1. INTRODUCTION
With the recent improvement in the quality of life, environmental noise has become a serious issue; therefore, there is a growing demand for the noise control (Jang et al., 2018; Kim et al., 2012; Kook et al., 2007; Lee et al., 2011; Hwang et al., 2013). Several studies have investigated construction materials with an excellent sound absorption rate, methodologies for determining sound absorption rates, and sound insulation materials. Additionally, the unstable supply of industrial resources and an increase in the global effort on the reduction of greenhouse gases have led to a growing interest in recycling. South Korea, a country with a small land area and insufficient natural resources, should aim to save all its resources and develop recycling technologies for efficiently using various industrial byproducts (Kang et al., 2018a; Kang et al., 2018b; Kang et al., 2019).
Sound absorption dissipates sound energy for reducing reverberation and controls the reverberation time of a room. Sound absorbing materials should offer a high sound absorption rate, with little or no adverse effect on humans.
Sound insulation is required to block indoor noise and establish excellent indoor sound environment; its performance can be evaluated based on the sound transmission loss (STL), ratio of the intensity of incident sound to transmitted sound, and the transfer matrix method, and the reverberation method are often used to measure STL. By measuring STL using an impedance tube, the transfer matrix method is advantageous from the viewpoint of time, cost, space, and size of specimens; therefore, it is often used in rapid evaluations of STL during the development of sound materials. The reverberation method requires a large space and substantial amount of test materials, time, and cost; however, it offers more reliable results.
Meanwhile, wood bark is a byproduct obtained from processing wood materials. While there are differences in the wood species, approximately 10%–20% of wood materials are generated as wood bark worldwide, and wood bark can be considered as eco-friendly biomass owing to the little contamination in the process. However, wood barks have large difference in chemical components, and the shape of the particles is complex; therefore, its added value is rarely recognized. It is often used for additional materials for agricultural compost or fuel materials as low value-added materials.
To improve the usability of wood bark, Anderson et al. (1974) aimed to produce wood bark particle boards. Lee (1977) analyzed the physical and anatomical properties of pine, oak, and poplar trees, such as density, strength, heat, and moisture, and reported that there were substantial differences between the properties of different wood species. Mun and Kim (1994) reported that the pine wood bark has less fiber content and large amount of lignin extracts and ash content. Kim and Lee (2006) showed that Larch, nut pine, and pitch pine wood bark could be used as carbides after a 4-h process at 400°C. Additionally, Lee (1989) measured and reported the dynamic properties of oak wood bark using wood bark boards with a specific density ranging between 0.94 and 1.03. Although there have been some researches on wood bark properties and its potential as construction materials, but, to the best of our knowledge, no study has been conducted on the acoustic properties of wood bark particles.
In this study, wood barks of three different Korean tree species were used for comparison along with Douglas-fir, Radiata pine, and Hemlock wood barks, which are usually processed at a sawmill located in Gimje. Six kinds of wood bark, including five needleleaf trees and one broadleaf tree, were used herein. Several wood barks with different thickness and density were filled in sample holders, which were assumed to be wood bark mats. The vertical incident sound absorption rate was measured by the transfer function method, and the STL coefficients were measured by the transfer matrix method. In this way, the sound absorption performance and transmission loss of wood bark were determined, and its potential as construction materials or road sound insulation materials were examined.
2. MATERIALS and METHODS
As shown in Fig. 1, six species of wood bark particles were grinded with a coffee grinder for the same amount of time to control the size of particles. The resulting wood bark particles were filled into an impedance tube, as shown in Fig. 2. The target thickness of the wood bark matt was determined by the pressure of the sample holder knob at the back of the tube controlled to achieve the target density and the back knob of the sample holder fixed to a certain thickness; this thickness was presented for the measurement of the sound absorption rate and STL. Herein, to prevent wood bark from sliding down due to gravity, a circular net obtained using a 3D printer, as shown in Fig. 2, was installed at the front to measure the vertical incident sound absorption rate.
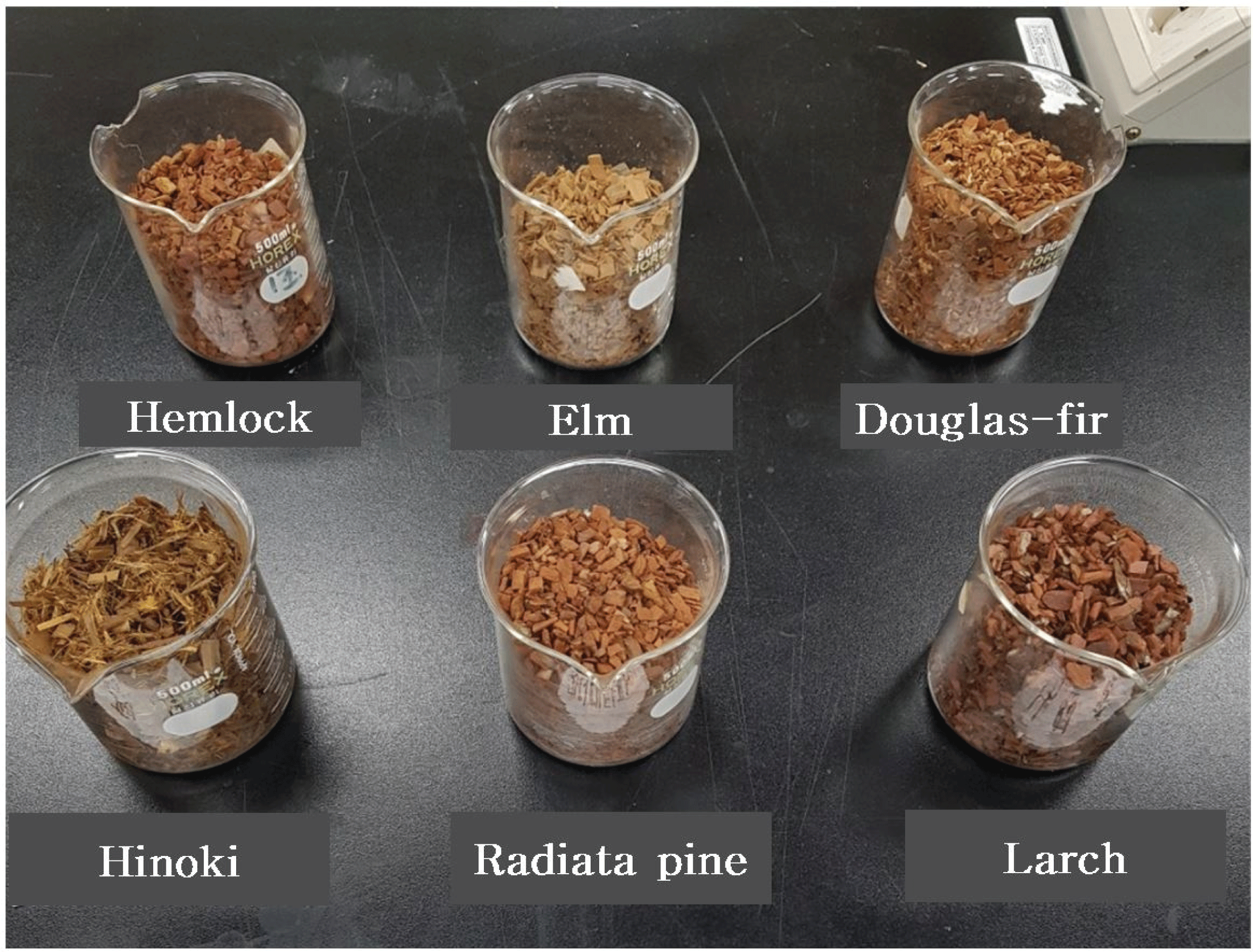
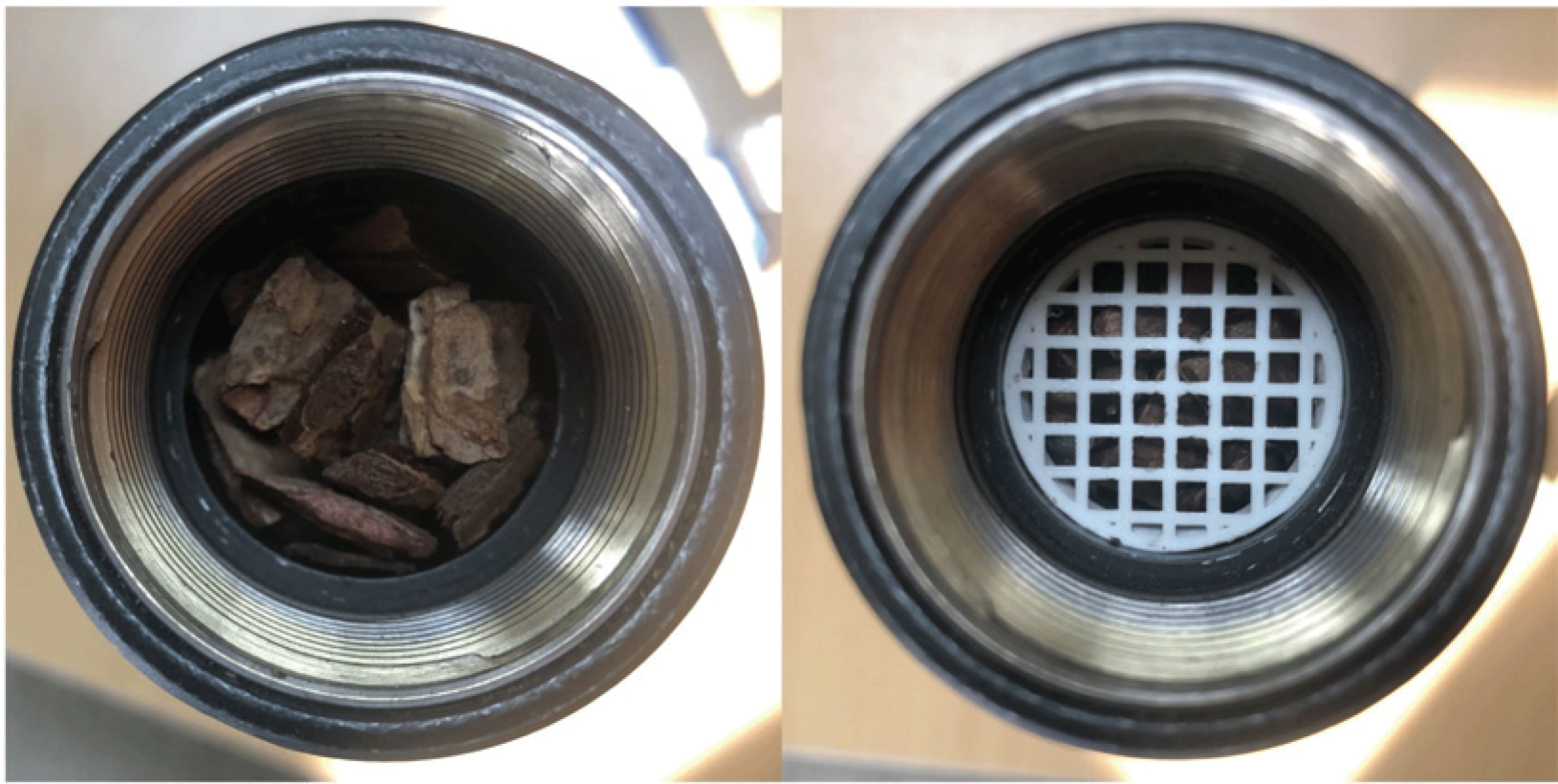
As described in a previous study (Kang et al., 2019), sound absorption rates were measured by the ISO 10534-2 transfer function method using an impedance tube, pulse analyzer, and spectrum analyzer (B&K Co.). Owing to the frequency limitation of the impedance tube, 29- and 99-mm tube is used for high and low frequency ranges, respectively. Herein, the 29-mm tube was used to measure the sound absorption rate as a function of the frequency in the range 100–6400 Hz.
During the measurement, temperature, relative humidity, and air pressure were 19.90°C, 39.00%, and 1032.00 hPa, respectively, and the sound speed, air density, and sound impedance were 343.18 m/s, 1.225 kg/m3, and 420.3 Pa/(m/s), respectively.
As described in a previous study (Kang et al., 2018b), transmission loss measurement was conducted using the impedance tube, pulse analyzer, and spectrum analyzer (B&K Co.) based on the transfer matrix method of ASTM E2611–09. A 29-mm impedance tube was used to measure the transmission loss in the frequency range 100–6400 Hz. During the measurement, external temperature and air pressure were 24.1°C and 1027.50 hPa, respectively.
3. RESULTS and DISCUSSION
The sound absorption rates of wood bark matts with thicknesses of 20, 30, 50, 80, or 100 mm with a specific density of 0.12 in the frequency range 100–6400 Hz is shown in Fig. 3. For 100-mm thickness, the mean sound absorption rate was 0.77 for Larch (Larix kaempferi), 0.93 for Hinoki (Chamaecyparis obtusa), 0.50 for Radiata pine (Pinus Radiata), 0.59 for Douglas-fir (Pseudotsuga menziesii), 0.56 for Elm (Zelkova serrata), and 0.58 for Hemlock (Tsuga heterophylla Sargent), and the NRC was 0.57 for Larch, 0.80 for Hinoki, 0.24 for Radiata pine, 0.31 for Douglas-fir, 0.30 for Elm, and 0.30 for Hemlock.
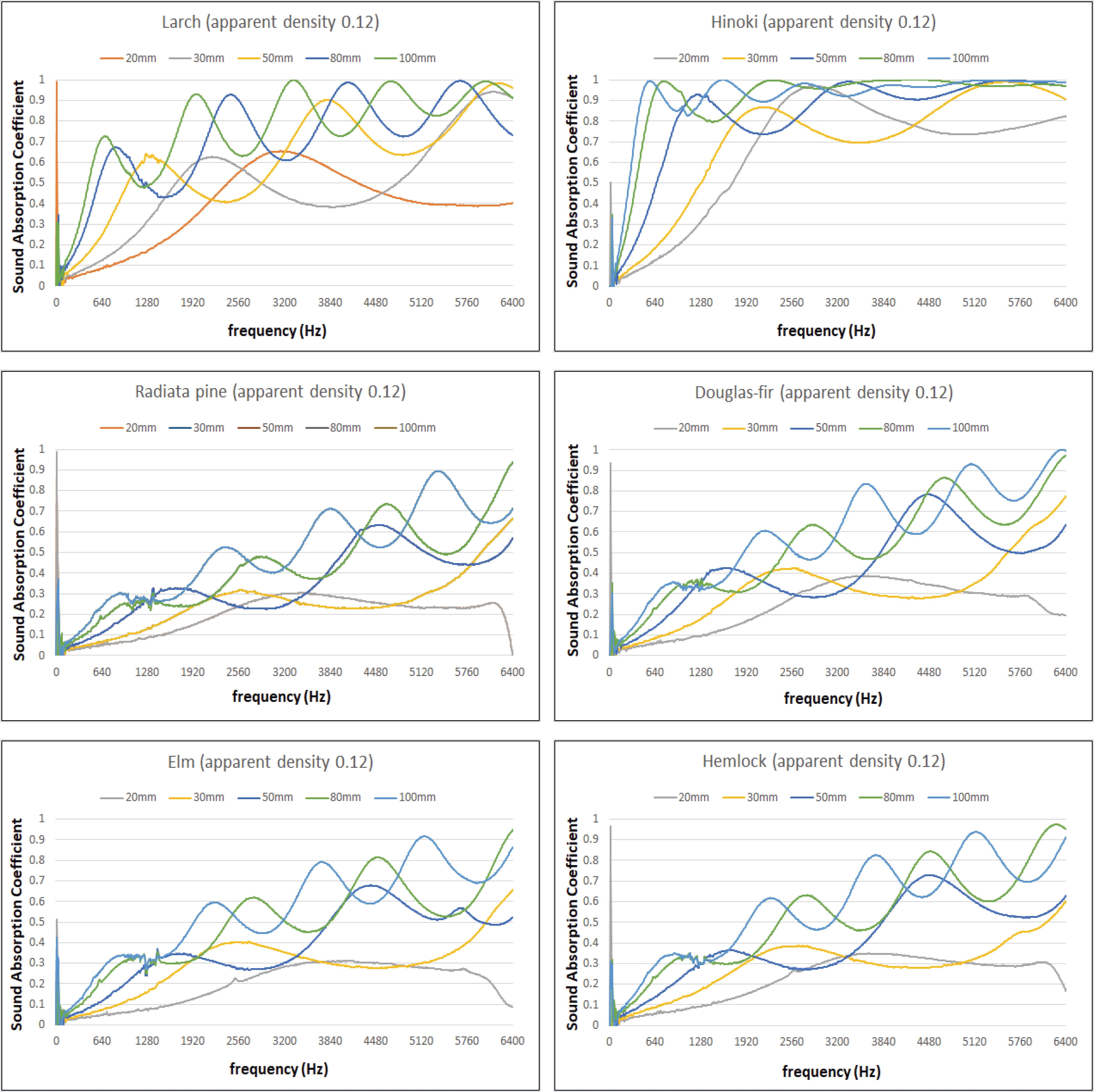
The sound absorption rates of wood bark matts determined in the frequency range 100–6400 Hz using the transfer function method are shown in Fig. 4. The specific density was 0.14 and thickness was 20, 30, 50, 80, or 100 mm. The thickness of aluminum frame sound insulation walls often used for highway sound insulation walls is approximately 100 mm. At 100-mm thickness, the mean sound absorption rate was 0.80 for Larch, 0.93 for Hinoki, 0.60 for Radiata pine, 0.67 for Douglas-fir, 0.56 for Elm, and 0.65 for Hemlock, and the NRC was 0.66 for Larch, 0.81 for Hinoki, 0.32 for Radiata pine, 0.41 for Douglas-fir, 0.30 for Elm, and 0.39 for Hemlock.
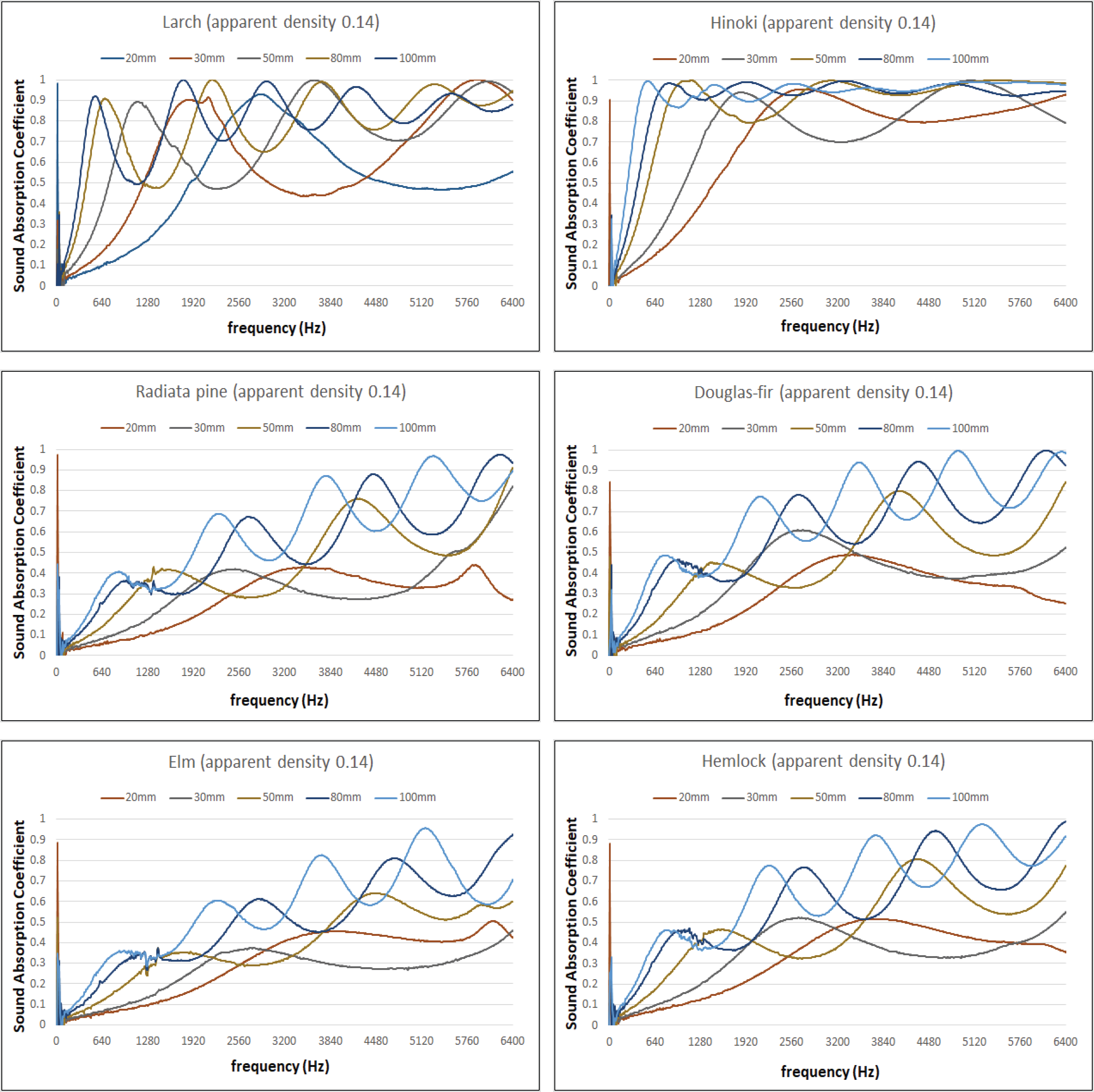
The sound absorption rates of wood bark matts measured in the frequency range 100–6400 Hz using the transfer function method are shown in Fig. 5. The density was 0.16 and thickness was 20, 30, 50, 80, or 100 mm. At 100-mm thickness, the mean sound absorption rate was 0.84 for Larch, 0.90 for Hinoki, 0.64 for Radiata pine, 0.70 for Douglas-fir, 0.62 for Elm, and 0.71 for Hemlock, and NRC was 0.70 for Larch, 0.82 for Hinoki, 0.40 for Radiata pine, 0.47 for Douglas-fir, 0.33 for Elm, and 0.45 for Hemlock.
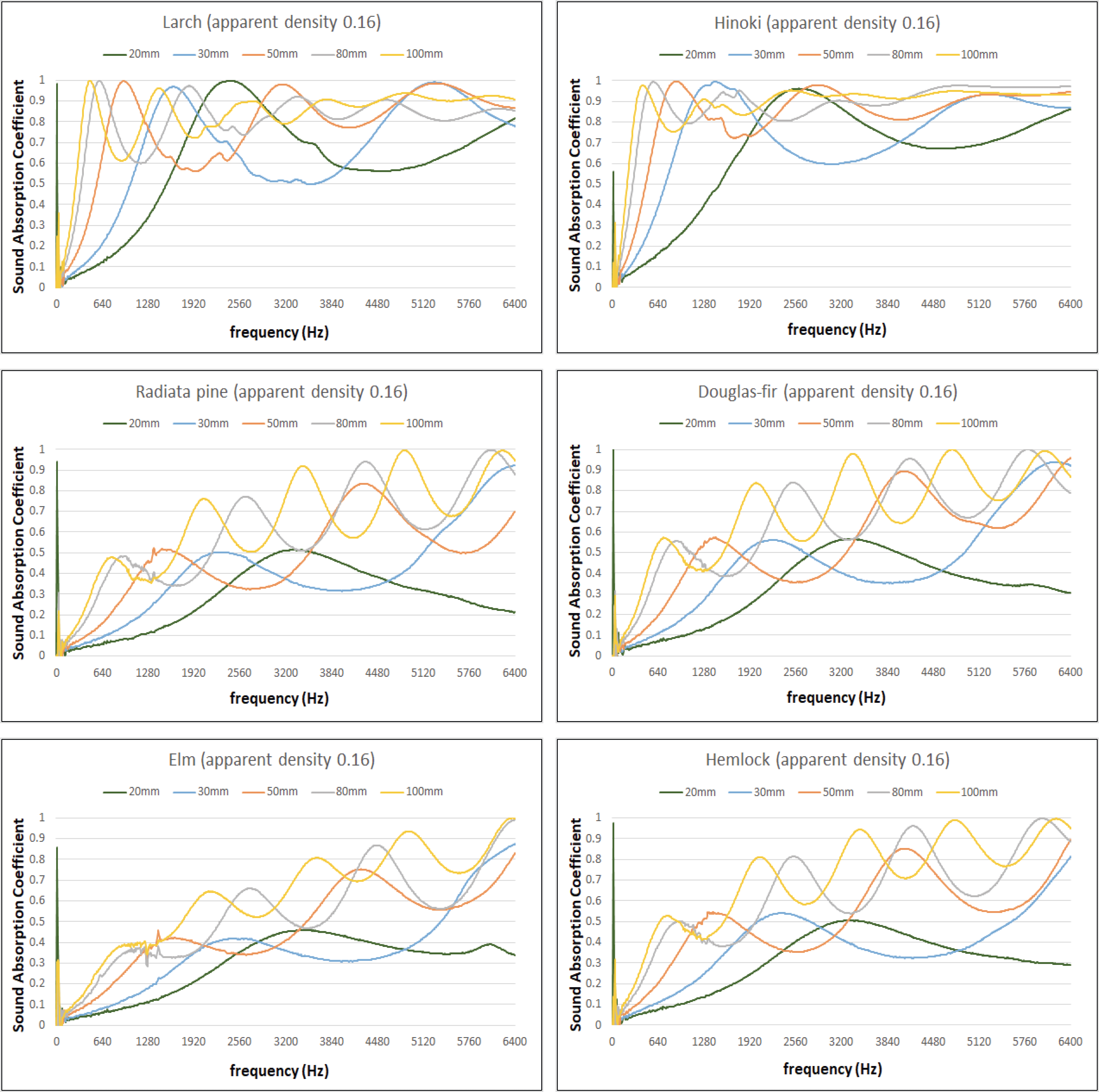
The sound absorption rates of wood bark matts using the transfer function method are shown in Fig. 6. The specific density was 0.12 and thickness was 50, 80, or 100 mm, and the frequency range was 100– 6400 Hz. To the back of all matts, 10-mm thick plywood was attached. At 100-mm thickness, the mean sound absorption rate was 0.73 for Larch, 0.94 for Hinoki, 0.54 for Radiata pine, 0.61 for Douglas-fir, 0.53 for Elm, and 0.56 for Hemlock, and the NRC was 0.54 for Larch, 0.80 for Hinoki, 0.30 for Radiata pine, 0.34 for Douglas-fir, 0.27 for Elm, and 0.32 for Hemlock.
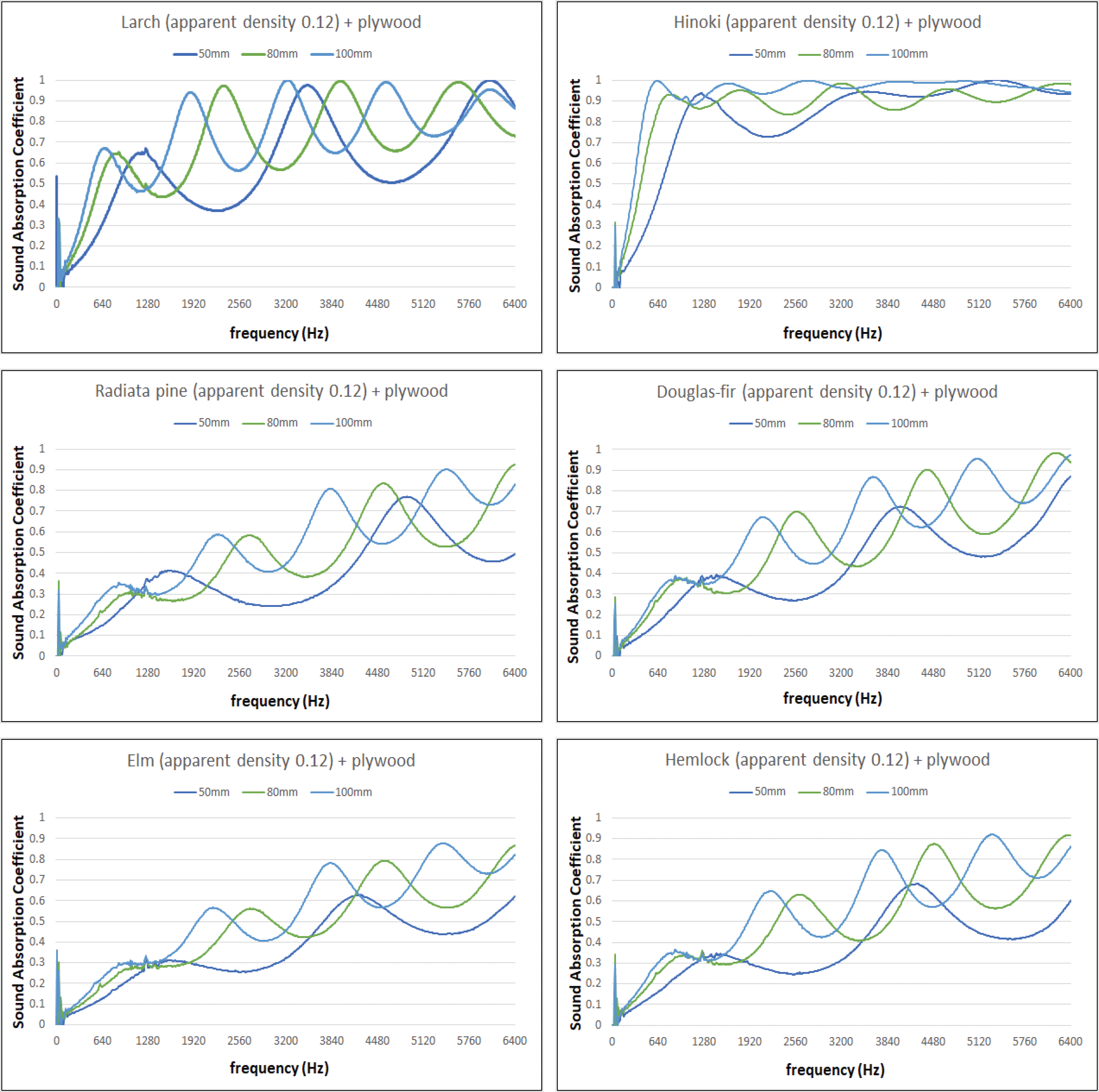
The sound absorption rates of wood bark matts using the transfer function method is shown in Fig. 7. The specific density was 0.14 and thickness was 50, 80, or 100 mm in the frequency range of 100–6400 Hz. To the back of all matts, 10-mm thick plywood was attached. At 100-mm thickness, the mean sound absorption rate was 0.84 for Larch, 0.90 for Hinoki, 0.56 for Radiata pine, 0.64 for Douglas-fir, 0.57 for Elm, and 0.63 for Hemlock, and the NRC was 0.63 for Larch, 0.82 for Hinoki, 0.32 for Radiata pine, 0.39 for Douglas-fir, 0.30 for Elm, and 0.38 for Hemlock.
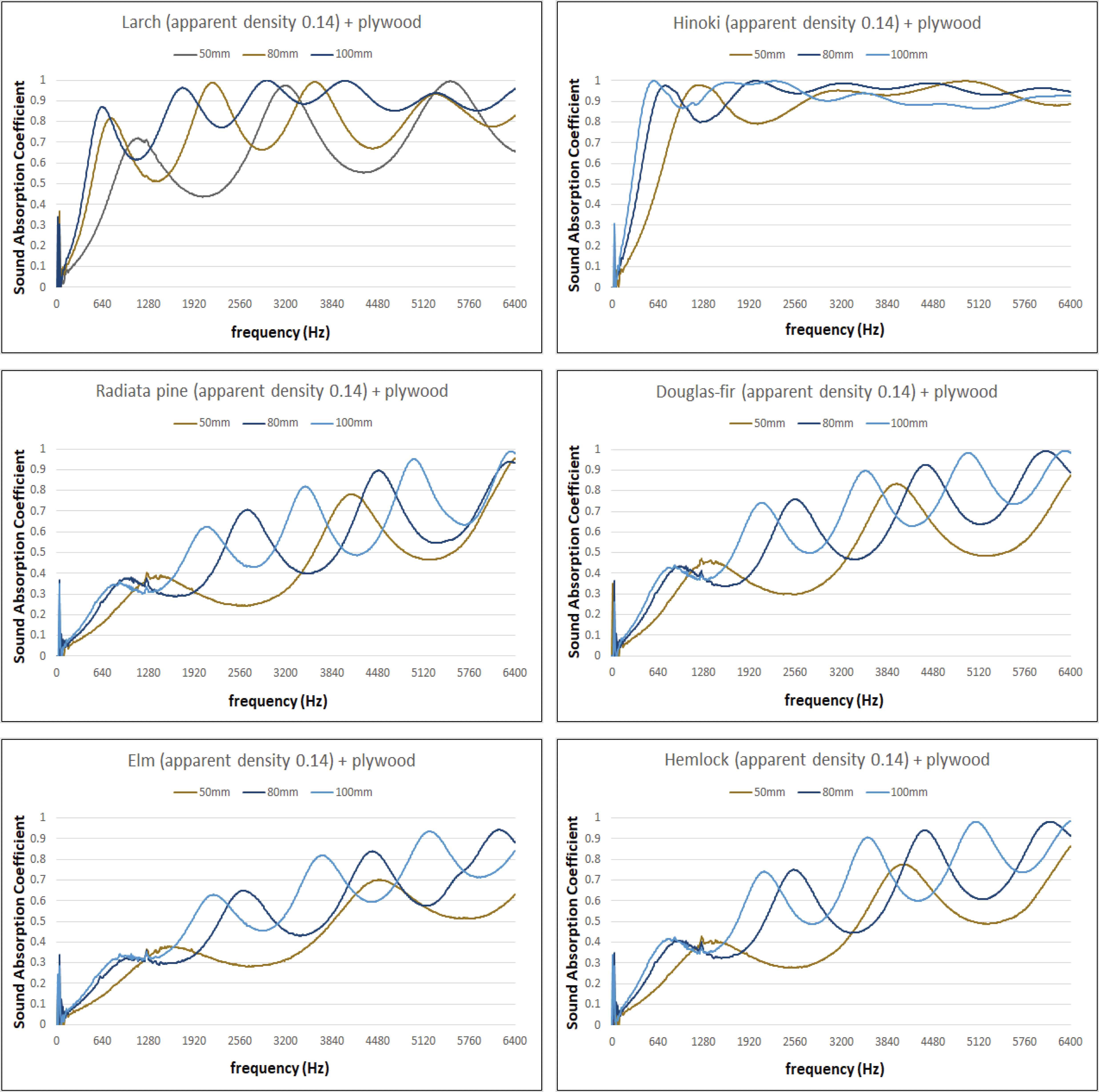
The sound absorption rates of wood bark matts measured using the transfer function method is shown in Fig. 8. The specific density was 0.16 and thickness was 50, 80, or 100 mm in the frequency range of 100– 6400 Hz. To the back of all matts, 10-mm thick plywood was attached. At 100-mm thickness, the mean sound absorption rate was 0.83 for Larch, 0.90 for Hinoki, 0.60 for Radiata pine, 0.68 for Douglas-fir, 0.63 for Elm, and 0.67 for Hemlock, and the NRC was 0.65 for Larch, 0.86 for Hinoki, 0.39 for Radiata pine, 0.42 for Douglas-fir, 0.34 for Elm, and 0.43 for Hemlock.
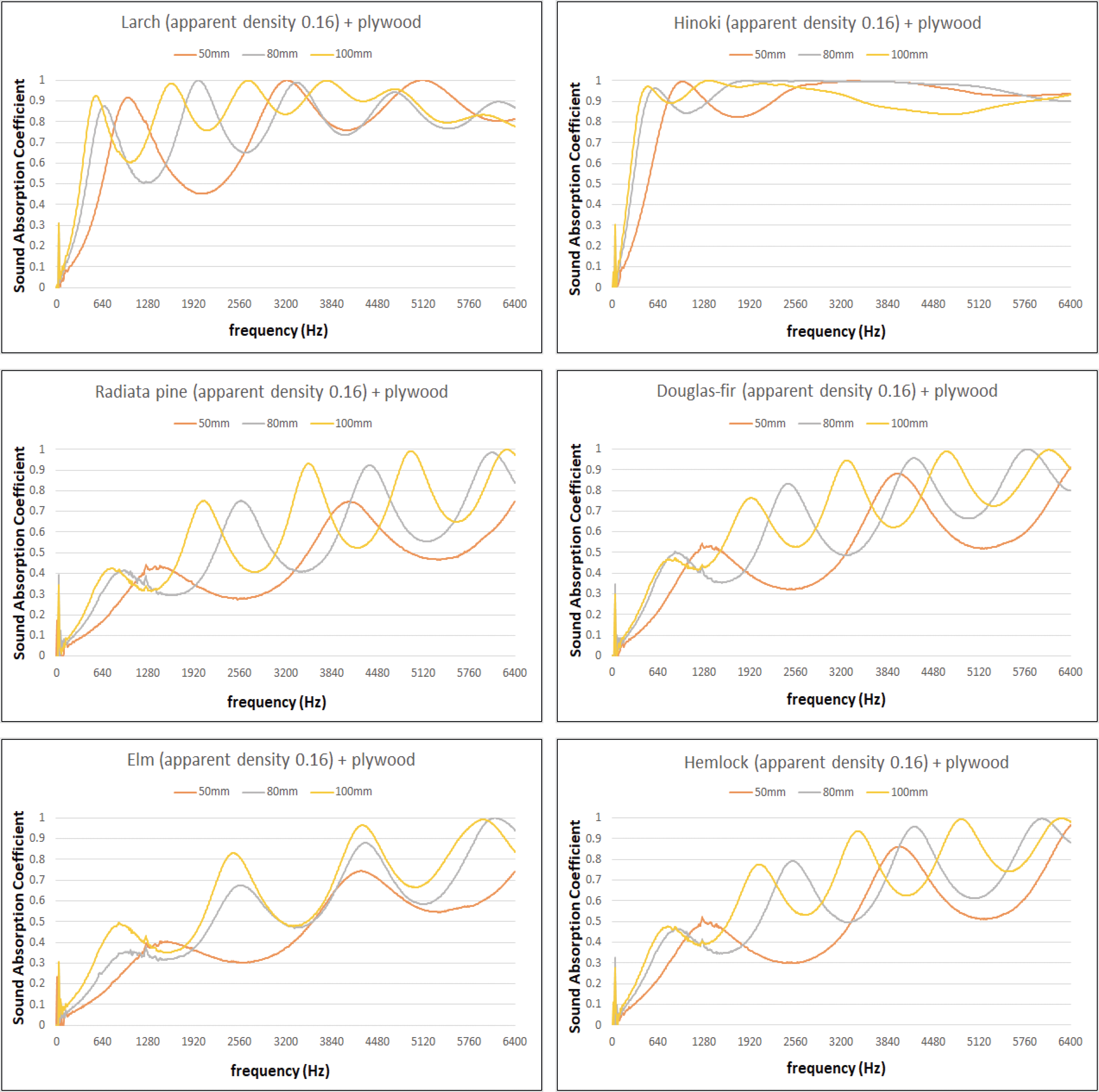
It is believed that the reason for such differences in the sound absorption rate of wood bark particles is because the components and shape of wood bark are different for different tree species (Lee, 1977). Accordingly, even if particles in similar size are used to create wood bark particle matts with the same target density, different air flow resistance would generate, resulting in different sound absorption performance. Air flow means that there exist penetrating pores. Li et al. (2014) reported that penetrating pores have a decisive impact on the sound absorption behavior and air flow resistance; therefore, it is important to appropriately increase the number and size of pores in improving the sound absorption properties lower frequency ranges where the sound absorption performance is low due to the reduction of the air flow resistance.
Overall, as the apparent specific density increases from 0.12 to 0.16, the mean sound absorption rate increased by 0.10 and 0.081 at 50 and 100 mm thickness, respectively.
The mean sound absorption rate with plywood was 0.37–0.94, and without plywood, it was 0.20–0.93, which is decrease of approximately 9.5%. At 100-mm thickness, the mean sound absorption rate of wood bark in the range 100–6400 Hz was 0.70. When the thickness of wood bark and plywood is 100 mm, it was 0.69.
Meanwhile, the NRC of the ceiling gypsum board used often in offices and lecture halls was approximately 0.30, and most wood bark matts in 100 mm herein were over 0.30, except 0.24 and 0.27 from Radiata pine and Elm, respectively, with the density of 0.12; therefore, they showed superior performance than the gypsum board. Particularly, the sound absorption coefficient was over 0.80 in Hinoki wood bark with the density of 0.16 and thickness of 10cm. Therefore, it is believed that the Hinoki wood bark particle with the density of 0.16 could be used as sound absorbing mat. In addition, further research on the sound absorp tion performance of oriental oak wood bark, which offers a high wood bark ratio, should be conducted for the high added value use of Korean species of trees.
The STL data from six species of wood bark and wood bark matts whose apparent specific density was 0.12, 0.14, and 0.16 is shown in Fig. 9. At a specific density of 0.12, the mean STL in the frequency range of 100–6400 Hz was 6.37 dB for Larch, 12.46 dB for Hinoki, 2.06 dB for Radiata pine, 2.41 dB for Douglas-fir, 1.69 dB for Elm, and 2.50 dB for Hemlock. At a specific density of 0.14, the mean STL in the frequency range 100–6400 Hz was 13.44 dB for Larch, 19.50 dB for Hinoki, 1.39 dB for Radiata pine, 3.63 dB for Douglas-fir, 2.38 dB for Elm, and 3.27 dB for Hemlock. At a specific density of 0.16, the mean STL in the frequency range 100–6400 Hz was 18.81 dB for Larch, 26.95 dB for Hinoki, 4.16 dB for Radiata pine, 5.25 dB for Douglas-fir, 3.31 dB for Elm, and 4.03 dB for Hemlock.
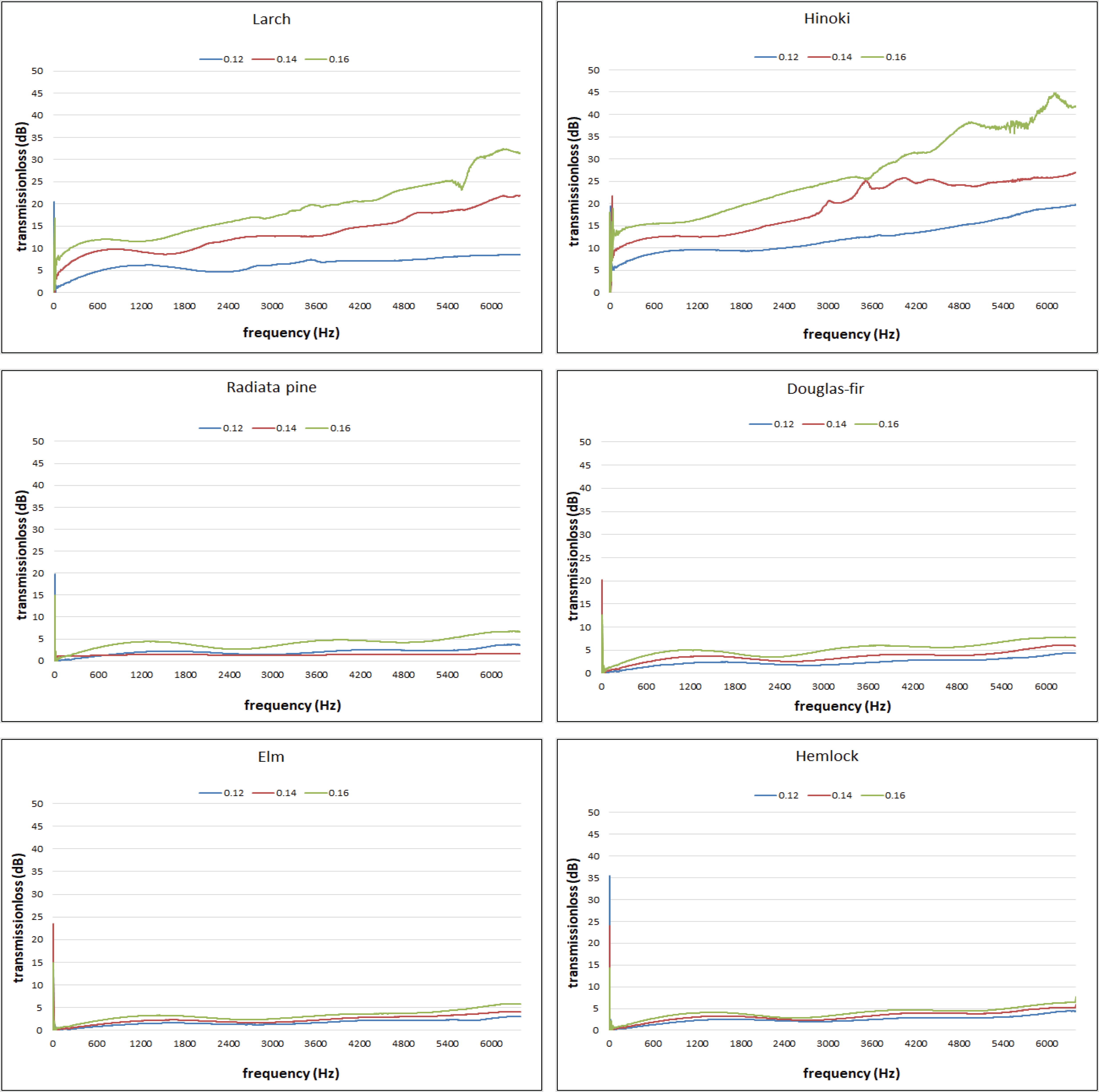
Wood bark particle matts from Radiata pine, Douglas-fir, Elm, and Hemlock showed low STL at or below 5 dB in the frequency range even after the increase of the apparent specific density from 0.12 to 0.16 due to the pores between wood bark particles. On the contrary, the wood bark particle matts from Larch with a specific density of 0.12 showed a STL between 5 and 9 dB, which was somewhat higher than those of Radiata pine, Douglas-fir, Elm, and Hemlock. However, the wood bark particle matts of Hinoki showed a STL higher by more than two times than Radiata pine, Douglas-fir, Elm, and Hemlock showing the loss of 5–10 dB at 100–1000 Hz, 10–15 dB at 1000–4000 Hz, and 15–20 dB at 4000–6400 Hz, respectively. When the apparent specific density was increased to 0.16, Larch wood bark particles showed a loss of 8–12 dB at 100–1000 Hz, 15–20 dB at 1000– 4000 Hz, and 20–30 dB at 4000–6400 Hz, and Hinoki wood bark particles showed the loss of 13–15 dB at 100–1000 Hz, 15–30 dB at 1000–4000 Hz, and 25–40 dB at 4000–6400 Hz. The reason for such high STL of Larch and Hinoki wood bark particles in comparison with other species of wood is because their wood bark is thin and dense. The apparent specific density is increased by applying pressure, and small and thin particles are tightly attached together to reduce or stop air flow, which increases the STL. As the frequency increases, the STL increased as well. The STL of wood bark particles was generally between 0 and 20 dB, making it difficult to expect sound insulation performance.
The STL of six species of wood bark with plywood whose apparent specific density was 0.12 and 0.16 is shown in Fig. 10. At a specific density of 0.12, the mean transmission loss at 100–6400 Hz was 37.36 dB for Larch, 45.99 dB for Hinoki, 38.87 dB for Radiata pine, 33.54 dB for Douglas-fir, 38.76 dB for Elm, and 38.11 dB for Hemlock. At specific density of 0.16, the mean transmission loss at 100–6400 Hz was 46.80 dB for Larch, 48.35 dB for Hinoki, 36.41 dB for Radiata pine, 38.54 dB for Douglas-fir, 38.79 dB for Elm, and 38.17 dB for Hemlock. With a drastic increase in the transmission loss than the wood bark particle matts, the loss at or below 1000 Hz was approximately 30 dB, and above 1000 Hz, it increased to 30–50 dB. Overall, it increased by approximately 20 to 30 dB. Therefore, it is believed that the addition of plywood would offer better sound insulation performance.
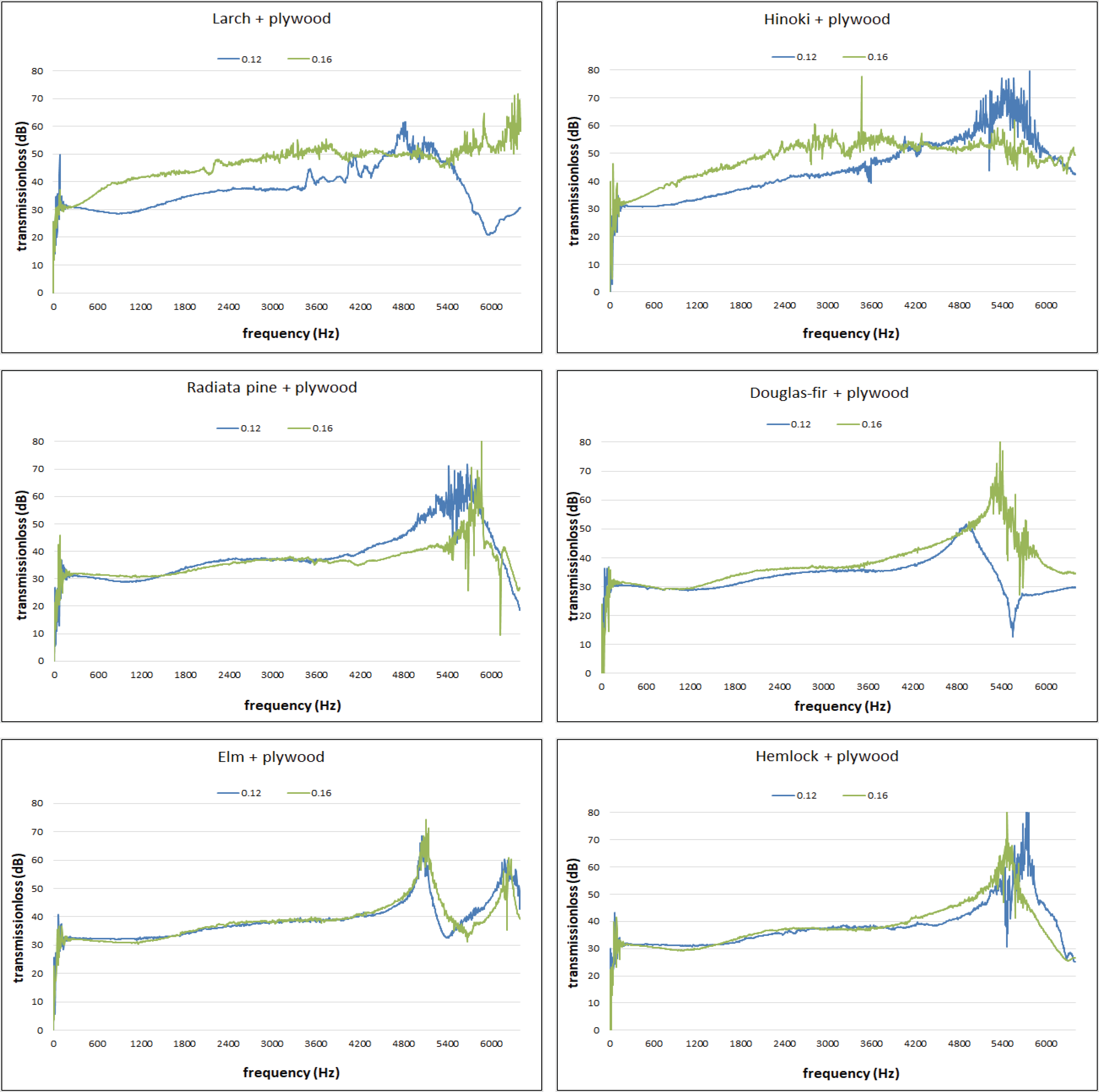
4. CONCLUSION
Herein, the sound absorption performance of wood bark was measured by changing its apparent specific density and thickness, and the results were compared to the specimens attached with plywood. Plywood was attached to the wood bark with the specific apparent specific density and thickness whose sound absorption performance was shown to be excellent in the sound absorption rate measurement results, and its STL was measured and compared with the transfer matrix method. Therefore, the study resulted in the following conclusions:
It was determined that wood bark offered a higher sound absorption rate than existing gypsum boards; therefore, it could be used as sound absorbing materials.
The STL of wood bark was low, but after plywood was attached at the back of wood bark matts, it increased by 20-30 dB.
It was determined that by adjusting the thickness and apparent specific density and attaching plywood at the back, wood bark particle matts would offer excellent sound absorption and insulation performance; therefore, they could be used as acoustic materials for building projects or sound insulation materials for road noise reduction.