1. INTRODUCTION
Pretreatment is an essential process to improve the enzymatic saccharification efficiency of lignocellulosic biomass because of its recalcitrance characteristics (Wu et al., 2013). Moreover, pretreatment is the most expensive process, which reportedly costs approximately 20% of the total cost for ethanol production from lignocellulosic biomass (Yang and Wyman 2008). In this context, many studies have attempted to develop a novel pretreatment process to improve the economic feasibility of the biorefinery process from lignocellulosic biomass (Jung et al., 2017; Yanti et al., 2019). Among them, the pretreatment using ionic liquids (ILs) has attracted attention as an environment-friendly process because of their various advantages such as low volatility, high thermal and chemical stability, excellent solubility, non-flammability, and recovery. IL pretreatments are also known effective as the biological and chemical conversion of lignocellulosic biomass into a wide range of biomaterials and bioenergy (Park et al., 2015; Dutta et al., 2016; Han et al., 2020c). The IL pretreatment is known to be more environment-friendly and facile but less economical than other organic-solvent- based processes (Kim et al., 2012; George et al., 2015). Therefore, it is recommended to recover and reuse the ILs for industrial applications (Elgharbawy et al., 2016). Sangian et al. (2015) investigated the effect of recycling an IL (methylmethylimidazolium dimethyl phosphate, [MMIM]DMP) after pretreatment of coconut coir for enzymatic saccharification. The used IL was recycled twice to re-employ for pretreatment. The yields of sugar after the pretreatment using fresh IL and IL recycled once and twice were 0.19, 0.15, and 0.15 g per gram of polysaccharide (cellulose+hemicellulose), respectively. Ding et al. (2016) pretreated corn stover using dilute NaOH (1 wt% solution) followed by pretreatment with fresh and recycled IL (1-butyl-3-methylimidazolium chloride, [BMIM]Cl). The glucose concentration from the product pretreated with the IL recycled 10 times was 18.7 g/L after 12 h of enzymatic hydrolysis, which was 5.5 g/L lower than that with fresh IL. Cheenkachorn et al. (2016) reported that the pretreatment of rice straw with [EMIM]Ac could afford the glucose yield of 90% compared to untreated products. The recycling of [EMIM]Ac using methanol as an anti- solvent reportedly retains more than 90% efficiency without any modification in the pretreatment process despite 5 recycles. Xu et al. (2017) investigated the effect of recycling 1-allyl-3-methylimidazolium chloride ([AMIM]Cl) and 1-butyl-3-methylimidazolium acetate ([BMIM]Ac) on the pretreatment of eucalyptus for enzymatic hydrolysis. The glucose yield by ILs recycled 4 times was 54.3% for [AMIM]Cl and 72.8% for [BMIM]Ac, which was 5.0- and 6.7-folds higher than that of untreated eucalyptus. The pretreatment effect of the recycled ILs deteriorated after 4 times, showing relatively lower sugar conversion and lignin removal.
In this study, the effect of the number of recycling of [EMIM]Ac on the enzymatic saccharification was investigated to improve the economic feasibility of the pretreatment. The higher solid loading of 15 wt% was adapted, which is higher than about 5% in the general studies described above. Salix gracilistyla Miq. is a native species in Korea and known as one of the rapidly growing wood species for bioenergy production (Lee et al., 2018).
2. MATERIALS and METHODS
Salix gracilistyla Miq. wood powder (40 mesh) was extracted at 85 °C for 5 h with an ethanol/benzene mixed solution (1:2, v/v) and used as the lignocellulose material. The chemical composition of Salix gracilistyla Miq. was 47.2, 26.4, 25.1, and 5.6 wt% α-cellulose, hemicellulose, klason lignin, and extractives, respectively and these results have been reported previously (Han et al., 2017a). [EMIM]Ac was purchased from IoLiTec (Heilbronn, Germany), and other chemicals used in this study were obtained from Daejung Chemicals & Metals (Gyeonggi, Korea). Acremonium cellulase and Optimash BG were purchased from Meiji Seika Co. (Tokyo, Japan) and Genencor International, Inc. (Palo Alto, CA, USA).
The Salix gracilistyla Miq. wood powder was pretreated using [EMIM]Ac with 15 wt% solid loading at 120 °C for 2 h (Han et al., 2017b; Han et al., 2020a). The pretreated product was regenerated using 500 mL distilled water at room temperature for 1 h. The regenerated Salix gracilistyla Miq. was collected by filtration under vacuum and washed with distilled water (500 mL) to remove the residual IL and water soluble fraction. The fractionated residue was freeze-dried using FDB- 5503 (Operon Co., Ltd., Korea) and subjected to crystallinity analysis and enzymatic saccharification. The filtrate was collected from recycling the IL with an evaporator (Rotavapor, R-3000; Buchi Analytical Inc., USA) at 45 °C under a pressure of 700 mmHg and stored at 40 °C for 3 days, which was sufficient to remove almost all the water from the IL. [EMIM]Ac was recycled for 1-4 times. Then, the recycled IL was used as the raw material, and the treatment procedure was the same as mentioned above.
The compositional measurement of the monosaccharides before and after pretreatment was conducted using the Laboratory Analytical Procedure (LAP) by NREL (Sluiter et al. 2008). The raw material and pretreated samples (100 mg) were added to 1.5 mL Eppendorf tubes with 72% sulfuric acid solution (1 mL). For hydrolysis, the tubes were kept in a shaking incubator (Shaking incubator, VS-101Si, vision scientific Co., Korea) at 30 °C for 1 h. The hydrolysates were diluted to 4% using deionized water (19.8 mL) and further hydrolyzed at 120 °C for 1 h. Next, it was separated from the acid slurry for the measurement of acid-insoluble lignin to determine the acid-soluble monosaccharide. Calcium carbonate was used to neutralize the sample to a pH of 5-6. The supernatant was passed through a 0.2 μm filter into an autosampler vial before monosaccharide analysis by HPLC. The yields of glucose and xylose were measured by HPLC (YL9100, Younglin Co., Anyang, Korea) with a carbohydrate analysis column (Aminex HPX-87P, 300×7.8 mm, hydrogen form, 8% cross-linkage, Bio-Rad Laboratories, Inc., CA, USA) at a flow rate 0.6 mL/min at 85 °C. For acid-insoluble lignin measurement, the acid slurry was filtrated through the Whatman filter paper by adding distilled water until neutralized, dried at 100 °C, and weighed.
Enzymatic hydrolysis was conducted using an enzyme cocktail of Acremonium cellulase (15 FPU per gram of substrate) and Optimash BG (0.2%, v/v) as a supplement to β-xylosidase (Han et al., 2020b). The pretreated substrates (250 mg) were added to the enzyme cocktail at a solid loading of 2.5% in a sodium acetate buffer solution (50 mM, pH 5). Hydrolysis was performed in a shaking incubator at 50 °C for 72 h (150 rpm). Hydrolysates of 1 mL were sampled at 3, 6, 12, 24, 48, and 72 h intervals. The enzyme inactivation was conducted by heating at 95 °C for 15 min in a heating block (HB-48-Set, Wisd; Daihan Scientific Co., Ltd., Wonju, Korea) and stored at 4 °C. The enzymatic hydrolysate was centrifuged at 7000 rpm for 15 min and filtered through a syringe filter (0.2 μm).
X-ray diffraction analysis was conducted for the crystallization evaluation of the pretreated sample. For this analysis, the specimen was prepared by substituting the suspension with t-butyl alcohol and freeze-drying. X-ray diffraction analysis was performed at a rate of 2 ° per minute using an X-ray diffractometer (Rigaku RINTTTR III, Tokyo, Japan) at a range of 2θ = 2-60 °. The crystallinity index (CrI) was determined by the Segal method (Segal et al., 1959).
The monosaccharide analysis was conducted with an HPLC system (YL9100; Young Lin Instrument Co., Ltd., Anyang, Korea) equipped with an Aminex HPX- 87P column (Bio-Rad Laboratories, Inc., Hercules, CA, USA). The mobile phase was deionized water, and the flow rate was 0.6 mL/min at 85 °C. The glucose and xylose yields in the enzymatic hydrolysate were calculated using equation 1 and 2:
where 0.9 and 0.88 are conversion factors for glucose and xylose to glucan and xylan, respectively.
3. RESULTS and DISCUSSION
Fig. 1 shows the effect of the recycling number of [EMIM]Ac on the amount of water soluble fraction. Compared to the 21% fraction obtained by pure [EMIM]Ac, all samples pretreated with recycled [EMIM]Ac showed lower values. On increasing the recycling number from 1 to 4, the amount of water soluble fraction decreased from 18% to 15%. The water soluble fraction may contain low molecules of hemicellulose and lignin degraded by [EMIM]Ac, which can act as a physical barrier to block enzyme accessibility to cellulose (Shi et al., 2014; Kumagai et al., 2016). After extracting the water soluble fraction, the residual substrate will be cellulose-rich and very porous, which will increase the surface area of cellulose. Lee et al. (2010) reported that the nanospace could be generated between cellulose microfibrils by extracting hemicellulose by the hot-compressed water treatment. Moreover, delignification can increase the surface area of polysaccharides, i.e., cellulose and hemicellulose.
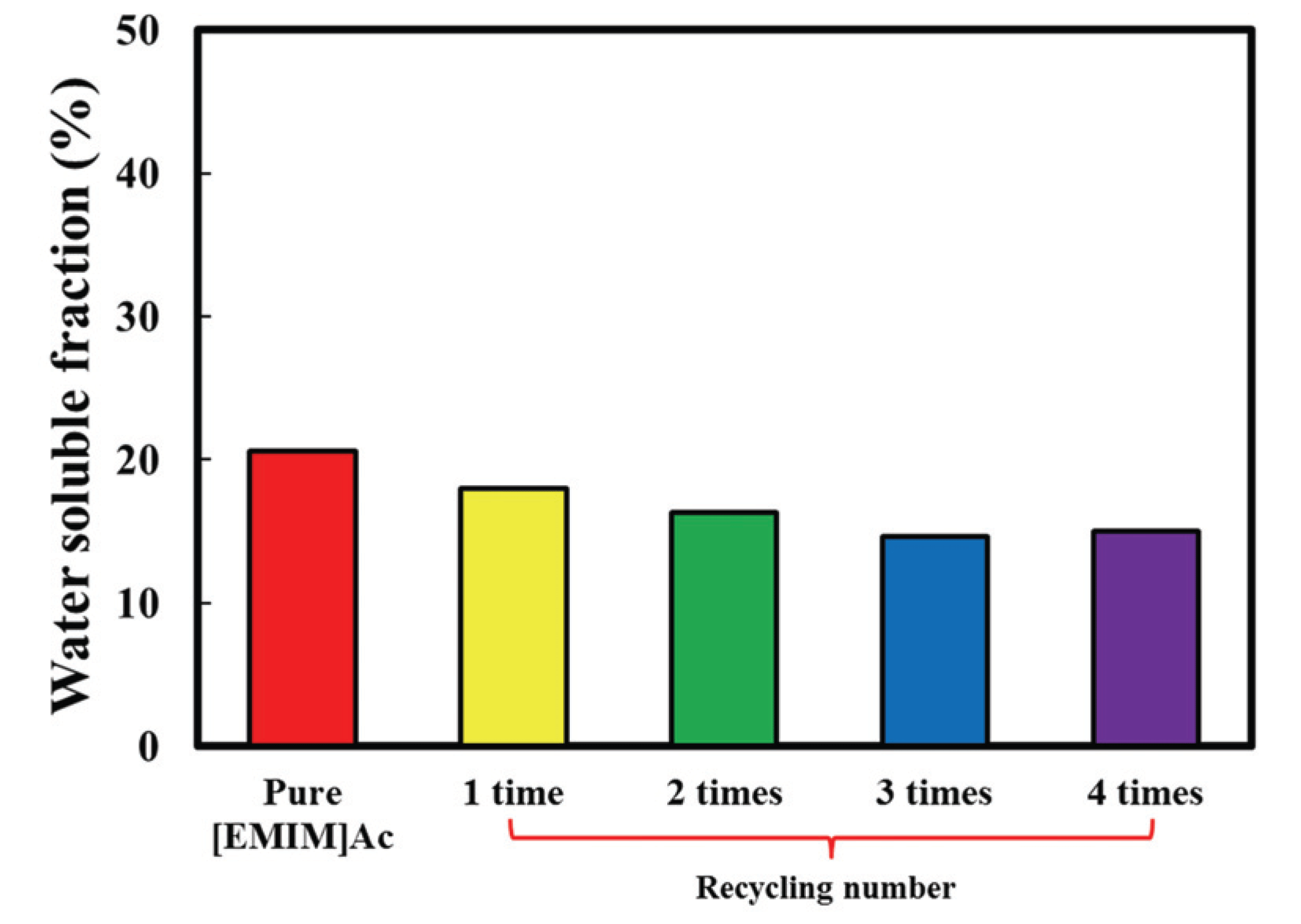
The main aim of pretreatment is to disrupt the cell wall structure of the lignocellulosic biomass by partial or complete removal of hemicellulose or lignin, resulting in the increase in the surface area and porosity of the substrates, and to decrease cellulose crystallinity (Kucharska et al., 2018). Fig. 2 shows the XRD patterns of the products pretreated with pure and recycled [EMIM]Ac for different recycling numbers, and their CrI are summarized in Table 1. The raw material and the product pretreated with pure and recycled [EMIM]Ac displayed a strong peak at around 22.8° (2θ), corresponding to the (002) crystal plane of cellulose, as well as composite peaks at 15° and 15.5°, corresponding to the (101) and (10) crystal planes. This pattern represents the cellulose I polymorph. In the sample pretreated with pure [EMIM]Ac, however, the intensity of the (002) plane dramatically decreased and no distinct peak for the (101) and (10) planes were observed. This indicates that the crystallinity of cellulose is significantly disrupted by partial dissolution and distension of the cellulose crystal (Zhang et al., 2014). The increase in the amorphous portion of cellulose will improve its enzyme accessibility (Ling et al., 2017). This disruption ability was diminished by [EMIM] Ac recycling, regardless of the recycling numbers.
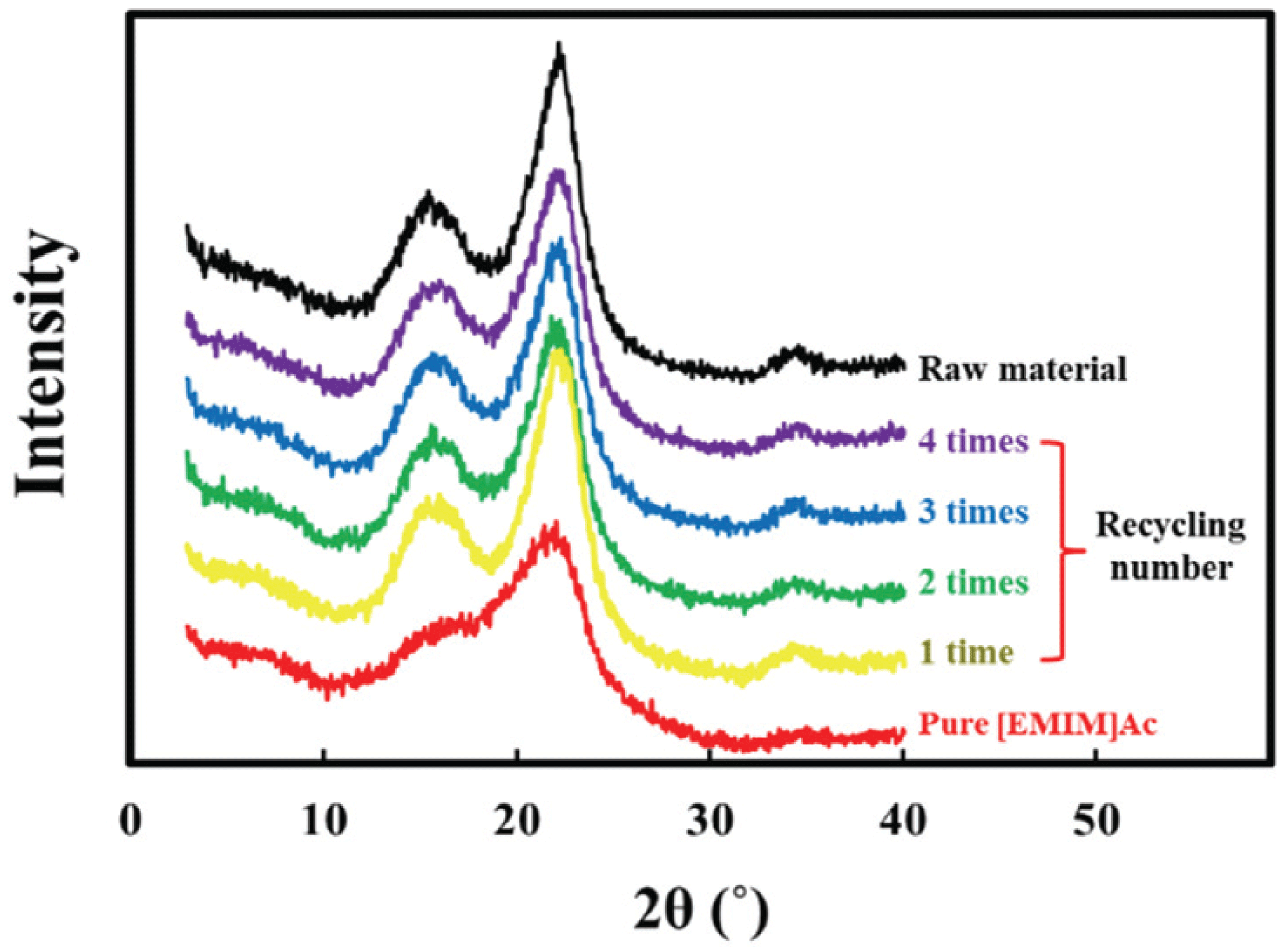
Raw material | Pure [EMIM]Ac | Number of the recycling | ||||
---|---|---|---|---|---|---|
1 | 2 | 3 | 4 | |||
CrI (%) | 55 | 33 | 49 | 47 | 47 | 47 |
The CrI of the raw material was 55%, which decreased to 33% by pretreatment with pure [EMIM]Ac. However, the CrI of the product pretreated with recycled [EMIM]Ac ranged from 47 to 49%, which was higher than that with pure [EMIM]Ac. This indicates that the pretreatment effect of lowering the CrI is deteriorated by recycling. Hamidah et al. (2018) reported the pretreatment of softwood (Cryptomeria japonica) with a recycled [EMIM]Ac without the dissolution of cellulose and lignin. It was reported that CrI (34.0%) of the product pretreated with [EMIM]Ac recycled for 3 times were similar with 30.7% of the products with pure [EMIM]Ac, and glucose yields were also not significantly different between the products pretreated with recycled and pure [EMIM]Ac. Although lignin dissolved in [EMIM]Ac continued to accumulate after [EMIM]Ac recycling, the pretreatment was found to be effective for three consecutive cycles without the need for the removal of dissolved materials.
Fig. 3 shows the glucose and xylose yields of the product pretreated with pure and recycled [EMIM]Ac depending on enzymatic saccharification time. The glucose and xylose yields were evaluated from the original masses of glucan and xylan, which were obtained by acid hydrolysis. With increasing enzymatic saccharification time, the glucose and xylose yield increased in all products. The product pretreated with pure [EMIM]Ac showed the highest glucose and xylose yields, which were more than 80% for 72 h saccharification. On the other hand, the raw material exhibited the lowest yields, i.e., approximately 20% and 10% for glucose and xylose, respectively. With recycled [EMIM]Ac, both yields decreased compared to pure [EMIM]Ac. There was no significant difference in both yields among the products pretreated with recycled [EMIM]Ac yields of 66-69% for glucose and 55-63% for xylose for 72 h saccharification.
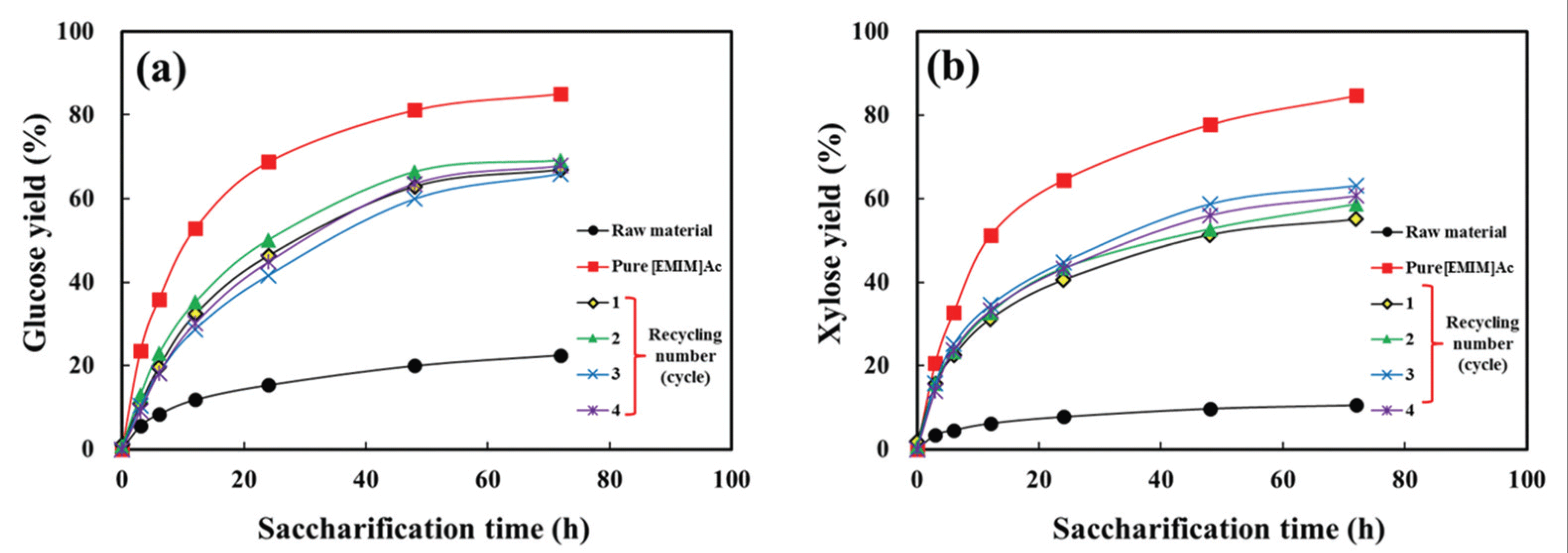
The glucose and xylose yields of the product pretreated with pure and recycled [EMIM]Ac after enzymatic saccharification are calculated using equation 2 and summarized in Table 2. These values are calculated on the basis of the original mass and the glucan (xylan) after acid hydrolysis (equation 1) in paren thesis as well. The glucose and xylose yields of the product pretreated with pure [EMIM]Ac were 42% and 13%, respectively. These values decreased with the pretreatment with recycled [EMIM]Ac. Regardless of the recycling number, the glucose yield on enzymatic saccharification was 34-36%, which was lower than that with pure [EMIM]Ac. However, the xylose yield (9-12%) was not significantly different from that with pure [EMIM]Ac (13%). This result is attributed to the extraction amount of the water soluble fraction because the value was calculated by compensating the amount of water soluble fraction. This also indirectly indicates that the water soluble fraction contains hemicellulose components degraded by [EMIM]Ac.
Yield of enzymatic saccharification | |||
---|---|---|---|
Glucose (%) | Xylose (%) | ||
Raw material | 14 (22) | 3 (11) | |
Pure IL | 42 (85) | 13 (85) | |
Recycling number | 1 | 34 (67) | 9 (55) |
2 | 32 (69) | 10 (59) | |
3 | 34 (66) | 11 (63) | |
4 | 34 (68) | 12 (61) |
In general, there is a correlation between the saccharification yield and the CrI of the cellulose (Cui et al., 2014). It is also known that the initial rate of the cellulase-catalyzed hydrolysis of cellulose is linearly proportional to the crystallinity index of cellulose. In this study, the CrI of the product pretreated with pure [EMIM]Ac was 33%, showing the highest saccharification yield. On the other hand, the CrI values (47-49%) increased for the product pretreated with recycled [EMIM]Ac, showing the lower saccharification yield than that with pure [EMIM]Ac. Hall et al. (2010) reported that the CrI of cellulose is a key predictor of the enzymatic saccharification efficiency and rate. They stated that the initial enzymatic rate continued to increase with a decreasing crystallinity index, even though the bound enzyme concentration stayed constant. They insisted that their finding supports the determinant role of crystallinity rather than adsorption on the enzymatic rate. Hou et al. (2012) reported that [Ch]Lys showed excellent reusability over five successive batches in the pretreatment of rice straw. Lignin continued to accumulate in [Ch]Lys during recycling, and delignification efficiency decreased slightly from 59% to 53% over the five recycling batches for rice straw. Glucose yields (84-87%) and initial glucose release rates (2.4-2.5 mg/mL/h) remained almost constant after the IL was reused for five batches.
4. CONCLUSION
Pretreatment with recycled [EMIM]Ac of Salix gracilistyla Miq. was successfully conducted to achieve more than 80% yield of glucose and xylose by enzymatic saccharification. Compared to the product pretreated with pure [EMIM]Ac, the product pretreated with recycled [EMIM]Ac showed a lower amount of water soluble fraction, cellulose I polymorph, and higher CrI, and lower yields of glucose and xylose. However, there was no significant difference in these properties among the product pretreated with recycled [EMIM]Ac. It is concluded that the pretreatment effect of recycled [EMIM]Ac was declined, compared to pure [EMIM]Ac, but more than 60% enzymatic saccharification yield was able to be achieved by the pretreatment using [EMIM]Ac recycled for 4 times.