (Medina and Schledjewski, 2009; Lee and Thole, 2018). In particular, water glass is known as an effective material that can improve durability and flame retardancy in the field of fire retardants (Lee and Thole, 2018) and has been applied to noncombustible coatings and paints (Pereyra and Giudice, 2009; Son et al., 2013). Various studies have been conducted previously to improve the bond strength and flame retardancy of sodium silicate. It was revealed that acidic sodium silicate mixed with sulfuric acid, acetic acid (Stark and Wicht, 1998), and boric acid (Obut and Girgin, 2006) can improve the stability of siloxane bonds. Moreover, it was reported that sodium silicate and boron compounds are effective in increasing biological resistance and fire resistance (Furuno and Imamura, 1998; Yamaguchi, 2005).
Therefore, in this study, we analyzed the flame retardancy based on the concentration of water glass and type and ratio of additives in the flame retardant by 45° MecKel’s Burner method, as the basic data for improving the flame retardancy using water glass as the main component for a wood flame retardant.
2. MATERIALS and METHOD
To test the flame retardancy based on the concentration of water glass and additives, we used plywood that satisfies the standards of flame retardant performance of National Fire Agency (NFA). The test specimen was prepared with a 190 mm width × 290 mm length × 5 mm thickness as presented by 45° Meckel’s Burner method in the standards of flame retardant performance (NFA Notification No. 2019-2; Korean National Fire Agency, 2019). To measure the flame retardant performance based on the concentration of water glass, water glass of 20, 30, 40, and 50% concentration was used. To measure the flame retardant performance based on the additives, potassium hydroxide (KOH), aluminum hydroxide (Al(OH)3), and magnesium sulfate (MgSO4) were used as additives. The test specimen and nontreated control specimen were prepared in a quantity that can be used in 3 repeated experiments for each water glass concentration and additive. Based on the standards of flame retardant performance, the prepared test specimen was subjected to go through humidity controlling for 24 hours in a thermo-hygrostat with a temperature of 23 °C and humidity of 50% until it reached a constant weight. Then, it was stored in a desiccator with silica gel for 2 hours and used for the experiment. Table 1 shows the concentration and the content of additives for each treatment of the test specimen used in the experiment.
Test specimens were treated with water glass and three additives (KOH, Al(OH)3, MgSO4). The treated amount, treatment method, and number of treatments of flame retardants were determined based on the results of the previous study on commercial flame retardants (Seo et al., 2017). The amount of water glass was determined to be 500 g/m2. For the treatment method, flame retardants were applied to the test specimens with a brush until the surface of the test specimen was sufficiently wet, then it was dried for 24 hours at a temperature of 23 °C and humidity of 50%. The flame retardant was applied again, and the same process was repeated for 3 times. To analyze the flame retardant performance based on the additives, the concentration of water glass was fixed and the concentration of each additive was determined as follows: 5, 10, and 15% for KOH, 1, 2, 5 and 10 % for Al(OH)3, 0.5 and 1% for MgSO4.
For the evaluation of flame retardant performance, 45° Meckel’s Burner method presented in the standards of flame retardant performance (NFA Notification No. 2019-2) of Article 20, Paragraph 2 of 「Enforcement Decree of the Act on Fire Prevention and Installation, Maintenance, and Safety Control of Fire-Fighting Systems」 was applied. For the fuel used in combustion, butane gas presented in KS M 2150 (Liquefied petroleum gas; Korean Agency for Technology and Standards, 2017) was used. The test specimen was fixed to the pedestal in the 45° flammability tester, and the flame of the heating device with a length of 65 mm was set to be in contact with the lower part of the center of the test specimen. The heat treatment was proceeded with on each test specimen for 2 minutes, and for the test specimen complexed during the heating process, the heating device was removed 2 second after the complexation occurred. For each test specimen, flame retardant performance was measured in terms of afterglow time (s), after-flame time (s), char length (mm), and char area (mm2).
3. RESULTS and DISCUSSION
Table 2 and Fig. 1 show the results of measuring the afterglow time, after-flame time, char length, and char area based on the concentration of the water glass treated on the plywood using 45° Meckel method.
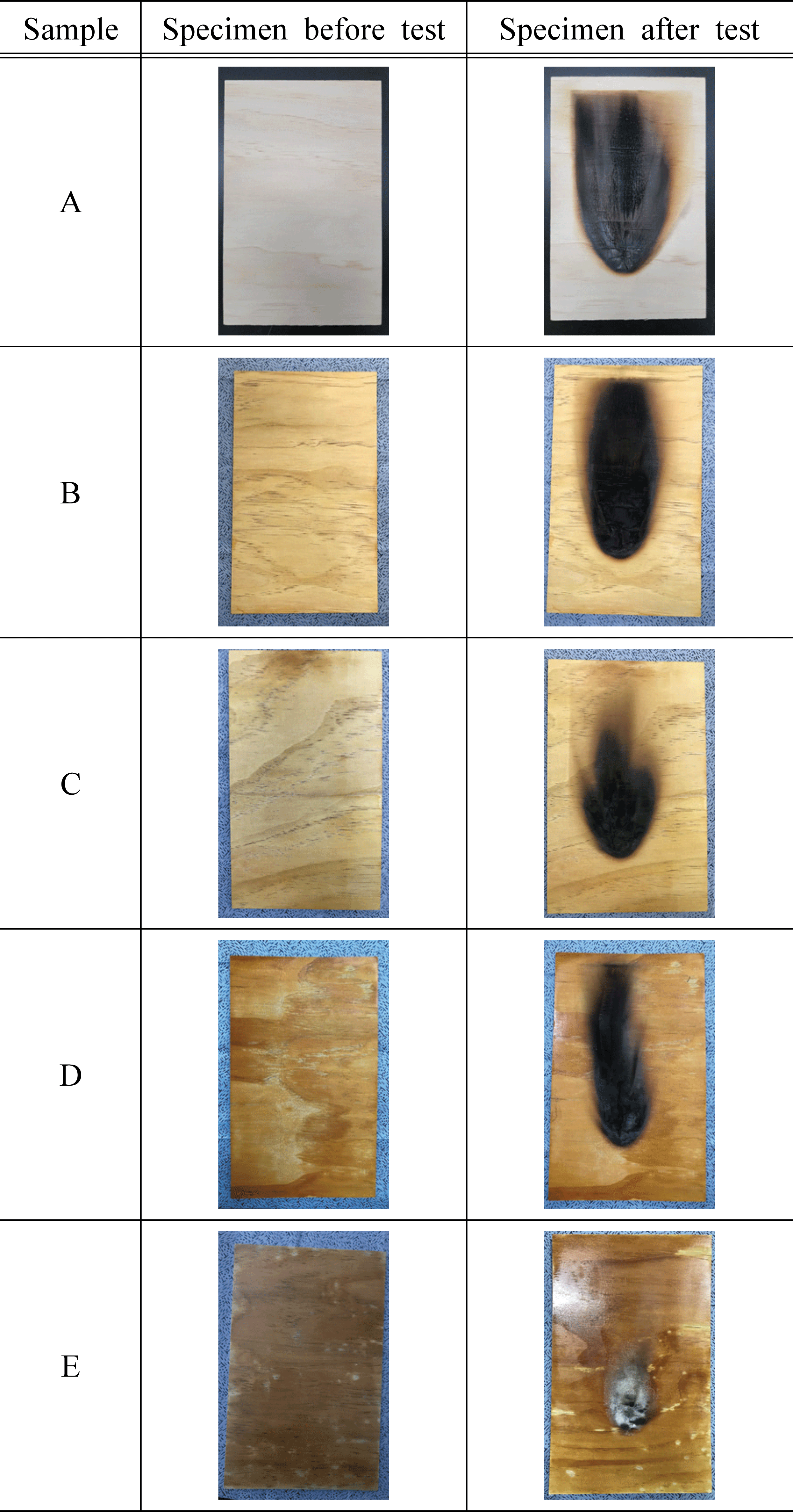
Afterglow and after-flame time were all measured as 0 second regardless of presence of the flame retardant, which satisfied the standard of flame retardant performance. However, as the generation of toxic gases may become a bigger problem than the continuous combustion in the event of a fire (White, 2000), it is considered that a further research on this subject is necessary to be conducted (Kim and Lee, 2016).
The char length of the test specimen without water glass treatment was measured as 201 mm, which did not satisfy the standard of 200 mm. On the other hand, the char length of the test specimen with water glass treatment was measured in the range of 70~189 mm, which satisfied the standard of flame retardant performance. The char areas of the test specimen without water glass treatment and the test specimen treated with water glass concentration of 20~40 % were measured in the range of 8,590~16,524 mm2, which did not satisfy the standard of 5,000 mm2. In contrast, in the case of the test specimen treated with 50 % water glass, the char area was measured as 2,589 mm2, and it satisfied the standard. These results indicate that the flame retardant performance improves as the concentration of glass water increases, showing a similar trend to the previous study (Lee and Thole, 2018) which reported that the carbonization rate of a particle board decreased as the water glass concentration increased. Meanwhile, Seekamp (1954) claimed that such tendency is due to the inorganic polymer of the water glass, and thus, we assumed that the polymerization of inorganic compounds in glass water was also applied in this study as well. The char length and char area of the test specimens varied according to the concentration of water glass. As the concentration of water glass increased from 20 % to 50 %, the char length and char area decreased from 201 mm and 16,524 mm2 to 70 mm and 2,589 mm2, respectively. In particular, when the water glass concentration was 40%, the char length and char area were 117 mm and 5,151 mm2, respectively, which did not satisfy the standard of flame retardant performance. However, those of the test specimen with 50 % glass water were greatly reduced to 70 mm and 2,589 mm2, and it satisfied the standard. That is, the flame retardant performance was largely improved as the concentration of water glass increased from 40 % to 50 %, suggesting that more detailed studies on water glass concentration (e.g., 40, 42, 44, 46, 48 %) would be needed in the future.
In other words, increased water glass concentration led to the decreased char length and char area, which improved the flame retardant performance. However, stickiness and efflorescence occurred at 40 and 50% water glass concentrations, which lowered process-ability and aesthetic effect of wood. It was reported that the efflorescence may occur by the influence of free alkali in the specimen if alkali is added at a concentration above the appropriate range (Oh et al., 2014). It was also reported that the stickiness occurs when water in water glass evaporates, which increases the viscosity and aggregates particles (Huusmann, 2001). Considering these results from the previous studies, we determined that the water glass concentration of 30% is appropriate in this study and additionally evaluated the flame retardant performance using various additives to improve the performance.
Based on the standard of flame retardant performance of NFA Notification No. 2019-2, we used 45° Meckel burner method to measure afterglow time, after- flame time, char length, and char area based on additives, and the results are shown in Table 3 and Fig. 2~4.
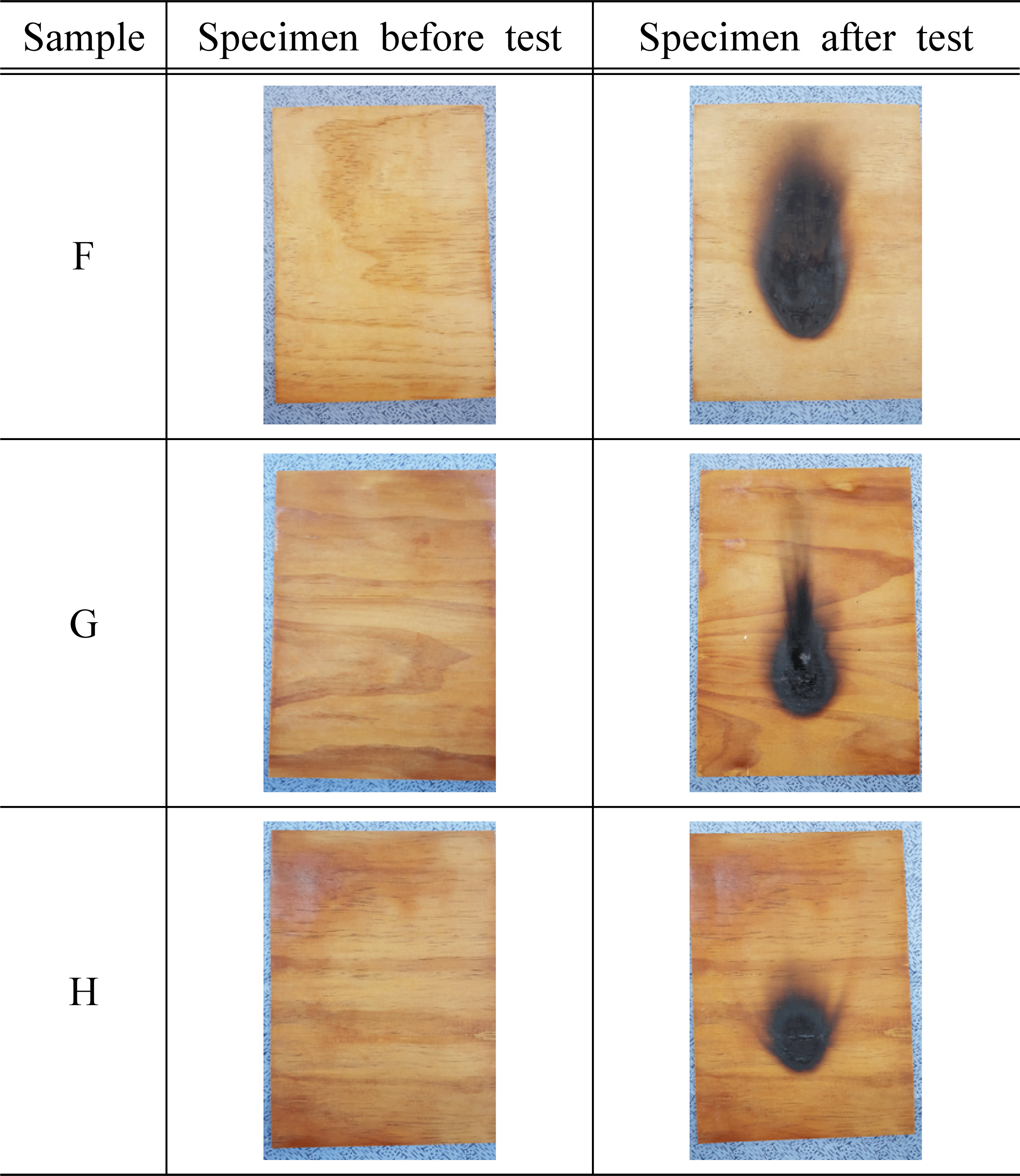
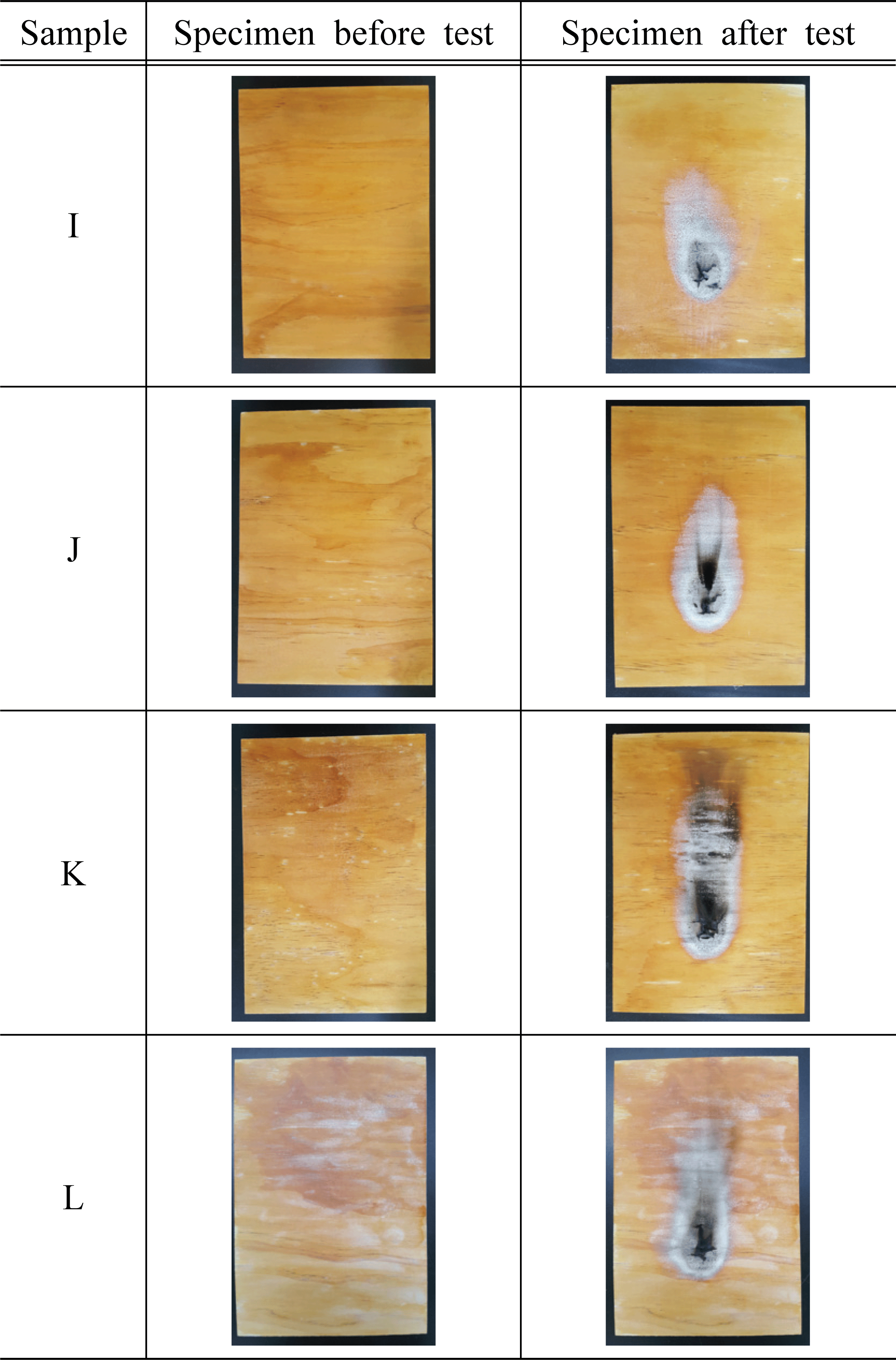
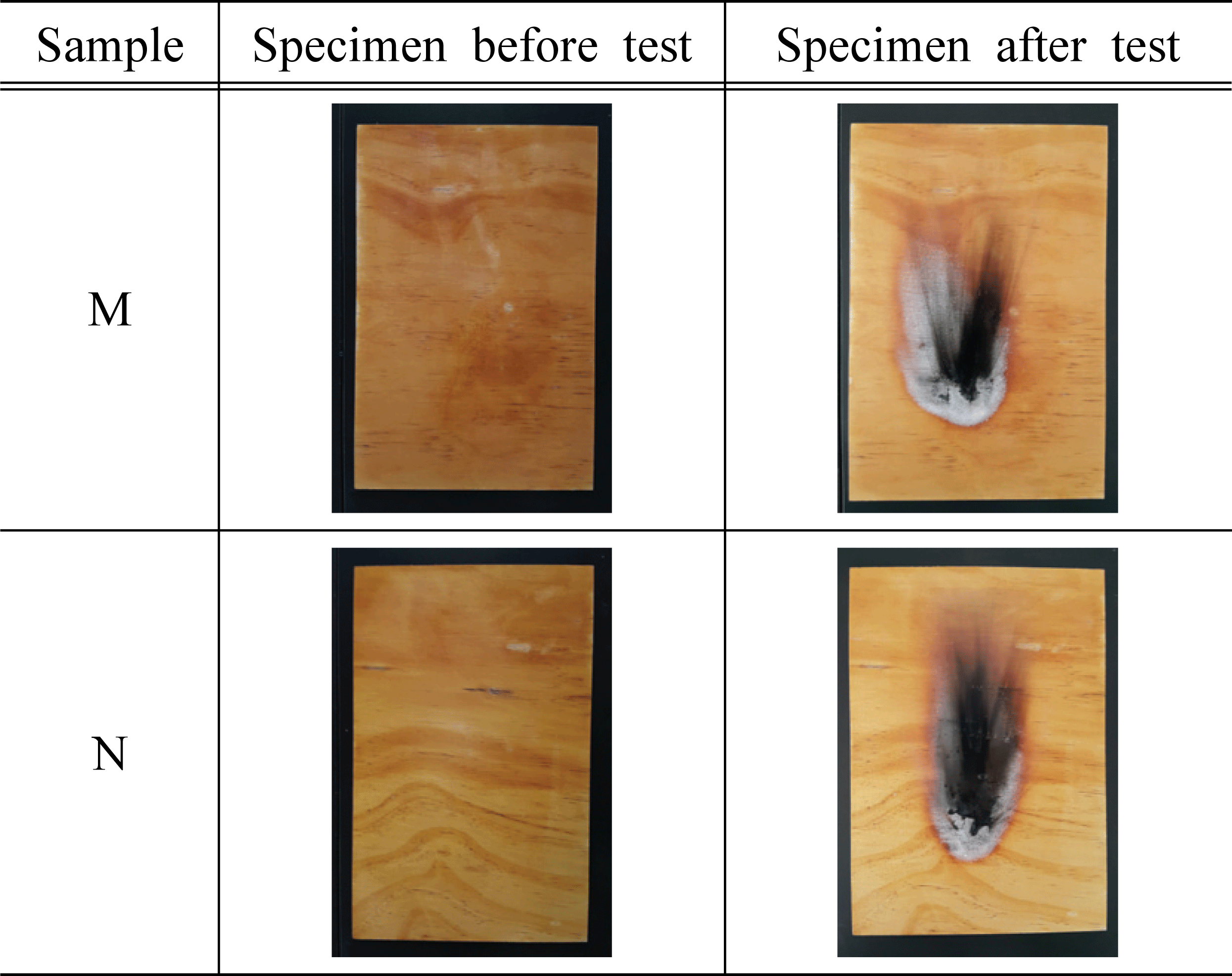
As a result of measuring afterglow time and after- flame time of the plywood containing 30% of water glass based on the type and concentration of inorganic additives, it was found that all of them satisfied the standard and had excellent performance. In addition, it was determined that there was no significant difference in afterglow time and after-flame time based on the type and concentration of additives. Park et al. (2006) reported that such phenomenon is caused by combustible gases in the gaseous phase diluted by the inorganic additives, and these gases act to prevent approach of oxygen near the surface. At the same time, it was also argued that endothermic reactions occur on the solid surface, reducing the cooling of the material and the generation of pyrolysis products.
For the char length of the plywood based on the type of inorganic additives, it was measured in the range of 71~158 mm for the specimen treated with additives, which satisfied the flame retardant performance of 200 mm. The char area of the test specimen treated with magnesium sulfate was in the range of 7,570~8,318 mm2, which did not satisfy the standard of 5,000 mm2. However, in the case of the test specimens treated with 15% of KOH, 1, 2, 5, and 10% of Al(OH)3, the maximum char area was measured as 4,766 mm2, and it exceeded the standard. The previous studies showed that magnesium sulfate was hydrated to become magnesium sulfate heptahydrate (MgSO4·5H2O) and it was used to improve the flame retardant performance (Mostashari et al., 2007). Thus, the reason for these tendencies in this study can be explained by anhydrous MgSO4 without having a hydrated structure which did not improve the flame retardant performance.
For the flame retardant performance based on the concentration of the additives, 5,127~7,863 mm2 was measured for the test specimens treated with 5% and 10% KOH, and it did not satisfy the flame retardant performance of 5,000 mm2 On the other hand, the test specimen treated with 15% KOH was measured as 3,947 mm2, which satisfied the standard. Therefore, it can be inferred that KOH contributes to improving the flame retardant performance. Furthermore, such result showed a similar tendency to the previous study (Mostashari et al., 2007) where the char length and char area decreased as the concentration of KOH increased.
As the concentration of KOH increased from 1% to 2%, the char length and char area decreased. However, they rather increased as the concentration increased from 5% to 10%. KOH affects the combustion reaction through physical processes, causing a series of endothermic reactions to lower the temperature of the combustion material so that the combustion reaction cannot be continued. However, Liang and Zhang (2010) reported that the high concentration of KOH diluted the flame retardants, generating too much of hydrates to lower the flame retardant performance. Similarly, the same phenomenon seems to have applied in this study.
In case of MgSO4, as the concentration increased, the char length and char area rather increased. This result showed a similar tendency to the previous study (Mostashari et al., 2008) where the char length increased as the concentration increased from 0.4 M to 0.5 M when the cellulosic fabric was treated with MgSO4.
In summary, as a result of evaluating the flame retardant performance, it was determined that the optimum additive and concentration for a plywood treated with inorganic additives and 30% glass water concentration was 1% of KOH.
4. CONCLUSION
In this study, we evaluated the flame retardant performance based on the concentration of water glass and the type and ratio of additives by measuring afterglow time, after-flame time, char length, and char area of plywood prepared in accordance with the standard of NFA Notification.
As a result of measuring the flame retardant performance based on the water glass concentration, the char length and char area decreased as the concentration increased, which improved the flame retardant performance. At a 50 % concentration of water glass, the NFA’s standard was satisfied, but the processability and aesthetic effect were lowered. In this regard, it is determined that 30% of water glass concentration is most suitable concentration for the flame retardant performance.
As a result of measuring the flame retardant performance based on the type and concentration of the additives treated on the plywood, we determined that 1% of KOH is most appropriate when inorganic additives are used in 30% of water glass concentration to make fire retardant plywood.
Through this study, we confirmed the flame retardant performance of water glass and additives on the plywood. Various concentrations of water glass and the additives have been shown to be effective in improving the flame retardant performance. However, as there is a difference based on the type and concentration of the additives, further researches on more various types of additives are needed. Consequently, we determined the most suitable concentration of water glass as 30 % and the type and concentration of the additive as 1% of Al(OH)3.